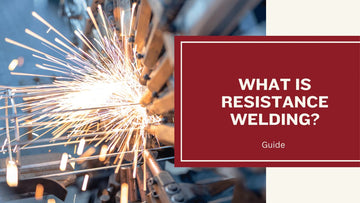
Resistance welding is a welding method that has been used in the industry for decades. It is a process where two metal parts are joined together by applying pressure and heat. The heat is generated by the resistance to the flow of electric current through the metal parts. The heat is then used to melt the metal parts, which are then joined together.
Resistance welding is a popular welding method because it is fast, efficient, and produces high-quality welds. It is commonly used in industries such as automotive, aerospace, and electronics. The process is also environmentally friendly because it does not produce any harmful gases or chemicals. Resistance welding is a reliable and cost-effective method that is widely used in the industry.
What is Resistance Welding?
Resistance welding is a welding process that uses electric current to join two metal pieces together. The process involves applying pressure and passing electric current through the metal pieces. The resistance of the metal generates heat, which melts the metal and creates a weld. Resistance welding is a popular welding method because it can produce high-quality welds quickly and efficiently.
Types of Resistance Welding
Resistance welding comes in a variety of forms, including butt, seam, and spot welding, each with its own applications. Every one of them has a unique welding application that makes it ideal for a given circumstance.
Here are the basic types of resistance welding:
1. Spot Welding
Spot welding is a type of resistance welding that is commonly used to join thin metal sheets together. The process involves applying pressure and passing electric current through two metal sheets that are held together by electrodes. The heat generated by the resistance of the metal causes the metal to melt and fuse together.
2. Seam Welding
Seam welding is a type of resistance welding that is used to join two overlapping metal sheets together. The process involves passing electric current through two metal sheets that are held together by electrodes. The heat generated by the resistance of the metal causes the metal to melt and fuse together, creating a continuous weld along the seam.
3. Projection Welding
Projection welding is a type of resistance welding that is used to join two metal pieces together at specific points. The process involves applying pressure and passing electric current through metal pieces that have raised projections on one or both sides. The heat generated by the resistance of the metal causes the metal to melt and fuse together at the projection points.
4. Flash Welding
Flash welding is a type of resistance welding that is used to join two metal pieces together by heating them to the melting point and then applying pressure to fuse them together. The process involves passing electric current through two metal pieces that are held together by electrodes. The heat generated by the resistance of the metal causes the metal to melt and fuse together.
5. Butt Welding
Butt welding is a type of resistance welding that is used to join two metal pieces together end-to-end. The process involves applying pressure and passing electric current through the metal pieces. The heat generated by the resistance of the metal causes the metal to melt and fuse together.
6. Upset Welding
Upset welding is a type of resistance welding that is used to join two metal pieces together by heating them to the melting point and then applying pressure to fuse them together. The process involves applying pressure and passing electric current through the metal pieces. The heat generated by the resistance of the metal causes the metal to melt and fuse together.
How Resistance Welding Works
Resistance welding is a process used to join metal pieces together. It's quite different from other welding methods like MIG or TIG. Here’s how it works, broken down into easy steps:
-
Applying Pressure:
- First, the metal pieces to be joined are firmly pressed together. This is usually done with special welding clamps or electrodes.
-
Passing Electricity:
- Next, a strong electric current is passed through the metals. This is done using electrodes that touch the metal pieces.
-
Generating Heat:
- The resistance of the metals to the electric current produces heat. This heat is what actually welds the pieces together.
-
Cooling Down:
- After the current is applied for a short time, it's turned off. The metal starts to cool and solidify, creating a strong weld.
-
Checking the Weld:
- Finally, the weld is checked for strength and quality. This ensures that the pieces are properly joined.
Resistance welding is efficient and fast, making it popular for manufacturing and industrial uses where many repetitive welds are needed. It's especially good for welding thinner metals.
Applications of Resistance Welding
Resistance welding is a widely used welding technique in various industries due to its high efficiency, low cost, and high-quality welds. In this section, we will discuss the applications of resistance welding in different industries.
Industrial Applications
Resistance welding is commonly used in industrial applications such as welding pipes and tubes, boilers, small tanks, and containers. It is an ideal welding technique for joining thin sheets of metal and for welding dissimilar metals. Resistance welding is also used in the production of wire products, such as wire mesh, and in the manufacturing of metal furniture.
Automotive Manufacturing
Resistance welding is extensively used in the automotive industry for welding body panels, frames, and other components. It is also used for welding fuel tanks, exhaust systems, and other parts that require a high-quality weld. Resistance welding is preferred in the automotive industry due to its fast cycle time, low heat input, and high repeatability.
Aerospace and Construction
Resistance welding is widely used in the aerospace and construction industries for welding aluminum and other lightweight metals. It is commonly used for welding structural components, such as frames, panels, and brackets. Resistance welding is preferred in these industries due to its high-quality welds, low heat input, and minimal distortion.
