FCAW vs. GMAW: Understanding the Key Differences in Welding Techniques
Mar 11, 2024
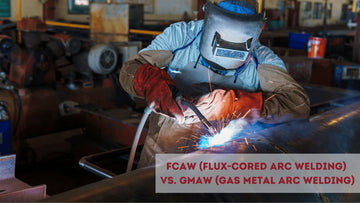
If you're new to welding, the different types of welding can be overwhelming. FCAW and GMAW are two of the most common welding types. Both are similar in many ways, but they have some significant differences that are important to understand. In this article, we'll explore the differences between FCAW and GMAW, the equipment and materials used, operational techniques, applications and suitability, and the advantages and disadvantages of each type of welding.
FCAW and GMAW are both arc welding processes that use an electric arc to create heat and melt metal. The main difference between the two is the type of electrode used. FCAW uses a continuously fed tubular electrode filled with flux, while GMAW uses a solid wire electrode. While both processes are similar in many ways, the type of electrode used affects the overall performance and suitability of each process. In the following sections, we'll explore the differences between these two welding processes, so you can choose the right one for your project.
Key Takeaways
- FCAW and GMAW are two of the most common welding types.
- FCAW uses a continuously fed tubular electrode filled with flux, while GMAW uses a solid wire electrode.
- The type of electrode used affects the overall performance and suitability of each process.
What is FCAW (Flux-Cored Arc Welding)?
If you are familiar with welding techniques, you may have heard of FCAW. FCAW stands for Flux-Cored Arc Welding, which is a type of welding process that uses a continuously fed wire electrode and a shielding gas to protect the weld from contamination.
In FCAW, the wire electrode contains a flux material that creates a shielding gas when it is melted by the arc. This shielding gas protects the weld from atmospheric contamination, which can cause defects in the weld. The flux also helps to remove impurities from the weld, improving its quality.
FCAW is a versatile welding process that can be used for both thick and thin materials. It is commonly used in the construction, shipbuilding, and automotive industries, as well as in the fabrication of heavy equipment and machinery.
Some typical applications of FCAW include welding of structural steel, pipelines, storage tanks, and pressure vessels. It is also used for welding of stainless steel and aluminum, although specialized equipment and techniques are required for these materials.
Overall, FCAW is a popular welding process due to its versatility, ease of use, and ability to produce high-quality welds.
What is GMAW (Gas Metal Arc Welding)?
Gas Metal Arc Welding (GMAW), also known as Metal Inert Gas (MIG) welding, is a welding process that uses a continuous solid wire electrode and shielding gas to create an electric arc between the electrode and the metal being welded. The shielding gas, usually a mixture of argon and carbon dioxide, protects the weld from atmospheric contamination and provides a stable arc.
GMAW is a versatile welding process that can be used on a wide range of metals, including steel, aluminum, and stainless steel. It is commonly used in automotive, construction, and manufacturing industries for its speed, efficiency, and ease of use.
One of the advantages of GMAW is its ability to weld in all positions, including overhead. It also produces a smooth, clean weld with minimal spatter. GMAW is ideal for welding thin materials, as the heat input can be easily controlled, and the process can be automated for high-volume production.
Common uses of GMAW include welding of sheet metal, pipes, and structural components. It is also used in the fabrication of machinery, equipment, and vehicles. GMAW is a popular welding process due to its flexibility, speed, and ease of use, making it a valuable tool for any welding project.
FCAW vs. GMAW: Know the Differences
When it comes to welding, there are many different processes to choose from. Two of the most popular welding techniques are FCAW (Flux-Cored Arc Welding) and GMAW (Gas Metal Arc Welding). While both techniques use an electric arc to create a weld, there are some key differences between them that you should be aware of.
Flux-Cored Arc Welding (FCAW)
FCAW is a welding process that uses a continuous wire feed and a flux-filled tubular electrode. The flux inside the electrode creates a shielding gas that protects the weld from contamination. This shielding gas also helps to stabilize the arc and improve the quality of the weld.
One of the biggest advantages of FCAW is that it can be used in a variety of positions, making it a versatile welding process. It is also a very efficient process, as it allows for high deposition rates and can be used to weld thicker materials.
