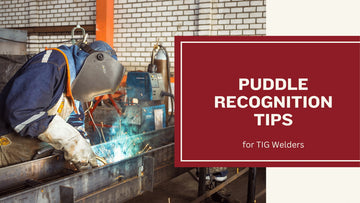
Recognizing weld puddle issues is crucial to ensure that you produce high-quality TIG welds. However, it is equally important to recognize when you are welding correctly. This way, you can reinforce good techniques and avoid issues in the future.
In this article, you will learn how to identify puddle issues when TIG welding and determine if you are running too hot or too cold of an arc. Additionally, we will provide some tips that are specific to TIG welding stainless steel and aluminum. By the end of this article, you will be equipped with the knowledge to improve your TIG welding skills and produce better welds.
Important Technique Requirements for Correct TIG Welding
To achieve high-quality TIG welds, you must follow several essential technique prerequisites.
- First, get into a comfortable body position over the welded piece to achieve good hand mobility and stability.
- Second, maintain a smooth torch travel, and use the correct torch angle for the joint type.
- Third, apply a consistent arc length and foot pedal control.
- Fourth, one hand moves the torch, and the other feeds the filler material.
- Fifth, ensure sufficient shielding gas coverage to avoid contamination.
- Sixth, avoid dipping the tungsten into the weld puddle, moving the filler material outside of the shielding gas zone beneath the cup, and touching the tungsten tip with the filler metal as you weld.
- Finally, don't use a thicker filler wire than the welded material. Violating any of the essentials listed above will cause puddle control issues and reduce, if not outright ruin, the weld quality.
Recognizing The Correct Amperage Input
When TIG welding, using the correct amperage input is crucial to achieve quality welds. Applying too much or too little heat can cause puddle control issues, poor penetration, warping, and burning through on thinner metal. Therefore, it's essential to recognize if you need to back off the amperage or increase it. Here are some signs that will help you recognize if your weld puddle is too hot or too cold.
Weld Puddle Is Too Hot
If your TIG welder is outputting too much amperage for the welded material thickness, you will experience the following issues:
-
Shaky puddle - It's normal to experience a little bit of an unsteady and wobbly molten puddle surface. But, if your weld puddle is too shaky and experiences high trembles, it won't be easy to direct and control.
-
Too wide heat-affected zone (HAZ) - Inputting too much heat when TIG welding causes a wide HAZ, risking warping and oxidation damaging the welded material, especially on stainless steel.
-
Oxides buildup in the weld pool - You may also experience oxides building up in the weld pool depending on your shielding gas coverage and travel speed.
-
Weld pool pulls contaminants into itself - If you didn't clean the material upfront properly, running your TIG welder too hot will pull more mill scale into the weld pool and other contaminants.
-
Undercut - Using too high amperage will cause undercutting, especially when making a fillet weld. High heat will erode the upper part of the fillet joint and cause undercutting, which weakens the weld.
-
Puddle is melting through - If the puddle falls through the edges of the joint, you are using too many amps.
To avoid these issues, reduce the amperage input and adjust the heat control. Ensure sufficient shielding gas coverage and keep the filler material within the shielding gas zone beneath the cup. Don't dip the tungsten into the weld puddle, and don't touch the tungsten tip with the filler metal as you weld.
Weld Puddle Is Too Cold
On the other hand, beginner TIG welders are often afraid of warping and burning through the thin material. So, it's a common mistake to use too low amperage. However, this fear is rational. It's easy to burn through and distort thin sheet metal, especially stainless steel. Here are some signs that indicate that you have reduced amperage output too much and that increasing it will help:
-
Forming the weld puddle is too slow - If the base metal melts too slowly, you are doing more harm than good by concentrating the arc into one spot for a prolonged period.
-
Filler material won't melt in the weld puddle - If you dab the filler wire into the weld puddle and it won't fully melt, increasing amperage output may help.
-
Poor puddle fluidity - Unlike the shaky, wobbly puddle made with too much heat, the low heat input will create a small puddle that barely consumes the base metal and moves slowly.
-
Poor penetration - Using too low amperage output results in poor joint penetration and fusion, making a weak bond.
To avoid these issues, increase the amperage input and adjust the power setting. Ensure sufficient shielding gas coverage, and keep the filler material within the shielding gas zone beneath the cup. Don't dip the tungsten into the weld puddle, and don't touch the tungsten tip with the filler metal as you weld. Use the correct travel speeds, arc length, and DCEN or DCEP polarity, depending on the material thickness and type. Consider using inert gases such as argon or helium for better penetration and cleaner welds.
