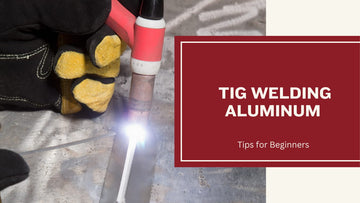
When it comes to welding aluminum, TIG welding, or Tungsten Inert Gas welding, is a highly precise method that welders use to join metals, and it’s particularly well-suited for working with aluminum. This type of welding involves using a tungsten electrode to produce the weld, while an inert gas like argon shields the weld from airborne contaminants.
Aluminum, known for its lightweight and strong properties, is a popular choice in industries ranging from automotive to aerospace. However, TIG welding aluminum comes with its own set of challenges. Unlike welding steel, aluminum’s high thermal conductivity and sensitivity to heat require a skilled hand and careful control. The process demands precision and patience, as even minor errors can lead to weak joints or weld contamination.
Despite its challenges, becoming good at TIG welding aluminum is very rewarding. It lets you make strong, yet light things and fix them too. In this guide, we'll teach you the important details of TIG welding aluminum. Whether you're just starting out or already know a lot about welding, learning to do this well is a great skill to have.
What is TIG Welding?
TIG welding is a popular welding process that uses a non-consumable tungsten electrode to produce a high-quality weld. TIG stands for Tungsten Inert Gas, which refers to the tungsten electrode and the inert gas used to protect the weld from contamination. This welding process is commonly used for welding aluminum, but can also be used on other metals such as stainless steel, copper, and brass.
TIG Welding Basics
TIG welding is an arc welding process that uses a constant current power supply to create an electric arc between the tungsten electrode and the workpiece. The arc creates heat, which melts the metal and creates a weld. The tungsten electrode does not melt during the process, so it is considered non-consumable.
It can be performed using either alternating current (AC) or direct current (DC). AC is used for welding aluminum because it helps to clean the oxide layer on the surface of the metal, while DC is used for welding other metals.
Properties of Aluminum in TIG Welding
Aluminum is a popular metal for TIG welding because it is lightweight, strong, and corrosion-resistant. However, aluminum can be difficult to weld because it has a high thermal conductivity and a low melting point. This means that the metal can quickly dissipate heat, making it difficult to maintain a consistent weld pool.
To overcome these challenges, TIG welding of aluminum requires a high level of skill and experience. The welder must use a high-frequency start to create a stable arc, and must maintain a consistent travel speed to prevent the metal from overheating.
Overall, TIG welding is a versatile and precise welding process that is commonly used for welding aluminum and other metals. With the right equipment and techniques, you can produce high-quality welds that are strong, durable, and corrosion-resistant.
Equipment and Materials to TIG weld Aluminum
When it comes to TIG welding aluminum, selecting the right equipment and materials is crucial to ensure a successful weld. Here are some key factors to consider when choosing your equipment and materials.
Choosing the Right TIG Welder
The TIG welder you choose should be capable of welding aluminum and have a high-frequency start feature to ensure a clean start to the weld. Look for a welder with at least 200 amps of power and a square wave AC output for optimal results. Make sure to choose a welder with a reliable cooling system to prevent overheating during extended use.
Choosing the Right Tungsten Electrode
When welding aluminum, it's important to choose the right tungsten electrode to ensure a clean and stable arc. A 2% thoriated tungsten electrode is a popular choice for welding aluminum due to its ability to maintain a sharp point and produce a stable arc. However, other options such as ceriated or lanthanated tungsten electrodes can also be used.
Selecting Filler Metals
Filler metals are used to fill the gap between the two pieces being welded together. For aluminum, a filler metal with a high silicon content is recommended as it helps to prevent cracking and produces a smooth, shiny finish. Look for a filler metal with a 4043 or 5356 designation for best results.
TIG Welding Torches
The TIG welding torch you choose should be specifically designed for aluminum welding. Look for a torch with a gas lens to provide better shielding and a larger cup size to help dissipate heat. Make sure to choose a torch with a flexible head to allow for easy access to tight spaces and angles.
Overall, choosing the right equipment and materials is essential to ensure a successful TIG welding project. With the right tools and a steady hand, you can achieve high-quality welds on your aluminum projects.
Steps on How to Weld Aluminum with a TIG Welder
Welding aluminum can be challenging due to its properties like high thermal conductivity and oxide layer. However, TIG (Tungsten Inert Gas) welding, known for its precision and cleanliness, is an excellent method for welding aluminum. Here are the steps on how to weld aluminum with TIG:Step 1: Safety First
Always wear appropriate safety gear, including a welding helmet, gloves, and flame-resistant clothing. Ensure your workspace is well-ventilated.
