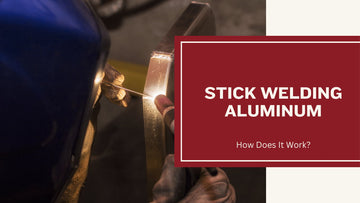
Many people ask if you can stick weld aluminum. The answer is yes, but it is much trickier than welding steel. You need special aluminum electrodes, the correct settings, and good surface prep for a solid weld.
Stick welding aluminum is more challenging because the metal conducts heat quickly and forms an oxide layer that can compromise your weld.
This guide will show you the basics, share tips for success, and help you determine when stick welding aluminum is the best choice or when another welding method is more suitable.
Quick Insights ⚡:
- Stick welding aluminum is possible but challenging due to oxide and low melting point
- Requires special aluminum electrodes (commonly E4043) and DCEP polarity
- Clean aluminum thoroughly before welding with a stainless‑steel brush
- Maintain tight arc control and appropriate amperage
- Practice multi‑pass fast runs rather than building a bead
Can You Stick Weld Aluminum?
Yes, you can stick weld aluminum, but it comes with serious challenges and limitations. Stick welding is more suitable for thick aluminum sections and repair work, rather than precision jobs.
Is Stick Welding Aluminum Practical?
Stick welding aluminum is possible but not your best choice. You can make it work, but expect more difficulties than with steel.
When stick welding aluminum works:
- Thick aluminum sections (1/4 inch or thicker)
- Field repairs where other equipment isn't available
- Situations where you only have a stick welder
When to avoid it:
- Thin aluminum sheets
- Precision work requiring clean, attractive welds
- Projects where weld quality is critical
TIG welding gives you the best results for aluminum. MIG welding comes in second place. Stick welding ranks last among the three main options.
The finished welds often look rough compared to TIG or MIG welds. You'll need special aluminum electrodes, which cost more than regular steel rods.
Your success depends heavily on your skill level and experience. Beginners will often find aluminum stick welding to be very frustrating.
Why Is Stick Welding Aluminum Difficult?
Aluminum creates several problems that make stick welding much harder than working with steel.
1. Heat dissipation issues:
- Aluminum conducts heat five times faster than steel
- Heat spreads away from your weld zone quickly
- You need higher amperage settings to maintain proper heat
- Arc control becomes much more difficult
2. Oxidation problems:
- Aluminum forms a tough oxide layer when exposed to air
- Aluminum melts at 1,220°F but aluminum oxide melts at 3,700°F
- This oxide prevents proper fusion between the base metal and filler
- You must clean the aluminum thoroughly before welding
3. Electrode challenges:
- Aluminum electrodes burn much faster than steel rods
- The flux coating can cause porosity in your welds
- Electrode storage requires special care to prevent moisture absorption
- Limited electrode options compared to steel welding
4. Current requirements:
- Aluminum needs AC current for best results
- Many basic stick welders only provide DC current
- DC welding is possible but produces lower quality results
Best Electrodes for Stick Welding Aluminum
For stick welding aluminum, the E4043 electrode is a good, all-purpose choice. It produces a steady arc, less spatter, and low fumes, making it suitable for many jobs.
You can find E4043 electrodes in various sizes, but 1/8 inch is the most popular choice for most people. Just remember to keep them dry because they can absorb moisture from the air.
Store them in a sealed container or a dry location to ensure they function properly when you weld.
Check Out Related Product:
ARCCAPTAIN ER4043 Aluminum Welding Wire
- Smooth Welding: Delivers a stable arc for easy control and a clean weld bead, great for both pros and hobbyists.
- ER4043 Aluminum Wire: Made with 5% silicon for reliable, easy MIG welding.
- Wide Use: Works with aluminum grades 3003, 3004, 5052, 6061, 6063, and casting alloys 43, 355, 356, and 214.
- Melting Point and Density: Melts at 1065–1170 °F, density is 0.097 lbs/in³, and turns gray after anodizing.
- Specs: Sold in 1 lb spools, 0.030 or 0.035 inch diameters, ready for any welding project.
How to Store Aluminum Electrodes
➝ Keep them completely dry because moisture destroys the flux coating on aluminum electrodes. Water causes the flux coating to break down, resulting in poor welds with numerous defects.
Store your aluminum rods in a sealed container with desiccant packs. A dry storage cabinet works even better if you have one.
➝ Use aluminum electrodes within 6 months of opening the package. These rods go bad much faster than steel welding rods because aluminum reacts with air and moisture.
Check the manufacture date before buying. Old stock sitting on shelves may already be damaged.
➝ Store at room temperature in a clean, dry place. Avoid temperature swings that cause condensation. Keep the original packaging until you're ready to use the rods.
Mark your containers with the date you opened them. This helps you use older rods first and avoid waste.
Read More: What Welding Rod to Use: A Beginner’s Guide
How to Stick Weld Aluminum: Step-by-Step

Stick welding aluminum requires careful preparation and precise technique. Clean surfaces, proper welder settings, and fast travel speeds are essential for strong welds.
