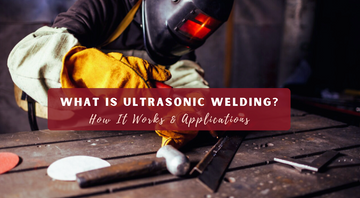
Ultrasonic welding is a fast, clean, and reliable method for joining materials such as plastics and thin metals using high-frequency sound vibrations. This process does not use glue, screws, or heat from a flame, making it particularly suitable for products that require strong, precise, and neat seams.
You may not realize it, but ultrasonic welding is all around you, in medical devices, cars, electronics, and even packaging. Its impact on modern manufacturing is huge, making the assembly of many products safer, quicker, and more efficient.
In this article, you will learn how ultrasonic welding works, what kinds of products use it, and why many industries choose this method over others. Get ready to discover the basics, main advantages, and interesting uses of this important technology.
Quick Insights ⚡:
- Ultrasonic welding joins materials using high-frequency vibrations.
- No need for glue, bolts, or solder, fast and clean process.
- Commonly used for plastics and metals in electronics, automotive, and medical devices.
- Saves time, energy, and reduces production costs.
What Is Ultrasonic Welding?
Ultrasonic welding is a process that joins materials, such as plastics or thin metals, using sound vibrations instead of heat from a flame or an electrical source. This method works fast and is often used for making products such as electronics, medical devices, and automotive parts.
How Does Ultrasonic Welding Work?
In ultrasonic welding, high-frequency vibrations, typically ranging from 20,000 to 40,000 cycles per second (20–40 kHz), are used to join two pieces of material. You place the materials together and apply pressure.

These strong vibrations cause the materials to rub against each other at the joint, generating friction. The friction builds up enough heat in a very small area, causing the material to soften or melt only at that spot.
There are no outside heating elements. Only the spot where the materials touch gets hot and bonds. After a few seconds, the joint cools and forms a solid, strong molecular connection.
The Key Components of an Ultrasonic Welding System
An ultrasonic welding machine consists of several key components that work together to create the weld. These include:
- Converter: Turns electrical energy into fast mechanical vibrations.
- Booster: Increases the strength of these vibrations and sends them toward the welding point.
- Sonotrode (Horn): Receives the amplified vibrations and applies them right to the materials you want to weld.
- Anvil: Holds and supports the pieces in place while the welding happens.
Each part has a specific job, allowing the energy to transfer from the machine into the materials, which are then pressed and vibrated to create a strong weld.
Essential Equipment Used in Ultrasonic Welding
When working with ultrasonic welding, you need several main pieces of equipment. Each tool plays a specific role in making a strong and reliable weld.
Key equipment includes:
-
Ultrasonic welder or machine: This machine generates high-frequency vibrations used to join materials. It usually includes a frame that holds all the other parts together.
-
Power supply and control system: The power supply converts standard electrical energy into high-frequency electrical signals required for welding. The control system allows you to adjust settings such as time, pressure, and amplitude.
-
Sonotrode (horn): The sonotrode takes the electrical vibrations from the power source and turns them into mechanical vibrations. These vibrations help melt and bond the parts. It is often made from strong metals, such as titanium.
-
Booster: The booster increases or decreases the vibration amplitude sent from the converter to the sonotrode. It helps control the energy delivered to the weld point.
- Anvil (fixture): The anvil holds and supports the materials you want to weld. It maintains the workpieces in the correct position during welding for improved accuracy.
Here is a quick table to show the main equipment and what it does:
Equipment |
Main Function |
Ultrasonic Welder |
Generates vibrations to weld materials |
Power Supply/Controls |
Provides energy and sets controls |
Sonotrode (Horn) |
Transfers vibrations to the welding area |
Booster |
Adjusts vibration strength |
Anvil (Fixture) |
Holds and supports the workpieces |
💥 Also Read: MIG Welding Wire Speed & Voltage Chart: Settings & Guidelines
Advantages and Disadvantages of Ultrasonic Welding
Ultrasonic welding is widely used in various industries due to its fast and clean method of joining plastics and certain metals. However, this method also has limits that could affect whether it is the right choice for your application.
Key Benefits of Ultrasonic Welding
Ultrasonic welding is known for its quick cycle times. You can join parts in just a few seconds, which helps boost your production speed. The process utilizes high-frequency vibrations to generate heat, allowing only the joint area to become hot. This keeps the rest of the material safe from damage.
Because ultrasonic welding does not require glue, screws, or solder, you save on extra materials and avoid the mess they can leave. Joints made with this method are usually strong, clean, and very precise. The results are repeatable, so your finished products are consistent.
Below is a quick list of key benefits:
- Fast production cycles enable you to manufacture more parts in a shorter timeframe.
- No extra materials are needed, which lowers costs.
- Clean joints mean there is little to no mess left over.
- Precise bonds with less risk of warping or discoloring your parts.
- Energy-efficient since heat is focused only where it is needed.