Step 2: Prepare the Aluminum
- Clean the Aluminum: Remove any dirt, oil, or oxide layer. Use a stainless steel brush (dedicated for aluminum) to brush the surface. Clean with acetone or a specialized aluminum cleaner.
- Cut and Fit the Pieces: If necessary, cut the aluminum to size and ensure a good fit before welding.
Step 3: Set Up Your TIG Welder
- Choose AC Mode: Set the welder to AC mode for aluminum.
- Balance Control: Adjust the AC balance control. A higher percentage of electrode negative (EN) cleans the oxide layer effectively.
- Amperage Setting: Set the right amperage based on the thickness of the aluminum.
Step 4: Prepare the Tungsten Electrode
- Select the Right Electrode: Pure or zirconiated tungsten electrodes are often used for aluminum.
- Grind the Electrode: Grind it to a point; this helps focus the arc.
Step 5: Start the Arc
- Tack Weld First: Make small tack welds to hold the pieces in position.
- Initiate the Arc: Step on the foot pedal to start the arc. Let the puddle form.
Step 6: Begin Welding
- Feed the Filler Rod: Introduce the filler rod to the weld pool at a 15 to 20-degree angle.
- Move Smoothly: Move the torch steadily along the seam. Maintain a consistent arc length and speed.
Step 7: Control Heat Input
Aluminum heats up quickly. Regulate the foot pedal to control the heat input, preventing warping or burn-through.
Step 8: Finishing Up
- Allow Cooling: Let the welded piece cool naturally. Do not quench as it may cause cracking.
- Clean the Weld: Clean any residue or oxidation formed during welding.
Step 9: Post-Weld Inspection
Examine the weld for any defects like cracks or porosity. A good aluminum weld should be clean and uniform.
Welding Process for Aluminum
When TIG welding aluminum, there are several important factors to consider in order to achieve a successful weld. In this section, we'll discuss the key aspects of the welding process, including controlling heat input, managing the weld puddle, and adjusting balance control.
Controlling Heat Input
One of the most critical aspects of TIG welding aluminum is controlling the heat input. This is because aluminum has a lower melting point than other metals, which means it can easily become overheated and melt away. To prevent this from happening, it's important to keep the heat input low and consistent.
To control the heat input, you should adjust the amperage on your welding machine. Start with a low amperage and gradually increase it until you find the right level for the thickness of the aluminum you're working with. You can also use a foot pedal to control the amperage while you're welding.
Managing the Weld Puddle
Another important factor in TIG welding aluminum is managing the weld puddle. The weld puddle is the molten metal that forms as you weld, and it's important to keep it under control to prevent it from spreading too far or becoming too hot.
To manage the weld puddle, you should keep the torch at a consistent angle and move it slowly and steadily along the joint. You should also use a filler rod to add material to the weld puddle as needed. This will help to maintain the shape and size of the weld puddle and prevent it from becoming too large or overheated.
Adjusting Balance Control
Finally, adjusting the balance control on your welding machine can help to improve the quality of your TIG welds on aluminum. The balance control adjusts the ratio of AC polarity between the electrode and the workpiece.
When welding aluminum, it's important to use more electrode-negative (EN) polarity, as this will help to clean the surface of the aluminum and prevent contamination. You can adjust the balance control to increase the amount of EN polarity and improve the quality of your welds.
By controlling the heat input, managing the weld puddle, and adjusting the balance control, you can achieve high-quality TIG welds on aluminum. With practice and experience, you'll be able to master these techniques and create strong, durable welds that will stand the test of time.
TIG Welding Aluminum Tips and Best Practices
When it comes to TIG welding aluminum, there are a few tips and best practices that can help you achieve a high-quality weld:
-
Cleanliness is key: Before you start welding, make sure that the aluminum is clean and free of any contaminants. This can be done by using a wire brush or grinder to remove any dirt, grease, or oxide layers.
-
Use the right technique: TIG welding aluminum requires a different technique than welding other metals. You should use a low amperage setting and a high frequency to create a stable arc. It is also important to maintain a consistent travel speed and keep the tungsten electrode pointed directly at the weld pool.
-
Choose the right filler metal: When welding aluminum, it is important to use a filler metal that is compatible with the base metal. 4043 and 5356 are two common filler metals for welding aluminum.
-
Preheat the aluminum: Preheating the aluminum can help prevent cracking and improve the overall quality of the weld. This is especially important when welding thicker sections of aluminum.
-
Use a gas lens: A gas lens can help improve gas coverage and reduce turbulence, resulting in a cleaner weld.
-
Practice, practice, practice: TIG welding aluminum can be challenging, so it is important to practice your technique on scrap pieces of aluminum before working on your final project.
By following these tips and best practices, you can achieve a high-quality TIG weld on aluminum and overcome common challenges that may arise during the welding process.
