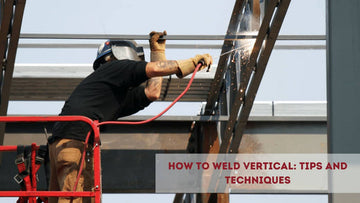
Vertical welding transforms ordinary metalwork into robust, professional-grade structures by overcoming the challenges of gravity.
Whether you’re repairing equipment or building new projects, mastering this technique will expand your capabilities and confidence as a welder.
Vertical welding is essential in construction, manufacturing, and pipeline work, where strong, reliable joints are non-negotiable. This position requires careful control and the right approach to prevent sagging or uneven welds.
Want to achieve clean, strong vertical welds every time? Read on to discover proven methods and practical tips for vertical welding success.
What Is Vertical Welding and Why Does It Matter?
Vertical welding is the process of joining metal pieces that stand upright, requiring precise control to prevent the molten weld from sagging.
This position is essential in construction, pipelines, and fabrication, where strength and reliability are critical.
Vertical welding means joining two pieces of metal together while they stand up straight, like two walls meeting at a corner.
You might see this in construction, shipbuilding, or when fixing pipes. Unlike flat welding, gravity pulls the hot, melted metal downward, making it tough to control.
The Four Core Welding Positions Explained
Understanding welding positions is key to choosing the right technique for your project. Welders typically use flat, horizontal, vertical, and overhead positions, each with unique challenges and best practices.
Every welder should know these four positions:
- Flat: Welding on top of a flat surface.
- Horizontal: Welding side-to-side on a vertical surface.
- Vertical: Welding up and down on a standing surface.
- Overhead: Welding from underneath the metal.
Vertical welding is usually the hardest, because you have to keep the melted metal from dripping or sagging.
How to Weld Vertical: The Step-by-Step Process
Welding in the vertical position requires careful preparation and attention to detail. By following a systematic approach, you can achieve consistent, high-quality welds even on challenging joints.
Setting Up for Vertical Welding Success
Proper setup lays the foundation for every strong vertical weld. Begin by cleaning your metal surfaces thoroughly and securely clamping your workpieces to prevent movement during welding.
- Clean your metal: Remove rust, paint, or dirt.
- Clamp or magnet: Hold your pieces steady.
- Safety first!: Wear a helmet, gloves, and long sleeves.
Choosing the Right Welding Method for Vertical Joints
Selecting the best welding process depends on your materials and project needs. Stick welding (SMAW) is popular for its versatility, while MIG and TIG welding offer different advantages for various applications.
There are three main ways to weld vertically:
Stick Welding (SMAW)
- Uses a metal rod (like 6010 or 7018).
- Great for outdoor jobs and thick metals.
- Perfect for beginners learning vertical welds.
MIG Welding (GMAW)
- Uses a wire fed through a gun.
- Fast and good for long welds.
- Needs shielding gas to protect the weld.
TIG Welding (GTAW)
- Uses a tungsten tip and separate filler rod.
- Makes neat, clean welds.
- Best for thin metals and fancy jobs.
Tip: For most vertical jobs, stick or MIG welding works best!
You May Shop
Stick Welding Vertical Joints: Technique and Tips
Stick welding is a reliable choice for vertical joints, especially on thicker materials or outdoor projects. Using the correct electrode angle and a steady, controlled motion is essential for preventing drips and ensuring full penetration.
Step-by-step:
- Pick the right rod. 6010 rods are great for vertical up, 7018 for strong, neat welds.
- Set your amperage. Start with the rod’s recommended settings.
- Hold your rod at a slight upward angle, about 10-15 degrees from vertical.
- Use a short arc. Keep the rod close to the metal.
- Move in a zigzag or “J” motion. This helps control the weld pool and stops drips.
-
Watch the weld pool. If it gets too big, pause or slow down.
Want to see what good welds look like? Check out these weld examples.
MIG Welding Vertical: Achieving Smooth, Clean Beads
MIG welding allows for faster travel speeds and smooth welds on vertical surfaces. Adjust your voltage and wire speed to suit the position, and use a gentle weaving motion to control the weld pool.
How to MIG weld vertical:
- Choose the right wire. ER70S-6 is a common pick.
- Set your machine. Use a lower voltage and wire speed than for flat welds.
- Start at the bottom. Weld upward for stronger joints.
- Use a “weave” or “stack of dimes” pattern. Move side-to-side gently as you go up.
-
Keep your gun at a 10-15 degree upward angle. Don’t point straight in!
Discover expert MIG tips in this comprehensive guide about welding with a wire welder.
