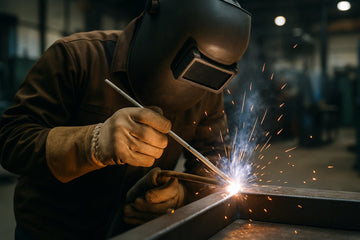
If you’re working on welding projects, understanding 7018 welding rod uses is key for making strong, professional welds. 7018 welding rods are multipurpose electrodes used mainly for welding carbon steel in structural work. They offer high strength and flexibility, creating solid welds with low risk of hydrogen cracks—ideal for critical builds like bridges, pipelines, and pressure tanks.
You’ll see 7018 rods everywhere in structural work—bridges, boilers, you name it. They make clean welds that pass codes and inspections. Their low hydrogen content helps stop weld defects, which is why folks trust them for demanding jobs.
If you want your project to meet welding standards and last, picking a rod like the 7018 just makes sense. Why risk it with anything less?
What Is 7018 Welding Rod And Why It Matters
Arccaptain 7018 Welding Rod 5LB Low Hydrogen Carbon Steel Stick Welding Electrodes
The 7018 welding rod is famous for strong, clean welds and reliable performance. It stands out for its special makeup, high strength, and the fact that you can use it in lots of positions.
Understanding its features helps you pick the right rod for your work. It’s not just about melting metal together—sometimes, you need the right tool for the job.
AWS E7018 Basics: Low‑Hydrogen, 70 Ksi Strength, All-Position Use
The 7018 rod is a low-hydrogen stick electrode. It releases less hydrogen while welding, which lowers the risk of cracks in your welds.
It has a tensile strength of about 70 Ksi (70,000 psi), so it’s built for heavy-duty jobs. That strength means your welds won’t snap under pressure, which is definitely what you want.
You can weld in any position—flat, horizontal, vertical, or overhead. That kind of flexibility is a big deal for a lot of projects.
The rod’s flux has potassium for low hydrogen and iron powder to boost how fast you can weld. So, you get things done quickly and still keep the weld quality up.
This rod works great in shielded metal arc welding (SMAW). That’s the bread and butter of structural and industrial welding.
If you need toughness, good stretch, and corrosion resistance, the 7018 delivers. People often pick it for welding mild steel and sometimes even stainless, especially when they can’t afford to mess around with reliability.
Explore our welding electrodes collection to discover top stick rods and their best applications.
Top Uses Of 7018 Welding Rod

The 7018 rod is known for strong, low-hydrogen welds and versatility. It works on different types of steel and fits right into all kinds of structural and industrial jobs that need clean, solid welds.
Structural Steel & Construction (Bridges, Buildings)
When you’re working with structural steel—bridges, buildings, all that—7018 rods give you tough, durable welds. They’re great for joining carbon steel and low alloy steel in construction.
The low hydrogen coating helps prevent cracking, which is huge for heavy-load jobs like bridges. You can use these rods in vertical, overhead, or any position you need, so they’re super flexible for fieldwork.
Architects and engineers often reach for 7018 when they want welds that can take stress and weather. It’s a go-to for a reason.
Pipe, Pipeline & Pressure Vessel Fabrication Or Repair
If you're welding pipes, pipelines, or pressure vessels, 7018 rods are a solid choice. They make smooth, crack-resistant welds, which you really need in high-pressure situations.
These rods work well on mild steel, low alloy steel, and even cast steel. That covers most pipeline and vessel materials. Using 7018 rods cuts down on defects, so your welds meet the tough standards the industry demands.
Also read our guide: Different Types of Metal Used in Welding
Heavy Equipment, Tank, Rail‑Car, Shipbuilding, Power Plants
For heavy equipment repair, tanks, rail-cars, or shipbuilding, you need welds that can handle stress. The 7018 rod delivers on that front.
In power plants or shipbuilding, where metals take a beating from force and heat, 7018 rods give welds with solid tensile strength and crack resistance. They work well for structural applications on both mild steel and trickier alloys.
That’s why folks use them for long-lasting repairs or new builds. If you’re working on something that can’t fail, 7018 is a smart bet.
Also read our article, Comparing Stick Welding Electrodes for Your Project to see how different rods perform in real jobs.
