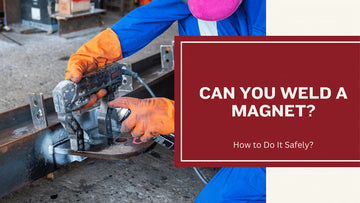
Wondering if you can weld a magnet? It's a common question, especially for those who often work with magnets. While welding typically joins metal pieces together, the scenario changes when one of those pieces is a magnet. It's not as simple as you might expect.
In this article, we’ll address the complexity of welding magnets. The key lies in understanding the type of magnet: permanent magnets, like those made of iron, nickel, or cobalt, and electromagnets, created by coiling wire around a core and electrifying it. The nature of the magnet you're dealing with plays a crucial role in determining if and how it can be welded. Let's dive into the details and clear up the confusion about welding magnets.
What is Magnetic Welding?
Magnetic welding is not a distinct welding technique, but rather a term used to describe the process of welding materials that possess magnetic properties. This form of welding typically involves magnetic metals, and while it isn't classified as a specific type of welding, it requires special considerations due to the magnetic nature of the materials involved.
Types of Magnetic Metals Involved
Common magnetic metals, such as certain varieties of steel and iron, are characterized by their ability to be attracted to magnets. These metals, known for their magnetic properties, play a significant role in various applications where magnetism is a key factor.
Magnetism and Welding Fundamentals
Magnetic Properties and Heat
When it comes to welding, the magnetic properties of the materials being welded can play a crucial role. Magnets can be classified into different types such as neodymium, alnico, ceramic, and ferrite. Each type of magnet has its unique magnetic properties that can affect the welding process.
One important factor to consider is the effect of heat on magnetic properties. High temperatures can cause a loss of magnetism in some materials, which can affect the strength of the magnet. This is particularly important when welding materials that are already magnets, as the heat from the welding process can cause the magnet to lose its magnetic properties.
Welding Techniques Impact on Magnet Properties
Understanding how different welding techniques affect magnet properties is key to successful welding involving magnets. Let’s delve into this:
1. Variety of Welding Techniques:
- Common Methods: AC, MIG, Arc, Stick, and TIG welding are widely used.
- Unique Effects: Each method impacts the magnetic properties of materials differently.
- Technique Selection: It's vital to pick the right method based on how it influences magnetism.
2. Choosing the Right Magnet for Welding:
-
Strength vs. Weldability:
- Neodymium Magnets: Known for their powerful magnetic field, but tricky to weld due to a high melting point and brittleness.
- Ceramic Magnets: Easier to handle in welding, thanks to a lower melting point and more flexibility.
3. Preserving Magnetic Qualities in Welding:
- Goal: Maintain the integrity of the magnet's magnetic properties during welding.
- Strategy: Selecting a welding technique that aligns with the magnet type.
4. Examples of Welding Techniques and Magnet Types:
Welding Technique | Magnet Type | Suitability | Key Considerations |
---|---|---|---|
TIG Welding | Neodymium | Less Suitable | Risk of demagnetization at high heat |
MIG Welding | Ceramic | More Suitable | Lower heat impact, easier handling |
Stick Welding | Neodymium | Moderately Suitable | Requires careful heat management |
In conclusion, a thorough understanding of magnetism's fundamentals and the nuances of various welding methods is essential when working with magnets. The right combination of welding technique and magnet type ensures the preservation of magnetic properties, leading to a high-quality final product.
ArcCaptain's High-Performance Welding Magnet Combination Set

-
Versatile Magnet Selection:
- Included in the Set: You get 4 magnets in total - 2 pcs with a 25lbs holding capacity and 2 pcs with a 55lbs capacity.
- For Varied Tasks: This mix is perfect for tackling a wide range of welding jobs.
-
For the Heavy-Duty Projects:
- The Powerhouse Addition: We’ve included a hefty 75-pound magnet for those more demanding projects.
- Comprehensive Set: This makes the set even more versatile and ready for any challenge.
-
Optimal Strength and Durability:
- Precision and Security: Each magnet is crafted to provide the strongest hold, ensuring your workpieces are precisely and securely positioned.
