
Grounding your welder is easy to do, but you've got to do it the right way. It's a safety must that also makes sure your welding turns out well. Our guide, "How to Ground Your Welder," will cover what you need to know to set up a good ground connection.
You'll learn the steps to ground your welding machine, which will help you dodge electric shocks and keep your arc steady for cleaner welds.
We'll pass on proven tips from our welding experience to help you work safely and effectively. This info is vital whether you're just starting with welding or you've been at it for years.
By the end of this guide, you'll know how to get your welder grounded and ready for action. Let's jump in and get your welding setup safe and solid.
To know more about welding, read our article: Is Welding Hard to Learn?
What Does Grounding Your Welder Mean?
Grounding your welder is an essential safety practice that involves connecting the metal components of your welding machine to the earth to prevent the buildup of electrical charge. This is done through various components, including a grounding clamp, grounding cable, and grounding rod.
In technical terms, grounding means creating a low-resistance path between the welding machine and the earth. This path allows any electrical charge that may build up in the machine to flow harmlessly into the earth. Without proper grounding, the electrical charge can build up and create a dangerous situation for the welder and anyone in the vicinity.
Prevent Electrical Shocks and Fires by Grounding Your Welder
Grounding your welder also helps to prevent electrical shocks and fires. The welding process generates a lot of heat and sparks, which can ignite flammable materials if not properly grounded. By grounding your welder, you can ensure that any stray electrical current is safely discharged into the earth.
Read related article: Welding Burns: Causes, Treatment, and Prevention
Why Grounding Your Welder is Essential
Grounding your welder is an essential step in the welding process. It is important for both your safety and the quality of your work. By grounding your welder, you complete the electrical circuit and create a safe working environment.
For Welder’s Safety
One of the main reasons why grounding your welder is important is for safety. When you ground your welder, you prevent the build-up of voltage that can cause electrical shock. Without proper grounding, you risk electrocution, which can be fatal. By grounding your welder, you also reduce the risk of fire and damage to your equipment.
Improved Welding Results
Grounding your welder also improves the quality of your welding results. When you ground your welder, you create an electrical circuit that allows the welder to create an arc. Without a good ground, you may experience poor weld quality and consumables, or even stop you from welding.
How to Ground a Welder: A Step-by-Step Guide
Grounding your welder is super important for keeping both you and your welding machine safe from any electric shocks.
To ground your welder the right way, you've got to hook up the grounding clamp to a clean piece of metal that's really close to where you're welding. Make sure the clamp is touching the metal well—there shouldn't be any dirt or oil in the way. It's got to be metal on metal. Also, check the grounding wire to be sure it's not damaged or worn out at all.
Here is a step-by-step guide to grounding your welder properly:
Select the Right Grounding Location
Before you begin, choose a location that is clean, dry, and free of any flammable materials. Your grounding location should be close to your welding area, and it should be a metal surface that is connected to the earth. Avoid using painted or coated surfaces, as they may not provide a good electrical connection.
Prepare the Welder for Grounding
Turn off the welder and unplug it from the power source. Remove any electrodes or welding wire, and clean the metal surface where you will attach the ground clamp.
Attach the Grounding Cable to the Welder
Locate the grounding cable on your welder. It is usually a thick, black cable with a clamp on the end. Connect the clamp to the metal surface you cleaned in step 2.
Prepare the Grounding Clamp
Inspect the grounding clamp for any damage or wear. If it is damaged, replace it before proceeding. Open the clamp and remove any debris or rust that may interfere with the electrical connection.
Connect the Grounding Clamp to the Workpiece
Place the workpiece on the metal surface you chose in step 1. Open the grounding clamp and attach it securely to the workpiece. Make sure the clamp is tight and that it makes good electrical contact with the workpiece.
Ensure Proper Grounding
Check the electrical connection between the welder, grounding cable, and grounding clamp. Make sure all connections are tight and secure. Turn on the welder and test the ground connection by welding a small test piece. If the weld is strong and consistent, your grounding is correct.
Stick to these steps, and you can ground your welder without any trouble. Always have your safety gear on—like welding gloves and glasses—when you're welding. If you're not sure about how to ground your welder or anything seems confusing, take a look at the instructions that came with it or ask someone who knows what they're doing.
Types of Grounding Clamps and Their Uses
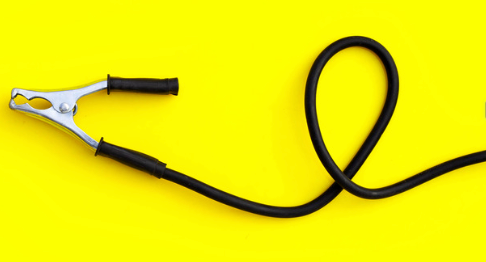
When you're grounding your welder, picking the right clamp is really important. There are all kinds of clamps out there, like ones made of copper, brass, bronze, and zinc. But most welders like to use copper or brass clamps the best.
Copper Clamps
Copper clamps are the most commonly used grounding clamps. They are highly conductive and durable, making them ideal for heavy-duty welding applications. Copper clamps are also resistant to corrosion and can withstand high temperatures.
Brass Clamps
Brass clamps are another popular type of grounding clamp. They are less conductive than copper clamps but are still effective for most welding applications. Brass clamps are also resistant to corrosion and can handle high temperatures.
Bronze Clamps
Bronze clamps are less commonly used than copper and brass clamps. They are highly conductive and durable, making them ideal for heavy-duty welding applications. Bronze clamps are also resistant to corrosion and can withstand high temperatures.
