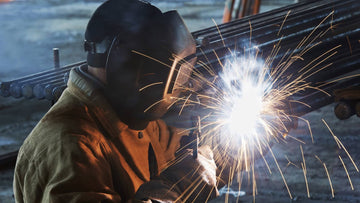
What is a combo welder? It’s a single machine that lets you perform different welding processes—like MIG, TIG, and stick—without needing separate equipment. This versatility makes it a favorite for both professionals and hobbyists who want to save space, cut costs, and tackle a wide range of projects. In this blog, we’ll look at how combo welders work, their key features, and why they’re becoming an essential tool across many industries.
What is a Combo Welder?
A combo welder, also known as a multi-process welder, is a versatile welding machine that combines multiple welding processes into a single unit. It allows the user to switch between different welding methods, such as MIG (Metal Inert Gas), TIG (Tungsten Inert Gas), and Stick welding, without the need for separate machines. This flexibility makes combo welders a popular choice for those who need to tackle a variety of welding projects.
MIG Welding Capability
A combo welder typically includes a MIG welding component that uses a spool of solid wire electrodes fed through a welding gun, along with an inert gas like argon to shield the weld pool from contaminants. This allows for strong welds on thinner metals like steel sheet metal. MIG welding is an easy process to learn, making it suitable for beginners.
TIG Welding Capability
The TIG welding function uses a non-consumable tungsten electrode and an inert gas like argon to produce high-quality, precise welds, especially on metals like aluminum, magnesium, and copper. TIG welding provides the strongest and cleanest welds but requires the most skill to master.
Stick Welding Capability
A combo welder will also usually provide stick or arc welding capabilities using consumable stick electrodes. Stick welding works in a wider range of positions and on dirtier, rustier metals. It does not require an external gas supply but produces more spatter and smoke than MIG or TIG welding.
In summary, a combo welder is a multifunctional tool providing MIG, TIG, and stick welding capabilities using a single, integrated power source. With some practice, this versatile welder allows professionals and hobbyists alike to perform a wide range of welding projects.
Key Features of Combo Welders
- Multiple Welding Processes: The primary feature of a combo welder is its ability to perform different welding processes. Whether you need to weld thin sheet metal using MIG or precision-weld aluminum with TIG, a combo welder has you covered?
- Adjustable Power Output: Combo welders often come with adjustable power output settings, allowing you to fine-tune the machine to suit the specific requirements of your project. This ensures optimal welding performance and results.
- Digital Displays: Many modern combo welders feature digital displays that provide clear and accurate readings of welding parameters, such as voltage, amperage, and wire feed speed. This helps in setting up the machine correctly and monitoring the welding process.
- Portability: Combo welders are often designed with portability in mind. They are compact and lightweight, making them easy to transport to different job sites or move around the workshop.
Benefits of Using a Combo Welder
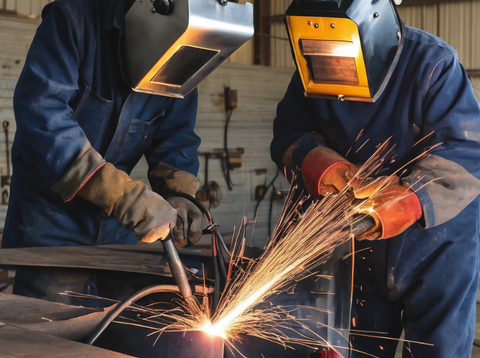
- Versatility: The most significant benefit of a combo welder is its versatility. With the ability to perform multiple welding processes, you can handle a wide range of materials and thicknesses, from thin gauge sheet metal to thick steel plates.
- Cost-Effectiveness: Investing in a combo welder can be more cost-effective than purchasing separate welding machines for each process. It eliminates the need for multiple machines, saving you money and valuable workshop space.
- Convenience: With a combo welder, you can quickly switch between welding processes without the hassle of setting up different machines. This saves time and increases productivity, especially when working on projects that require different welding methods.
- Skill Development: Using a combo welder allows welders to expand their skill set and gain experience with various welding techniques. It provides an opportunity to learn and master different processes, enhancing overall welding proficiency.