Gas Metal Arc Welding (GMAW)
GMAW, also known as MIG (Metal Inert Gas) welding, is a welding process that uses a wire electrode and a shielding gas to create a weld. The shielding gas is typically a mixture of argon and carbon dioxide, which helps to protect the weld from contamination and stabilize the arc.
One of the advantages of GMAW is that it is a very clean process, as there is no flux involved. This means that there is less cleanup required after the weld is completed. GMAW is also a very fast process, as it allows for high deposition rates and can be used to weld thin materials.
FCAW vs. GMAW: The Differences
To help you understand the differences between FCAW and GMAW, we have created the following table:
FCAW |
GMAW |
Uses a flux-filled tubular electrode |
Uses a wire electrode |
Creates a shielding gas from the flux inside the electrode |
Uses a separate shielding gas |
Can be used in a variety of positions |
Best used in flat or horizontal positions |
Can be used to weld thicker materials |
Best used to weld thin materials |
Higher deposition rates |
Lower deposition rates |
More efficient process |
Cleaner process |
As you can see, both FCAW and GMAW have their own unique advantages and disadvantages. When deciding which process to use, it is important to consider the materials you will be welding, the position you will be welding in, and the quality of the weld you require.
FCAW Equipment and Materials Used
Flux-Cored Arc Welding (FCAW) is a widely used welding process, particularly in construction, heavy equipment manufacturing, and shipbuilding. Here's a list of the essential equipment and materials used in FCAW
- Welding Machine: This is the power source for FCAW, providing the necessary current for the welding process. These machines can be either constant voltage (CV) or constant current (CC) types, depending on the application.
- Wire Feeder: This component feeds the flux-cored wire at a controlled rate. It's crucial for maintaining a consistent welding speed and quality.
- Flux-Cored Wire: This is the consumable electrode used in FCAW. It has a hollow center filled with flux, which provides necessary elements for shielding the weld pool from atmospheric contamination.
- Welding Gun and Cable Assembly: The welding gun controls the delivery of the wire and shielding gas to the weld pool, if gas-shielded FCAW is being used. The cable assembly provides power and material feed to the gun.
- Shielding Gas and Supply System (for Gas-Shielded FCAW): In gas-shielded FCAW, an external shielding gas (commonly CO2 or a mixture of Argon and CO2) is used. The supply system includes gas cylinders, regulators, and hoses.
- Contact Tips: These are replaceable components that conduct welding current to the wire. The size of the contact tip matches the diameter of the welding wire.
- Nozzle: The nozzle directs the shielding gas (if used) over the welding area and can protect the contact tip from spatter.
- Electrode Holder: For self-shielded FCAW, an electrode holder may be used. It's designed to hold the flux-cored wire and is part of the circuit.
- Personal Protective Equipment (PPE): This includes welding helmets, gloves, and protective clothing. PPE is essential for the safety of the welder, providing protection against sparks, spatter, and harmful radiation.
- Wire Brush and Chipping Hammer: Used for cleaning the weld area and removing slag, which is a byproduct of the flux in FCAW.
- Ground Clamp: This is used to complete the electrical circuit. It's clamped to the workpiece or a metal surface connected to the workpiece.
GMAW Equipment and Material Used
GMAW (Gas Metal Arc Welding), also known as MIG (Metal Inert Gas) welding, uses a welding gun, wire feeder, and contact tip similar to FCAW. However, in GMAW, a solid wire electrode is used instead of a tubular wire electrode. The shielding gas, typically a mixture of CO2 and argon, is provided through the welding gun.
Here is a list of the essential equipment and materials used in GMAW, along with a description of each:
- Welding Machine: This is the central power source for GMAW, providing the electrical current required for welding. It can be either constant voltage (CV) or constant current (CC), with CV being more common in GMAW.
- Wire Feeder: This component feeds the welding wire from the spool at a consistent rate. It's crucial for maintaining a uniform weld bead.
- Welding Gun: The welding gun controls the delivery of the wire and shielding gas to the weld area. It includes a trigger to control the wire feed and the arc.
