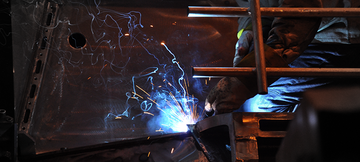
¿Cómo soldar aluminio? Quizás se esté preguntando acerca de esto, que es realmente un proyecto muy difícil para los recién llegados a la soldadura. Este artículo será una guía definitiva para ayudarle a aprender más sobre cómo soldar material de aluminio. Este es el esquema del artículo.
- Introducción
- Características del aluminio
- Designación de aleaciones de aluminio.
- Problemas de soldabilidad del aluminio.
- Selección de materiales de relleno para soldadura.
- Preparación para soldar
- Procesos de soldadura utilizados en la soldadura de aluminio.
- Soldadura TIG
- soldadura MIG
- MIG pulsado
Introducción
El aluminio y sus aleaciones pertenecen a los materiales no ferrosos y se caracterizan por su peso ligero y alta resistencia a la corrosión, por lo que estas aleaciones se utilizan en muchas aplicaciones importantes:
- Aviones: donde el aluminio representa alrededor del 80% del peso de un avión civil típico (fig. 1)
- Superestructuras de graneleros y buques (fig. 2)
- Material rodante ferroviario, mobiliario de carretera, tuberías y recipientes a presión, grandes estructuras civiles y militares como puentes y en la fabricación de láminas que se utilizan en la industria del embalaje.
- Vehículos blindados militares donde una combinación de peso ligero y rendimiento balístico lo convierte en el material ideal para vehículos militares rápidos (fig. 3).

Fig. 1 Avión conceptual Boeing SUGAR Volt ‐ Wikimedia Commons

Fig. 2 barcos construidos principalmente con aluminio.

Fig. 3 Vehículo blindado de transporte de personal del ejército M113.
Entonces, debido a la diversidad de usos modernos de las aleaciones de aluminio, el ingeniero de soldadura debe conocer los diferentes tipos de aleaciones de aluminio y cómo soldarlas sin ninguna degradación de sus propiedades, por eso en este artículo repasaremos los diferentes tipos de aleaciones de aluminio. aleaciones y los procedimientos de soldadura adecuados que se deben seguir y las técnicas de soldadura modernas utilizadas para soldar este tipo de aleaciones.
Características del aluminio
Hay algunas características del aluminio y sus aleaciones que se deben tener en cuenta:
- La gran diferencia entre el punto de fusión del aluminio y el óxido de aluminio, donde el punto de fusión del aluminio es de 1400 grados centígrados y el del óxido de aluminio es de 2060 grados centígrados, por lo que a medida que se forma óxido de aluminio durante la soldadura, resulta muy difícil tener soldadura sana debido a la falta de fusión del óxido de aluminio debido a su mayor punto de fusión, por lo que hay que utilizar una técnica para romper esta capa de óxido de forma continua durante la soldadura.
- La película de óxido sobre el aluminio es duradera, muy tenaz y autorreparable y se forma a temperatura normal, es por eso que las aleaciones de aluminio tienen una excelente resistencia a la corrosión sin ninguna protección adicional y, en consecuencia, se vuelven adecuadas para aplicaciones expuestas como aviones.
- La soldadura de aluminio incluye una alta probabilidad de distorsión en relación con el acero, ya que el coeficiente de expansión térmica del aluminio es aproximadamente el doble que el del acero.
- Alta disipación del calor de soldadura durante la soldadura en relación con el acero debido a la alta conductividad térmica del aluminio que alcanza 6 veces la del acero, además del alto calor específico del aluminio que alcanza 2 veces la del acero. Es por eso que la soldadura de aluminio requiere una fuente de calor altamente concentrada mediante el uso de procesos pulsados para lograr una fusión completa.
- La soldadura por puntos de resistencia del aluminio es muy difícil debido a la alta conductividad eléctrica del aluminio, que alcanza las tres cuartas partes de la del cobre pero seis veces la del acero.
- El aluminio no cambia de color a medida que aumenta la temperatura, a diferencia del acero. Esto puede dificultar que el soldador juzgue cuándo está a punto de producirse la fusión, lo que hace imperativo que se lleve a cabo una recapacitación adecuada del soldador al pasar de la soldadura de acero a la de aluminio.
- El aluminio no es magnético, lo que significa que el golpe de arco se elimina como problema de soldadura.
- El hecho de que el aluminio tenga una estructura cristalina cúbica centrada en las caras (ver Fig. 4) significa que no sufre una pérdida de tenacidad a la entalla cuando se reduce la temperatura. Por este motivo, el aluminio se utiliza en aplicaciones criogénicas hasta una temperatura de -200 grados centígrados.
- El aluminio tiene la misma estructura cristalina en los ciclos de calentamiento y enfriamiento, a diferencia del acero, que sufre transformaciones cristalinas, por lo que el enfriamiento rápido no tiene efecto en las aleaciones de aluminio.

