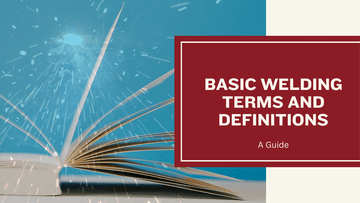
Understanding these terms is key to discussing and improving your welding skills.
In this easy-to-follow blog, we'll introduce you to the essential welding terms that light up this craft. Welding isn't new—it's an ancient skill that has played a crucial role in creating everything from tiny tools to towering skyscrapers. Our guide will demystify the complex language of welding, ensuring you're no longer in the dark when it comes to discussions about fusing metals.
Welding Terminology and Its Importance
Understanding welding terminology is crucial for effective communication among welders and ensuring the quality of work. It helps in deciphering welding symbols, following procedures, and promoting safety in the workplace.
Understanding Welding Terminology
Welding terms are like a special language. People who weld need to know these words to do their work well and stay safe. If two welders talk about a job, they use welding vocabulary so they both understand what needs to be done.
Knowing the correct terms helps them choose the right tools and techniques.
When someone learns welding, they start with basic words and definitions. This includes knowing different types of welding processes like arc welding or MIG welding gun. They also learn about the parts of a weld, such as filler metal and base metal.
Understanding this language is important because it helps people follow instructions, read blueprints, and make strong welds that last.
Importance of Knowing Welding Terms
Knowing welding terms is crucial for effective communication among welders. It ensures that everyone understands the specific techniques, equipment, and safety measures involved in various welding processes.
By having a shared understanding of terms like "weld joints," "coalescence of metals," and "shielded metal arc welding," welders can work together seamlessly, enhancing productivity and safety on the job.
Additionally, being knowledgeable about welding terminology also helps in interpreting instructions accurately, adhering to standards, and achieving high-quality results in welding projects.
Understanding basic welding terms enables clear communication within the welding community. It facilitates precise discussions about techniques, equipment, materials, tools, procedures, applications as well as certifications and safety standards.
Communication Among Welders
Understanding basic welding terms is important for effective communication among welders. When working together, clear and precise communication about the welding process, techniques, and safety measures ensures a smooth workflow and minimizes errors.
Keywords such as weld joints, coalescence of metals, electric arc, shielded metal arc welding help in conveying accurate information and ensuring that everyone is on the same page.
This collaborative approach fosters a productive and safe working environment for all involved.
Types of Welding Processes
Arc welding, MIG welding, and TIG welding are the three main types of welding processes used in various applications. Each process has its own unique characteristics and benefits, making it important for welders to understand the differences between them.
Arc Welding
Arc welding uses electricity to create an arc between the base metal and an electrode, melting both materials. The molten weld pool cools to form a strong joint when the weld solidifies.
This method is versatile and suitable for various metals, making it widely used in construction, fabrication, and repairs. Mastering arc welding is essential for any professional welder seeking diverse skill sets in their career.
Moving on to "MIG Welding," let's explore another popular welding technique that offers its unique set of advantages.
MIG Welding
MIG welding, also known as Gas Metal Arc Welding (GMAW), uses a wire electrode and a shielding gas to join two metal pieces together. This process is efficient and provides high productivity, making it popular in various industries such as automotive, construction, and manufacturing.
MIG welding allows for fast welds on thin or thick metals, with minimal post-weld cleaning needed.
By using MIG welding techniques, welders can create strong and clean welds while minimizing splatter. The process is versatile and can be used on different types of metals such as aluminum, stainless steel, and mild steel.
Additionally, with the right equipment setup and proper training in MIG welding procedures, precise and consistent results can be achieved across various welding applications.
TIG Welding
TIG welding, or Tungsten Inert Gas welding, uses a non-consumable tungsten electrode to produce the weld. This process provides precise control over the heat and is suitable for welding thin sections of stainless steel and non-ferrous metals.
The inert gas shield protects the molten weld pool from atmospheric contamination, resulting in high-quality welds with no spatter. TIG welding is widely used in industries requiring clean and aesthetically pleasing welds, such as aerospace and automotive manufacturing.
Basic Welding Accessories Terms and Definitions
-
Angle Grinder: A tool used for cutting, grinding, and polishing metal, often used in preparation or finishing of welds.
-
Chipping Hammer: A tool for removing slag from the weld bead.