Remember, recognizing the correct amperage input is crucial for achieving quality TIG welds. By reading the puddle and adjusting the heat control, you can avoid puddle control issues, poor penetration, warping, and burning through on thinner metal.
Puddle When Welding Dirty Material
When welding dirty material, it is essential to clean the surface from mill scale, oxides, paint, oils, and other contaminants to achieve a quality TIG weld. Failure to clean the material properly can lead to various weld puddle issues, including porosity, bubbles, smoke, and poor, brittle welds. Some signs that the material needs more cleaning include debris forming on the solidifying weld puddle and uneven ripples of the TIG welds. To avoid these issues, make sure to clean the material thoroughly before welding and use proper techniques to prevent dirt and other contaminants from affecting the weld quality.
Stainless Steel
Stainless steel is a unique material that requires special attention when welding. Due to its poor heat conductivity, stainless steel retains heat very well, which can cause it to oxidize and go through carbide precipitation if held at high heat for prolonged periods. As a result, it is essential to control heat input when welding stainless steel to avoid destroying its corrosion resistance.
To ensure a successful weld, the weld puddle shouldn't be more liquid than necessary, and the heat-affected zone (HAZ) should be as narrow as possible. Using a sharp tungsten tip and ensuring good shielding gas coverage is also crucial. High welding speed is preferred to avoid heat concentration in one area for too long, but do not use too low heat input either. The puddle must be fluid but not too runny.
It is important to note that stainless steel requires a different approach than mild steel.
Remember to take proper precautions when welding stainless steel to avoid damaging the material and ensure a successful weld.
Aluminum
Aluminum is a notoriously difficult material to weld, thanks to its oxide layer. But, this metal has another issue: excessive heat conductivity. So, unlike stainless steel, aluminum is very good at dissipating heat.
To weld aluminum, you need to use a much higher amperage than to weld stainless steel. Otherwise, the puddle will be unresponsive and not liquid enough. That's because the aluminum will dissipate the heat input from the arc into the HAZ and surrounding metal, and there won't be enough power left to keep the weld puddle liquid.
However, as aluminum gets hotter, you may need to back off the foot pedal to reduce the amperage input. If the puddle turns too wide and becomes uncontrollable, reduce the power input.
Aluminum Oxides
To weld aluminum, you must use an AC TIG welder because the DCEP part of the current is responsible for cleaning the aluminum oxides on the surface. The other part, DCEN, achieves the necessary penetration, melts the material, and fuses the two pieces together.
However, it's important not to start adding the filler wire and moving the torch until the DCEP cleans the initial puddle. When you initiate the high-frequency arc, you need to wait for a brief moment until the puddle looks like a shiny dot, and only then start moving the torch and adding the filler material.
The initial puddle becomes shiny because the DCEP has burned the oxide, and now the pure aluminum underneath is ready to be bonded with the filler metal.
If your AC balance setting is too shallow, the DCEP won't have much cleaning power. This can result in more oxide inclusion in the weld and make a poor joint. Keep an eye out for any debris floating in the molten aluminum puddle.
In summary, to weld aluminum, you need to use a higher amperage, and an AC TIG welder is necessary to clean the aluminum oxides on the surface. Be patient and wait for the initial puddle to become shiny before moving the torch and adding the filler material. Keep an eye out for any debris floating in the molten aluminum puddle.
Use a High-Quality Welding Helmet
To ensure you can see the weld puddle clearly, you need a welding helmet that transmits enough light and color. A good example of such a welding helmet is the ArcCaptain Auto-Darkening Welding Helmet Super Large Viewing Screen True Color. This helmet comes with advanced true-color technology and a 1/1/1/1 optical clarity lens provides excellent visibility over the weld puddle. The helmet also has a panoramic view and is auto-darkening, making it a great choice for TIG welding.