Fig. 4 Celda unitaria cúbica centrada en la cara
Designación de aleaciones de aluminio.
Existe un método numérico adoptado por el Comité Europeo de Normalización (CEN) que se utilizará como estándar. Este sistema utiliza cuatro dígitos para identificar las aleaciones forjadas y cinco dígitos para identificar las aleaciones fundidas.
Tabla 1: Clasificación de aleaciones de aluminio forjado.
Clasificación digital |
Elemento de aleación |
AW1XXX |
Aluminio comercialmente puro |
AW 2XXX |
Aleaciones de aluminio y cobre |
AW3XXX |
Aleaciones de aluminio y manganeso |
AW 4XXX |
Aleaciones de aluminio y silicio |
AW5XXX |
Aleaciones de aluminio y magnesio |
AW6XXX |
Aleaciones de aluminio, magnesio y silicio |
AW7XXX |
Aleaciones de aluminio, zinc y magnesio |
AW8XXX |
Otros elementos, por ejemplo, litio, hierro. |
AW9XXX |
No se han asignado grupos de aleaciones. |
Tabla 2: Clasificación de aleaciones de aluminio fundido.
Clasificación digital |
Elemento de aleación |
CA 2 1XXX |
Al-Cu |
CA 4 1XXX |
Al-SiMgTi |
CA 4 2XXX |
Al-Si7Mg |
CA 4 3XXX |
Al-Si10Mg |
CA 4 4XXX |
Al Si |
CA 4 5XXX |
Al-Si5Cu |
CA 4 6XXX |
Al-Si9Cu |
CA 4 7XXX |
Al-Si(Cu) |
CA 4 8XXX |
Al-SiCuNiMg |
CA 5 1XXX |
Al-Mg |
CA 7 1XXX |
Al-ZnMg |
En el sistema europeo se utilizan los prefijos:
- 'AB' indica lingotes para refundir.
- 'AC' indica un producto fundido.
- 'AM' es una aleación maestra fundida.
- El prefijo 'AW' es un producto forjado.
Problemas de soldabilidad del aluminio.
Antes de profundizar en los procesos y técnicas de soldadura utilizados en la soldadura, primero debemos conocer los desafíos comunes que enfrenta como ingeniero de soldadura, supervisor de soldadura y soldador durante la soldadura de aluminio y aleaciones de aluminio:

Fig. 5 Porosidad finamente distribuida en soldadura a tope de placa TIG de 6 mm de espesor. Cortesía de TWI Ltd.
Los gases que causan porosidad provienen de la humedad en las juntas o de los gases protectores utilizados. El cambio repentino en la solubilidad de gases como el H2 es la principal razón de la porosidad (ver en la Fig. 6), por lo que es extremadamente difícil producir una soldadura libre de porosidad en aluminio.

Fig. 6 Solubilidad del hidrógeno en aluminio.
Tabla 3: Resumen de causas y prevenciones de la porosidad.
Mecanismo de formación de porosidad. |
Causas potenciales |
Medidas correctivas |
Atrapamiento de hidrógeno |
|
|
Atrapamiento de gas/aire |
|
|
Gas atrapador de congelación rápida |
|
|
Alimentación de alambre errática |
|
punta de contacto, ajustar la presión del rodillo impulsor, colocar el revestimiento correcto, colocar los rodillos ranurados. |
En la soldadura MIG, existe un fenómeno conocido como limpieza catódica para romper la capa de óxido formada donde el electrodo está conectado al polo positivo de la fuente de energía en el que los electrones fluyen desde la pieza de trabajo al electrodo y los iones fluyen en la dirección opuesta. resultando en la rotura de la capa de óxido.
Pero hay un punto importante que explicar: ¿por qué utilizamos corriente CA y DCEP durante la soldadura MIG y CA sólo para la soldadura TIG?

Fig. 7 Física del arco para el proceso de soldadura MIG.
Fig. 8 Física del arco para el proceso de soldadura TIG.

Fig. 9 Física del arco con polaridad de corriente cambiante
De las figuras 7, 8 y 9, es evidente que el comportamiento al usar electrodo negativo y electrodo positivo no es el mismo, ya que la naturaleza de los electrodos utilizados no es la misma donde en la soldadura MIG el metal de aportación es el electrodo mismo, que es aluminio. tener la misma cantidad de electrones en la escala atómica donde el aluminio tiene 13 electrones, por lo que el poder de emisión de electrones es el mismo que el del metal base, es por eso que el electrodo positivo en MIG es muy adecuado para tener una penetración profunda ya que el área de superficie del metal base es muy grande en relación con el electrodo, lo que da como resultado un arco estable y una limpieza catódica.
Por otro lado en la soldadura TIG, el arco se inicia utilizando electrodos no consumibles como el tungsteno que tiene más electrones en la escala atómica donde cada átomo tiene 74 electrones, por eso es más adecuado TIG con electrodo negativo ya que logra mayor penetración como se muestra. en las figuras anteriores debido a la alta tasa de emisión de electrones durante el ensamblaje del proceso negativo del electrodo, pero este proceso no es eficiente para soldar aluminio ya que no ayuda en la limpieza catódica, es por eso que se recomienda la soldadura AC mediante TIG para el aluminio.
Por el nombre del problema, está claro que este problema ocurre durante la soldadura cuando el metal de soldadura aún está caliente y este problema es muy común durante la soldadura de algunas aleaciones de aluminio debido a la presencia de componentes de bajo punto de fusión a lo largo de los límites de grano de la matriz solidificada. .