-
Electrode Holder: A clamping device in stick welding for holding the electrode.
-
Ear Protection: Earplugs or earmuffs to protect the welder’s hearing.
-
Ground Clamp: A clamp that completes the electrical circuit by connecting the welding equipment to the workpiece.
-
MIG Gun: A tool in MIG welding gun for feeding the welding wire and delivering the shielding gas.
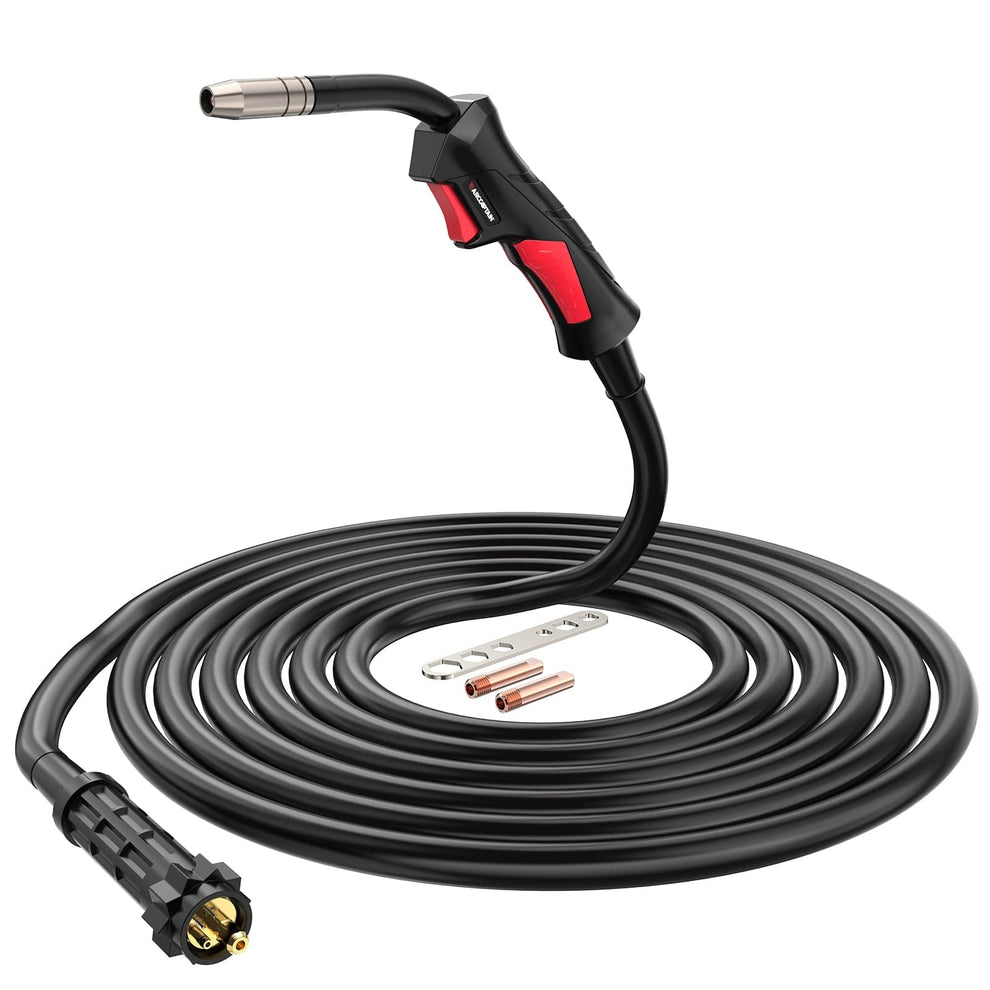
ARCCAPTAIN MIG200 MIG Welding Gun MB15 180 Amps 15AK MIG Torch
-
Safety Glasses: Glasses worn under the helmet for added eye protection.
-
TIG Torch: A tool in TIG welding that holds the tungsten electrode and provides a gas shield.