Potential Drawbacks or Limitations
Ultrasonic welding is not a perfect fit for all jobs. You can only use it with materials that conduct ultrasonic vibrations well, such as many plastics and some thin metals.
If your parts are too large, thick, or made from materials that absorb vibrations, welding may not be a suitable option.
The machines can be expensive to purchase initially, so the cost can be high if you only need to weld a few parts.
Also, the process works best on parts with simple shapes. If your part has thick sections or complex designs, ultrasonic welding may not form a strong bond.
Some specific limitations include:
- Not suitable for materials like glass, wood, or very thick metals.
- Higher upfront equipment cost compared to some traditional methods.
- Best for simple, small parts with even surfaces.
- Limited use for parts with odd shapes or large sizes.
- May require special tooling for each different part design.
💥 Also Read: Stick Welder Settings Chart: Amperage & Electrodes
Common Applications of Ultrasonic Welding
Ultrasonic welding is utilized in various industries due to its ability to create strong, clean joints efficiently. You will see it in products that need fast assembly, airtight seals, and gentle handling of materials.
Ultrasonic Welding in Plastics
Ultrasonic welding is widely used in the manufacturing of plastic items. This process is crucial in industries such as packaging and medical devices because it joins plastic parts without the use of glue or screws.
Key applications in plastics:
- Packaging: Seals blister packs, pouches, and containers to maintain product freshness.
- Toys and consumer products: Join parts of toys, electronics housings, and plastic tools.
- Medical devices: Assembles syringes, filters, IV catheters, and other sterile products.
Ultrasonic welding is fast and repeatable. It helps keep costs down, and you get strong, precise welds without melting or damaging sensitive parts.
Ultrasonic Welding in Metals
You can use ultrasonic welding to join thin metals, especially when traditional welding methods are too aggressive or generate excessive heat. It is commonly used in the electronics and automotive sectors.
Primary uses in metals:
- Electronics: Bonds wires, connectors, and microcircuits without extra materials.
- Automotive wiring: Assembles and welds cable harnesses and battery cables for electric vehicles.
- Battery tabs: Join the metal tabs in lithium-ion batteries to ensure good electrical contact.
This method helps avoid overheating, which is important for delicate electronic components. Parts can be joined quickly, and the process works well for mass production.
Other Notable Uses
Ultrasonic welding has also found applications outside of plastics and metals. It helps join and handle soft or difficult-to-sew materials.
Other important uses include:
- Textiles and nonwovens: Cut and seal synthetic fabrics for things like disposable gowns and face masks.
- Filters: Connects layers of filter media in air, water, and oil filters.
- Custom parts: Manufacturers' specialty components for industries such as food packaging and appliances.
This process gives clean edges and strong seams. It is useful when you need a fast, efficient, and clean way to bond thin layers or fragile materials.
💥 Also Read: 6013 vs. 7018: How To Decide for Your Next Weld
Ultrasonic Welding vs Traditional Welding
When you look at ultrasonic welding and traditional welding, you’ll notice some clear differences in how they work and what they can join.
Heat Source:
- Ultrasonic welding uses high-frequency sound waves to create heat through friction. This heat joins the materials together.
- Traditional welding uses high heat from electricity or a flame to melt and fuse materials.
Speed:
- Ultrasonic welding is usually much faster. You can often finish a weld in just a few seconds.
- Traditional welding can take longer. It depends on the type of weld and the material thickness.
Material Compatibility:
- Ultrasonic welding is most effective with plastics and thin metals.
- Traditional welding connects a wider range of metals but usually can't handle plastics.
Table: Key Differences
Feature |
Ultrasonic Welding |
Traditional Welding |
Heat Source |
Sound waves, friction |
Electrical or flame heat |
Typical Speed |
Very fast |
Slower |
Best For |
Plastics, thin metals |
Most metals |
Material Melting |
No melting needed |
Metal melts together |
Fumes or Sparks |
Few or none |
Usually present |
Other Points:
- Ultrasonic welding is common in electronics, medical devices, and packaging.
- Traditional welding is commonly used in heavy construction, automotive manufacturing, and pipeline construction.
- Safety: Ultrasonic welding produces fewer fumes, resulting in a cleaner process.
You should choose the method based on the materials you use and the speed you need.
💥 Also Read: Best Portable Welding Guns in 2025: 4 Expert Picks
Ultrasonic Welding vs Laser Welding
Ultrasonic welding and laser welding are both used to join materials, but they work in different ways.
Ultrasonic welding utilizes high-frequency vibrations to generate heat between two pieces. This heat makes the materials bond together without melting them. You often see ultrasonic welding used for plastics and some thin metals.
Laser welding, on the other hand, uses a focused laser beam. The beam melts the materials at the joining point, allowing them to fuse as they cool. This method is used for a wide range of metals and sometimes plastics.
Key differences:
- Ultrasonic welding is particularly well-suited for small parts, thin materials, and plastics.
- Laser welding is better for thicker, stronger metals and complex shapes.