Fig. 10 Grietas por solidificación en una placa A6082 de 3 mm de espesor utilizando soldadura TIG de metal de aportación 4043. Cortesía de TWI Ltd.

Fig. 11 Efecto de la concentración de átomos de soluto sobre la sensibilidad al craqueo en caliente.
Como se muestra en la Fig. 11, la sensibilidad al craqueo en caliente depende principalmente de la concentración del elemento de aleación en la aleación de aluminio.
En resumen, si se produce craqueo en caliente, existen algunos factores que se pueden utilizar para eliminar dicho problema:
- El uso de alambres de relleno que pueden producir soldaduras de tamaño de grano pequeño y esto puede suceder mediante la adición de titanio, circonio o escandio actuará como núcleos para la formación de un grano muy fino durante la solidificación.
- Preparación adecuada de las juntas soldadas controlando la preparación de los bordes y el espaciamiento de las juntas para permitir que se agregue suficiente metal de aportación a la junta para controlar que la composición del metal de soldadura esté fuera del rango corto de temperatura.
- Acortamiento del tiempo en el rango corto en caliente mediante el uso de alta velocidad de soldadura.
Selección de materiales de relleno para soldadura.
Los metales de aportación de aluminio se seleccionan en función de los problemas que preocupan al ingeniero de soldadura, como la resistencia al agrietamiento, la resistencia, el color y la resistencia a la corrosión, a diferencia de la selección de metales de aportación de acero que se seleccionan en función de las propiedades químicas y mecánicas.
AWS A5.10 “Especificación para varillas y electrodos de soldadura de aluminio desnudo y aleaciones de aluminio” incluye 15 composiciones de metal de aportación independientes, que comprenden aleaciones de las series 1XXX, 2XXX, 4XXX y 5XXX.
Tabla 4: Guía para la selección del material de relleno
Metal de origen |
1050 1080 1200 |
2219 |
3103 3105 |
5005 5083 5251 5454 |
6061 6063 6082 |
7005 7019 7020 7039 |
8090 |
8090 |
5556 |
5556 |
|||||
7039 |
5556 |
5556 |
5356 |
5556 |
5556 |
||
7019 |
5356 |
5356 |
5356 |
5356 |
|||
7020 |
5183 |
5183 |
5183 |
5183 |
|||
7005 |
5039 |
||||||
6061 |
5356 |
4043 |
5356 |
5556 |
|||
6063 |
5356 |
5356 |
|||||
6082 |
4043 |
5183 |
|||||
5454 |
5356 |
5356 |
5356 |
||||
5251 |
5356 |
5356 |
5056 |
||||
5083 |
5356 |
5356 |
|||||
5005 |
5356 |
||||||
3103 |
5356 |
2319 |
5356 |
5356 |
5356 |
5556 |
5556 |
3105 |
4043 |
5056 |
5356 |
||||
2219 |
4043 2319 |
2319 |
|||||
1050 |
4043 |
2319 |
|||||
1080 |
1050 |
4043 |
|||||
1200 |
1080 |
Hay una serie de puntos específicos que se deben señalar para ampliar la orientación proporcionada en las Tablas 4:
- Cuando suelde aleaciones que contengan más del 2 % de magnesio, evite utilizar metales de aportación que contengan silicio para evitar la formación de compuestos intermetálicos de siliciuro de magnesio (Mg3Si) que provocan la fragilización de las juntas.
- Cuando se utilizan metales de aportación 5XXX con más del 5% de Mg como 5654, se debe considerar que la temperatura de servicio no excede los 65 grados centígrados para evitar la formación de Al2Mg, lo que hace que la aleación sea susceptible a la corrosión por tensión. En este caso, debes utilizar metales de aportación con menor contenido de Mg, como 5454 o 5554, que contienen 3 % de Mg.
- Se prefiere el 5654 de alta pureza para soldar aluminio de alta pureza en servicio de peróxido de hidrógeno.
- 4643 debe usarse con aleaciones 6XXX ya que el pequeño contenido de magnesio mejorará la respuesta al tratamiento con solución.
- Las aleaciones de aluminio puro 1XXX son muy blandas y dúctiles, por lo que se pueden experimentar problemas de alimentación de alambre.
- Las aleaciones 5XXX con bajo contenido de magnesio (<2%) como la 5251 pueden volverse susceptibles a problemas de agrietamiento en caliente durante la soldadura cuando se utilizan metales de aportación con una composición química coincidente, por lo que se recomienda utilizar el tipo Al-Mg5 en su lugar.
- Se recomienda utilizar alambre de relleno 5039 al soldar aleaciones 7XXX para obtener buenos resultados en aplicaciones de baja dilución.
- Tenga cuidado al soldar aleaciones 6XXX, ya que presentan grietas por solidificación si se sueldan de forma autógena.
- Elementos de aleación A veces se añaden titanio y circonio a los metales de aportación para reducir el riesgo de agrietamiento en caliente del metal de soldadura mediante el refinamiento del grano.
Preparación para soldar
La preparación de la soldadura incluye procesos de corte, biselado y ajuste fino que comúnmente utilizan herramientas mecánicas como las tradicionales que se utilizan en todos los talleres tradicionales, como herramientas ligeras de corte y rectificado, o la preparación se puede realizar mediante una herramienta de corte por arco de plasma.
Las herramientas de corte mecánico son los métodos más rentables que se utilizan comúnmente en los talleres debido a su menor capital en comparación con los sistemas de corte por láser y plasma.
La preparación de los bordes para la soldadura se puede realizar mediante métodos mecánicos utilizando muchas herramientas, incluidas fresadoras de alta velocidad, cepilladoras de bordes, fresadoras y varios tipos de sierras, además de equipos neumáticos en los que hay que tener cuidado de que el aire suministrado esté seco y Limpiar y no provocar porosidades durante la soldadura.
El arco de plasma se puede utilizar para soldar o cortar y se considera el proceso térmico más común para cortar aleaciones de aluminio que puede operarse en modo manual, mecanizado o totalmente automatizado.

