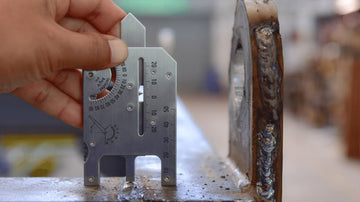
Bevel welds are a key part of building things with metal, making sure the pieces stick together well and stay strong.
Bevel welding is used when metal parts are too thick for a welding machine to penetrate directly. Creating a beveled edge allows the machine to reach and penetrate the entire thickness of the metal, leading to a stronger weld.
In this article, we're going to explore bevel welding, a method where the edges of the metal are cut into a slope to help the weld go deeper and hold better. You'll learn about the different kinds of bevel welds, what makes each one special, and where they're used.
We'll also look at the symbols used in welding to represent bevel welds, so you can understand the drawings and plans that use them.
Whether you're new to welding or know a bit about it, this guide will help you get to know more about bevel welds and how important they are.
What is a Bevel Weld?
A bevel weld is when you cut the edge of one piece to slant it into a V, U, or J shape before welding. This makes the welding area bigger so it can spread out the weight better, making a stronger joint.
You often see this kind of weld in big projects like bridges, buildings, and pipes, where the joints need to be really tough.
Bevel welds are also used to create a smooth and aesthetically pleasing finish on the welded joint. However, bevel welding requires more preparation and skill than other types of welding, as the edges of the workpieces must be carefully prepared to ensure a proper fit and alignment.
What are the Types of Bevel Weld Symbol?
There are different types of bevel welds, including single-V, double-V, single-U, and double-U. The type of bevel weld used depends on the thickness and type of the materials being welded, as well as the required strength of the joint.
For example, a single-V bevel weld is commonly used for butt joints in plates that are up to 3/8 inch thick, while a double-V bevel weld is used for thicker plates.
Let’s discuss different types of bevel welds:
Single Bevel Weld
The single bevel weld is created by preparing one of the two pieces of metal with a beveled edge. This type of weld is commonly used when one piece of metal is significantly thicker than the other.
It offers excellent penetration and is ideal for use in heavy-duty applications such as shipbuilding, construction, and pipelines.
Double Bevel Weld
A double bevel weld is created by preparing both pieces of metal with a beveled edge. This type of weld is often used when both pieces of metal are of equal thickness.
It offers excellent strength and penetration, making it ideal for use in applications such as bridges, pressure vessels, and heavy machinery.
J-Bevel Weld
The J-bevel weld is created by preparing one piece of metal with a beveled edge and the other with a straight edge. This type of weld is commonly used when one piece of metal needs to be joined to a flat surface. It offers good penetration and is ideal for use in applications such as automotive manufacturing, aerospace, and structural steelwork.
V-Bevel Weld
The V-bevel weld is created by preparing both pieces of metal with a V-shaped groove. This type of weld is commonly used when both pieces of metal are of equal thickness.
It offers excellent penetration and is ideal for use in applications such as shipbuilding, construction, and pipelines.
U-Bevel Weld
The U-bevel weld is created by preparing both pieces of metal with a U-shaped groove. This type of weld is commonly used when both pieces of metal are of equal thickness.
It offers excellent penetration and is ideal for use in applications such as pressure vessels, heavy machinery, and structural steelwork.
By understanding the different types of bevel welds and their applications, you can choose the right one for your specific needs. Whether you need excellent penetration, strength, or versatility, there is a bevel weld that can get the job done.
Bevel Weld Design
When designing a bevel weld, it is important to consider the type of joint and the structural integrity of the finished product. There are several factors to consider when designing a bevel weld, including groove welds and bevels, welding symbols and meanings, and beveling vs chamfering.
Groove Welds and Bevels
Groove welds are used to join two pieces of metal that are at an angle to each other. A V-shaped groove is commonly used for this type of weld, but other types of groove welds include square grooves, bevel grooves, and J-grooves.
The bevel angle is the angle between the surface of the metal and the edge that is being welded. The bevel angle can vary depending on the thickness of the metal and the type of joint being welded.
Bevel Weld Symbols and Meanings

In professional jobs, or even with advanced DIY welding kits, a welder might come across a bevel groove ready for welding. Documentation should include welding symbols for these specific joints.
These symbols guide the welder on which weld type to use for the best joint strength. The bevel weld symbol, looking like a tilted 'V', tells you it's a bevel weld.
Sometimes, the symbol shows that the joint edges need chamfering. If an edge needs this treatment, you'll notice a symbol with two arrows pointing at an angle, usually hovering above the joint, signaling where to bevel at an angle, often around 40 degrees.
