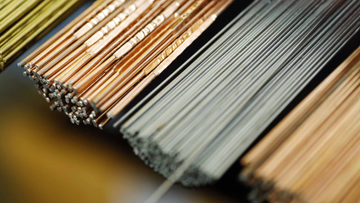
Choosing what welding rod to use is a key step in making your welding project successful. The rod you select impacts the weld’s strength, penetration, and position, so it’s important to choose carefully.
There are many types of welding rods, each designed for specific tasks. Common options include consumable and non-consumable electrodes, which work for different welding projects.
In this article, we’ll explore the types of welding rods, their uses, and tips for beginners to help you decide what welding rod to use for your project. Picking the right rod makes welding easier and ensures better results!
What Are Welding Rods?

Welding rods are an essential component of the welding process, and they come in different types and sizes. These rods are made from metal and coated with a flux that helps to protect the weld from contamination and oxidation.
Welding rods are also known as electrodes, and they play a crucial role in the welding process. They are used to create an arc between the welding machine and the metal being welded. This arc melts the metal, and the molten metal then cools and solidifies to form the weld.
What To Consider When Choosing a Welding Rod

Here are some factors to consider when selecting a welding rod:
1. Base Metal Properties
The first and most important factor to consider when choosing a welding rod is the properties of the base metal. The welding rod should be compatible with the base metal to ensure a strong and durable weld.
For example, if you are welding mild steel, you should choose a welding rod that is specifically designed for use with mild steel.
2. Welding Current
The welding current is another important factor to consider when selecting a welding rod. The welding rod must be able to handle the current output of the welding machine.
If the welding rod is not designed for the current output of the welding machine, it may not produce a strong enough weld.
3. Base Metal Thickness
The thickness of the base metal is also an important factor to consider when selecting a welding rod. Thicker base metals require welding rods with higher amperage ratings.
If you use a welding rod that is not designed for the thickness of the base metal, you may end up with a weak or incomplete weld.
4. Welding Position
The welding position is another important factor to consider when selecting a welding rod. Different welding positions require different types of welding rods.
For example, vertical welding requires a welding rod with a fast-freezing slag, while overhead welding requires a welding rod with a low-hydrogen coating.
5. Skill Level
Finally, your skill level is an important factor to consider when selecting a welding rod. If you are a beginner, you may want to choose a welding rod that is easy to use and forgiving.
On the other hand, if you are an experienced welder, you may want to choose a welding rod that requires more skill and precision.
4 Types of Welding Electrodes and Their Applications

Welding rods are classified based on their properties and are assigned an alphanumeric code.
This code is one or two letters followed by four or five numbers, and each has a specific meaning.

1. 6010 Welding Rods for Specific Applications
6010 welding rods are used for welding in all positions and are ideal for welding in tight spaces. These rods are suitable for welding mild steel and are known for their deep penetration and excellent arc stability.
They are often used in the construction of pipelines and pressure vessels and are also used for general fabrication.
2. 6011 Welding Rods for Specific Applications
6011 welding rods are similar to 6010 welding rods but are more versatile. They are ideal for welding in all positions and are suitable for use on both AC and DC welding machines.
These rods are often used for welding mild steel, galvanized steel, and some low alloy steels.
They are commonly used in the construction industry for welding structural steel and are also used for general fabrication.
3. 6013 Welding Rods for Specific Applications
6013 welding rods are versatile and easy to use. They are suitable for welding in all positions and are used for welding mild steel, galvanized steel, and some low alloy steels. They are commonly used in the automotive industry, general fabrication, and repair work.
4. 7018 Welding Rods for Specific Applications
7018 welding rods are known for their high tensile strength and are ideal for welding in all positions.
They are commonly used for welding low alloy steels and are often used in the construction of pressure vessels, bridges, and other structural applications.
These rods require a higher amperage and are best suited for use on DC welding machines.
Other Types of Welding Rods for Specific Applications
There are several other types of welding rods available, each with their unique properties and applications. Some of these include:
-
7024 welding rods: These rods are known for their high deposition rates and are often used for welding heavy plate steel.
-
308L welding rods: These rods are used for welding stainless steel and are often used in the food and beverage industry.
-
309L welding rods: These rods are used for welding dissimilar metals and are commonly used in the petrochemical industry.
Welding Techniques and Rod Selection