Fig. 12 Esquema que ilustra los principios del corte por chorro de plasma. Cortesía de TWI Ltd.
Como se muestra en la Fig. 12, el soplete de corte por plasma utiliza un electrodo de tungsteno que está rodeado por un flujo de gas de plasma que puede ser aire, argón, argón-hidrógeno, nitrógeno y dióxido de carbono.
Hay dos tipos de arco de plasma, incluido el arco transferido y el arco no transferido. En el arco transferido, el arco se genera entre el electrodo de tungsteno y la pieza de trabajo, pero en el caso del arco no transferido, el arco se genera dentro del soplete de plasma entre el electrodo de tungsteno y el anillo. En el corte se suele utilizar arco transferido.
La composición del gas para corte por plasma depende de la calidad requerida del corte, el espesor del metal a cortar y el costo del gas (Tabla 3). El aire es la opción más barata y se han desarrollado sistemas de un solo gas que utilizan aire y un electrodo de hafnio para cortar materiales de hasta aproximadamente 6 mm de espesor (Fig. 13).

Fig. 13 Corte por plasma de aire. Cortesía de TWI Ltd.

Espesor del metal (mm) |
gas plasmático |
Flujo de gas (L/min) |
Gas protector |
Flujo de gas (L/min) |
Corriente (Amperios) |
Voltaje (voltios) |
Velocidad de corte (mm/min) |
Tipo de método |
1 |
Aire |
98 |
4800 |
Manual |
||||
1.5 |
Aire |
98 |
6300 |
Manual |
||||
3 |
Aire |
98 |
3000 |
Manual |
||||
6.5 |
Aire |
98 |
1000 |
Manual |
||||
6.5 |
N2 |
34 |
CO2 |
100 |
1800 |
Manual |
||
6.5 |
Ar+H2 |
25 |
200 |
50 |
1500 |
Manual |
||
10 |
N2 |
35 |
CO2 |
100 |
200 |
1250 |
Manual |
|
12.5 |
Ar+H2 |
28 |
280 |
55 |
1000 |
Manual |
||
25 |
Ar+H2 |
33 |
330 |
70 |
500 |
Manual |
||
50 |
Ar+H2 |
45 |
400 |
85 |
500 |
Manual |
||
6 |
Ar+H2 |
55 |
300 |
140 |
7500 |
Motorizado |
||
6 |
N2 |
32 |
CO2 |
100 |
115 |
1800 |
Motorizado |
|
10 |
N2 |
32 |
CO2 |
100 |
120 |
900 |
Motorizado |
|
12.5 |
N2 |
32 |
CO2 |
100 |
120 |
480 |
Motorizado |
|
12.5 |
N2 |
32 |
CO2 |
100 |
300 |
3200 |
Motorizado |
|
12.5 |
Ar+H2 |
60 |
300 |
140 |
5000 |
Motorizado |
||
25 |
N2 |
70 |
CO2 |
100 |
400 |
1800 |
Motorizado |
|
25 |
Ar+H2 |
60 |
375 |
160 |
2300 |
Motorizado |
||
50 |
N2 |
32 |
CO2 |
100 |
400 |
800 |
Motorizado |
|
50 |
Ar+H2 |
60 |
375 |
165 |
500 |
Motorizado |
||
75 |
Ar+H2 |
95 |
420 |
170 |
380 |
Motorizado |
||
75 |
Ar+H2 |
45 |
N2 |
100 |
400 |
500 |
Motorizado |
|
75 |
Ar+H2 |
45 |
N2 |
100 |
700 |
650 |
Motorizado |
|
100 |
Ar+H2 |
95 |
450 |
180 |
750 |
Motorizado |
||
125 |
Ar+H2 |
95 |
475 |
200 |
250 |
Motorizado |
Tabla 3 Parámetros sugeridos para el corte por chorro de plasma
Para la soldadura TIG de aluminio, se sugieren preparaciones de soldadura según BS 3019, como se muestra en la siguiente Tabla 4:
Espesor (mm) |
Preparación de bordes |
Observaciones |
20swg = El reborde debe 0,9 mm y utilizarse únicamente 16swg = donde cuadrado 1,6 mm |
![]() |
Se recomiendan preparaciones de bordes rebordeados cuando las preparaciones de bordes cuadrados no son prácticas. |
3,8 milímetros |
![]() |
Cuando no se puede utilizar la barra de respaldo, se recomienda soldar desde ambos lados. |
4,8 mm |
|
|
6,4 mm |
![]() |
Si no se utiliza una barra de respaldo, se realiza el desconchado hasta obtener el metal de soldadura sano y se agrega una carrera de sellado. |
9,5 mm |
![]() ![]() |
|
12,7 mm |
|
Puede ser necesario precalentar |
|
![]() |
La Tabla 4 sugiere la preparación de bordes para soldadura TIG según BS 3019.