Beveling vs Chamfering
Beveling and chamfering are two methods of preparing a metal surface for welding. Beveling is the process of cutting a groove into the metal surface, while chamfering is the process of cutting a beveled edge on the metal surface. Beveling is typically used for thicker metals, while chamfering is used for thinner metals.
Preparing for a Bevel Weld
Getting ready for a bevel weld means you've got to take a few important steps to make sure you do a good job. It's all about being prepared. Doing things right from the start helps make sure your weld is strong and lasts a long time.
Here are steps to prepare for bevel welding:
Step 1. Material Selection
The first step in preparing for a bevel weld is to select the right materials for the job. This includes choosing materials that are compatible with the welding process you will be using, as well as materials that are suitable for the specific application. For example, if you are welding two pieces of steel together, you will need to choose a steel filler material that is compatible with the base metal.
Step 2. Cleaning and Surface Preparation
Before you can begin welding, you will need to clean and prepare the surfaces of the materials that you will be joining. This involves removing any dirt, rust, or other contaminants that could interfere with the welding process. You may also need to grind or sand the edges of the materials to create a clean, smooth surface that will allow for a strong weld.
Step 3. Beveling
Once the surfaces of the materials are clean and prepared, you will need to create a bevel on the edges that will be joined. This involves cutting or grinding a sloped edge on the materials to create a V-shape or U-shape groove. The angle and depth of the bevel will depend on a variety of factors, including the thickness of the materials and the welding process you will be using.
Step 4. Fit-Up
After the bevels have been created, the materials will need to be fit together to ensure a tight, secure joint. This may involve clamping the materials in place or using other methods to hold them together while you weld. It's important to ensure that the materials are properly aligned and that there is no gap between them, as this can result in a weak weld.
If you stick to these steps, you'll make sure your materials are all set for a bevel weld. This careful prep means you'll end up with a weld that's top quality and lasts long. Plus, it'll help you dodge issues like cracking or metal warping, and stop other flaws from messing up your work.
Welding Machine Used for Bevel Welding
You can use a hand-held angle grinder to quickly shape the edges of flat bars and rods. For working with thicker metals, an automatic beveling machine is a good choice. These machines can cut into flat metal surfaces to create the right shape.
Some bevel machines stay in one place and are quick and safe to use, while others are made to move around. The portable ones often cost more because they're specially built to work fast and give you even edges every time.
When you want to practice your bevel welding before tackling big work, you can start with a small MIG welder or TIG welder that plugs into a regular outlet. MIG welding is great for joining thinner metals and is one of the most popular ways to weld.
Check out ArcCaptain best-seller MIG welder - ARCCAPTAIN MIG130 Best 3 in 1 110V Portable No Gas Flux Core Welder

Step-by-Step Guide to Bevel Welding
Bevel welding is a really important job in welding work. It's when you shape the edge of the piece you're going to weld into a slant. This makes it ready to join together with another piece.
Here is a step-by-step guide on how to perform a bevel weld:
Step 1: Choose the Right Tools
To perform a bevel weld, you'll need a few tools, including an angle grinder, a beveling machine, or a cutting torch. You'll also need protective gear such as gloves, a welding helmet, and a welding jacket.
Step 2: Prepare the Workpiece
Before you start beveling, prepare the workpiece by cleaning it thoroughly to remove dirt, rust, or any other debris. This step is crucial to ensure that the weld joint is strong and durable.
Step 3: Create the Bevel
Using the angle grinder or beveling machine, create a beveled edge on the workpiece. The type of bevel you create will depend on the joint design, welding process, and other factors. Some common bevel types include U, V, and J bevels.
Step 4: Fit the Workpieces Together
Once you've created the beveled edge, fit the workpieces together to ensure a tight fit. Use clamps or other fixtures to hold the workpieces in place during the welding process.
Step 5: Weld the Joint
With the workpieces in place, start welding the joint. Use the appropriate welding process and filler material for the job. Be sure to follow all safety procedures and guidelines when welding.
Step 6: Inspect the Weld
After welding, inspect the weld joint to ensure that it meets all quality standards. Look for any signs of defects or irregularities that could compromise the integrity of the weld.
By following these steps and best practices, you can perform a bevel weld that is strong, durable, and meets all quality standards.
What are the Common Bevel Weld Issues
Bevel welding is a common welding technique used in different industries, but it can come with its own set of challenges. Here are some common bevel weld issues and how to solve them:
Lack of Fusion
Lack of fusion is a common issue that occurs when the weld material fails to fuse with the base metal. This issue can occur due to insufficient heat input, incorrect welding speed, or incorrect electrode angle.
To solve this issue, you need to adjust the welding parameters such as the heat input, welding speed, and electrode angle to ensure that the weld material fuses with the base metal.
Porosity
Porosity is another common issue that occurs when gas pockets are trapped in the weld material. This issue can occur due to improper shielding gas, contaminated welding wire, or incorrect welding technique.
