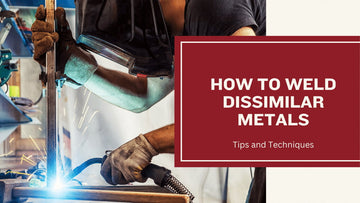
Welding is a widely used metal joining process due to its strength and simplicity. However, welding same-grade metals is much easier than welding dissimilar metals. Welding dissimilar metals requires an understanding of the chemical and physical properties of each metal to adapt the welding procedure for a successful weld.
To help you save time and effort, we have compiled a detailed guide on dissimilar metal welding. In this guide, you will learn about the challenges of welding dissimilar metals, the factors to consider before welding, and the common welding processes used.
Is It Possible To Weld Dissimilar Metals?
If you are a beginner in welding, you might wonder if it is possible to weld dissimilar metals. The answer is yes, but with certain precautions. Welding different metals comes with certain challenges, including differences in physical properties such as thermal conductivity and expansion, magnetic properties, metallurgical structure, and corrosion resistance. Nonetheless, welding has significantly advanced, and there are specific processes that will allow welding even the most different metals.
Crucial Factors To Consider Before Welding Dissimilar Metals
Before welding two dissimilar pieces, you should identify them and understand their physical, chemical, and mechanical properties. Most metals have their physical, chemical, and mechanical properties standardized by ASTM/ASME. For example, each austenitic stainless steel, such as 304 or 316, will have the same properties regardless of the manufacturer. However, in specific applications such as repair welding where you cannot precisely identify two pieces, you would have to perform a spark test, send a material sample to be analyzed, or consult with the original manufacturer or blueprints.
Once you understand the basic chemistry of dissimilar materials, you can make the strongest welds according to service conditions. The crucial factors to pay attention to are the physical properties, mechanical properties, and corrosion resistance of both pieces and the filler used to join them.
-
Physical Characteristics: The physical characteristics of the weld metal should be matched to the base metal. Different metals have different melting points and coefficients of thermal expansion. As a result, one can reach its melting point faster, then melt and flow away without fusing with the second piece. In addition, thermal expansion differences can make one piece extend more due to heat, leading to thermal cracking.
-
Mechanical Properties: When matching mechanical properties, the strength of the weld metal should be equal to or stronger than the weaker material. In certain applications, the American Society of Mechanical Engineers (ASME) code allows a weld strength of 95%. It is also desirable to match the ductility of the welded pieces, but it is not always possible.
-
Corrosion Resistance: Retaining good corrosion resistance of the weld is crucial in pipe welding or any application where welds might be subjected to corrosion. The corrosion resistance should be matched to the least resistant base metal in the weld. If the weld is subjected to saltwater, it should be more corrosion-resistant than both pieces to prevent galvanic corrosion.
Common Dissimilar Metal Welding Processes
Welding dissimilar metals can be successfully done with one of the fusion welding methods, non-fusion welding, or low-dilution welds.
-
Fusion Welding: This includes the most common arc welding methods, such as gas metal arc welding (GMAW or MIG), gas tungsten arc welding (GTAW or TIG), Stick welding, Submerged Arc Welding (SAW), or Flux core welding (FCAW). As a hobbyist, your go-to choices for dissimilar metals are MIG or TIG welding method. The MIG welding process is more straightforward, but with TIG, you can control the filler metal deposition perfectly, which is crucial in dissimilar metal welding.
-
Low-Dilution Methods: These are the electron beam welding process, laser welding, and pulsed arc welding. These are commonly used to join delicate and thin dissimilar metals with no added filler metal.
-
Non-Fusion Welding: This includes friction welding, explosion welding, diffusion bonding along with brazing and soldering. Non-fusion and low-dilution methods are commonly used in heavy production and specific industrial applications. On the other hand, you will be more than fine with fusion welding in your everyday DIY, home shop, or repair welding projects.
In conclusion, welding dissimilar metals is possible, but it comes with certain challenges. It is crucial to consider the physical properties, mechanical properties, and corrosion resistance of both pieces and the filler used to join them. With the right welding process and precautions, you can weld even the most different metals.
Guide On How To Weld Dissimilar Metals
When it comes to welding dissimilar metals, there are a few things that you need to keep in mind. In this section, we will discuss some of the most common types of dissimilar metal welding and provide some tips and tricks for each.
Welding Steel To Stainless Steel
Welding mild steel to stainless steel is one of the most common types of dissimilar metal welding. The biggest issue with this type of welding is that carbon can affect the biggest advantage of stainless steel - corrosion resistance. In addition, there are vast differences in the physical and mechanical properties of stainless and regular steel.
Challenges in Welding Steel to Stainless Steel
- Corrosion Resistance Issue: Carbon from mild steel can compromise the corrosion resistance of stainless steel.
- Physical and Mechanical Differences: Stainless and regular steel have vastly different properties.
To weld steel to stainless steel, you can use one of the common fusion welding methods, but typical choices are Metal inert gas (MIG) Welding and tungsten inert gas (TIG) welding. Carbon steels with less than 0.2% carbon can generally be welded with austenitic fillers without preheating. However, if the carbon content is greater than 0.3%, temperature control is crucial.