Para la soldadura MIG, se sugieren preparaciones de bordes según BS 3019 según la siguiente tabla 5:
Espesor del material (mm) |
Preparación de bordes |
Observaciones |
1,6-4,8 mm |
![]() |
La barra de respaldo proporciona un mayor control de la penetración. |
6,4-9,5 mm |
![]() |
Soldar por ambos lados |
4,8-12,7 mm |
![]() |
Adecuado para soldar por ambos lados |
6,4-12,7 mm |
![]() |
El astillado posterior es imprescindible antes de soldar desde el otro lado. |
6,4-19,1 mm |
![]() |
Adecuado para soldar por ambos lados, pero es imprescindible realizar un desconchado posterior además del precalentamiento. |
12,7-25,4 mm |
|
El astillado posterior es imprescindible antes de soldar desde el otro lado. |
La Tabla 5 sugiere preparaciones de bordes para soldadura MIG.
La cortadora de plasma ARCCAPTAIN 50A ofrece un rendimiento excelente al cortar acero aleado, acero inoxidable, acero dulce, cobre, aluminio, etc. Equipado con una gran pantalla LED, puede leer todos los datos y funciones de forma clara y sencilla sin quitarse el casco.
Fuente: Arccaptain , Arccaptain CUT50| Cortadora de plasma portátil de 50 amperios CUT 50|Fácil de usar para principiantes
Procesos de soldadura utilizados en la soldadura de aluminio.
Soldadura TIG
TIG significa soldadura con gas inerte de tungsteno y también se llama GTAW, que significa soldadura por arco de tungsteno con gas según el estándar de EE. UU., pero según el estándar europeo, el proceso toma una abreviatura numérica que es 144 para soldadura TIG.
Como se muestra en la Fig. 14, se utiliza un electrodo de tungsteno no consumible para crear el arco de soldadura que representa la fuente de calor de soldadura y este arco está protegido por un gas inerte que comúnmente es argón para proteger el electrodo, la columna del arco y el baño de soldadura.

Fig. 14 Esquema del proceso de soldadura TIG.
La soldadura TIG de aluminio generalmente se realiza mediante el uso de corriente alterna para lograr el efecto de limpieza mediante la eliminación de la capa de óxido y esto tiene lugar en el semiciclo positivo del electrodo en el que los electrones fluyen desde la pieza de trabajo al electrodo no consumible y los iones fluyen en sentido contrario. dirección pero en la otra mitad del ciclo de CA en la que el electrodo es negativo, el electrodo se enfría y se logra una penetración profunda.
En la soldadura de CA, el arco se extingue y se vuelve a encender cada medio ciclo a medida que la corriente del arco pasa por cero, es por eso que generalmente se usa una fuente de energía de alta frecuencia para lograr el reencendido instantáneo del arco a alta frecuencia (HF), lo que permite la soldadura. que el arco se vuelva a encender con un retraso mínimo.
Como se muestra en la Fig. 15, el equipo moderno utiliza un circuito de estado sólido que cambia la corriente CA de la forma de onda sinusoidal normal a la forma de onda CA cuadrada. Estas fuentes de energía se pueden ajustar según sea necesario, ya sea cambiando la frecuencia o cambiando el tiempo de las mitades positiva o negativa del ciclo.
Las últimas unidades basadas en inversores proporcionan un alto grado de control y el tiempo de duración negativa del electrodo se puede ajustar del 50 % al 90 % del ciclo, lo que da como resultado una mayor penetración. El aumento de la frecuencia da como resultado un arco más enfocado, lo que aumenta la penetración, permite utilizar velocidades de desplazamiento más rápidas y reduce la distorsión.