Overall, resistance welding is a versatile welding technique that is widely used in various industries. It offers many advantages over other welding techniques, including low cost, high efficiency, and high-quality welds. Whether you are in the automotive, aerospace, or construction industry, resistance welding can provide you with a reliable and cost-effective solution for your welding needs.
Materials and Equipment
Metals and Alloys
Resistance welding is a versatile process that can be used to join a wide range of metals and alloys. The most commonly welded metals include steel and stainless steel, but it is also possible to weld aluminum, copper, brass, and other alloys. The key to successful resistance welding is choosing the right material for the job. The material should have good electrical conductivity and be able to withstand the heat generated during welding.
Electrode Materials
The electrodes used in resistance welding are typically made of copper or a copper alloy. Copper is an excellent conductor of electricity and heat, which makes it ideal for use in welding applications. The electrodes can be shaped in a variety of ways to suit the specific welding task. For example, spot welding electrodes are typically shaped like pointed tips to create a small, concentrated weld.
Welding Equipment and Transformers
Resistance welding requires specialized equipment, including a welding transformer and a welding machine. The welding transformer is responsible for converting the electrical current from the power source into a high-voltage, low-current output that is suitable for welding. The welding machine controls the welding process and provides the necessary current and voltage to create a strong, reliable weld.
In addition to the transformer and welding machine, other equipment may be required depending on the specific welding application. For example, a water cooling system may be necessary to prevent overheating of the electrodes and workpiece. It is important to select the right equipment for the job to ensure a successful welding process.
Overall, resistance welding is a reliable and efficient method for joining metals and alloys. With the right materials and equipment, you can create strong, durable welds that will last for years to come.
Benefits of Resistance Welding
Resistance welding has several advantages that make it a popular choice in various industries. Here are some benefits of resistance welding:
-
Efficiency: Resistance welding is a fast and efficient process, which means that it can be used to produce a large number of products in a short amount of time.
-
Cost-effectiveness: Resistance welding is a cost-effective process because it requires less filler metal and flux compared to other welding methods.
-
Consistency: Resistance welding produces consistent and high-quality welds, which means that the products are more reliable and durable.
-
Environment-friendly: Resistance welding produces minimal pollution and does not require any hazardous materials, making it an eco-friendly process.
Limitations and Considerations
While resistance welding has several advantages, it also has some limitations and considerations that should be taken into account. Here are some limitations and considerations of resistance welding:
-
High-cost machinery: Resistance welding requires specialized equipment, which can be expensive to purchase and maintain.
-
Equipment cost: The cost of resistance welding equipment can be a significant investment for small businesses.
-
Pollution: While resistance welding produces less pollution compared to other welding methods, it still produces some emissions that can be harmful to the environment.
-
Filler metal and flux: Resistance welding requires filler metal and flux to be added to the weld, which can add to the cost of the process.
-
Extraneous materials: Resistance welding can be affected by extraneous materials, such as dirt or rust, which can affect the quality of the weld.
Overall, resistance welding is a popular and efficient welding method that has several benefits. However, it is important to consider the limitations and challenges of resistance welding before deciding to use it for a specific project.
Conclusion
Now that you have a better understanding of resistance welding, you can see how it plays an important role in the manufacturing and engineering industries. Resistance welding is a reliable and efficient way to join two pieces of metal together, and it is used in a variety of applications such as automotive, aerospace, and construction.
Some key points to remember about resistance welding include the fact that it uses heat generated by electrical resistance to join metals, and that there are several different types of resistance welding techniques such as spot welding and seam welding. It is also important to note that resistance welding requires proper equipment and training to ensure safety and effectiveness.
Overall, resistance welding is a valuable technique that should be understood by anyone involved in the manufacturing or engineering industries. By utilizing this technique, companies can improve their production processes and create high-quality products that meet the needs of their customers.
Frequently Asked Questions
What is meant by resistance welding?
Resistance welding is a type of welding process that joins two metal parts by applying pressure and heat to the area of the joint. The heat is generated by the resistance to the flow of electric current through the metal parts, which causes the metal to melt and fuse together.
Is TIG welding resistance welding?
No, TIG welding is not a type of resistance welding. TIG welding, also known as Gas Tungsten Arc Welding (GTAW), uses a non-consumable tungsten electrode to create an arc that melts the metal parts to be joined.
What is the most common resistance welding?
Spot welding is the most common type of resistance welding. It is used to join two or more metal parts together by applying pressure and heat to a specific spot on the parts. The heat is generated by the resistance to the flow of electric current through the metal parts, which causes the metal to melt and fuse together.
What is the difference between spot welding and resistance welding?
Spot welding is a type of resistance welding that joins two or more metal parts together by applying pressure and heat to a specific spot on the parts. Resistance welding is a broader term that encompasses various welding processes that use electric current to join two or more metal parts together. Spot welding is just one of the many types of resistance welding.