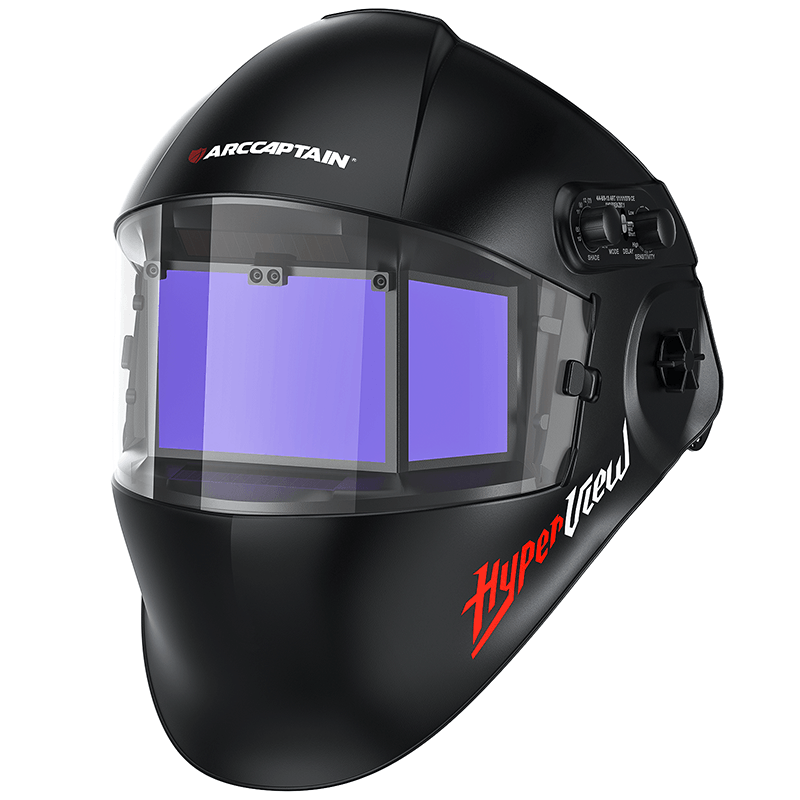
Conclusion
TIG welding is a highly advanced welding process that requires a lot of skill and practice to master. One of the most challenging aspects of TIG welding is recognizing and addressing puddle issues in real-time. This requires a keen eye and a deep understanding of the welding process.
Although observing the puddle is important in MIG and stick welding as well, it is much harder to do so due to the smoke and nozzle obstruction. In TIG welding, there is very little room for error, and any issues with the puddle must be addressed immediately.
With practice, you can develop the necessary muscle memory to master TIG welding. By controlling the heat input, travel speed, and recognizing the puddle cues, you can create fantastic TIG welds and tackle even the most challenging welding jobs.
In conclusion, mastering TIG welding takes time and effort, but with the right approach and mindset, you can become a skilled TIG welder and produce high-quality welds.
Frequently Asked Questions
How to Identify an Ideal TIG Welding Puddle Size?
To identify an ideal TIG welding puddle size, you need to ensure that it is not too big or too small. A good puddle size is typically about the size of a dime or a quarter. The puddle should be evenly distributed and should not have any irregular shapes. If the puddle is too small, it can lead to a weak weld, whereas a large puddle can cause the metal to warp or burn through.
What Techniques Are Used for Maintaining Puddle Control in TIG Welding?
Maintaining puddle control is crucial for successful TIG welding. Some techniques that you can use to maintain puddle control include:
- Adjusting the amperage and travel speed
- Using a foot pedal to control the amperage
- Keeping the torch at a consistent angle
- Using filler rod to add material to the puddle
- Keeping the torch close to the workpiece
Is It Better to Push or Pull the Puddle in TIG Welding, and Why?
It is generally better to pull the puddle in TIG welding. Pulling the puddle allows you to see where you are going and helps you maintain control. Pushing the puddle can cause the weld to become distorted or even break. Additionally, pulling the puddle allows you to maintain a consistent travel speed and angle, which is crucial for a stable weld.
What Are the Characteristics of a Stable Weld Puddle in TIG Welding?
A stable weld puddle in TIG welding should have the following characteristics:
- Evenly distributed
- Consistent in shape and size
- No irregularities or cracks
- No porosity or pinholes
- No discoloration or burnt spots
How Does Puddle Shape Affect the Outcome of a TIG Weld?
Puddle shape can have a significant impact on the outcome of a TIG weld. A puddle that is too wide or too narrow can cause the weld to become distorted or even break. Additionally, a puddle that is too shallow can lead to a weak weld, whereas a puddle that is too deep can cause the metal to warp or burn through.
What Are Common Mistakes to Avoid When Learning Puddle Control in TIG Welding?
Some common mistakes to avoid when learning puddle control in TIG welding include:
- Moving the torch too quickly or too slowly
- Not maintaining a consistent travel speed or angle
- Using too much or too little filler rod
- Not adjusting the amperage or travel speed correctly
- Not keeping the torch close enough to the workpiece
By avoiding these mistakes and practicing good puddle control techniques, you can improve your TIG welding skills and create high-quality welds.