- Welding Wire: This is a consumable electrode, coming in various diameters and compositions to suit different applications. The wire is usually a mild steel, stainless steel, or aluminum alloy.
- Shielding Gas and Supply System: GMAW uses an external shielding gas (commonly Argon, Carbon Dioxide, or a mixture) to protect the weld area from atmospheric contamination. The system includes gas cylinders, regulators, flow meters, and hoses.
- Contact Tip: A replaceable component in the welding gun through which the welding wire passes. It must match the wire diameter and is essential for good electrical contact.
- Gas Nozzle: This part of the gun directs the shielding gas around the welding wire and into the weld pool. It helps protect the weld from oxidation and contamination.
- Ground Clamp: This is used to complete the electrical circuit. It's attached to the workpiece or the work table.
- Personal Protective Equipment (PPE): Includes items like a welding helmet with appropriate shading, gloves, and protective clothing to safeguard the welder from sparks, spatter, and UV radiation.
- Wire Brush and Chipping Hammer: These are used for cleaning the weld surface and removing any slag or spatter.
- Welding Wire Spool: This is the supply of welding wire, available in various sizes depending on the welder's requirements.
FCAW Welding Techniques
When it comes to Flux-Cored Arc Welding (FCAW), there are a few operational techniques you should keep in mind. First, you need to adjust the heat and speed settings based on the thickness of the material you're welding. The thicker the material, the higher the heat and slower the speed. You also need to control the amperage and travel speed to ensure a consistent weld.
One technique that can help you achieve a smooth weld is to pause at the end of each pass. This allows the weld to cool slightly, reducing the likelihood of burn-through or distortion. Additionally, you can use a weaving motion to create a wider weld bead and increase penetration.
GMAW Welding Techniques
Gas Metal Arc Welding (GMAW) also requires careful attention to operational techniques. One important factor is controlling the heat input to avoid overheating the material. You should adjust the voltage and wire feed speed based on the thickness of the material and the desired weld size.
Another technique to keep in mind is maintaining a consistent travel speed. This helps ensure a uniform weld and prevents burn-through. You can also use a push or pull technique to control the direction of the weld and reduce the likelihood of defects.
Overall, both FCAW and GMAW require attention to detail and careful control of the welding process. By adjusting the heat, speed, and amperage settings, and using techniques like pausing and weaving, you can achieve high-quality welds with either process.
Flux-cored Arc Applications
Flux-cored arc welding (FCAW) is particularly useful for welding thicker materials and for outdoor welding because it is less affected by wind and drafts than gas-metal arc welding (GMAW). FCAW is also suitable for welding dirty or rusty materials, making it a popular choice in industrial settings.
FCAW is commonly used for welding mild steel, stainless steel, and aluminum. It is a popular choice for welding structural steel, such as in the construction of buildings and bridges. FCAW is also used in the fabrication of industrial machines and equipment, such as mining machinery and agricultural equipment.
Gas Metal Arc Welding Applications
Gas metal arc welding (GMAW), also known as metal inert gas (MIG) particularly suitable for welding thin materials, making it a popular choice for welding sheet metal and other thin materials.
GMAW is commonly used for welding steel, stainless steel, and aluminum. It is a popular choice for welding in indoor settings, such as in the manufacturing of automobiles and other machinery. GMAW is also used for welding outdoor structures, such as fences and gates.
In general, FCAW is a better choice for welding thicker materials and for outdoor welding, while GMAW is a better choice for welding thinner materials and for indoor welding. However, the choice between the two processes ultimately depends on the specific application and the materials being welded.