- Laser welding usually requires more expensive equipment.
- Ultrasonic welding machines can be more affordable.
Here is a quick comparison:
Feature |
Ultrasonic Welding |
Laser Welding |
Main Use |
Plastics, some metals |
Metals, some plastics |
Heat Source |
Vibrations |
Laser beam |
Cost |
Lower |
Higher |
Precision |
Good |
Very high |
Material types |
Dissimilar materials |
Wide range |
If you need a quick, cost-friendly method for small or thin parts, ultrasonic welding could be the best. If you need high strength or to join thick metals, laser welding may be the ideal solution for your needs.
💥 Read more about What is Laser Welding.
How to Get Started with Ultrasonic Welding

Getting started with ultrasonic welding involves selecting the most suitable equipment for your specific needs and ensuring a safe working environment during use. Both your choice of tools and your work habits will affect your results.
Choosing the Right Ultrasonic Welding Equipment
Before purchasing an ultrasonic welder, consider what you need to weld. The material type is key, as not all plastics or metals are suitable for this process. For plastics, choose a machine that matches your material’s melting point.
Consider the size and shape of your parts. Some welders are designed for small, delicate parts, while others are suited for handling tough, larger items.
If you plan to produce a large number of pieces, look for machines that operate efficiently and can complete multiple cycles without interruption.
Budget also matters. Entry-level ultrasonic welders are less expensive but may have limited features or lower power capabilities. High-end machines are more precise and often have digital controls or extra safety features.
Make a checklist of what you need:
- What types of materials will you weld?
- How big and thick are your parts?
- How many parts do you plan to weld each day?
- What is your budget for equipment?
Ask the manufacturer for support or a demo if you are unsure. Check for customer reviews and service options.
Safety Tips for Ultrasonic Welding
Safety is important when working with ultrasonic welders. Always wear the right personal protective equipment (PPE):
- Safety glasses or a face shield for eye protection
- Heat-resistant gloves to prevent burns
- Ear protection if the equipment is loud
Keep the welder clean and check it for loose parts, worn wires, or broken components before each use. A regular maintenance schedule can prevent problems from arising.
Training is important. Ensure that everyone using the welder is familiar with its operation, has read the manual, and knows how to handle emergencies. Do not bypass safety covers or modify the machine in any way.
Keep the work area free of clutter. Use a non-slip mat on the floor to avoid slips or falls. Store tools and supplies within easy reach to prevent accidents.
If you notice any unusual noises, overheating, or sparks, turn the machine off immediately and inspect it. Always unplug the equipment before doing any repair work.
Best Welding Helmet You May Also Like 👍
Conclusion – Is Ultrasonic Welding Right for You?
Ultrasonic welding is a joining method that uses high-frequency sound waves and pressure to weld materials. The process melts and bonds parts together without using extra glues, bolts, or heat sources.
Key Benefits:
- Fast joining time
- Clean and precise welds
- Works well for plastics and some metals
- No extra materials needed
You should consider ultrasonic welding if your project needs strong, neat joints for plastics or thin metals. It’s especially useful for medical, electronic, or automotive parts where clean and repeatable results matter.
Situations where ultrasonic welding is a good fit:
- You want to avoid using glue or solder
- Your parts are small or have delicate shapes
- Consistent quality is important in production
However, ultrasonic welding does require special equipment and skilled operators. It may not work well for thick or very large parts.
Consider your project's needs, materials, and objectives before selecting this method. If you need fast, clean, and repeatable bonds, especially with plastics, ultrasonic welding could be the right choice for you.
Best Welding Machines You May Also Like 👍
❓Frequently Asked Questions
Ultrasonic welding is used in many industries to join plastics and some metals. It is valued for its speed, clean process, and reliable welds.
What materials can be joined with ultrasonic welding?
You can use ultrasonic welding to join many types of thermoplastics, like ABS, polycarbonate, and PVC. Some soft metals, such as aluminum and copper, can also be welded by this method. Using compatible materials helps create strong and lasting bonds.
Is ultrasonic welding safe for medical devices?
Yes, ultrasonic welding is often used in the medical field. It does not use glues or other chemicals, thereby reducing the risk of contamination. Many medical products like filters, IV bags, and face masks, are made with this process.
How strong are ultrasonic welds?
Ultrasonic welds can be very strong if the materials are compatible and the process is appropriately set up. In many cases, the weld can be as strong as the parts themselves. Joint design and material choice both affect final weld strength.
Can ultrasonic welding be used for large parts?
Ultrasonic welding is most effective for small to medium-sized parts. Larger parts can be joined, but the process may require specialized equipment, such as larger ultrasonic horns. Sometimes, joining sections one at a time is needed for very big items.
What range of materials can be effectively joined using ultrasonic welding?
Ultrasonic welding is most effective on thermoplastics and some soft metals. Rigid plastics and thin metals are well-suited for this method. It is not suited for hard metals or materials that do not transmit vibrations easily.