Why Pros Choose 7018 – Key Advantages
With the 7018 welding rod, you get strong, clean welds and less risk of cracks. Its special coating and easy control let you work in all sorts of positions and on different metals, and you still get good results.
Crack-Resistant Low‑Hydrogen Coating & High Ductility
The 7018 rod uses a low-hydrogen coating to help stop cracks from forming. Hydrogen can make welds brittle, so keeping it low is pretty important, especially on thick or critical stuff.
Its high ductility means your welds won’t snap if they’re bent or stressed. That matters when the metal might move or carry weight. The rod also gives medium penetration, so you get a deep, secure weld without burning up the base metal.
The flux coating shields the molten metal from air, keeping it clean and free of junk you don’t want in your weld.
Smooth Arc, Minimal Spatter, All‑Position Versatility
The 7018 rod gives you a stable and smooth arc, so there’s less spatter and less cleanup. That smooth arc also makes it easier to lay down neat weld beads that look sharp and hold up.
You can weld in any position—flat, vertical, overhead, or horizontal—with 7018 rods. That flexibility is a big plus. Its high deposition rate means you can weld faster and still get solid joints.
The rod’s flux coating helps form a clean weld by creating a protective slag that’s easy to chip off. That keeps things tidy and reduces the odds of defects from dirt or air.
All these advantages make 7018 a top pick for welders who want results they can trust, without a bunch of extra hassle.
Also read our article, What Welding Rod to Use: A Beginner's Guide, which is ideal for new stick welders.
Best Practices When Using 7018 Welding Rod

If you use the 7018 welding rod the right way, you can boost the quality and strength of your welds. You’ll need to get your amperage right, store the rods dry, and use good technique—stuff like pre-heating and keeping a steady arc.
These steps help you avoid flaws and keep your welds consistent. It’s not rocket science, but there’s a bit of an art to it.
Amperage Guide By Diameter (E.G. 1/8″ ≈ 90–150 A)
Your amperage depends on the electrode diameter and the thickness of what you’re welding. For example, a 1/8-inch (3.2 mm) 7018 rod runs best at 90 to 150 amps.
If you go too low, you won’t get good penetration or fusion. Too high, and you’ll burn the coating or get too much spatter.
Here’s a quick guide for common sizes:
Electrode Diameter |
Amperage Range (A) |
1/16 inch (1.6 mm) |
55 - 90 |
3/32 inch (2.4 mm) |
90 - 130 |
1/8 inch (3.2 mm) |
90 - 150 |
5/32 inch (4.0 mm) |
140 - 180 |
Stay within these ranges to control bead width and penetration, depending on your joint and material. Make sure your power source is set for the right polarity—7018 rods usually want DC electrode positive (DCEP).
Storage & Baking Rules To Avoid Moisture
7018 rods need to stay dry, or you risk hydrogen cracks. Store them in a sealed container or rod oven at 250°F to 300°F (120-150°C).
If they get damp, bake them before use—shoot for about 600°F (315°C) for an hour. That dries them out and brings back their low hydrogen properties.
Don’t leave rods in cool, damp spots. Moisture can mess up your welds later. On big jobs, keep drying logs to track rod condition and baking cycles. It’s not glamorous, but it saves headaches.
Pre‑Heating, Technique Tips, Arc Control Essentials
Pre-heating thick or cold metal helps reduce shock and crack risk. For steel over 1/2 inch thick, aim for 200°F to 300°F (93-149°C).
Drag the rod steadily along the joint, keeping the arc length around 1/8 inch. For vertical up welds, hold the electrode at a slight angle—about 10 degrees from vertical.
Use a minor weaving technique on wide joints to fill the groove. Keep your arc short for better control and penetration.
Good arc control also means less spatter and slag. Don’t forget your safety gear—some techniques can throw sparks or UV light. These tips help your welds stay strong and clean, which is what you want at the end of the day.
When Not To Use 7018 Rod
The 7018 rod is reliable, but it doesn’t fit every job. Some materials and situations can lead to cracking or bad welds if you use 7018.
Knowing when to skip it helps you get better results and avoid trouble. Sometimes, it’s just smarter to reach for something else.