Zinc Clamps
Zinc clamps are the least conductive of all grounding clamps. They are suitable for light-duty welding applications and are not recommended for heavy-duty welding. Zinc clamps are also prone to corrosion and are not as durable as copper, brass, or bronze clamps.
Grounding Techniques and Equipment
Grounding is a crucial aspect of welding that ensures safety and good-quality welds. There are different grounding techniques and equipment that you can use to ground your welding machine. In this section, we will discuss some of the most common grounding techniques and equipment.
Grounding for Different Welding Machines
Different welding machines require different grounding techniques. For instance, MIG welding machines require a direct connection to the workpiece, while arc welding machines require a grounding clamp to be attached to a clean metal surface near the welding area. It is essential to follow the manufacturer's instructions on how to ground your welding machine properly.
Using Grounding Clamps and Conductors
Grounding clamps and conductors are essential equipment for grounding your welding machine. A grounding clamp is typically made of copper or brass and is used to complete the circuit, allowing the welder to create an arc. When using a grounding clamp, ensure that it has good surface contact, free from debris and grease, and that the contact is metal to metal. The clamp and clamp cable must be in good working condition to ensure a safe and effective connection.
Extension Cord Grounding Methods
Extension cords are commonly used in welding, and it is essential to test the welding machine's extension cord for its continuity regularly. One extension cord grounding method involves using a receptacle circuit tester to ensure that the extension cord is in good condition. Another method is to use a grounding wire to connect the extension cord to a clean metal surface near the welding area.
Common Grounding Mistakes and How to Avoid Them
Grounding is a crucial step in welding that ensures the safety and quality of the weld. However, there are common mistakes that people need to correct while grounding their welders that can lead to poor weld quality, equipment damage, and even injury. Here are some of the most frequent grounding mistakes and how to avoid them:
Mistake #1: Poor Ground Clamp Connection
One of the most common grounding mistakes is not connecting the ground clamp properly. The ground clamp should be connected to a clean, bare metal surface that is close to the welding area. If the ground clamp is not properly connected, it can cause electrical arcing, which can damage the equipment and create a safety hazard.
To avoid this mistake, make sure that the ground clamp is connected to a clean, bare metal surface that is close to the welding area. Also, make sure that the connection is tight and secure.
Mistake #2: Using a Damaged or Worn Ground Cable
Another common grounding mistake is using a damaged or worn ground cable. A damaged or worn ground cable can cause electrical arcing, which can damage the equipment and create a safety hazard.
To avoid this mistake, inspect the ground cable before each use. If you notice any signs of damage or wear, replace the cable immediately.
Mistake #3: Grounding Through a Painted or Coated Surface
Grounding through a painted or coated surface is another common grounding mistake. Paint and other coatings can create a barrier between the ground clamp and the metal surface, which can prevent a good electrical connection.
To avoid this mistake, make sure that the ground clamp is connected to a clean, bare metal surface. If the metal surface is painted or coated, remove the paint or coating before connecting the ground clamp.
Mistake #4: Using the Wrong Size Ground Cable
Using the wrong size ground cable is another common grounding mistake. If the ground cable is too small, it can cause electrical resistance, which can lead to poor weld quality and equipment damage.
To avoid this mistake, use a ground cable that is the correct size for your welding machine. Refer to the manufacturer's specifications to determine the correct size.
Conclusion
In How to Ground Your Welder, we covered everything you need to know to ground your welding machine correctly. Grounding is a critical safety step to prevent electric shocks and to make sure your welding is strong and clean.
As a welder myself, I can't stress enough the importance of always wearing your protective gear and double-checking your setup before starting.
If there's any doubt, better safe than sorry—check the manufacturer's instructions or talk to a pro.
Remember, a solid ground means safe and top-quality welding.
Frequently Asked Questions
What happens if you don't ground a welder?
If you don't ground your welder, you risk electrical shock, fire, and damage to your equipment. The ground provides a safe path for the electrical current to flow, which helps prevent electrical shock. It also helps protect your welding machine and other electrical devices from damage caused by electrical surges or other electrical problems. Without a good ground, you may experience poor weld quality, and consumables, or even stop you from welding.
Can you ground a welder with a magnet?
No, you cannot ground a welder with a magnet. A magnet does not provide a reliable ground connection for your welding machine. Instead, you should use a dedicated grounding clamp or connect it to a metal structure. A good ground connection is essential for safe and effective welding.
How do you ground a welding table?
To ground a welding table, you need to connect it to a suitable ground source. You can use a dedicated grounding clamp or connect it to a metal structure. The ground connection should be made as close to the welding zone as possible, and the clamp needs good surface contact, free from debris and grease. Contact must be metal to metal. Clam and clamp cable must be in good working condition.
Can you ground a welder?
Yes, you can ground a welder. To ground your welder, you can use a dedicated grounding clamp or connect it to a metal structure. The ground connection should be made as close to the welding zone as possible, and the clamp needs good surface contact, free from debris and grease. Contact must be metal to metal. Clam and clamp cable must be in good working condition.
What is the safety ground for welding?
The safety ground for welding is a grounding system that provides a safe path for electrical current to flow. It helps prevent electrical shock, fire, and damage to your equipment. The ground connection should be made as close to the welding zone as possible, and the clamp needs good surface contact, free from debris and grease. Contact must be metal to metal. Clam and clamp cable must be in good working condition.