Welding Steel To Stainless Steel - Weld Preparation
Welding mild steel directly to stainless steel is not recommended since an exceptionally hard martensite phase of steel can occur. Martensite steel is prone to cracking, so welders usually bevel the pieces. Due to the nickel content in stainless steel, the root gap is larger, but the root face is reduced to promote wetting.
- Avoiding Martensite Formation: Beveling and adjusting root gaps are crucial to prevent cracking.
- Cleanliness is Key: Oil, grease, or contaminants can jeopardize the weld's integrity.
Specific pipeline applications may require joining galvanized steel and stainless steel. In that case, you must thoroughly remove the zinc coating. Burning zinc can cause liquid embrittlement, cracking, and toxic welding fumes, so cleaning it is crucial.
Welding Steel To Stainless Steel - Filler Metal Selection
The filler metal selection in steel to stainless steel joining will differ depending on applications and service condition temperatures.
- Service Conditions: Choose filler metal based on application and temperature.
- Common Choices: Type 309 or 312 for temperatures below 800°F; ERNiCr-3 or ENiCrFe-2/3 for higher temperatures.
Nickel alloy fillers have a coefficient of thermal expansion (COE) between ordinary steel and austenitic stainless, which helps them battle thermal fatigue failures that are more likely with 309 or 312 fillers.
Welding Steel To Stainless Steel - Shielding Gas Choice
When joining mild steel to stainless, you want to exclude reactive gases such as oxygen from the mixture. Oxygen can react with the atmosphere causing imperfections and defects in carbon steel, but you can replace it with small amounts of CO2, which is semi-reactive.
Important Note:
- Excluding Reactive Gases: Avoid oxygen in the mixture; small amounts of CO2 are preferable.
- Nitrogen Levels: Keep nitrogen low to prevent hot cracking.
Nitrogen in the mixture can decrease the ferrite content of the weld metal, which results in hot cracking. Therefore, you want to keep levels as low as possible.
Welding Steel To Stainless Steel - Battling Thermal Expansion Differences
Thermal conductivity and thermal expansion of stainless steel and mild steel are significantly different, and these differences are what make welding dissimilar metals challenging.
Thermal expansion is defined as the change in length per degree temperature to length. Mild steel has a lower coefficient of 5.9 (10-6 in/(in oF)) compared to common stainless steel with 9.4. As a result, stainless steel will change its length more than mild steel during the welding, which can lead to residual stress.
In addition, stainless steel takes more time to heat compared to steel, but it also needs more time to cool down. With thermal expansion differences, thermal stresses increase, leading to distortion.
Examples of Welding Combinations:
Steel Type | Stainless Type | Filler Metal | Shielding Gas | Preheating Temp. |
---|---|---|---|---|
Mild Steel | 304 Stainless | Type 309 | C25 Mix | None |
Carbon Steel | 316 Stainless | ERNiCr-3 | 100% Argon | 300°F |
Galvanized | 304L Stainless | Type 312 | C25 Mix | Remove Zinc Coating |
Final Thoughts
Successfully welding dissimilar materials requires a thorough understanding of the physical and mechanical properties of all materials involved, including the filler metal. Accurately matching these properties ensures a strong, reliable welded joint. To achieve this, you must carefully prepare the materials, select the appropriate equipment and filler material, use proper welding techniques, and apply post-weld treatment as needed. While it can be a challenging process, with the right approach and attention to detail, dissimilar material welding can be accomplished successfully.
Arccaptain Premium Welding Machines:
Frequently Asked Questions 🧐
What is the most suitable welding process for joining dissimilar metals?
The most suitable welding process for joining dissimilar metals depends on the metals being joined. However, fusion welding, which includes methods such as gas metal arc welding (GMAW or MIG), gas tungsten arc welding (GTAW or TIG), stick welding, submerged arc welding (SAW), or flux core welding (FCAW), is generally the preferred method.
Can carbon steel and stainless steel be welded together, and if so, which electrode is recommended?
Yes, carbon steel and stainless steel can be welded together. However, it is important to use a specific electrode, such as a 309L electrode, to ensure a strong bond between the two metals.
What are the considerations for preventing corrosion when welding dissimilar metals?
When welding dissimilar metals, it is important to consider the potential for galvanic corrosion, which occurs when two different metals are in contact with each other in the presence of an electrolyte. To prevent corrosion, it is recommended to use a filler metal that is as close as possible in composition to the base metal, and to avoid using dissimilar metals in wet or corrosive environments.
What is the purpose of using a 309 welding rod in dissimilar metal welding?
A 309 welding rod is commonly used in dissimilar metal welding because it is designed to weld stainless steel to other metals, including carbon steel. It also provides good resistance to cracking and corrosion.
How do you prepare dissimilar metals for welding to ensure a strong bond?
To prepare dissimilar metals for welding, it is important to remove any rust, dirt, oil, or other contaminants from the surface of the metal and welded joints. This can be done by grinding, sanding, or using a wire brush. It is also recommended to preheat the metals to reduce the risk of thermal shock and to ensure a strong bond.
Is it possible to stick weld different types of metals, and what are the limitations?
Yes, it is possible to stick weld different types of metals, but there are limitations. Stick welding is generally not recommended for dissimilar metal welding because it requires a specific electrode for each metal being welded, and the process can result in cracking and corrosion if not done correctly. It is also not suitable for thin metals or metals that require precise control of the heat input.