Welding Aluminum Common Mistakes and How to Avoid Them
Dealing with Porosity
Porosity is one of the most common problems encountered while TIG welding aluminum. It is the formation of small gas pockets within the weld, which can weaken the joint and cause it to fail. Porosity is caused by the presence of contaminants such as oil, grease, or moisture on the surface of the aluminum.
To avoid porosity, make sure to clean the aluminum thoroughly before welding. Use a wire brush or sandpaper to remove any dirt, oil, or grease from the surface. You can also use a solvent such as acetone to clean the surface.
Another cause of porosity is the presence of hydrogen in the weld. To prevent this, make sure to use a dry filler rod and keep the welding area dry. You can also use a preheating technique to reduce the amount of hydrogen in the weld.
Preventing Contamination
Contamination is another common problem encountered while TIG welding aluminum. It occurs when foreign materials such as dirt, oil, or grease get into the weld. Contamination can weaken the joint and cause it to fail.
To prevent contamination, make sure to clean the aluminum thoroughly before welding. Use a wire brush or sandpaper to remove any dirt, oil, or grease from the surface. You can also use a solvent such as acetone to clean the surface.
Another cause of contamination is the presence of oxygen in the weld. To prevent this, use a shielding gas such as argon to protect the weld from the atmosphere. You can also use a back-purging technique to remove any oxygen from the weld zone.
Peppering is another problem that can occur while TIG welding aluminum. It is the formation of small black spots on the surface of the weld. Peppering is caused by the presence of contaminants such as oil, grease, or moisture on the surface of the aluminum.
To prevent peppering, make sure to clean the aluminum thoroughly before welding. Use a wire brush or sandpaper to remove any dirt, oil, or grease from the surface. You can also use a solvent such as acetone to clean the surface.
In summary, to avoid common mistakes while TIG welding aluminum, make sure to clean the aluminum thoroughly before welding, use a dry filler rod, keep the welding area dry, use a shielding gas, and use a back-purging technique to remove any oxygen from the weld zone. By following these tips, you can achieve high-quality welds and avoid common problems such as porosity, contamination, and peppering.
Safety Considerations
When it comes to TIG welding aluminum, safety should always be your top priority. Here are some important safety considerations to keep in mind:
Welding Fumes
Welding fumes can be hazardous to your health, so it's important to take proper precautions when welding. Always work in a well-ventilated area or use a fume extractor to remove any harmful particles from the air. You should also wear a respirator to protect your lungs from inhaling any fumes.
Eye Protection
TIG welding aluminum produces intense light and heat, which can be harmful to your eyes. To protect your eyes, always wear a welding helmet with a shade level appropriate for the welding amperage you're using. You should also wear safety glasses underneath your helmet to protect your eyes from any debris that may fly up during welding.
Protective Clothing
Welding can be dangerous to your skin, so it's important to wear protective clothing to prevent burns and other injuries. Wear a welding jacket or apron made from flame-resistant material to protect your arms and torso. You should also wear welding gloves to protect your hands from the heat of the welding arc.
Argon Gas
Argon gas is commonly used in TIG welding aluminum to shield the weld from the air. While argon is not toxic, it can displace oxygen in the air and cause asphyxiation if you're working in a confined space. Always work in a well-ventilated area and avoid welding in areas with low oxygen levels.
By following these safety considerations, you can ensure that your TIG welding aluminum project is completed safely and successfully.
Advanced TIG Welding Topics
Welding Aluminum to Other Metals
Welding aluminum to other metals can be challenging due to the differences in melting points and thermal expansion coefficients. However, it is possible to weld aluminum to other metals such as steel and copper using TIG welding.
To weld aluminum to steel, you need to use a filler material that is compatible with both metals. The most commonly used filler material for this application is 4043 aluminum-silicon alloy. This filler material has a lower melting point than aluminum and can bond with steel without cracking.
Welding aluminum to copper requires the use of a copper-aluminum filler material. This filler material has a lower melting point than copper and can bond with aluminum without cracking. It is recommended to use a non-consumable tungsten electrode with a zirconiated tip for welding aluminum to other metals.
Using Alternating Current (AC) for Welding Aluminum
-
AC is Key for Aluminum: Alternating current (AC) is really important when welding aluminum. Normally, the AC output is set to 60 Hz, which is what we use for electricity in North America.
-
Higher Frequency for Better Stability: You can set a higher frequency than 60 Hz to make the welding arc more stable and prevent it from moving around too much.
-
Choosing the Right Electrode: Zirconiated tungsten electrodes are the best for this job. They can handle more current and the high heat of welding aluminum.
-
Starting and Controlling the Arc: Use a high-frequency start to get the arc going. Also, adjust the cleaning action of the electrode with something called balance control.
