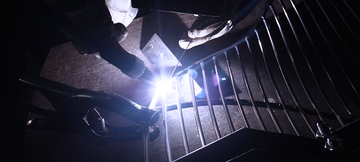
What is the cold welding machine
Cold welding is a process that joins two pieces of metal together without using heat, solder, or any other external substance. Cold welding machines use high pressure to create a molecular bond between the two metal surfaces.
The basic principle of cold welding is that when two clean metal surfaces are brought into contact under high pressure, the atoms on the surface of the metal become excited and bond together, creating a strong, permanent joint. Cold welding is particularly useful for joining metals that are difficult to weld by other means, such as aluminum, copper, and other non-ferrous metals.
Cold welding machines typically consist of a hydraulic or pneumatic press that applies pressure to the metal surfaces, as well as a set of tooling or dies that hold the parts in place during the welding process. Some cold welding machines are capable of welding large or irregularly-shaped parts, while others are designed for smaller or more intricate work.
Cold welding is commonly used in the aerospace, automotive, and electronics industries, as well as in the production of jewelry, medical devices, and other precision parts.
The buy factors you need to consider when buy cold welding machine
Here are the general steps you can follow to buy a cold welding machine:
-
Determine your needs: Before you start shopping for a cold welding machine, determine your specific needs. Consider the materials you will be welding, the size and shape of the parts you will be working with, the production volume you require, and any other special features or capabilities you need.
-
Research available options: Once you have a clear understanding of your needs, research the available options. Look for reputable manufacturers and suppliers, and compare different machines based on their features, specifications, and price.
-
Check reviews and testimonials: Look for reviews and testimonials from other customers who have used the machine you are considering. This can give you valuable insights into the machine's performance, reliability, and ease of use.
-
Contact the supplier: Once you have narrowed down your options, contact the supplier or manufacturer directly. Ask any questions you have about the machine, including its specifications, features, and warranty. You can also ask for a quote and information about financing options if needed.
-
Make a purchase: Once you have decided on a machine that meets your needs and budget, make a purchase. Make sure to carefully review the terms and conditions of the sale, including the warranty and return policy.
-
Arrange for delivery and installation: If necessary, arrange for the delivery and installation of your cold welding machine. Make sure to follow all safety guidelines and instructions provided by the manufacturer or supplier.
-
Train operators: Finally, make sure to train operators on the safe and proper use of the machine. This can help ensure optimal performance and prevent accidents or injuries.
Cold welding machine price
The price of a cold welding machine can vary widely depending on the size, capacity, and features of the machine. Generally speaking, smaller and simpler machines designed for hobbyist or small-scale use can cost anywhere from a few hundred to a few thousand dollars, while larger, industrial-grade machines with advanced features and capabilities can cost tens of thousands of dollars or more.
It's important to note that the cost of a cold welding machine is just one factor to consider when deciding which machine to purchase. Other important considerations include the types of metals and parts you will be welding, the size and complexity of the parts, the production volume and speed you require, and the level of precision and accuracy you need.
If you're interested in purchasing a cold welding machine, it's a good idea to research the different options available and compare prices and features before making a purchase. You may also want to consult with a welding expert or supplier to help you determine the best machine for your needs and budget.
The usage scenarios of cold welding machine
Cold welding machines can be used in a variety of scenarios, depending on the specific needs of the application. Here are some common usage scenarios for cold welding machines:
-
Aerospace and aviation: Cold welding machines are used in the aerospace and aviation industries to repair or join thin-walled components, such as fuel tanks, engine components, and hydraulic lines.
-
Automotive: Cold welding machines are used in the automotive industry to repair or join aluminum and other non-ferrous materials, such as oil coolers, radiators, and transmission lines.
-
Electronics: Cold welding machines are used in the electronics industry to bond components and wires without using heat or solder, which can damage delicate electronic components.
-
Jewelry making: Cold welding machines are used in the jewelry making industry to join precious metals without using heat or solder, which can damage the metals and their finishes.
-
Medical devices: Cold welding machines are used in the production of medical devices, such as surgical instruments and implants, to create strong, precise, and biocompatible joints.
-
Research and development: Cold welding machines are used in research and development to join metals without altering their properties, allowing for precise testing and analysis of the material's characteristics.
-
Welding of dissimilar materials: Cold welding machines can be used to join dissimilar metals, such as aluminum to copper or titanium to stainless steel, which can be difficult or impossible to weld using traditional methods.
Overall, cold welding machines are particularly useful in applications where heat, solder, or other external substances cannot be used or may cause damage to the material or the surrounding environment.
What kind of metal is suitable for welding cold welding machine
Cold welding machines are typically used for welding non-ferrous metals, which are metals that do not contain iron. This is because non-ferrous metals do not easily bond with each other using traditional welding methods, such as heat-based welding or soldering.
Some common non-ferrous metals that are suitable for welding with a cold welding machine include:
-
Aluminum: Cold welding machines can be used to weld aluminum components in the aerospace, automotive, and electronics industries.
-
Copper: Cold welding machines can be used to weld copper components in the electrical and electronics industries.
-
Brass: Cold welding machines can be used to weld brass components in the plumbing and electrical industries.
-
Nickel: Cold welding machines can be used to weld nickel components in the aerospace and electronics industries.
-
Silver: Cold welding machines can be used to weld silver components in the jewelry and electronics industries.
-
Gold: Cold welding machines can be used to weld gold components in the jewelry and electronics industries.
It's important to note that the suitability of a metal for cold welding depends on several factors, including the cleanliness and surface finish of the metal, the pressure applied during the welding process, and the skill and experience of the operator. Before welding any metal with a cold welding machine, it's important to carefully follow the manufacturer's instructions and guidelines, and to perform a thorough test to ensure the quality and strength of the joint.
The Pros and Cons of Cold Welding Machine
Cold welding machines, also known as cold pressure welders, are used to join two pieces of metal together through a process of pressure without the use of heat. This method of welding offers several advantages and disadvantages, which are discussed below:
Pros:
-
No heat required: Cold welding machines do not use heat, which means that they do not produce any harmful fumes or gases. This makes them safer to use than other welding methods, particularly in enclosed spaces.
-
High-quality welds: Cold welding machines create high-quality, permanent welds that are free from oxidation, contamination, and distortion. This is particularly useful for joining delicate or heat-sensitive materials, such as wires or thin sheets.
-
Cost-effective: Because cold welding machines do not require consumables, such as electrodes or shielding gas, they are more cost-effective than other welding methods over the long-term.
-
Environmentally-friendly: Cold welding machines are environmentally-friendly because they produce no waste, use no consumables, and do not emit any harmful gases.
Cons:
-
Limited applications: Cold welding machines are best suited for joining thin materials, such as wires or sheets, and may not be suitable for thicker materials or more complex shapes.
-
High initial cost: Cold welding machines can be expensive to purchase initially, which may be a barrier for some users.
-
Limited joint strength: While cold welding machines create high-quality welds, the strength of the joint may not be as high as those created by other welding methods.
-
Limited availability: Cold welding machines are not as widely available as other welding methods, which may make them harder to access for some users.
Overall, cold welding machines can be a useful welding method for certain applications, particularly those that require precision, safety, and environmental-friendliness. However, they may not be suitable for all welding needs and may have some limitations in terms of joint strength and material thickness.