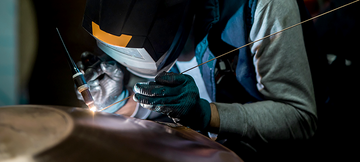
Wire feeding is a key factor to influence welding, and choosing the right drive roll is critical for smooth wire feeding.The drive roller is responsible for feeding the wire from the spool to the torch, through the bushing, and finally to the weld pool. The correct drive roll will ensure a smooth wire feed without interruption or slippage, resulting in a high-quality weld. The step by step guide can help you choose the right drive roll for your welding needs.
1.Be Sure The Wire Size and Type
The first step in selecting the proper drive roll is to determine the wire size and type. Wire size refers to the diameter of the welding wire, usually measured in inches or millimeters. Wire sizes can vary from as small as 0.023 inches to as large as 0.045 inches or more. The type of wire can also vary from solid to flux cored.
2.Check drive roll compatibility with welder
It is imperative to ensure that the drive roll you choose is compatible with your welder. Some drive rollers are designed specifically for some machines and may not work with others. Check the manufacturer's recommendations for your welder to find the right drive roll.
3.Consider the number of grooves on the drive roller
The drive roller can have one or more grooves. The number of grooves on the drive roller depends on the type of wire you are using. For example, solid wire typically requires a drive roll with a single groove, while flux-cored wire may require a drive roll with two or more grooves.
4.Choosing the Right Material for Drive Rollers
Drive rollers can be made from a variety of materials including steel, aluminum and plastic. Steel drive rolls are the most common and are suitable for most welding applications. Aluminum drive rolls are ideal for feeding annealed aluminum wire. Plastic drive rollers are ideal for feeding flexible wires that are prone to deformation, such as silicon bronze.
5.Consider the type of knurling on the drive roller
Knurling on a drive roll refers to the pattern or texture on the surface of the roll. Knurling can range from simple diamond patterns to more intricate designs. The type of knurling on the drive roll affects wire grip and feed speed. For example, thicker knurling may provide better grip on softer wires, while thinner knurling may be better for stiffer wires.
What are the different types of drive rolls and when is each one used?
The different types of drive rolls are used to accommodate different wire types and ensure smooth wire feeding during the welding process. V Groove drive rolls are used for hard solid wires, U Groove drive rolls are used for soft solid wires, and Knurled drive rolls are used for flux-cored wires. Understanding which drive roll to use for each wire type can help optimize the welding process and achieve high-quality welds.
V Groove Drive Roll :

for hard solid wires: steel, stainless steel. Provides good grip without damaging the copper coating on solid steel wires.
U Groove Drive Roll:

for soft solid wires: Aluminium/Aluminum. Provides good grip via friction. Aluminium/Aluminum wires are very clean wires and have no surface lubricants. A U Groove drive roll does not squash the wire and allows a controlled amount of slippage to stop the wire from birds nesting (a big tangle of wire that can happen if too much force is used to feed the wire).
Knurled Drive Roll :
for flux-cored wires. Provides good grip on flux-cored wires which usually have a surface lubricant for better feeding.
Knurled drive rolls have little teeth on them that provide extra grip on flux-cored wires. Flux-cored wires usually have a surface lubricant that can cause slippage, which can lead to inconsistent wire feeding. The knurled drive roll is designed to grip the flux-cored wire and ensure smooth, consistent wire feeding. Knurled drive rolls are commonly used in flux-cored welding applications.
6.Check drive roller tension
Drive roller tension is the amount of pressure that the drive roller exerts on the wire. It must be ensured that the drive roller tension is set correctly for the wire size and type. Too little tension can cause the wire to slip, while too much tension can deform or damage the wire.
This is a video guide to help you know how to adjust the drive roller tension.
In summary, choosing the right drive roll is critical for smooth wire feeding and high-quality welding. When selecting a drive roll, consider wire size and type, compatibility with your welder, number of grooves on the roll, roll material, knurling type, and drive roll tension. By considering these factors, you can be sure to choose the right drive roll for your welding needs.