In short, welding aluminum, especially with AC, is an advanced skill in TIG welding. Using the right materials and settings, you can make great welds on aluminum with little distortion.
Optimizing Weld Quality and Productivity
When it comes to TIG welding aluminum, optimizing weld quality and productivity is essential. By following the right techniques and using the best equipment, you can achieve strong, ductile welds that offer excellent corrosion resistance and conductivity.
Increasing Weld Strength and Ductility
To increase weld strength and ductility, it's important to choose the right filler metal. 4043 and 5356 are popular choices for welding aluminum, with 4043 being the most commonly used. These filler metals offer excellent strength and ductility, and they also provide good corrosion resistance.
Another way to increase weld strength and ductility is to use a preheat. Preheating the aluminum before welding can help reduce the risk of cracking and improve the overall quality of the weld. However, it's important to use the right temperature and preheat time to avoid damaging the material.
Aluminum is already great at resisting corrosion and conducting electricity, but TIG welding can make these properties even better. Here's how:
-
For Better Corrosion Resistance:
- Pick the Right Filler Metal: Choose one that matches well with your aluminum and is known for its corrosion resistance. A popular choice is 5356, especially when you need really strong corrosion resistance.
-
For Improved Conductivity:
- Use the Right Welding Technique: Aim for a weld that's clean and even. This starts with good preparation of the aluminum before welding.
- Select a Conductive Filler Metal: Use one that enhances the aluminum's ability to conduct electricity.
In summary, with the correct filler metal and welding practices, you can make aluminum even more resistant to rust and better at conducting electricity through TIG welding.
Applications of TIG Welding Aluminum
TIG welding aluminum is a popular method of welding due to its ability to produce high-quality welds with good precision and control. Here are some common applications of TIG welding aluminum:
Aluminum GTAW
TIG welding aluminum is commonly referred to as Gas Tungsten Arc Welding (GTAW). This technique is ideal for welding aluminum because it produces a clean, precise weld that is free from defects. It is also the preferred method for welding thin aluminum sheets because it allows for greater control over the heat input.
Hobbyist
TIG welding aluminum is popular among hobbyists who enjoy DIY projects such as building custom cars, motorcycles, and bicycles. With the right equipment, hobbyists can produce high-quality welds that are both strong and aesthetically pleasing.
Modern Equipment
Modern TIG welding equipment has made it easier than ever to weld aluminum. With features such as AC/DC power sources, pulse welding, and digital controls, welders can produce high-quality welds with ease. Additionally, modern equipment has made it possible to weld aluminum in tight spaces, making it ideal for welding in confined areas.
Tight Spaces
TIG welding aluminum is ideal for welding in tight spaces because it produces a precise, clean weld that is free from defects. This makes it ideal for welding in areas where access is limited, such as inside engine compartments, under car frames, and in other confined spaces.
In conclusion, TIG welding aluminum is a versatile and effective method of welding that is ideal for a wide range of applications. Whether you are a hobbyist or a professional welder, TIG welding aluminum can help you produce high-quality welds that are both strong and aesthetically pleasing.
Conclusion
Therefore in TIG welding aluminum, it's evident that this skill is both challenging and immensely rewarding. We've covered everything from aluminum's unique properties to the precision needed in welding techniques, emphasizing the importance of preparation, temperature control, and using the right equipment to avoid contamination. Whether you're just starting out or are an experienced welder, remember that mastering TIG welding aluminum requires patience, practice, and a willingness to continually learn and adapt. Keep applying these insights in your projects, stay open to new methods, and embrace the evolving world of welding to enhance your skills further.
Frequently Asked Questions
Can you weld aluminum with a TIG welder?
Yes, you can weld aluminum with a TIG welder. TIG welding is one of the best methods for welding aluminum due to its precision and control. However, welding aluminum can be more challenging than welding steel due to its lower melting point and higher thermal conductivity.
Is AC or DC for TIG welding aluminum?
AC is typically used for TIG welding aluminum. This is because aluminum has an oxide layer that forms on the surface, and AC current helps to break down this layer and create a clean weld. DC can also be used for welding aluminum, but it may require more cleaning and preparation of the surface.
What rod I use for aluminum TIG welding?
When TIG welding aluminum, it is recommended to use a filler rod that matches the base metal as closely as possible. The most common filler rods for aluminum TIG welding are 4043 and 5356. 4043 is a softer rod that is easier to work with, while 5356 is stronger and more durable.
How many amps does it take to TIG weld aluminum?
The amount of amps needed for TIG welding aluminum depends on the thickness of the material being welded. As a general rule, you should use 1 amp for every thousandth of an inch of thickness. For example, if you are welding a piece of aluminum that is 1/8 inch thick, you would need around 125 amps. However, it is important to note that different factors, such as the type of aluminum and the welding technique, can affect the amount of amps needed.