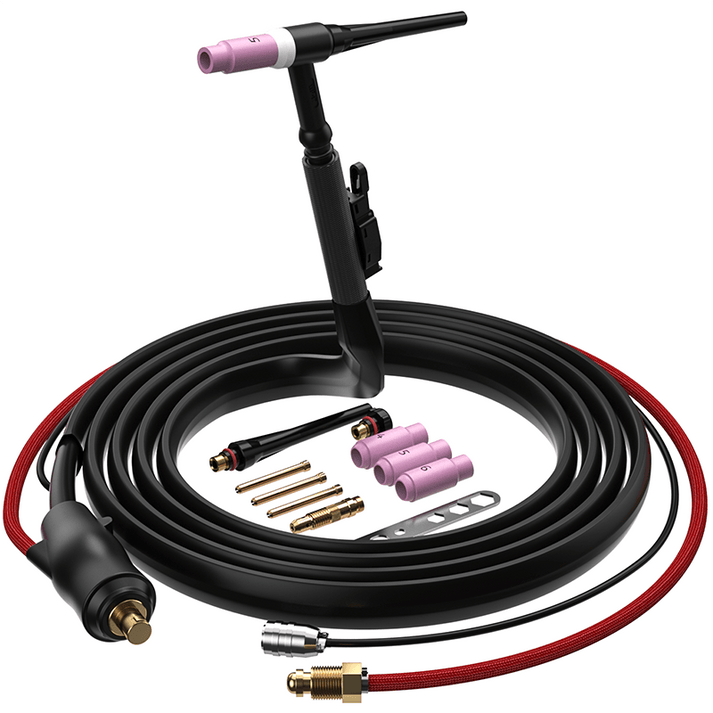
ARCCAPTAIN High Frequency Air Cooled TIG200/TIG200PAC DC TIG Torch 13-FT 150 Amps Gun
-
Welding Apron: A protective leather welding apron made of leather or other durable materials.
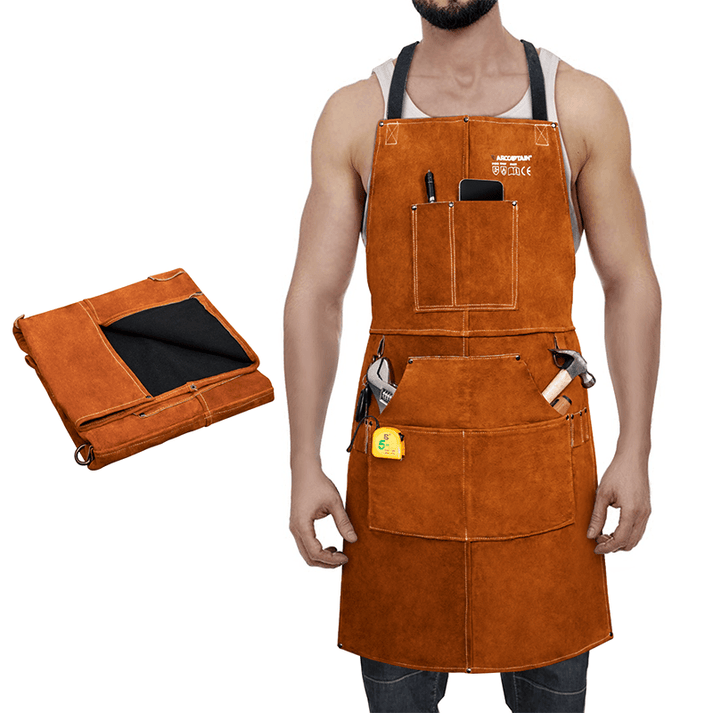
Heavy Duty Thick Leather Welding Apron/Heat Resistant Multi-Function Apron
-
Welding Clamps: Clamps used to hold and secure the metal pieces together before welding.
-
Welding Curtains: Curtains designed to shield bystanders from the welding arc light.
-
Welding Gloves: Heat-resistant gloves to protect the welder's hands.
