
Confused by the array of MIG welding wires at your local hardware store? You're not alone. Picking the wrong wire can lead to weak welds, rust, or just not fitting your project needs. But here’s the key: each wire type has its own purpose, and the right choice can transform your work from average to outstanding.
Did you know? A significant 25% of industrial robots are used for welding. This highlights how crucial it is to know your wires – not just for DIY projects, but to stay in step with industry trends.
In this straightforward guide, we’ll walk you through the different MIG welding wires, explaining their properties and applications. We aim to help you understand how choosing the correct wire can significantly improve your welding quality. Let’s dive in and help you make an informed choice for your next welding project.
Primary Types of MIG Welding Wire
Flux-core wire and solid MIG welding wire are the two main types of MIG welding wire used in various applications. Each type has its own composition, structure, and specific uses in welding.
Flux-core Wire
Flux-core wire is a special kind of welding filler material designed for metal inert gas (MIG) welding. This type of wire has a hollow center filled with flux. The flux inside the wire melts during welding and protects the weld pool from air and contamination.
This means you don't always need external shielding gas, like argon or carbon dioxide, when you're using flux-core wire.
Many welders pick flux-cored wire for outdoor work because it's not affected by wind like solid MIG welding wires that require gas protection. It can also handle dirty or rusty materials better than solid wires can.
Next up is solid MIG welding wire which needs a separate shielding gas to protect the weld area from air and impurities.
Check out ArcCaptain Flux Core Welding Wire Non-GAS Mild Carbon Steel Welding Wire!
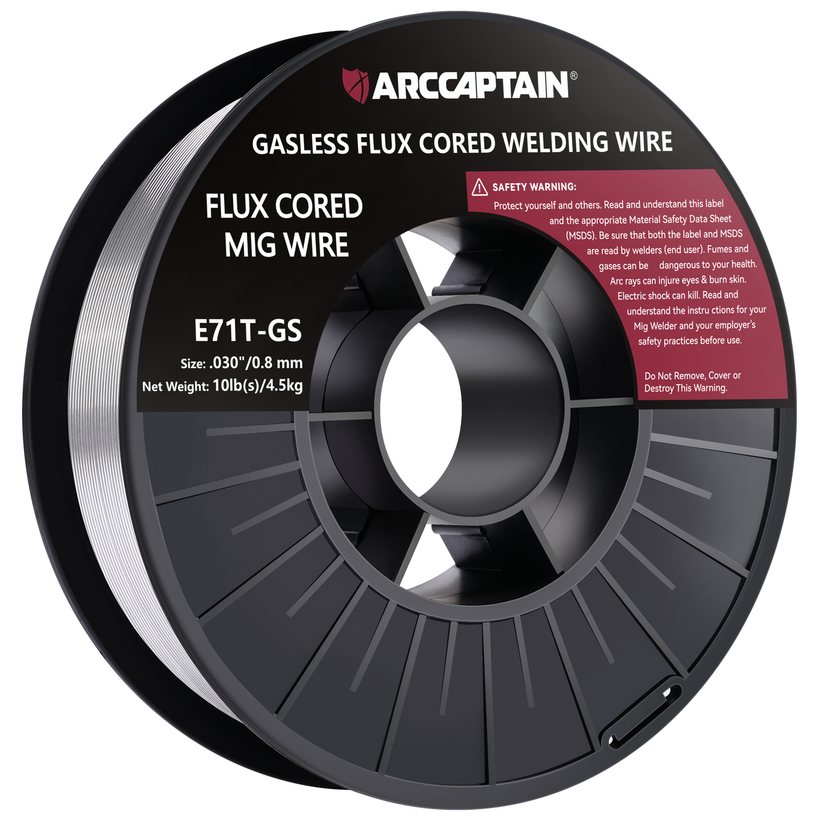
ARCCAPTAIN E71T-GS 10 Lbs Flux Core Welding Wire
Solid MIG Welding Wire
Solid MIG welding wire, also known as solid wire or GMAW wire, is made of a single, solid piece of metal. It doesn't contain any flux and relies on an external shielding gas to protect the molten weld pool from atmospheric contamination.
Solid MIG welding wire is commonly used with a mix of carbon dioxide and argon as the shielding gas for general steel welding applications. This type of wire produces less spatter and provides better control over the weld bead profile.
For stainless steel and aluminum welding, specific types of solid MIG wires are required due to their different compositions compared to regular carbon steel. These wires are formulated to match the chemical composition of the base metal being welded, ensuring high-quality and precise welds.
Check out ArcCaptain MIG Welding Wire Gas Solid Wire!