Applications of Combo Welders
Combo welders find applications across a wide range of industries and projects. Some common applications include:
The three most common types of welding that combo welders execute are stick welding, also known as shielded metal arc welding (SMAW); flux-cored arc welding (FCAW); and gas metal arc welding (GMAW), commonly referred to as metal inert gas (MIG) welding.
Stick Welding
Stick welding uses an electric current to melt electrode sticks that have a flux coating, creating an arc between the stick and the base metal. As the electrode melts, it deposits metal into the joint. Stick welding can weld both ferrous and non-ferrous metals and is often used in construction and repair work.
Flux-Cored Arc Welding
Flux-cored arc welding is a variation of MIG welding that uses a hollow wire filled with flux. It can weld ferrous metals like steel and is often used for structural welding in construction. The flux protects the weld puddle from contamination. FCAW is a high-deposition welding process suitable for welding thick materials.
Gas Metal Arc Welding
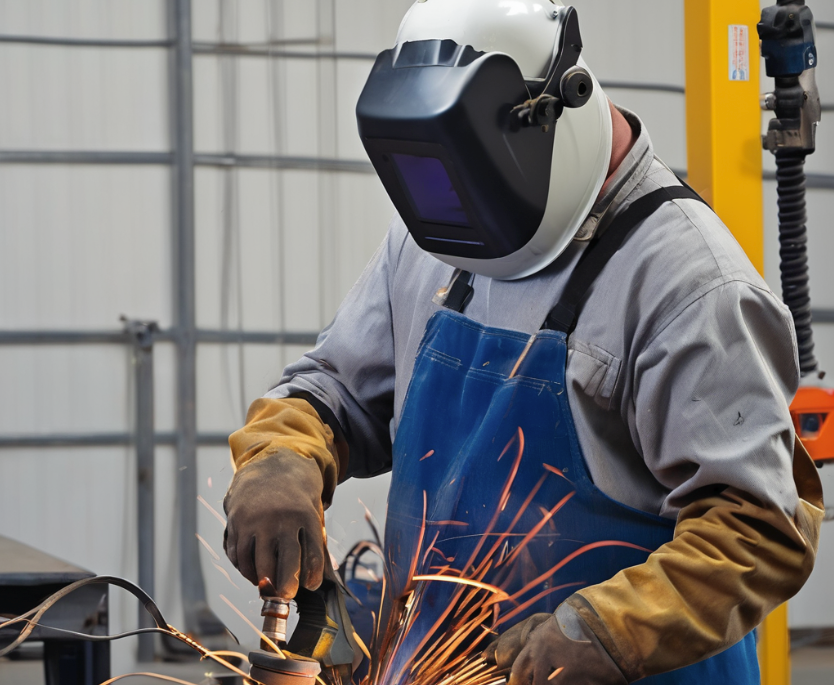
Gas metal arc welding uses a continuous solid wire electrode and an inert gas shield to protect the weld puddle. It can weld ferrous and non-ferrous metals like aluminum and is often used for sheet metal fabrication. GMAW is a versatile and high-speed welding process suitable for thin materials. The inert gas prevents oxidation and contamination of the weld puddle.
Combo welders can perform stick welding, flux-cored arc welding, and gas metal arc welding. Their ability to execute multiple welding processes allows fabricators and welders significant flexibility and efficiency. With a combo welder, welders have access to a range of welding options without needing separate machines for each process.
What to Look for When Buying a Combo Welder
Quality and Construction
When purchasing a combo welder, consumers should consider the overall quality and construction. Higher quality welders that are built to last longer typically cost more upfront but require fewer repairs and replacement parts over time. ArcCaptain recommends looking for a combo welder with an all-metal wire drive and gearbox, as well as a heavy-duty transformer and rectifier. These industrial-grade components can handle higher workloads and more demanding welding applications.
Adequate Power and Performance
The power output and performance of a combo welder significantly impact its capabilities. For most hobbyists and professionals, a welder that can produce between 140 to 230 amps using both AC and DC power is ideal. This range of power can weld materials of varying thicknesses, including steel, stainless steel, and aluminum. Welders in this range can also support different welding processes like MIG, TIG, stick, and flux-cored welding.
Essential Features
Useful features to consider when comparing combo welders include:
- An adjustable voltage and wire feed speed for different materials and welding positions.
- A multi-voltage plug that can connect to different power supplies.