- Built to Last: Expect enduring performance from each magnet in the set.
-
Upgrade Your Welding Toolkit:
- Enhanced Efficiency: With ARCCAPTAIN's Welding Magnet Combination Set, your welding becomes more efficient and reliable.
- A Must-Have: An essential addition for anyone serious about welding.
Elevate your welding experience with the strength and reliability of ARCCAPTAIN's Welding Magnet Combination Set – your new partner in achieving flawless welds.
Challenges in Welding Magnets
Welding magnets can be a challenging task due to the unique properties of magnetic fields. Here are some of the challenges you may encounter when welding magnets.
1. Demagnetization Risks
One of the biggest risks when welding magnets is demagnetization. High temperatures can cause magnets to lose their magnetic field, which can render them useless. This is especially true for magnets made from materials like Alnico and Samarium Cobalt, which are more susceptible to demagnetization than other types of magnets.
To avoid demagnetization, it's important to use low-heat welding techniques and to avoid exposing the magnet to high temperatures for extended periods of time. Additionally, it's important to avoid exposing the magnet to strong magnetic fields during the welding process, as this can also cause demagnetization.
2. Impact of Heat on Magnetic Fields
The impact of heat on magnetic fields is another challenge when welding magnets. When a magnet is exposed to high temperatures, it can cause the magnetic field to weaken or even disappear. This can make it difficult to weld the magnet properly, as the magnetic field can interfere with the welding process.
To avoid this, it's important to use low-heat welding techniques and to avoid exposing the magnet to high temperatures for extended periods. Additionally, it's important to use welding techniques that minimize the impact of the magnetic field on the welding process.
3. Arc Blow Phenomenon
Arc blow is a phenomenon that occurs when the magnetic field of a magnet interferes with the welding process, causing the arc to deviate from its intended path. This can result in a poor weld and can also cause damage to the welding equipment.
To avoid arc blow, it's important to use welding techniques that minimize the impact of the magnetic field on the welding process. This can include using low-heat welding techniques, using welding techniques that minimize the impact of the magnetic field on the welding process, and using welding equipment that is designed to handle magnetic fields.
In conclusion, welding magnets can be a challenging task due to the unique properties of magnetic fields. To avoid demagnetization, minimize the impact of heat on magnetic fields, and avoid arc blow, it's important to use low-heat welding techniques, avoid exposing the magnet to high temperatures for extended periods, and use welding techniques and equipment that minimize the impact of the magnetic field on the welding process.
What to Do Before Welding a Magnet?
Before welding a magnet, it is important to consider a few factors to ensure the process is safe and effective. This section will cover two key areas to consider before welding a magnet: assessing metal and magnet compatibility and safety and precautionary measures.
Assessing Metal and Magnet Compatibility
The first step in welding a magnet is to assess the compatibility of the metal and magnet. Magnets are typically made of materials such as iron, cobalt, or nickel, which are all ferromagnetic metals. When exposed to high temperatures, these materials can lose their magnetic properties. Therefore, it is important to choose a welding method that will not damage the magnet or alter its magnetic properties.
Additionally, the metal being welded to the magnet must also be compatible. The two metals should have similar melting points and thermal expansion rates to prevent warping or cracking during the welding process. It is recommended to consult with a welding expert or manufacturer to ensure compatibility before beginning the welding process.
Safety and Precautionary Measures
Welding magnets can pose certain safety risks, so it is important to take precautionary measures to protect yourself and others. Before beginning the welding process, make sure to wear appropriate personal protective equipment (PPE), such as welding helmets, gloves, and aprons.
In addition, ensure that the welding area is well-ventilated to prevent the inhalation of harmful fumes. Welding magnets can also create sparks, so it is important to remove any flammable materials from the area and have a fire extinguisher nearby.
Finally, it is important to handle magnets with care before and after welding. Magnets can attract metal objects and can be difficult to separate once they are stuck together. It is recommended to keep magnets separated and use non-magnetic tools during the welding process to prevent accidents.
By considering metal and magnet compatibility and taking appropriate safety measures, you can successfully weld a magnet without damaging its magnetic properties or posing a safety risk.