When it comes to welding, selecting the right technique and rod is crucial. Different welding techniques require different rods, and choosing the right one can make all the difference in the quality of the weld.
Here are some of the most common welding techniques and the rods that work best with them.
Stick Welding (SMAW)
Stick welding, also known as Shielded Metal Arc Welding (SMAW), is a popular welding technique that uses a consumable electrode coated in flux. The flux helps to protect the weld from contaminants and also helps to make a good weld. Stick welding is commonly used for welding thick materials and is ideal for outdoor welding applications.
When it comes to selecting a rod for stick welding, there are a few factors to consider. The most important factor is the type of material you are welding. If you are welding mild steel, then the 6013 or 7018 rod is a good choice.
For stainless steel, you should use a 308 or 309 rod, and for cast iron, a 312 or 316 rod is recommended.
MIG Welding (GMAW)
MIG welding, also known as Gas Metal Arc Welding (GMAW), is a welding technique that uses a wire electrode and a shielding gas to protect the weld from contaminants. MIG welding is commonly used for welding thin materials and is ideal for indoor welding applications.
When it comes to selecting a rod for MIG welding, the most important factor to consider is the type of material you are welding.
For mild steel, an ER70S-6 rod is a good choice. For stainless steel, an ER308 or ER309 rod is recommended, and for aluminum, an ER4043 or ER5356 rod is ideal.
TIG Welding (GTAW)
TIG welding, also known as Gas Tungsten Arc Welding (GTAW), is a welding technique that uses a non-consumable tungsten electrode and a shielding gas to protect the weld from contaminants. TIG welding is commonly used for welding thin materials and is ideal for precision welding applications.
When it comes to selecting a rod for TIG welding, the most important factor to consider is the type of material you are welding.
For mild steel, a ER70S-2 rod is a good choice. For stainless steel, a ER308 or ER316 rod is recommended, and for aluminum, a ER4043 or ER5356 rod is ideal.
Flux-Cored Arc Welding (FCAW)
Flux-Cored Arc Welding (FCAW) is a welding technique that uses a wire electrode with a flux core to protect the weld from contaminants. FCAW is commonly used for welding thick materials and is ideal for outdoor welding applications.
When it comes to selecting a rod for FCAW, the most important factor to consider is the type of material you are welding.
For mild steel, a E71T-1 or E71T-11 rod is a good choice.
or stainless steel, a E308LT-1 or E309LT-1 rod is recommended, and for aluminum, a E4043 or E5356 rod is ideal.
How to Choose the Right Welding Rod for Mild Steel

When it comes to welding mild steel, there are several factors to consider before selecting the right welding rod.
The first thing to consider is the thickness of the metal you will be welding. For thinner metals, a smaller-diameter welding rod is recommended, while thicker metals require a larger-diameter rod. The most common diameters for welding mild steel are 3/32", 1/8", and 5/32".
Another important consideration is the welding position. If you will be welding in a flat position, a smaller diameter rod will work well. However, if you will be welding in an overhead position, a larger diameter rod may be necessary to ensure proper penetration.
It's also important to consider the type of joint you will be welding. For butt joints, a smaller diameter rod is recommended, while larger diameter rods are better suited for fillet welds.
When selecting a welding rod, it's important to consider the type of welding you will be doing.
- For TIG welding, a high-quality mild steel rod like the PGN ER70S-6 5LB 1/16" x 16" is recommended for clean, slag-free welds.
- For stick welding, the E6013 welding rod is a good choice for mild steel due to its tensile strength of 60,000 psi and all-position electrode capabilities.
Best Welding Rods for Cast Iron and Other Metals
When it comes to welding, choosing the right welding rod is crucial for achieving a strong and durable weld. Here are some of the best welding rods for cast iron and other metals:
Cast Iron Welding Rods
For cast iron welding, there are two main types of welding rods: nickel-based rods and pure iron rods.
Nickel-based rods are preferred because they resist absorbing carbon from the casting, preventing the hardening of the weld metal and keeping it ductile.
Pure iron rods are cheaper but are more prone to cracking and are less ductile.
Some of the best nickel-based welding rods for cast iron include:
-
ENiFe-CI (AWS A5.15): This rod is ideal for welding cast iron to itself or to other metals. It produces a strong, crack-resistant weld that is also machinable.
-
ENi-CI (AWS A5.15): This rod is a good choice for welding cast iron to steel. It produces a strong, ductile weld that is also machinable.
-
ENiCrFe-2 (AWS A5.11): This rod is designed for welding cast iron to stainless steel. It produces a strong, crack-resistant weld that is also corrosion-resistant.
Stainless Steel Welding Rods
Stainless steel welding rods are available in a variety of types, each suited for different applications.
Some of the most commonly used stainless steel welding rods include:
-
ER308L (AWS A5.9): This rod is ideal for welding 304 and 304L stainless steel. It produces a strong, corrosion-resistant weld that is also easy to machine.
-
ER316L (AWS A5.9): This rod is designed for welding 316 and 316L stainless steel. It produces a strong, corrosion-resistant weld that is also resistant to pitting and crevice corrosion.
-
ER309L (AWS A5.9): This rod is best for welding dissimilar metals, such as stainless steel to carbon steel. It produces a strong, corrosion-resistant weld that is also resistant to thermal shock.
Aluminum Welding Rods
Aluminum welding rods are available in both TIG and MIG varieties. Some of the most commonly used aluminum welding rods include:
-
ER4043 (AWS A5.10): This rod is ideal for welding 6061 and 6063 aluminum alloys. It produces a strong, crack-resistant weld that is also corrosion-resistant.
-
ER5356 (AWS A5.10): This rod is designed for welding 5050, 5052, 5083, 5356, 5454, and 5456 aluminum alloys. It produces a strong, corrosion-resistant weld that is also easy to machine.
- ER4047 (AWS A5.10): This rod is best for welding cast aluminum alloys. It produces a strong, crack-resistant weld that is also highly ductile.
Tips for Using Different Welding Rods