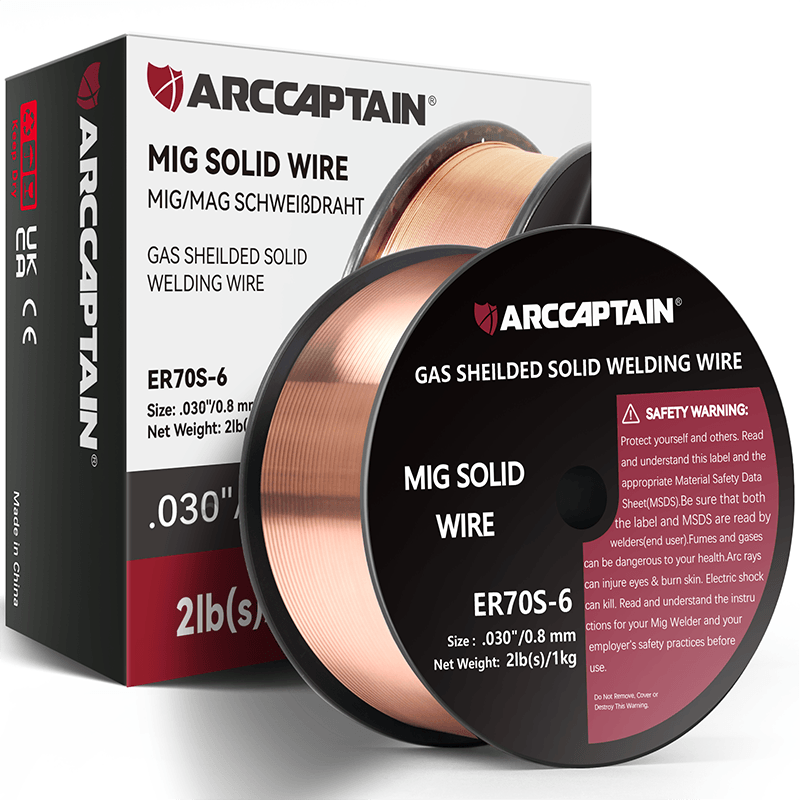
Comparison and Uses of Flux-core and Solid MIG Welding Wire
Flux-core wire and solid MIG welding wire have different compositions and structures, leading to variations in their welding applications. Understanding the differences can help welders choose the right type of wire for their specific project needs.
Composition and Structure
Flux-cored MIG welding wire consists of a hollow tube filled with flux materials. This flux helps protect the molten weld pool from contaminants and can provide additional deoxidizers to improve the quality of the weld.
On the other hand, solid MIG welding wire is made from a single piece of metal, typically mild steel, stainless steel, or aluminum. The composition and structure play a crucial role in determining how well the welding wire performs during the welding process and its suitability for different types of metal.
The composition and structure of MIG welding wires directly impact factors such as their tensile strength, ductility, resistance to corrosion, and overall performance during welding.
Welding Applications
Now, let's delve into the practical side of MIG welding wire – its applications. The solid MIG welding wire excels in clean and smooth welds on thin materials like stainless steel and aluminum.
It's also your go-to for automotive repairs, robotics, and general fabrication due to its precise control. Conversely, flux-core wire is a boon for outdoor work or windy conditions due to its self-shielding properties, making it ideal for structural steel fabrication and heavy equipment repair.
Additionally, gas-shielded flux-cored arc welding (FCAW) wires are perfect for industrial manufacturing because they provide high deposition rates.
When working with composite GMAW (metal-cored) wires or aluminum MIG wires – both renowned for their crack-resistant properties – you'll find them commonly used in shipbuilding and aerospace applications where extreme precision is required.
Other Types of MIG Welding Wire
Composite GMAW (metal-cored) wire, gas-shielded flux-cored arc welding (FCAW) wire, and aluminum MIG wires are also commonly used in welding applications. Each type has its own unique properties and uses that cater to specific welding needs.
Composite GMAW (metal-cored) Wire
Composite GMAW (metal-cored) wire combines characteristics of both flux-core and solid MIG welding wires. It has a tubular design with a metal sheath and core materials, offering high deposition rates and good penetration.
This type of welding wire is known for its low spatter levels, smooth arc transfer, and excellent weld bead appearance. It's suitable for welding thicker materials where higher travel speeds are required, making it a versatile choice for industrial applications across various materials like carbon steel, stainless steel, or aluminum alloys.
The unique composition of composite GMAW (metal-cored) wire provides better wetting action to the weld joint along with improved resistance to burn-through on thinner metals. With its ability to produce high-quality welds efficiently, this type of welding wire is popular among professional welders looking for increased productivity and superior welding performance in their projects.
Gas-shielded Flux-cored Arc Welding (Fcaw) Wire
Gas-shielded flux-cored arc welding (FCAW) wire is designed for high-strength welding and works well with thick materials. It has a tubular design filled with flux, protecting the weld pool from contaminants.
This wire is ideal for outdoor welding due to its resistance to wind and other atmospheric elements.
The gas shield protects the molten weld metal as it solidifies, reducing the chances of imperfections in the finished weld. FCAW wire is versatile, suitable for various materials including stainless steel and carbon steel.