Welding Procedures for Magnets
When it comes to welding magnets, it is important to follow the proper procedures to ensure a successful and safe weld. Here are some tips to help you weld magnets effectively.
Selecting the Right Welding Method
There are various welding methods available, but not all of them are suitable for welding magnets. DC welding is the most commonly used method for welding magnets. It is important to note that arc welding processes are not recommended for welding magnets, as they can cause magnetic interference.
Steps to Minimize Magnetic Interference
Welding magnets together can create magnetic interference, which can cause problems with electronic devices and other sensitive equipment. To minimize magnetic interference, it is important to take the following steps:
- Keep the welding area clear of any magnetic materials.
- Use non-magnetic clamps and fixtures to hold the magnets in place during welding.
- Weld the magnets in a demagnetized state to reduce the magnetic field.
It is also important to have experience with welding magnets before attempting to weld them. Welding magnets require a certain level of skill and knowledge to ensure a successful and safe weld.
In conclusion, selecting the right welding method and taking steps to minimize magnetic interference are crucial when welding magnets. By following these tips and having the necessary experience, you can successfully weld magnets together.
What to Do After Welding Magnets?
After welding a magnet, there are several post-welding processes that you should consider to ensure that the magnet performs optimally. This section will cover two important post-welding processes: dealing with welding defects and demagnetizing techniques.
1. Dealing with Welding Defects
Welding defects can occur during the welding process, and it is essential to identify and correct them to ensure that the magnet performs correctly. Some common welding defects include porosity, cracks, and incomplete fusion.
Porosity occurs when gas bubbles are trapped in the weld, resulting in voids. To prevent porosity, you should ensure that the welding area is free of moisture, oil, or other contaminants. Additionally, you should use the correct welding technique and filler material to prevent porosity.
Cracks can occur due to excessive heat or cooling rates, and they can weaken the magnet. To prevent cracks, you should use the correct welding technique and filler material, and control the heat input during welding.
Incomplete fusion occurs when the weld does not penetrate the base metal, resulting in a weak joint. To prevent incomplete fusion, you should ensure that the welding area is free of contaminants, and use the correct welding technique and filler material.
2. Demagnetizing Techniques
After welding a magnet, it is essential to demagnetize it to prevent any interference with other magnetic materials. There are several demagnetizing techniques available, including:
- AC Demagnetizing: This technique involves applying an alternating current to the magnet to reduce its magnetic field.
- DC Demagnetizing: This technique involves applying a direct current to the magnet to reduce its magnetic field.
- Mechanical Demagnetizing: This technique involves subjecting the magnet to a mechanical shock to reduce its magnetic field.
It is essential to choose the correct demagnetizing technique based on the magnet's size, shape, and material. Additionally, you should follow the manufacturer's recommendations for demagnetizing the magnet to avoid damaging it.
In conclusion, post-welding processes are essential to ensure that a welded magnet performs optimally. By identifying and correcting welding defects and demagnetizing the magnet, you can ensure that it operates correctly and does not interfere with other magnetic materials.
Can You Weld Magnets to Steel?
Welding magnets to steel is a topic that intrigues both professional welders and hobbyists. The concept of attaching a magnet, a material known for its magnetic properties, to steel, a ferrous and magnetic-responsive metal, raises several practical and scientific considerations.
The Feasibility of Welding Magnets to Steel
-
Material Properties:
- Magnets: Most magnets, especially strong ones like neodymium, are not made from materials that are traditionally weldable. They often consist of alloys that are sensitive to heat.
- Steel: Being a ferrous metal, steel is conducive to standard welding techniques.
-
Heat Sensitivity:
- The intense heat required for welding can demagnetize the magnet. The Curie temperature, the point at which a magnet loses its magnetic properties, can be easily exceeded in a typical welding process.
-
Alternative Methods:
- Given the challenges with direct welding, alternative methods like epoxy or mechanical fastening (screws, bolts) are often recommended for attaching magnets to steel.
- In industrial applications, specialized adhesives are designed to create strong bonds without compromising the magnetic properties.