Using the right welding rod for your project is essential for creating a strong and durable weld. Here are some tips for using different types of welding rods effectively:
Storage and Handling Tips
- Store your welding rods in a dry place to prevent moisture from affecting their performance.
- Use a rod oven to keep your welding rods dry and to prevent them from absorbing moisture from the air.
- Handle your welding rods carefully to prevent damage to the coating, which can affect their performance.
Technique Tips
- Use the recommended amperage settings for your welding rod to ensure a strong weld.
- Use the correct welding technique for your welding rod. For example, some welding rods require a weaving motion while others require a straight drag.
- Keep your welding rod at the correct angle to prevent the weld from being too wide or too narrow.
Common Mistakes to Avoid When Selecting Welding Rods

Selecting the right welding rod is crucial to achieve a strong and durable weld. However, there are some common mistakes that welders make when selecting welding rods.
Here are some of the most common mistakes and how to avoid them:
1. Choosing the Wrong Type of Rod
One of the most common mistakes welders make is choosing the wrong type of rod for the job. Different rods are designed for different welding applications, and using the wrong type of rod can result in a weak or brittle weld.
Always check the manufacturer's recommendations for the type of rod that is best suited for your welding job.
2. Using the Wrong Diameter
Using the wrong diameter of the welding rod can also result in a weak or brittle weld. The diameter of the rod you need depends on the thickness of the metal you are welding.
Always make sure to choose a rod with the correct diameter for the job.
3. Not Considering the Welding Position
Another common mistake is not considering the welding position when selecting a welding rod. Some rods are designed for use in specific positions, such as overhead or vertical welding. Using the wrong rod for the position can result in a poor quality weld.
4. Ignoring the Material Compatibility
Using a welding rod that is not compatible with the base metal can result in a weak or brittle weld. Always make sure to choose a welding rod that is compatible with the base metal you are welding.
5. Failing to Store the Rods Properly
Improper storage of welding rods can also result in poor-quality welds. Always store your welding rods in a dry place to prevent moisture from getting into the flux coating. Moisture in the coating can result in porosity and other defects in the weld.
What Welding Rod To Use: Final Thoughts
Choosing the right welding rod depends on your project, the materials you're working with, and the welding process you’re using.
Whether you’re repairing metal, building structures, or creating art, having the right tools makes all the difference.
Don’t forget, a quality stick welder pairs perfectly with top-notch electrodes like 2% Blue Lanthanated or Red Thoriated Tungsten.
Ready to level up your welding game? Grab a reliable stick welder along with premium tungsten electrodes today and ensure smooth, strong, and professional welds every time. Let’s get welding!
Frequently Asked Questions
How do I Know which Welding Rod to Use?
Choosing the right welding rod for your project can be a bit daunting, but it's not as difficult as it may seem. The most important factor to consider is the type of metal you're welding. Different metals require different types of welding rods. For instance, if you're welding mild steel, you should use an E6013 or E7018 welding rod. If you're welding stainless steel, you should use an E308L welding rod. If you're welding aluminum, you should use an ER4043 or ER5356 welding rod.
What Welding Rod Should a Beginner Use?
If you're just starting out with welding, it's best to use a welding rod that's easy to work with and forgiving. The E6013 welding rod is a good choice for beginners. It's easy to strike an arc with, and it produces a smooth and stable arc. It's also versatile and can be used for welding a variety of metals, including mild steel, stainless steel, and cast iron.
Which is Better 6011 or 6013 Welding Rods?
Both the E6011 and E6013 welding rods are good choices for welding mild steel. The E6011 welding rod is better suited for welding in tight spaces and vertical welding, while the E6013 welding rod is better suited for welding on thin materials and in flat positions. Ultimately, the choice between the two will depend on the specifics of your project.
What is a 7018 Welding Rod Used For?
The E7018 welding rod is a low-hydrogen electrode that's designed for welding carbon and low-alloy steels. It produces a strong, high-quality weld and is ideal for welding structures, such as bridges, buildings, and pipelines. It's also a good choice for welding heavy equipment, such as cranes and bulldozers. The E7018 welding rod requires a bit more skill to use than some other welding rods, but it's worth the effort for the quality of the weld it produces.