To solve this issue, you need to ensure that the welding area is properly cleaned, use the right shielding gas, and check the welding wire for contaminants.
Cracks
Cracks are a serious issue that can occur due to high levels of stress in the weld material. This issue can occur due to improper welding technique, incorrect electrode angle, or lack of preheating.
To solve this issue, you need to ensure that the welding technique is correct, use the right electrode angle, and preheat the welding area to reduce stress.
Undercut
Undercut is a groove-like depression that occurs in the base metal near the weld bead. This issue can occur due to incorrect welding technique, incorrect electrode angle, or excessive welding speed.
To solve this issue, you need to ensure that the welding technique is correct, use the right electrode angle, and adjust the welding speed to prevent undercut.
Distortion
Distortion is a common issue that occurs due to the heat generated during welding. This issue can occur due to incorrect welding technique, incorrect electrode angle, or lack of clamping. To solve this issue, you need to ensure that the welding technique is correct, use the right electrode angle, and clamp the welding area to prevent distortion.
By addressing these common bevel weld issues, you can improve your welding techniques and ensure that your welds are of high quality.
Beginner's Tips for Bevel Welding
Bevel welding is a process that requires precision and attention to detail. Here are some tips to help you get started:
1. Choose the Right Bevel Angle
The bevel angle is an essential aspect of bevel welding. It is the angle formed between the prepared edge of the material and the surface of the material.
The bevel angle should be chosen based on the thickness of the material being welded, the welding process, and the type of joint being welded. According to Material Welding, the bevel angle for a single bevel preparation should be between 40-50 degrees.
2. Use the Right Welding Technique
There are different welding techniques that can be used for bevel welding, including MIG, TIG, and Stick welding. Each technique has its advantages and disadvantages, and the choice of the technique will depend on the material being welded, the thickness of the material, and the type of joint being welded.
Welding Logic provides an overview of different welding techniques and their advantages and disadvantages.
3. Prepare the Material Properly
Preparing the material properly is crucial for successful bevel welding. The material should be cleaned and free of any rust, dirt, or other contaminants.
The edges of the material should be prepared by using a grinder or other cutting tools to create a bevel. The bevel should be smooth and free of any burrs or sharp edges.
4. Use the Right Welding Consumables
Using the right welding consumables is essential for successful bevel welding. The consumables should be chosen based on the welding technique being used, the material being welded, and the type of joint being welded.
For example, ArcCaptain recommends using a 70S-6 wire for MIG welding and an E7018 electrode for Stick welding.
5. Practice, Practice, Practice
As with any welding technique, practice is essential for mastering bevel welding. Start with simple joints and gradually work your way up to more complex joints. Share insights on advanced techniques and practical tips to help readers refine their bevel welding skills.
By following these tips, you can improve your bevel welding skills and create strong, high-quality welds.
Conclusion
To sum it up, a bevel weld means shaping the edges of metal before welding for a solid, even joint. You need to look at the groove type, bevel angle, and depth. Grooves can be straight, slanted, or V-shaped, with angles from around 8 degrees to 50 depending on the job.
For a good bevel weld, use the right technique, gear, and materials. Choose the best welding process and filler metal for the task.
Bevel welding helps make strong joins, and with these tips, you can get better at it and make your welds last.
Frequently Asked Questions About Bevel Weld Symbol
Is a bevel weld a groove weld?
Yes, a bevel weld is a type of groove weld. It is created by preparing a beveled edge on the workpiece to be welded. The bevel allows for better penetration of the weld and increases the surface area for the weld to bond to.
What is the best bevel angle for welding?
The best bevel angle for welding depends on the thickness of the material being welded and the welding process being used. In general, a bevel angle of 30-45 degrees is common for welding thicker materials, while a bevel angle of 20-30 degrees is common for thinner materials. The specific angle used will vary depending on the welding procedure specification (WPS) being followed.
What is a bevel joint used for?
A bevel joint is commonly used in welding to join two pieces of metal together at an angle. The bevel allows for better penetration of the weld and increases the surface area for the weld to bond to. Bevel joints are often used in applications where the welded joint will be subjected to high stress or where a smooth surface finish is desired.
What is flare bevel welding?
Flare bevel welding is a type of bevel welding where the bevel is flared out from the base material at a specific angle. This type of welding is commonly used in pipe welding applications, where it allows for a stronger weld joint and better flow characteristics.
What is the difference between a bevel and a square weld?
A bevel weld is created by preparing a beveled edge on the workpiece to be welded, while a square weld is created by welding two pieces of metal together at a 90-degree angle. Bevel welds are commonly used in applications where a smooth surface finish is desired, while square welds are often used in applications where strength is the primary concern.