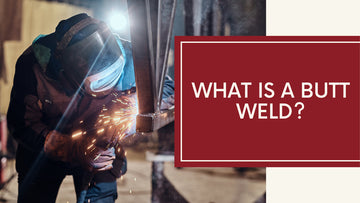
When you ask "what is a butt weld," you're referring to one of the simplest yet strongest types of welding joints. It connects two metal pieces end-to-end and is commonly used across various industries for its reliable strength.
Creating a butt weld involves heating the metal ends until they melt and then fusing them. This direct method forms a durable bond that can handle significant stress and strain.
For a successful butt weld, it's essential to align the metal pieces accurately. The welding technique, whether TIG welding, MIG welding, or stick welding, varies based on the metal types and the project's requirements. The right approach ensures a robust and enduring butt weld.
What is a Butt Weld - Basics of Butt Welding Explained
When it comes to joining two metal pieces together, butt welding is a popular method. This technique involves welding two metal pieces together at their ends, creating a butt joint. The resulting weld is known as a butt weld, and it is commonly used in a wide range of applications.
Butt Welding Definition and Types
Butt welding is a type of welding that involves joining two metal pieces together at their ends. The process involves heating the metal pieces to their melting points and then fusing them together. There are several types of butt welding, including:
- Gas Tungsten Arc Welding (GTAW)
- Gas Metal Arc Welding (GMAW)
- Shielded Metal Arc Welding (SMAW)
- Flux Cored Arc Welding (FCAW)
Each type of butt welding has its own advantages and disadvantages, and the choice of welding method will depend on the specific application.
Applications and Advantages of Butt Welding
Butt welding is commonly used in a wide range of applications, including:
- Automotive and Aerospace industries
- Construction and Infrastructure
- Manufacturing and Fabrication
- Shipbuilding and Offshore industries
One of the main advantages of butt welding is that it produces a strong, reliable joint that is capable of withstanding significant stress. Additionally, the joint is smooth and flush, which makes it ideal for applications where appearance is important.
In conclusion, butt welding is a popular method for joining two metal pieces together. By heating the metal pieces to their melting points and fusing them together, a strong, reliable joint is created. This technique is commonly used in a wide range of applications and offers many advantages over other welding methods.
Butt Welding Techniques
When it comes to butt welding, there are several techniques that you can use. Each technique has its own advantages and disadvantages, so it's important to choose the right one for your project. Here are some of the most common butt welding techniques:
Arc Welding Techniques
Arc welding is one of the most popular butt welding techniques. It involves heating the edges of the two pieces of metal until they melt and then fusing them together with an electric arc. Arc welding can be done using a variety of different methods, including stick welding, MIG welding, and TIG welding.
Resistance Welding Techniques
Resistance welding is another common technique used for butt welding. This method involves passing an electric current through the metal pieces, which heats them up and fuses them together. Resistance welding is often used in the automotive industry for welding sheet metal.
TIG Welding Techniques
TIG welding, or tungsten inert gas welding, is a precise and versatile butt welding technique. It involves using a non-consumable tungsten electrode to create the arc and a separate filler metal to fill the joint. TIG welding is often used for welding thin materials or materials that require a high level of precision.
MIG Welding Techniques
MIG welding, or metal inert gas welding, is a fast and efficient butt welding technique. It involves using a consumable wire electrode to create the arc and fill the joint. MIG welding is often used in the manufacturing industry for welding thicker materials.
No matter which butt welding technique you choose, there are a few things to keep in mind. First, make sure you choose the right welding process for your project. Second, make sure you use the right filler metal for the job. Finally, always follow proper safety procedures when welding, including wearing protective gear and working in a well-ventilated area.
Materials and Equipment Compatible with Butt Welding
Butt welding is a versatile welding technique that can be used to join a wide variety of metals. The most common metals that are compatible with butt welding include steel, copper, aluminum, and stainless steel. However, it is important to note that not all metals are compatible with each other. In some cases, dissimilar metals may require special welding techniques to ensure a strong and durable joint.
When selecting metals for butt welding, it is important to consider their physical properties, such as melting point, thermal conductivity, and coefficient of thermal expansion. Metals with similar properties are often easier to weld together, as they will expand and contract at similar rates during the welding process. This can help to prevent distortion and cracking in the weld.