- A spool gun for easier aluminum welding.
- A foot pedal or torch switch for TIG welding control.
- An easy-to-read display that shows current settings.
- A thermal overload protection system to prevent overheating.
- A sturdy handle and wheels for portability.
By assessing the quality, power, performance, and features of different combo welders, buyers can determine which model suits their needs and budget. An ArcCaptain combo welder provides the ideal balance of quality, capability, and value for most welding applications. With the right technique and safety equipment, a high-performance combo welder can produce professional-looking welds on a variety of metals.
How to Use a Combo Welder Safely and Effectively
Proper Safety Equipment
When operating an arc welder like the ArcCaptain combo welder, proper safety equipment is essential. Welders should wear a welding helmet with a shade 10 or higher lens to protect their eyes from the intense ultraviolet and infrared rays produced during welding. Thick, fire-resistant gloves and protective clothing should also be worn to prevent burns from heat and sparks. Proper ventilation, like an exhaust fan, should be used to remove toxic fumes.
Choosing the Correct Settings
Before welding, the machine must be properly set up for the specific task. The welder should select the appropriate amperage based on the thickness and type of metal being joined. For most mild steel welding, amperages between 50 and 200 amps are common.
The voltage should also be set to the proper level, typically between 15 to 25 volts. The welder can then choose between direct current electrode negative (DCEN), direct current electrode positive (DCEP), or alternating current (AC) based on the welding application.
Maintaining a Steady Hand
Once the welder helmet is lowered and the ArcCaptain is activated, maintaining a steady hand is key to creating a high-quality weld. The welder should hold the electrode at a 45-degree angle in the joint of the metals and move it smoothly along the seam using a small circular motion. Travel speed should remain consistent to achieve even penetration and avoid overheating the base metals. Proper welding technique takes a significant amount of practice to master.
By following essential safety protocols, choosing the proper machine settings, and practicing steady welding techniques, a combo welder like the ArcCaptain has can be used safely and effectively for a variety of welding applications. With regular practice, welders can master this versatile tool to create high-quality welds.
Conclusion: What is a Combo Welder?
Combo welders offer a versatile and efficient solution for welders who require the flexibility to perform multiple welding processes. With their ability to handle MIG, TIG, and Stick welding, combo welders provide convenience, cost-effectiveness, and expanded welding capabilities.
When considering purchasing a combo welder, it's essential to assess your specific welding needs, budget, and the features offered by different models. Investing in a quality combo welder can streamline your welding projects, enhance your skills, and achieve professional-grade results.
At Arc Captain, we offer a range of high-quality combo welder products designed to meet the diverse needs of welders. Our combo welders are engineered with advanced features and robust construction to deliver exceptional performance and reliability. Whether you're a professional welder or a DIY enthusiast, Arccaptain's combo welders provide the versatility and precision you need to tackle any welding project with ease.
Whether you're working on automotive fabrication, metal artwork, home repairs, or construction projects, Arccaptain's combo welders are your reliable companions. Experience the versatility and precision of our combo welders and take your welding skills to the next level.
Frequently Asked Questions: What is a Combo Welder
Can a combo welder handle both thin and thick materials?
Yes, combo welders are designed to handle a wide range of material thicknesses. By adjusting the power output and selecting the appropriate welding process, you can weld thin sheet metal as well as thick steel plates with a combo welder.
What welding processes can a combo welder perform?
Combo welders typically offer a combination of MIG, TIG, and Stick welding processes. Some models may also include additional features like plasma cutting or flux-cored welding.
Are combo welders suitable for beginners?
Combo welders can be a great choice for beginners who want to learn and explore different welding techniques. However, it's essential to familiarize yourself with the machine's features, safety precautions, and proper welding techniques before starting. Attending welding classes or workshops can provide valuable guidance and help you develop your skills.
How portable are combo welders?
Many combo welders are designed with portability in mind. They are compact and lightweight, making them easy to transport to different job sites or move around the workshop. However, the level of portability may vary depending on the specific model and its features.
Where can I find high-quality combo welders?
At Arccaptain, we offer a range of top-notch combo welder products designed to meet the needs of welders across industries. Our combo welders are engineered with advanced features, robust construction, and user-friendliness in mind, ensuring exceptional performance and reliability.