FCAW and GMAW Advantages and Disadvantages
Here's a table comparing the advantages and disadvantages of FCAW (Flux-Cored Arc Welding) and GMAW (Gas Metal Arc Welding):
Aspect |
FCAW Advantages |
GMAW Advantages |
---|---|---|
Deposition Rate | Higher deposition rate; lays down more weld metal quickly. | Lower deposition rate. |
Versatility | Suitable for thicker materials and outdoor environments. | Limited in welding thicker materials and not ideal for outdoors. |
Portability | More portable as it doesn't require a shielding gas cylinder. | Requires a shielding gas cylinder, affecting portability. |
Weld Appearance | May produce more spatter and porosity. | Cleaner welds with less porosity and spatter. |
Cost-Effectiveness | Less cost-effective due to need for consumables like flux-core wire. | More cost-effective, uses less filler metal, lower cost per pound. |
Aspect |
FCAW Disadvantages |
GMAW Disadvantages |
---|---|---|
Porosity & Spatter | Produces more porosity and spatter, leading to more cleanup. | Produces cleaner welds with less cleanup needed. |
Cost | Requires additional consumables like flux-core wire, increasing costs. | More cost-effective in terms of filler metal and overall expenses. |
Versatility | More versatile in different environments and material thicknesses. | Less versatile, not suitable for thicker materials or outdoors. |
Deposition Rate | Faster deposition rates, efficient for larger projects. | Slower deposition rates, may take longer for project completion. |
This table outlines the key points of comparison between FCAW and GMAW, highlighting their strengths and limitations in various welding scenarios.
Common Misconceptions About FCAW and GMAW
When it comes to welding, there are many misconceptions about the different methods, including Flux-Cored Arc Welding (FCAW) and Gas Metal Arc Welding (GMAW). Here are a few common misconceptions that you should be aware of:
Misconception #1: FCAW is always better than GMAW
While FCAW can be a great option for certain applications, it is not always better than GMAW. FCAW can produce a higher deposition rate and deeper penetration than GMAW, but it can also produce more spatter and require more cleanup. GMAW can produce a cleaner weld, but it may not be as suitable for thicker materials.
Misconception #2: FCAW is only for outdoor welding
While FCAW is often used for outdoor welding because it can handle windy conditions and does not require a shielding gas, it can also be used for indoor welding. In fact, FCAW can be a great option for welding in tight spaces or hard-to-reach areas.
Misconception #3: GMAW is always more expensive than FCAW
While GMAW does require a shielding gas, which can add to the cost, it can also be more efficient than FCAW in terms of material usage and cleanup. Additionally, the cost of FCAW wire can vary depending on the type and quality, so it is not always a cheaper option.
Misconception #4: FCAW and GMAW are interchangeable
While these two welding methods may seem similar, they are not interchangeable. FCAW requires a flux-cored wire and does not require a shielding gas, while GMAW requires a solid wire and a shielding gas. Attempting to use the wrong wire or gas can result in a poor-quality weld.
By understanding these common misconceptions about FCAW and GMAW, you can make informed decisions about which welding method is best for your specific application.
Advantages of FCAW Over GMAW
If you are considering using Flux-Cored Arc Welding (FCAW) or Gas Metal Arc Welding (GMAW) for your welding project, you may want to know the advantages of FCAW over GMAW. Here are some of the advantages that FCAW offers:
-
FCAW is more versatile than GMAW. It can be used for welding thicker materials and in a wider range of positions, including overhead welding. This makes it a better choice for welding structural steel, heavy equipment, and pipelines.
-
FCAW produces a higher deposition rate than GMAW. This means that you can weld faster and complete your project in less time. This is especially useful for large-scale welding projects.
-
FCAW is more tolerant of dirty or rusty materials than GMAW. This is because the flux in FCAW helps to clean the metal as it is being welded. This makes FCAW a better choice for welding materials that are not perfectly clean.
-
FCAW is more cost-effective than GMAW. This is because FCAW uses a flux-cored wire that is more efficient than the solid wire used in GMAW. This means that you will use less wire and spend less money on consumables.
-
This means that you can weld thicker materials with a FCAW produces a deeper penetration than GMAW.single pass. This is especially useful for welding materials that require a high degree of penetration, such as pressure vessels and structural steel.
In summary, FCAW offers several advantages over GMAW, including greater versatility, higher deposition rates, better tolerance of dirty or rusty materials, lower cost, and deeper penetration. If these advantages are important to your welding project, you may want to consider using FCAW instead of GMAW.
Advantages of GMAW Over FCAW
When it comes to welding, there are several methods to choose from. Two of the most popular methods are Gas Metal Arc Welding (GMAW) and Flux-Cored Arc Welding (FCAW). While both methods have their advantages, GMAW has several distinct advantages over FCAW.