Filler Materials and Electrodes
In addition to selecting the right metals, it is also important to choose the right filler materials and electrodes for butt welding. Filler materials are used to fill the gap between the two metal pieces being joined, while electrodes are used to create the arc that melts the metal and forms the weld.
The choice of filler material and electrode will depend on the type of metal being welded, as well as the specific welding application. For example, non-ferrous metals such as copper and aluminum may require different filler materials and electrodes than ferrous metals like steel and stainless steel. Additionally, nickel alloys may require specialized filler materials and electrodes to ensure a strong and durable joint.
Some common filler materials used in butt welding include:
- ER70S-6: A mild steel filler material commonly used in welding applications that require high strength and good ductility.
- ER4043: A filler material used in welding aluminum and other non-ferrous metals.
- ER309L: A filler material used in welding stainless steel and other high-alloy metals.
When selecting electrodes for butt welding, it is important to consider factors such as electrode diameter, polarity, and amperage. The specific electrode used will depend on the type of metal being welded, as well as the welding position and joint configuration.
Butt Welding Preparation and Process
When it comes to butt welding, preparation is key. The process involves joining two pieces of metal by heating them to their melting point and then allowing them to cool and solidify. Here are the three main aspects of preparation and process that you need to consider:
Groove Preparation
Groove preparation is the first step in creating a butt weld. The type of groove you need to prepare will depend on the type of joint you are creating. Common groove types include V-groove, U-groove, J-groove, bevel butt, square butt, and V-butt.
Before you begin welding, you need to clean the surfaces of the metal pieces thoroughly. Any dirt, rust, or other impurities can affect the quality of the weld. You can use a wire brush, grinder, or chemical cleaner to clean the surfaces.
Joint Configuration
The joint configuration is the way the two pieces of metal are positioned and aligned before welding. The joint configuration you choose will depend on the type of metal you are welding, the thickness of the metal, and the welding process you are using.
For butt welding, the joint configuration is a square edge. This means that the two pieces of metal are aligned in a straight line, with no overlap or gap between them.
Welding Parameters
Welding parameters refer to the settings you use on your welding equipment to create a successful weld. These settings include the type of welding process, the welding speed, the amperage, and the voltage.
The type of welding process you choose will depend on the type of metal you are welding and the thickness of the metal. Common welding processes for butt welding include MIG welding, TIG welding, and stick welding.
The welding speed, amperage, and voltage will depend on the type of metal you are welding, the thickness of the metal, and the welding process you are using. It is important to follow the manufacturer's recommendations for these settings to ensure a successful weld.
By taking the time to properly prepare your metal pieces and set the correct welding parameters, you can create a strong and durable butt weld.
Quality and Inspection
When it comes to butt welding, quality and inspection are crucial to ensure that the weld is strong and reliable. There are several common defects that can occur during the welding process, but with proper testing and standards, they can be avoided.
Common Defects and Solutions
Porosity is a common defect that can occur in butt welding. This is when small holes or voids are present in the weld, which can weaken its strength. To avoid porosity, it is important to ensure that the welding area is clean and free of any contaminants. Additionally, proper welding techniques and materials should be used to prevent porosity.
Full penetration is another important factor in butt welding. This refers to the depth of the weld, and it is important to ensure that the weld penetrates the entire thickness of the material being welded. Tack welds can be used to hold the material in place before the full weld is completed. It is also important to use the correct welding technique and materials to ensure full penetration.
Distortion is another common issue that can occur during butt welding. This is when the material being welded warps or changes shape during the welding process. To prevent distortion, it is important to use the correct welding technique and materials, as well as proper clamping and support to hold the material in place during welding.
Testing and Standards
To ensure the quality of a butt weld, various testing methods and standards can be used. The Testing and Standards section of the Welding Institute (TWI) provides guidelines for testing and inspection of welded joints. These guidelines include non-destructive testing methods such as radiography, ultrasonic testing, and magnetic particle inspection.
In addition to TWI standards, there are also industry-specific standards that must be followed. These standards ensure that the weld meets the required specifications for strength, durability, and safety.
In conclusion, quality and inspection are crucial in butt welding to ensure that the weld is strong and reliable. By following proper welding techniques, using the correct materials, and adhering to industry standards and testing methods, common defects such as porosity, full penetration, and distortion can be avoided.