Fig.15 Ondas cuadradas AC.
Existen parámetros de soldadura recomendados para soldadura de aluminio como se muestra en la Tabla 6:
La Tabla 6 sugiere parámetros de soldadura: protección con gas argón en posición plana .
Espesor (mm) |
Tipo de articulación |
Espacio de raíz (mm) |
Corriente (A) |
nº de pases |
Diámetro de relleno. (mm) |
Velocidad de viaje (mm/min) |
Diámetro de la boquilla. (mm) |
0,8 |
trasero cuadrado |
nulo |
55 |
1 |
1.6 |
300 |
9.5 |
1.2 |
trasero cuadrado |
nulo |
100 |
1 |
2.4 |
400 |
9.5 |
1.5 |
trasero cuadrado |
0,8 |
130 |
1 |
2.4 |
470 |
9.5 |
1.5 |
Filete |
100 |
1 |
2.4 |
250 |
9.5 |
|
2 |
trasero cuadrado |
0,8 |
160 |
1 |
3.2 |
380 |
9.5 |
2.5 |
trasero cuadrado |
0,8 |
170 |
1 |
3.2 |
300 |
9.5 |
2.5 |
Filete |
140 |
1 |
3.2 |
250 |
9.5 |
|
3.2 |
trasero cuadrado |
0,8 |
180 |
1 |
3.2 |
300 |
12.7 |
3.2 |
Filete |
175 |
1 |
3.2 |
300 |
12.7 |
|
5 |
trasero cuadrado |
1.6 |
250 |
1 |
4.8 |
200 |
12.7 |
5 |
Filete |
240 |
1 |
4.8 |
250 |
12.7 |
|
6.5 |
Culata de 70 V |
nulo |
320 |
1 |
4.8 |
150 |
12.7 |
6.5 |
Filete |
290 |
1 |
4.8 |
250 |
12.7 |
|
8 |
Culata de 70 V |
nulo |
340 |
2 |
4.8 |
165 |
12.7 |
10 |
Culata de 70 V |
nulo |
350 |
2 |
6.4 |
180 |
12.7 |
10 |
Filete |
370 |
2 |
6.4 |
250 |
dieciséis |
Notará que no hay recomendaciones para los parámetros de soldadura TIG para soldar aluminio con un espesor superior a 10 mm debido a consideraciones económicas donde la soldadura TIG rara vez se utiliza.
La soldadora AC/DC TIG 200P es una potente máquina de soldadura TIG de aluminio que ofrece soldadura con métodos TIG AC Cuadrado/Triangular/Pulso Cuadrado/Pulso Triangular/DC Pulso/DC/STICK. Se puede utilizar para soldar varios metales, incluidos aluminio, acero, acero inoxidable, acero al carbono y cobre. La tecnología patentada DASH-ARC mejora la velocidad de encendido del arco, la eficiencia de la soldadura y los resultados, mientras que las funciones de forma de onda de pulso, cuadrada y triangular previenen la quema del material, minimizan la distorsión y mejoran la apariencia del cordón. El sistema de control digital hace que la máquina sea confiable y estable, y la gran pantalla LED permite un fácil ajuste de parámetros.
Fig. 16 Soldadora multiproceso AC/ DC TIG 200P
soldadura MIG
MIG significa soldadura de metal con gas inerte en la que los consumibles de soldadura tienen forma de carretes, no de electrodos como en SMAW o TIG, y el alambre se alimenta al soplete a través de la unidad de alimentación de alambre y el blindaje del alambre fundido se realiza mediante el uso de gas inerte que es generalmente argón o una mezcla de argón y helio o helio.
El arco MIG requiere de una fuente de energía que proporcione corriente continua y con una adecuada relación establecida entre corriente y voltaje de soldadura, relación que se conoce como característica dinámica de la fuente de energía. Como se mencionó anteriormente, el proceso MIG utiliza una alimentación de alambre continua y para la mayoría de las operaciones de soldadura es importante que la velocidad a la que el alambre se quema en el arco coincida con la velocidad de alimentación del alambre. De lo contrario, se puede producir un arco inestable y una calidad de soldadura variable.
Los desarrollos recientes en fuentes de energía han logrado permitir que el proceso MIG también se utilice con CA. La mayor parte del calor desarrollado en el arco se genera en el polo positivo, en el caso de la soldadura MIG del electrodo, lo que da como resultado altas tasas de quemado del alambre y una transferencia eficiente de este calor al baño de soldadura por medio del alambre de relleno.
En soldadura MIG. El alambre de relleno fundido se transfiere a la unión a través de diferentes tipos de modos de transferencia que dependen principalmente de la corriente y el gas de protección utilizados y pueden estar relacionados con el diámetro del alambre en el caso de soldadura de aluminio como en la Tabla 7.
Modo de transferencia de metal |
Diámetro del cable |
Aderezo |
0,8 milímetros |
Pulsado |
1,2 a 1,6 mm |
Pulverización convencional |
1,2 a 1,6 mm |
Pulverización de alta corriente |
1,6 milímetros |
Mixto de alta corriente |
2,4 milímetros |
Tabla 7 Modo de transferencia de metal y diámetro del alambre.
Cuando se suelda aluminio con MIG, el bajo punto de fusión del aluminio da como resultado una transferencia por pulverización hasta corrientes de soldadura relativamente bajas, lo que proporciona una unión sin salpicaduras.
En la siguiente Tabla 8, los parámetros de soldadura recomendados para soldadura de aluminio mediante soldadura MIG:
Espesor (mm) |