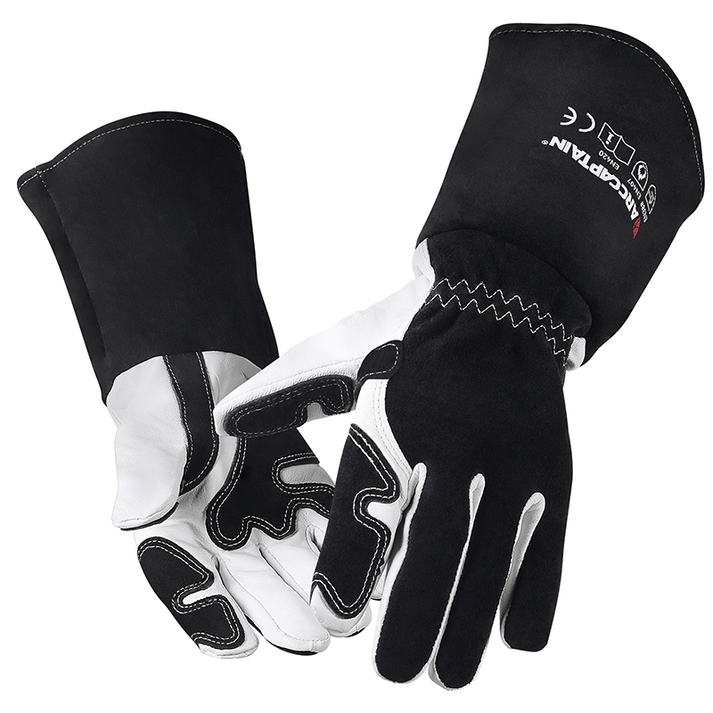
-
Welding Helmet: A protective headgear that guards the eyes, face, and neck from various hazards.
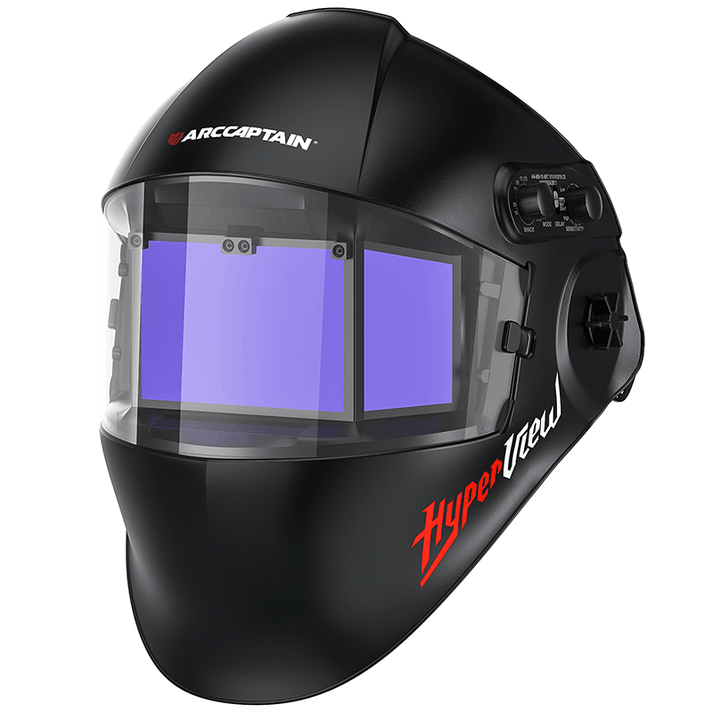
ArcCaptain Collection of Large-View Welding Helmet
-
Welding Jacket: A flame-resistant garment to protect the welder's body.
-
Welding Respirator: A device to protect the welder from inhaling harmful fumes.
-
Wire Brush: A brush for cleaning the weld area before and after welding.
Essential Welding Terms and Definitions
Understanding key terms such as alloy, annealing, and joint is crucial for successful welding projects. To learn more about these essential welding terms and definitions, keep reading to expand your knowledge of the welding industry.
Alloy
An alloy is a mixture of metals or a metal combined with other elements. The purpose of creating an alloy is to enhance specific properties like strength, durability, or resistance to corrosion.
Common examples of alloys include steel, which is a combination of iron and carbon, and brass, which combines copper and zinc. Alloys are frequently used in welding gun as they provide diverse material options to meet different project requirements.
Understanding the composition and properties of alloys is essential for welders as it influences the choice of welding gun materials and techniques. Welders must be familiar with the behavior and characteristics of various alloys to ensure successful welds that meet specific quality standards.
Annealing
Annealing is a heat treatment process used to soften metal by heating it and then gradually cooling it. This reduces hardness and increases ductility. During annealing, the metal is heated to a specific temperature and then allowed to cool slowly at a controlled rate.
It helps relieve internal stress, refine the grain structure, and improve machinability of the metal.
The annealing process is crucial in welding as it helps in reducing brittleness in metals after they have been welded. It also helps to restore the material's properties, making it easier to work with during subsequent processes such as shaping or forming.
Base Metal
The base metal refers to the primary metal being welded. It is the main piece that needs to be joined together using welding techniques. The choice of base metal affects the type of welding process and filler metal used, as well as the overall strength and quality of the weld.