1. Prepare the Aluminum
Clean the metal surface thoroughly. Use a stainless steel brush specifically designed for aluminum. Regular steel brushes will contaminate the aluminum and ruin your weld.
Remove all oxidation and dirt. Aluminum forms a thin oxide layer that blocks good welds. Clean with acetone or a specialized aluminum cleaner to remove oils and oxidation.
Beveled thick joints. For aluminum over 1/4 inch thick, grind a V-groove to help the weld penetrate properly. Make the groove about 60 to 90 degrees wide.
Fit pieces tightly together. Leave no gaps between the metal pieces. Aluminum expands when heated, so tight fit-up prevents problems during welding.
2. Preheat (If Needed)
Preheat thick aluminum to 200-300°F. This step helps prevent cracking and improves weld quality. Use a torch or heating pad to warm the metal evenly.
Skip preheating for thin metal. Aluminum under 1/8 inch thick does not need preheating. Too much heat will burn through thin material.
Check the temperature with a thermometer or a crayon. Heat the area around your weld joint, not just one spot. Even heating prevents warping and stress cracks.
3. Set Up Your Welder
Use DC reverse polarity (DCEP). This setting gives better penetration and arc stability with aluminum electrodes. Check your welder manual to set this up correctly.
Set higher amperage than steel welding. Aluminum needs about 20% more heat than steel.
Use these settings:
- 1/8 inch electrode: 80-120 amps
- 5/32 inch electrode: 120-160 amps
- 3/16 inch electrode: 160-220 amps
Choose the right aluminum electrode. Use E4043 rods for general welding or E5356 for stronger joints. Keep electrodes dry in a heated rod oven.
4. Welding Technique
Travel fast to prevent burn-through. Move the electrode quickly across the joint. Aluminum conducts heat fast, so slow travel will create holes in your work.
Keep a short arc length. Hold the electrode tip close to the work, almost touching. This reduces contamination and gives better control.
Use a straight welding motion. Do not weave side to side like with steel. Move in a straight line along the joint for best results.
Listen for the right arc sound. A good aluminum weld sounds like bacon frying. Crackling or popping means your settings need adjustment.
Clean between passes. Remove flux residue with a wire brush before making additional weld passes. Left-over flux will contaminate new welds.
Best Stick Welders You May Also Like
Common Problems & Solutions
Stick welding aluminum creates specific challenges that can lead to weak or flawed welds. The most frequent issues include gas bubbles forming in the weld metal, cracks developing along the joint, and incomplete bonding between materials.
1. Porosity (Bubbles in Weld)
Porosity appears as small holes or bubbles throughout your weld. This happens when gases get trapped in the molten aluminum as it cools.
Main causes include:
- Moisture on the base metal or welding rod
- Oil, dirt, or grease on the aluminum surface
- Using old or contaminated electrodes
- Inadequate preheating
Solutions to prevent porosity:
- Clean the aluminum with acetone or degreaser before welding
- Store electrodes in a dry place or rod oven
- Preheat the aluminum to 300-400°F before starting
- Use fresh welding rods that haven't absorbed moisture
- Remove any paint, oxidation, or coatings from the weld area
Always wire brush the aluminum right before welding. Even a few minutes of air exposure can create new oxidation that causes porosity problems.
2. Cracking
Cracks can form either during welding or after the metal cools. Aluminum expands and contracts quickly due to temperature changes.
Why does cracking occurs:
- Rapid cooling of the weld area
- High stress from thermal expansion
- Incorrect filler metal selection
- Welding too fast without proper heat control
Prevention methods:
- Preheat thick aluminum sections to 200-400°F
- Use a heat blanket or place the welded piece in sand to slow cooling
- Select the correct aluminum welding rod for your base metal
- Maintain steady travel speed and consistent heat input
- Allow gradual temperature reduction over several hours
For thick pieces over 1/4 inch, always use preheating. This reduces the temperature difference between the weld and the surrounding metal.
3. Poor Fusion
Poor fusion means the weld metal doesn't properly bond with the base aluminum. You'll see gaps or weak spots along the joint.
Common causes:
- The amperage is set too low for the material thickness
- Wrong electrode angle during welding
- Contaminated base metal surface
- Traveling too fast across the joint
How to achieve proper fusion:
- Increase amperage by 10-20 amps if fusion looks weak
- Maintain a 10-15 degree drag angle with your electrode
- Clean the joint area thoroughly before welding
- Slow down your travel speed to allow deeper penetration
- Watch for a bright, fluid weld puddle that wets out properly
Good fusion creates a smooth transition between the weld and base metal. If you see distinct lines or gaps, your heat input needs adjustment.
Pros and Cons of Stick Welding Aluminum
Stick welding aluminum has both benefits and drawbacks. Understanding these concepts will help you determine if this method is suitable for your project.