Espacio de raíz/cara (mm) |
Ángulo incluido (grados) |
Apoyo |
Corriente (A) |
Voltaje (V) |
No. de pases |
Diámetro de relleno. (mm) |
Velocidad de desplazamiento (mm/min) |
1.6 |
nulo |
Cuadrado |
Temporario |
100 |
19 |
1 |
0,6 |
1000 |
1.6 |
2.5 |
Cuadrado |
Permanente |
100 |
19 |
1 |
0,6 |
1000 |
2.4 |
nulo |
Cuadrado |
Temporario |
140 |
21 |
1 |
0,6 |
1000 |
2.4 |
3.2 |
Cuadrado |
Permanente |
130 |
23 |
1 |
0,6 |
780 |
3.2 |
2.5 |
Cuadrado |
Temporario |
160 |
24 |
1 |
1.2 |
780 |
3.2 |
5 |
Cuadrado |
Permanente |
135 |
23 |
1 |
1.2 |
720 |
4 |
1.5 |
Cuadrado |
Ninguno |
170 |
26 |
2 |
1.2 |
750 |
4 |
1,5/2,5 |
60 simple-V |
Temporario |
160 |
27 |
1 |
1.2 |
750 |
4 |
4,5/2,5 |
60 simple-V |
Permanente |
185 |
27 |
2 |
1.6 |
750 |
6.3 |
2.5 |
60 simple-V |
Ninguno |
200 |
28 |
3 |
1.6 |
750 |
6.3 |
2,5/2,5 |
60 simple-V |
Temporario |
185 |
27 |
2 |
1.6 |
750 |
6.3 |
6/1.5 |
60 simple-V |
Permanente |
225 |
29 |
3 |
1.6 |
750 |
8 |
2,5/1,5 |
60 simple-V |
Temporario |
245 |
29 |
2 |
1.6 |
750 |
8 |
4,5/cero |
60 simple-V |
Permanente |
255 |
29 |
3 |
1.6 |
750 |
10 |
2,5/4,5 |
60 simple-V |
Ninguno |
290 |
29 |
1 |
1.6 |
750 |
10 |
2,5/2,5 |
60 simple-V |
Temporario |
275 |
29 |
2 |
1.6 |
900 |
10 |
4,5/cero |
60 simple-V |
Permanente |
275 |
26 |
1 |
1.6 |
800/850 |
12.5 |
0,8/1,5 |
60 simple-V |
Ninguno |
260/225 |
24/26 |
3 caras/3 reversas |
1.6 |
1050 raíz/800 |
12.5 |
2,5/1,5 |
60 simple-V |
Permanente |
260 |
24 |
3 caras/1 reversa |
1.6 |
850 raíz/550 |
12.5 |
4,5/cero |
60 simple-V |
Ninguno |
270 |
24 |
3 |
1.6 |
550 raíz/500 |
dieciséis |
1,5/1,5 |
60 simple-V |
Permanente |
275 |
23/26 |
4 caras/4 reversas |
1.6 |
850 raíz/650 |
dieciséis |
4,5/cero |
60 simple-V |
Temporario |
280 |
26 |
4 |
1.6 |
550 raíz/450 |
20 |
1,5/1,5 |
60 simple-V |
Ninguno |
255 raíz/230 |
22/26 |
4 caras/4 reversas |
1.6 |
900 raíz/550 |
20 |
3/2.5 |
60 simple-V |
Permanente |
350 |
29 |
4 caras/1 reversa |
2.4 |
1000 |
20 |
6/cero |
60 simple-V |
Temporario |
380 |
30 |
5 |
2.4 |
1000 |
25 |
1,5/1,5 |
60 simple-V |
Ninguno |
255 raíz/230 |
22/26 |
6 cara/6 reversa |
1.6 |
600 |
25 |
4/2.5 |
60 simple-V |
Permanente |
350 |
29 |
2.4 |
1000 |
|
25 |
6/cero |
60 simple-V |
Temporario |
350 |
29 |
2.4 |
1000 |
Tabla 8 Parámetros de soldadura sugeridos para aluminio mediante soldadura MIG.
Fig. 16 ARCCAPTAIN MIG200 Soldadora MIG Multiproceso 200 Amperios, Máquina Multisoldadora 6 en 1 (MIG, Spot, TIG, MMA...) - ARCCAPTAIN MIG200 | Unboxing y prueba
Uno de los buenos soldadores que se utiliza en la soldadura de aluminio es ARCCAPTAIN MIG200, que utiliza un soldador mig 6 en 1 multiproceso de doble voltaje, que es muy adecuado para proyectos de bricolaje, fabricación, reparación, etc., ya sea principiante o profesional. Soldador, puedes usarlo fácilmente. El diseño multiusos del MIG200 lo convierte en una excelente inversión para cualquiera que busque un soldador MIG confiable y eficiente.
El MIG 200 integra las funciones de soldador de electrodo , soldador mig, soldador de aluminio y soldador lift tig, que en realidad es un soldador para todo uso. Dado su rendimiento y precio asequible, esta soldadora es una soldadora mig realmente excepcional para soldadores principiantes y profesionales. Es ideal para el típico proyecto de bricolaje porque puede soldar prácticamente cualquier cosa que un propietario pueda necesitar. Puede ajustar la corriente fácilmente mediante la gran pantalla LED. Su tamaño compacto lo hace liviano y ultraportátil. Esta máquina pesa sólo 28,2 libras, puede llevarla fácilmente a cualquier lugar donde necesite soldar.
MIG pulsado
El proceso MIG pulsado utiliza una corriente de "fondo" baja, suficiente para mantener el arco pero no lo suficientemente alta como para provocar que el cable se derrita. A esta corriente de fondo se superpone un pulso de "pico" de alta corriente. En condiciones óptimas, esto provoca que una sola gota de alambre de relleno fundido se proyecte a través del arco hacia el baño de soldadura mediante transferencia por pulverización. De este modo es posible conseguir una transferencia por pulverización y un arco estable con corrientes de soldadura medias bajas. Esto permite soldar metales muy finos con alambres de gran diámetro donde antes era necesario utilizar alambres muy delgados, difíciles de alimentar en aluminio blando. Las corrientes más bajas también reducen la penetración, lo que resulta útil al soldar.
materiales finos y también permiten utilizar velocidades de soldadura más lentas, facilitando al soldador la manipulación del soplete en condiciones de difícil acceso o cuando suelda posicionalmente.