Understanding the properties and composition of the base metal is crucial for achieving a successful weld that meets specific requirements such as tensile strength, ductility, and corrosion resistance.
Knowing about the base metal helps in selecting appropriate welding methods, ensuring proper heat input, controlling distortion, and preventing defects like cracking or weakening. Additionally, it allows for matching compatible filler metals which are essential for creating strong bonds between materials during welding procedures.
Bond
A bond in welding refers to the strength with which two metal pieces are joined together. It is crucial for a strong and durable bond that can withstand various forces and conditions.
The process of creating a bond involves carefully melting and fusing the metals, ensuring that they form a solid connection.
Understanding the different types of bonds is essential in welding to ensure that the right method is used for specific applications. Whether it's creating a seamless joint or forming a secure spot weld, knowing how to achieve a strong bond is fundamental for successful welding projects.
Case Hardening
Case hardening is a method of creating a hard outer layer on metal while keeping the interior tough. This process involves heating the metal in a carbon-rich environment, allowing carbon to penetrate the surface.
As a result, the outer layer becomes hardened while the inner core remains strong and durable.
The case hardening process enhances the wear resistance of metals such as steel, making them suitable for applications requiring toughness and durability. It's an essential technique in welding because it helps increase the lifespan of welded components by making them more resistant to abrasion and impact.
Joint
Before moving on to the welding term "joint," it's important to understand that case hardening is a process used to make the outer layer of a metal harder. Now, let's talk about joints in welding.
A joint refers to the location where two or more workpieces are joined together during the welding process. There are various types of joints such as butt joint, lap joint, corner joint, and T-joint.
The type of joint used depends on the specific requirements of the project and the welding process being employed.
Melt-thru
Moving on from understanding different welding joints, another important term is "melt-thru." This refers to the process of completely penetrating and fusing the base metals together during welding.
It's essential for welders to achieve proper melt-thru to ensure strong and durable welds. Melt-thru also plays a crucial role in determining the quality and integrity of the welded joint, making it a fundamental concept in welding processes.
Understanding melt-thru is vital for ensuring the effectiveness and durability of welds. Achieving proper melt-thru ensures that base metals are thoroughly fused together, resulting in strong and reliable welds.
Seam Weld
Moving from discussing "Melt-thru" welding to another essential term, let's understand "Seam weld." Seam welding involves joining two pieces of metal along a continuous line. This type of welding is commonly used in automotive and aerospace industries for creating leak-proof joints.
The process involves the use of a rotating wheel to apply pressure and heat along the seam, resulting in a strong and uniform bond between the metals. Understanding this term is crucial for anyone involved in metal fabrication or manufacturing processes.
It allows welders to create durable and reliable seams, ensuring the integrity and quality of the final product.
Spot Weld
Spot weld refers to a type of welding where two pieces of metal are joined together at small, specific points. This is done by applying pressure and heat to the pieces being welded.
It's commonly used in automobile manufacturing and sheet metal work due to its speed and cost-effectiveness.
Conclusion
In conclusion, understanding basic welding terms is essential for effective communication and safety in the welding industry. By familiarizing oneself with these terms, welders can efficiently carry out various welding processes such as arc welding, MIG welding, and TIG welding.
Knowing the definitions of terms like alloy, annealing, base metal, and joint ensures practical and efficient application in welding projects. This knowledge not only impacts the quality of work but also contributes to overall safety.
For further learning on this topic, consider exploring reputable resources or seeking guidance from experienced professionals in the field. Remember: mastering these basic welding terms lays a strong foundation for professional growth and success in the world of welding.
Frequently Asked Questions
1. What are some basic welding terms I should know?
Some basic welding terms include the types of welding equipment, different welding tools used for joining metals, and important safety practices to follow while welding.
2. Why is it important to use proper welding safety gear?
Using proper welding safety gear protects you from sparks, heat, and harmful light that can hurt your eyes and skin when you're working with welding tools.
3. What's the purpose of having a welding certification?
A welding certification shows that a welder knows how to handle the equipment safely and can do good-quality work following industry standards.
4. Can anyone learn to use welding tools?
Yes, anyone interested in learning can start with understanding basic terms and definitions related to equipment and techniques; however, they must be trained on safely using those tools before starting any actual work.