Applications of Butt Welding
Butt welding is a popular method of joining two pieces of metal together. It is widely used in various industries due to its strength and durability. Here are some of the common applications of butt welding:
Industrial Piping Systems
Butt welding is widely used in industrial piping systems. It is used to join two pipes or pipe fittings together. Butt-welded pipe fittings such as elbows, tees, reducers, and flanges are commonly used in industrial piping systems. Butt welding provides a strong and leak-proof joint, which is essential for industrial piping systems that transport fluids and gases under high pressure.
Structural Frameworks
Butt welding is also used in the construction of structural frameworks. It is used to join two pieces of metal together to form a strong and durable structure. Butt welding is commonly used in the construction of buildings, bridges, and other structures. It provides a strong and stable joint that can withstand heavy loads and stresses.
Automotive Components
Butt welding is used in the manufacture of automotive components. It is used to join two pieces of metal together to form a strong and durable component. Butt welding is commonly used in the manufacture of exhaust systems, chassis, and other automotive components. It provides a strong and leak-proof joint that can withstand the high temperatures and pressures generated by the engine.
In conclusion, butt welding is a reliable and efficient method of joining two pieces of metal together. It is widely used in various industries due to its strength and durability. Whether you are working with pipes, building structures, or manufacturing automotive components, butt welding is an excellent choice for joining metal parts together.
Challenges and Innovations of Butt Welding
Butt welding can be a challenging process when it comes to thicker metals. When the thickness of the metal increases, it becomes more difficult to achieve proper weld penetration. This is because the heat from the welding process dissipates more slowly in thicker materials, making it harder to achieve the necessary temperature for proper fusion.
Sheet metal can also present challenges when it comes to butt welding. Due to its thinness, sheet metal is more susceptible to warping and distortion during the welding process. This can be mitigated by pre-heating the metal or using specialized welding techniques.
Advancements in Welding Technology
Advancements in welding technology have led to a number of innovations in butt welding. Automated welding systems can improve efficiency and accuracy, while high-energy beams can allow for faster and more precise welding.
Flash welding, flash butt welding, and resistance butt welding are all specialized forms of butt welding that can be used in specific applications. These techniques can offer advantages such as improved weld quality and reduced distortion.
Miter joints, which are commonly used in butt welding, can present challenges due to the need for precise alignment and root gap. However, advancements in welding technology have made it easier to achieve proper alignment and root gap, resulting in stronger and more reliable welds.
Overall, while butt welding can present challenges, advancements in welding technology have made it a more efficient and reliable process. By carefully considering the specific requirements of each application and utilizing the appropriate techniques and equipment, high-quality butt welds can be achieved with confidence.
Frequently Asked Questions
How do you differentiate between a square butt weld and a bevel butt weld?
A square butt weld is made by joining two pieces of material at a 90-degree angle with no bevel or angle cut into the edges. A bevel butt weld, on the other hand, is made by cutting an angle into the edges of the material to be joined. The angle can vary depending on the thickness of the material and the desired strength of the weld.
What are the characteristics of a high-quality butt weld?
A high-quality butt weld should have a smooth, consistent appearance with no visible cracks or voids. The weld should also be strong enough to withstand the stresses placed on it without breaking or deforming. Proper preparation of the material and precise welding techniques are key to achieving a high-quality butt weld.
Can you explain the process of flash butt welding?
Flash butt welding is a type of resistance welding that involves passing a high current through the material to be welded, causing it to heat up and melt. The two pieces of material are then pressed together under pressure, creating a weld. Flash butt welding is commonly used for joining rails and other large metal components.
What are the advantages of using a butt weld over other types of welding joints?
Butt welds offer several advantages over other types of welding joints. They are typically stronger and more durable than lap or fillet welds, and they require less material to create. Butt welds also provide a smooth, clean appearance that is ideal for applications where aesthetics are important.
In what applications is a butt weld typically used?
Butt welds are commonly used in applications where strength and durability are critical, such as in the construction of buildings, bridges, and other infrastructure. They are also used in the fabrication of machinery and other metal components.
How does the thickness of the material affect the choice of butt weld type?
The thickness of the material being joined can have a significant impact on the choice of butt weld type. For thinner materials, a square butt weld may be sufficient, while thicker materials may require a bevel butt weld to ensure adequate strength and durability. The angle of the bevel will also vary depending on the thickness of the material and the desired strength of the weld.