While welding magnets directly to steel is not generally recommended due to the heat sensitivity of magnets and the risk of losing their magnetic properties, there are alternative methods to effectively attach these two materials. Using adhesives or mechanical fastening provides a viable solution, maintaining the integrity of the magnet while ensuring a secure bond to the steel.
Special Considerations for Different Magnet Types
When it comes to welding magnets, different types of magnets require different considerations. Here are some special considerations for two common magnet types:
1. Neodymium and Rare Earth Magnets
Neodymium magnets are the strongest type of permanent magnet, and they are made from rare earth metals. These magnets are commonly used in motors, generators, and other high-tech applications. When welding neodymium magnets, it's important to take special precautions to prevent damage to the magnet.
First, you should remove the magnet from any nearby magnetic fields to prevent interference. Next, you should clean the surface of the magnet to remove any dirt or debris. Finally, you should use a low-heat welding method to avoid demagnetizing the magnet.
2. Ceramic and Alnico Magnets
Ceramic and alnico magnets are two other common types of magnets. Ceramic magnets are made from a composite of iron oxide and barium or strontium carbonate, while alnico magnets are made from a combination of aluminum, nickel, and cobalt. These magnets are commonly used in speakers, sensors, and other applications.
When welding ceramic or alnico magnets, it's important to take special care to avoid damaging the magnet. These magnets are more resistant to heat than neodymium magnets, but they can still be damaged if exposed to high temperatures. You should use a low-heat welding method and avoid heating the magnet for extended periods.
By taking these special considerations into account, you can safely weld different types of magnets without damaging them.
How to Weld Magnets Safely?
Welding magnets can be tricky, but with the right approach, you can do it safely. Here's a straightforward guide:
Applications and Practical Tips
Welding Magnets in Motors and Generators
When it comes to welding magnets in motors and generators, it is important to consider the thickness of the material being welded. Thicker materials require stronger magnets or multiple magnets to ensure a secure hold during the welding process. Additionally, it is important to minimize or eliminate any cables or other objects that may interfere with the magnet's magnetic field.
When welding magnets in motors and generators, it is recommended to use arrow magnets or other welding clamp magnets to ensure a secure hold. These magnets are designed specifically for welding and provide a strong, reliable hold during the welding process.
Effective Use of Magnetic Clamps and Holders
Magnetic clamps and holders are essential tools for any welding project. When using these tools, it is important to consider the ampere rating of the magnet and ensure it is appropriate for the size and thickness of the material being welded.
It is also important to consider the type of magnet being used. Electromagnets can be more powerful than permanent magnets, but they require an electrical source to function. Permanent magnets, on the other hand, do not require an electrical source but may not be as powerful as electromagnets.
When using magnetic clamps and holders, it is important to ensure they are properly positioned and secured to prevent any movement during the welding process. Additionally, it is important to avoid using magnetic clamps and holders near any sensitive electronic equipment, as the magnetic field can interfere with their operation.
Overall, welding magnets can be a useful tool in many welding applications. By following these practical tips and guidelines, you can ensure a successful and efficient welding process.
Frequently Asked Questions:
What happens if you weld on a magnet?
Welding directly on a magnet typically results in the magnet losing its magnetic properties. The intense heat generated during the welding process can demagnetize the magnet, especially if it reaches the material's Curie temperature, at which point its magnetic domains lose alignment. This change is usually permanent, making the magnet ineffective post-welding.
Can you weld magnetic steel?
Yes, you can weld magnetic steel, but it requires specific techniques and considerations. The key challenge in welding magnetic steel is its tendency to become demagnetized or have altered magnetic properties due to the heat involved in the welding process. Therefore, specialized welding methods and careful control of heat input are essential for successful results.
Can you solder magnets together?
Direct soldering or welding to neodymium magnets is generally not recommended due to the high temperatures involved in these processes. Because neodymium magnets are formed of an alloy of neodymium, iron, and boron, they are prone to corrosion and degeneration when exposed to high temperatures.
Are welding magnets any good?
Yes, magnets are an excellent quick and easy way to position and hold metals in place for tack welding. Magnets are available in a variety of shapes and sizes, including 90-degree magnets for gripping corners and adjustable angle magnets for maximum adaptability.