Thin Sheet Metal Or Dirty/Rusty Surfaces – Use Other Rods
If you’re welding thin sheet metal, 7018 isn’t the best choice. This rod produces a heavier, slower weld, which can burn through thin metal.
Instead, rods like E6013 or E6011 work better here. They create a softer arc and less heat, so you’re less likely to punch holes through your work.
Also, skip 7018 if your metal’s dirty, rusty, or has oil on it. The low hydrogen coating on 7018 needs a clean surface to prevent porosity and slag inclusions.
Dirt and rust trap gases that make the weld weak or full of holes. For these kinds of surfaces, rods like E6010 or E6011 handle contamination way better because their slag freezes fast and they dig in deeper.
Learn more about these by reading our article: What Is Porosity in Welding?
Lack Of Rod Oven Or Re‑Baking → Risk Of Moisture Cracking
7018 rods have a low-hydrogen coating that helps prevent hydrogen cracking. But honestly, this only works if the rods stay dry.
If your rods soak up moisture, they’ll release extra diffusible hydrogen into the weld. That can cause cracks as the weld cools down.
You’ve got to store 7018 rods in a rod oven at about 250°F (120°C). If the rods get wet or lose their heat, you need to re-bake them before you start welding.
If you can’t keep rods dry or don’t have a rod oven, just use something less fussy—like E6011. Those rods burn off moisture easier and don’t mind a bit of humidity.
Check out our guide on 6013 vs. 7018: How To Decide for Your Next Weld to find out which rod fits your next project.
Final Thoughts
The 7018 welding rod is a go-to for structural steel, pipelines, and heavy equipment thanks to its low-hydrogen coating and stable, quiet arc.
It delivers strong, crack-resistant welds with minimal spatter and works in all positions. With proper amperage and storage in a rod oven, it consistently makes clean, durable joints.
That said, it’s not meant for thin sheet metal or rusty, unprepared surfaces. Use it right—for tough, critical builds—and you’ll get quality weld after weld. And for welding essentials including machines, helmets, and gloves, visit ArcCaptain.
Frequently Asked Questions
Is 7018 good for cold environments?
Yeah, 7018 rods actually do pretty well in the cold thanks to their low hydrogen coating. That coating helps stop cracking, which is a pain when you’re welding in low temps.
Still, you’ll want to preheat your metal if it’s really cold—say, below 50°F (10°C). Preheating slows down cooling and eases stress on the weld.
After that, keep the rod dry so you don’t lose that low hydrogen benefit. That’s how you keep your welds tough, even in chilly weather.
Can I skip baking?
Honestly, you shouldn’t skip baking 7018 rods if they’ve been exposed to moisture. These rods are like sponges—they’ll suck up water from the air, and that can lead to cracks or weak welds.
Baking means heating them up, usually at 250–300°F (120–150°C) for about an hour. If your rods are fresh and stored right in a sealed container or rod oven, you might get away without baking. But if you’re not sure, it’s safer just to bake them.
Which is better, 6011 or 7018?
Honestly, it depends on what you’re doing. 6011 is a fast-freeze rod that’s great for welding dirty, rusty, or painted metal. It digs in deep and works in any position, but the weld isn’t as smooth or strong as 7018.
7018 gives you a stronger, cleaner weld with low hydrogen—perfect for structural steel, bridges, or pipes. If you care about strength and looks, go with 7018. If you’re just patching something up or working on junk metal, 6011 is your friend.
Does 7018 welding rod need to be heated?
Yeah, you usually need to heat 7018 rods before you use them. The coating grabs moisture fast, and that can mess up your weld with cracks or porosity.
Most folks bake rods at 250–300°F (120–150°C) for about an hour. Some welders keep a rod oven running while they work, just to keep things dry. If your rods get wet, you’ll need to bake them again before you weld.
Do you push or pull 7018?
With a 7018 rod, you usually pull (drag) the electrode when you weld. Pulling gives you more control over the weld puddle.
You'll also get deeper penetration this way. It just feels more solid and tends to make a cleaner, stronger weld bead.
If you push instead, you might see poor penetration and a weaker weld. There’s often more spatter, too.
So, if you want the best results with 7018, stick with a steady pulling motion. Keep your arc tight and watch your angle, depending on the position you’re working in.