Benefits:
- No shielding gas needed - You can weld outdoors without worrying about wind blowing away protective gas
- Very portable - Stick welders are lighter and easier to move than TIG or MIG setups
- Works on dirty surfaces - You can weld over rust, paint, or light oxide layers without perfect cleaning
- Lower cost - Stick welders cost less than TIG or MIG equipment
- Good for field repairs - Perfect for construction sites and remote locations
Drawbacks:
- Messy weld appearance - The finished welds look rough and need cleanup work
- Slower process - Takes more time than TIG or MIG welding methods
- Not suitable for thin aluminum - Only works well on aluminum thicker than 1/8 inch
- Inconsistent results - Weld quality varies more than in other welding types
- Poor for detailed work - Not suitable when you need clean, precise welds
- Requires experience - Harder to learn than other aluminum welding methods
Stick welding is most effective for repairing thick aluminum in outdoor settings. It struggles with thin materials and projects that need attractive finished welds.
Also Read: Can You Weld A356 Aluminum? Techniques for Successful Joining
When to Stick Weld Aluminum and When to Choose Else

Stick welding is most effective on thick aluminum pieces. You should use it for repairs on cast aluminum parts, heavy frames, and trailer work. The process handles thick plate aluminum well.
Best situations for stick welding aluminum:
- Repairing thick aluminum rafters and structural frames
- Working on trailer components and heavy equipment
- Fixing cast aluminum parts like engine blocks
- Outdoor repairs where portability matters
- When you only have stick welding equipment available
Stick welding struggles with thin aluminum sheets. The heat is difficult to control and can easily burn through thin metal.
Choose TIG welding when you need:
- Clean, smooth weld appearance
- Precise control on thin materials
- High-quality joints for critical applications
- Professional-looking results
Pick MIG welding for:
- Faster welding on medium thickness aluminum
- Good balance of speed and quality
- Less skill required than TIG welding
- Production work with consistent results
Stick welding aluminum gives rough, messy welds. The finished joints appear less attractive than those produced by TIG or MIG welding. You also get more spatter and cleanup work.
Use stick welding only when other methods are not available. It works for basic repairs and thick materials.
For anything requiring strength, appearance, or precision, TIG and MIG welding give much better results.
Also Read: TIG Welding Aluminum Tips for Beginners
Final Thoughts
Stick welding aluminum requires patience and practice. You won't master it overnight, but you can learn the basics with time.
AC welders work best for aluminum stick welding. DC welders can work but make the job harder.
Choose the right electrode for your project:
- E4043 for general aluminum work
- E5356 for stronger welds on thicker material
Your technique matters more than expensive equipment. Keep a steady arc length and move at the right speed.
Preheat your aluminum pieces before welding. This prevents cracking and allows the weld to flow more smoothly.
Clean your metal well before you start. Remove all dirt, oil, and oxidation for good results.
Practice on scrap pieces first. Aluminum behaves differently than steel, so you need to adjust your approach.
Stick welding aluminum works great for field repairs and outdoor jobs. You can't always bring a TIG welder to remote locations.
For critical structural work, consider TIG or MIG welding instead. These methods give you better control and stronger welds.
Keep your workspace well-ventilated. Aluminum welding creates fumes that you shouldn't breathe.
Store your electrodes in a dry place. Moisture ruins aluminum welding rods quickly.
Your first attempts might look rough, but don't give up. Each weld teaches you something new about working with aluminum.
FAQs About Stick Welding Aluminum
Stick welding aluminum requires special aluminum electrodes and AC current settings. You'll need to reverse your polarity and adjust amperage based on material thickness for successful welds.
Can you stick weld aluminum without special rods?
No, you cannot stick weld aluminum without special aluminum electrodes. Regular steel welding rods will not work with aluminum.
You need aluminum-specific electrodes like E4043 or E4047. These rods contain aluminum alloys that match the base material.
Standard flux-coated steel rods create poor welds and contamination when used on aluminum. The chemistry is completely different between steel and aluminum welding.
Do you stick weld aluminum with AC or DC?
You should use AC (alternating current) when stick welding aluminum. AC provides the cleaning action needed to break through aluminum's oxide layer.
DC current can work but produces lower quality welds. AC current changes direction rapidly, which helps clean the aluminum surface during welding.
Most modern stick welders have AC output capability. Check your welder settings before starting your aluminum project.
What should I set my stick welder to for aluminum?
Set your stick welder to AC current for aluminum welding. Use 100-150 amps for thin aluminum around 1/8 inch thick.
Thicker aluminum requires higher amperage settings. Use 150-200 amps for material between 1/8 and 1/4 inch thick.
Start with lower settings and increase amperage if the arc won't start properly. Too much heat will burn through thin aluminum quickly.
Do you reverse polarity when stick welding aluminum?
Yes, you should use electrode positive polarity (reverse polarity) when stick welding aluminum with DC current. This sends more heat to the base metal.
However, AC current is the preferred choice for aluminum stick welding. AC alternates polarity automatically during the welding process.
If your welder only has DC output, use DC electrode positive (DCEP) for better penetration and cleaning action.
What's the best polarity for stick welding aluminum?
AC polarity works best for stick welding aluminum. The alternating current provides cleaning action that removes aluminum oxide during welding.
AC current switches between electrode positive and negative rapidly. This creates the ideal balance of heat and cleaning for aluminum welds.
If you must use DC, choose electrode positive polarity (DCEP). Avoid electrode negative polarity as it produces poor aluminum welds.