Fig. 17 Corriente pulsada CC, soldadura Miller
Como se muestra en la Fig. 17, el cambio en la frecuencia conduce a un cambio en el número de pulsos durante la misma porción de tiempo y también se puede controlar el período de tiempo en la corriente de pulso y la corriente de fondo.
Resumen:
El artículo proporciona una descripción general de la soldadura de aluminio, incluidas las características del aluminio, la designación de la aleación de aluminio, los problemas de soldabilidad del aluminio, la selección de materiales de relleno para soldadura, la preparación para la soldadura y los procesos de soldadura utilizados en la soldadura de aluminio. Destaca la importancia de comprender las diferentes aleaciones de aluminio y los procedimientos de soldadura adecuados para mantener la integridad de las uniones soldadas.
El aluminio se utiliza ampliamente en diversas aplicaciones debido a su peso ligero y alta resistencia a la corrosión. Se utiliza en aviones, barcos, material rodante ferroviario, puentes y vehículos militares. Sin embargo, soldar aluminio presenta desafíos como la formación de una película de óxido, porosidad, agrietamiento en caliente y distorsión.
Para superar estos desafíos, se utilizan varios procesos de soldadura, incluida la soldadura TIG (gas inerte de tungsteno) y la soldadura MIG (gas inerte de metal). La soldadura TIG utiliza un electrodo de tungsteno no consumible y corriente alterna para romper la capa de óxido y lograr una penetración profunda. La soldadura MIG utiliza una alimentación continua de alambre y un gas protector para proteger el baño de soldadura.
El artículo también proporciona parámetros de soldadura recomendados para soldadura TIG y MIG de aluminio según el espesor, tipo de junta, corriente, voltaje, diámetro del relleno y velocidad de desplazamiento. Enfatiza la importancia de una preparación adecuada de los bordes y la selección de materiales de relleno en función de las propiedades deseadas de la junta soldada.
El artículo es una buena guía para ingenieros, supervisores y soldadores de soldadura para comprender los fundamentos de la soldadura de aluminio e implementar procedimientos de soldadura efectivos para aleaciones de aluminio.