TIG Welding Vertical: Precision for Thin Metals
TIG welding creates precise, clean welds on vertical surfaces, making it ideal for thin metals or projects that require a flawless finish. Control your amperage and travel speed to prevent overheating, and use a steady hand to guide the weld pool.
How to TIG weld vertical:
- Choose the right tungsten. 2% thoriated or ceriated tungsten works well for most steels.
- Set your machine. Use lower amperage than for flat welds to avoid burning through.
- Start at the bottom. Weld upward for better control and penetration.
- Use a slight weaving motion. Move the torch gently side-to-side to manage the weld pool.
- Keep your torch at a 10-15 degree upward angle. Maintain a consistent angle for even results.
Uphill vs. Downhill: Choosing the Best Vertical Welding Direction
The direction you weld matters when working vertically. Welding uphill, from bottom to top, produces stronger, deeper welds, while downhill welding can be faster but is best reserved for thin materials.
- Vertical Up (uphill): Best for thick metal and strong welds. More control, but takes practice.
-
Vertical Down (downhill): Faster, easier for thin metal, but not as strong.
Tip: For most important jobs, weld uphill for strength!
Common Challenges in Vertical Welding and How to Solve Them
Vertical welding presents unique obstacles, such as weld pool sagging, uneven beads, and excess spatter. By adjusting your technique and settings, you can overcome these issues and produce professional results.
Common problems:
- Dripping weld pool. Gravity can make melted metal fall.
- Uneven beads. It’s hard to keep your weld straight.
- Weld spatter. Hot metal can splatter and make a mess.
- Overheating. Too much heat can cause the weld to sag.
How to fix it: Use a smaller weld pool, steady hands, and the right rod or wire.
Advanced Tips for Mastering Vertical Welding
Refining your vertical welding skills takes practice and attention to detail. Using a controlled "J" or zigzag motion and keeping your weld pool small are proven ways to boost bead quality and consistency.
- Practice the “J” or Zigzag Motion: Moving your rod or gun in a “J” shape helps control the weld pool.
- Keep Your Weld Pool Small: Don’t let too much metal build up. Pause if needed.
- Hold a Consistent Angle: Keep your rod or gun at a 10-15 degree upward tilt.
- Use Both Hands for Control: Rest your arms or hands on something steady.
- Check Your Settings: Lower your amperage or voltage compared to flat welding.
You may also browse these weave patterns to find the one that works for you!
Applications and Industry Uses for Vertical Welding
Vertical welding is vital in construction, manufacturing, and repair work where strength and durability are non-negotiable. From building frames to pipeline repairs, this skill opens doors to a wide range of demanding projects.
Common uses:
- Construction: Building beams, columns, and bridges.
- Pipelines: Joining pipes standing up.
- Manufacturing: Making tanks, frames, or heavy machinery.
Vertical welding is everywhere. Once you master it, you can take on almost any welding project.
Conclusion
Vertical welding is a valuable skill that unlocks new possibilities in metalwork, construction, and repair.
With the right preparation, technique, and practice, you can achieve strong, clean welds in even the most challenging positions.
For more helpful welding tips and step-by-step guides, visit Arccaptain’s blogs.
Ready to upgrade your gear? Shop high-quality welding tools, equipment, and accessories to support your next project with confidence.
Frequently Asked Questions on Vertical Welding
What is the trick to vertical welding?
The key to vertical welding is controlling the weld pool so it doesn’t sag or drip due to gravity. Use a steady, upward motion with a small, consistent weld pool and employ a zigzag or “J” pattern to help support the molten metal.
Keeping your heat input lower than in flat welding also makes it easier to manage the weld as you go.
Do you weld vertical up or down?
Most welders choose to weld vertical up, from bottom to top, because it creates stronger, deeper welds and better penetration, especially on thicker materials.
Vertical down, from top to bottom, is faster and easier for thin metals, but the welds are generally weaker and less reliable for structural work. For most critical or load-bearing jobs, vertical up is strongly recommended.
Why is vertical welding hard?
Vertical welding is challenging because gravity constantly pulls the molten metal downward, making it difficult to control the shape and size of the weld pool.
This can lead to sagging, drips, and uneven beads if your technique or settings aren’t just right. It takes extra practice and careful heat management to produce neat, strong vertical welds.
What is the best angle for vertical welding?
The ideal angle for vertical welding is holding your electrode or gun about 10 to 15 degrees upward from perpendicular to the workpiece.
This slight tilt helps direct the weld pool upward and gives you better control over the molten metal. Maintaining a consistent angle throughout the weld is crucial for achieving uniform, high-quality results.