Aluminum MIG Wires
Aluminum MIG wires are used for welding aluminum and aluminum alloys. These wires are designed to work with the metal inert gas (MIG) welding process, where an electric arc forms between the wire electrode and the metal being welded.
The composition of aluminum MIG wires is specially formulated to match the properties of aluminum, ensuring strong and durable welds.
Unlike other types of MIG welding wire, such as flux-core or solid wire, aluminum MIG wires require a shielding gas like argon or helium to protect the molten weld pool from contaminants in the air during the welding process.
This helps produce clean, high-quality welds on aluminum materials, making them suitable for various applications in industries like automotive manufacturing, aerospace, and construction.
Factors to Consider When Choosing MIG Welding Wire
When choosing MIG welding wire, factors such as the material being welded, thickness of the material, and welding environment must be considered. Additionally, the desired weld strength and welding method will also play a crucial role in selecting the right type of welding wire.
Material Being Welded
Consider the material being welded when choosing MIG welding wire. Match the wire to the material, such as stainless steel wire for stainless steel and aluminum alloy wire for aluminum.
The type of metal affects the weld strength and quality, so select the welding wire accordingly. When selecting MIG welding wire, always consider the material being welded to achieve strong and reliable welds.
Welding Method
The type of MIG welding wire you choose is also influenced by the welding method. Different welding gun methods require specific types of wire for optimal results. The choice of wire will depend on whether you are using metal inert gas (MIG) or flux-cored arc welding (FCAW).
Each method has its own requirements, and selecting the right type of MIG welding wire to match your welding method is crucial in achieving strong, durable welds.
It's important to understand that the characteristics and performance of the MIG welding wire can be affected by the specific welding method being employed. Whether it's metal inert gas (MIG) or flux-cored arc welding (FCAW), ensuring that you select the appropriate type of wire for your chosen method is essential for successful welds that meet your quality standards.
Thickness of Material
When choosing MIG welding wire, consider the thickness of the material. Thicker materials require more heat and weld penetration. For thicker materials, a higher voltage setting and a thicker MIG wire diameter are usually needed to provide enough filler metal for the weld.
Thinner materials need less heat to avoid burn-through or warping. Use a lower voltage setting and thinner MIG wire diameter for thinner materials to achieve better control over the weld pool and prevent excessive heat input.
Adapting the MIG welding wire to the thickness of the material ensures proper fusion and strength in your welds while reducing the risk of defects like lack of fusion or excessive spatter.
Welding Environment
The welding environment also plays a vital role in choosing the right MIG welding wire. Factors such as the presence of oxygen, nitrogen, and other atmospheric elements can affect the welding process.
For instance, when welding outdoors or in drafty areas, flux-core wire is often preferred since it provides better protection against atmospheric contamination compared to solid MIG welding wire.
Additionally, the cleanliness of the work area and proper ventilation are essential for maintaining weld quality.
Moreover, humidity levels in the welding environment can impact the performance of certain types of MIG wires. High humidity may require adjustments to voltage settings and gas flow rates to ensure optimal weld results.
Desired Weld Strength
Before selecting the MIG welding wire, consider the desired strength of the weld. The strength depends on the material being welded and its application. Factors such as tensile strength, yield strength, and elongation need to be evaluated based on the specific requirements of your project.
Understanding these factors will help you choose the right welding wire for achieving the desired weld strength.
Aspects like ductility, toughness, and hardness play a crucial role in determining the overall performance of a weld in different applications. It's important to select a welding wire that aligns with these criteria to ensure optimal weld quality and durability for your projects.
Conclusion
In conclusion, understanding the different types of MIG welding wire is essential for welders. By knowing the primary types - flux-core and solid MIG welding wire - and their uses, you can select the right one for your specific welding needs.
Considering factors such as material being welded, thickness, and environment helps in making a practical and efficient choice. Have you considered how these strategies could optimize your welding process? Applying this knowledge can lead to improved welding efficiency and high-quality results.
Explore further resources to deepen your understanding of MIG welding wire types and make informed choices in your welding projects.
Frequently Asked Questions
What is MIG welding wire?
MIG welding wire is a special filler wire that feeds through the welding gun during metal inert gas (MIG) welding.
How many types of MIG welding wires are there?
There are two main types: solid carbon steel wire for gas metal arc welding and flux core welding wire, which includes both gas-shielded and self-shielded options.
What does flux cored mean in MIG welding?
Flux cored means the wire has a core filled with materials that prevent rust and help the metal flow better when molten.
Can you use any type of wire for all MIG welding jobs?
No, you need to choose the right kind based on your job. Each type of welder's electrode or filler material works best for different kinds of metals and conditions.
Why do welders need different types of MIG wires?
Different wires provide better results on various metals or in unique environments because they have special properties like more strength or flexibility, helping craft high-quality welds with suitable tools and technology.