Here are some advantages of GMAW over FCAW:
-
Cleaner Welds: GMAW produces a cleaner weld than FCAW because it uses a shielding gas to protect the weld from contaminants in the air. FCAW, on the other hand, uses a flux that can leave slag on the weld, which must be removed after welding.
-
Higher Quality Welds: GMAW produces higher quality welds than FCAW because it uses a more precise heat input and produces less spatter. This means that GMAW is better suited for welding thin materials and producing aesthetically pleasing welds.
-
Less Smoke and Fumes: GMAW produces less smoke and fumes than FCAW because it uses a shielding gas instead of a flux. This makes GMAW a better choice for welding in confined spaces or areas with poor ventilation.
-
Easier to Learn: GMAW is easier to learn than FCAW because it requires less skill to produce a good weld. This makes GMAW a better choice for beginners or those who need to produce a large number of welds quickly.
-
Lower Cost: GMAW is generally less expensive than FCAW because it requires less equipment and consumables. This makes GMAW a better choice for those who need to produce a large number of welds on a budget.
Overall, GMAW has several advantages over FCAW. It produces cleaner, higher quality welds, produces less smoke and fumes, is easier to learn, and is generally less expensive. If you're looking for a welding method that is versatile, produces high-quality welds, and is easy to learn, GMAW is an excellent choice.
Choosing Between FCAW and GMAW
When it comes to choosing between FCAW and GMAW, there are a few factors to consider. Both welding processes have their advantages and disadvantages, and the decision ultimately depends on your specific welding needs.
Here are some reasons why you might choose FCAW:
- FCAW is a versatile process that can be used on a variety of materials, including stainless steel, aluminum, and nickel alloys.
- FCAW is ideal for welding thicker materials, as it produces deeper penetration than GMAW.
- FCAW is a cost-effective option, as it does not require a shielding gas.
On the other hand, here are some reasons why you might choose GMAW:
- GMAW produces a cleaner weld than FCAW, as it does not produce slag.
- GMAW is a faster process than FCAW, as it uses a continuous wire feed.
- GMAW is a good option for welding thinner materials, as it produces less heat and distortion.
Ultimately, the choice between FCAW and GMAW depends on your specific welding needs. Consider the material you are welding, the thickness of the material, and the desired outcome of the weld. With these factors in mind, you can make an informed decision on which process is right for you.
Conclusion
In conclusion, both FCAW and GMAW welding processes have their own advantages and disadvantages. It is important to consider the specific needs of your project when deciding which welding process to use.
If you are looking for a welding process that is cost-effective and provides high deposition rates, GMAW may be the right choice for you. However, if you need to weld thicker materials or work in outdoor environments with wind and draft, FCAW may be a better option due to its ability to produce a stronger weld and its self-shielding capabilities.
Ultimately, the decision between FCAW and GMAW will depend on your specific project needs, budget, and skill level. It is important to do your research and seek guidance from a professional before making a final decision.
Frequently Asked Questions
Why is FCAW used instead of GMAW?
FCAW is often used instead of GMAW because it provides higher deposition rates, deeper penetration, and better weld quality. FCAW also allows for welding thicker materials and can be used in outdoor environments where wind can affect the shielding gas used in GMAW.
What are the differences between a GMAW and FCAW gun?
The main difference between a GMAW and FCAW gun is the type of wire used. GMAW uses a solid wire, while FCAW uses a tubular wire filled with flux. FCAW guns are also typically larger and heavier than GMAW guns due to the larger wire size and the need for a larger motor to feed the wire.
What metals cannot be welded with FCAW?
FCAW is not recommended for welding aluminum or other non-ferrous metals. It is also not recommended for welding materials that are thinner than 20 gauge.
What is the difference between FCAW and MIG welding?
FCAW and MIG welding are similar in that they both use a wire feed to deposit filler metal. However, FCAW uses a tubular wire filled with flux, while MIG welding uses a solid wire and a shielding gas. FCAW is typically used for welding thicker materials and in outdoor environments, while MIG welding is better suited for thinner materials and indoor applications.