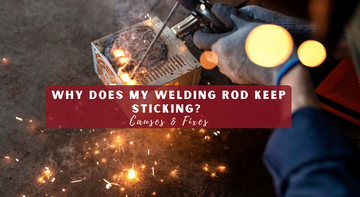
Every welder knows the frustration of a welding rod that just won’t stop sticking to the metal. It interrupts your work, wastes time, and can make welding feel impossible, even if you’ve practiced for hours.
A welding rod usually sticks because the arc heat is too low or the connection between the rod and the holder isn’t strong enough. This problem is common for beginners, but it can still happen to anyone, even if you’ve been welding for years.
In this article, you’ll find out why this problem happens, the most common causes, and how you can stop your electrode from sticking.
Whether you’re just getting started or want to improve your results, you’ll get simple solutions and tips to make your welding smoother and less stressful.
Quick Insights ⚡:
- Sticking rods usually indicate incorrect amperage, poor technique, or contaminated materials.
- Using the correct settings and clean metal can prevent sticking.
- New welders often struggle, but small adjustments can quickly resolve the issue.
- Rod angle, speed, and electrode storage matter too.
- Learn the top causes, solutions, and pro tips below.
💥 Also Read: What Welding Rod to Use: A Beginner’s Guide
Why Does My Welding Rod Keep Sticking? (Top 7 Causes & Fixes)

Welding rods can stick for several reasons, and it is often easy to resolve once the cause is identified. This section breaks down the main problems and provides you with specific steps to address them.
1. Incorrect Amperage Settings
When your amperage is set too low, the arc does not make enough heat. This causes the rod to melt too slowly and adhere to the workpiece. A rod that freezes in place right after you strike an arc is a clear sign the amps are too low.
Each rod size and type needs a certain amperage. For example, a 1/8-inch E7018 rod typically requires between 120 and 130 amps.
If you notice sticking, try raising your amperage in small steps, about 5 to 10 amps at a time.
High amps are better than too low, but be careful not to go too high or you risk burning holes in thin metal. Always check the manufacturer's settings for each electrode.
Tips:
- Check your welder's amp setting.
- Increase amps if the rod keeps sticking.
- Never exceed the recommended range for your rod.
2. Improper Rod Angle
Holding the rod at the wrong angle often causes it to stick. If you push the rod ahead of the puddle, slag can get trapped under the rod, and it will freeze to the base metal.
Dragging (pulling) the rod is the correct method for most electrodes.
Try to keep your electrode at a drag angle of approximately 15 to 20 degrees away from the welding direction. If you go too steep or too flat, you risk sticking or bad welds.
This angle helps keep the arc stable and lets slag move away from the puddle.
Checklist:
- Hold the rod at a 15–20 degree angle from the workpiece.
- Avoid pushing the rod forward.
- Watch the slag and keep it flowing behind the arc.
3. Moisture in Electrodes
Moisture inside welding rods is a common reason for erratic arcs and sticking. This occurs most frequently with rods like E7018, which have a special flux that readily absorbs water from the air. Damp rods will often spark, pop, and stick when you try to weld.
Always store your rods in a sealed container or, if you use low-hydrogen rods, a heated rod oven. Reheated rods work better and last longer.
If a rod feels damp or you hear “sizzling” while welding, stop and check for moisture.
How to keep rods dry:
- Store rods in a moisture-proof container.
- Use a rod oven set at 250–300°F for low-hydrogen rods.
- Never weld with rods left open in a humid shop.
4. Dirty or Rusty Base Metal
Dirt, oil, paint, and rust on your base metal can block a good electrical connection between the rod and the metal. With a poor connection, the arc will be weak, and rods tend to stick right after striking.
Always clean your metal before welding. Use a wire brush, grinder, or sandpaper to take off all contaminants and rust. The cleaner the surface, the easier it is for the arc to start and keep going.
Cleaning steps:
- Remove paint, oil, and rust from the weld area.
- Polish until shiny and smooth if possible.
- Use a grinder for heavy rust and a brush for surface dirt.
5. Old or Damaged Rods
Welding rods lose their quality if they are too old or have been stored improperly. The protective flux can crack, fall off, or lose its power. Bad rods are harder to strike and often stick at the start.
Check your rods before use. If the flux is chipped, cracked, or missing, throw that rod away. Use rods before their expiration date and follow the storage instructions provided in the box.
Checklist for good rods:
- Use rods with smooth, undamaged flux.
- Avoid using rods that are more than a year old if they have been stored in poor conditions.
- Store new rods in a dry, sealed container.
6. Incorrect Arc Length
The correct arc length refers to the distance between the tip of your rod and the metal you are welding.
A gap that is too small (allowing the rod to sit on the work) can cause it to freeze and stick. Too wide a gap makes the arc weak and hard to control.
A good rule is to keep the arc length equal to the diameter of the electrode. For a 1/8 inch rod, keep the arc about 1/8 inch from the metal. Practicing your hand control helps keep the arc steady.
Tips for arc length:
- Keep a tight but not touching gap.
- Adjust your hand, not just your eyes, to maintain the gap.
- Practice makes perfect for steady movement.
7. Wrong Polarity Settings
Welding machines give you a choice between reverse polarity (DCEP) and straight polarity (DCEN). Most rods require you to use reverse polarity to function correctly.
If you have straight polarity selected, the arc may be weak, and the rods will stick.
Check your welder’s settings before you start. For most jobs with E6010, E7018, and similar rods, use DCEP (electrode positive).
Always read the label on your rod to ensure the correct polarity.
Polarity guide:
Recommended Polarity |
|
E6010 |
DCEP (reverse) or DCEN |
E6011 |
AC or DCEP |
E6013 |
AC, DCEP, or DCEN |
E7018 |
DCEP (reverse polarity) |
If you're unsure, try switching the polarity and see if your rod stops sticking. A correct setting makes striking and holding the arc much easier.
💥 Also Read: What Is Polarity in Welding? A Comprehensive Guide
Pro Tips to Prevent Welding Rod Sticking

Getting your arc started well, matching your settings to the metal, and choosing the right rod make a huge difference when it comes to avoiding sticking.
Even minor adjustments to your technique and equipment can help you weld more smoothly and cleanly.
Scratch-Start vs. Tapping Method
There are two main ways to start an arc: scratch-start and tapping.
- Scratch-start is simple and is often easier for beginners. You strike the tip of the rod against the metal, like lighting a match. This helps heat the rod quickly and keeps it from freezing to the work surface.
- Tapping involves quickly jabbing the electrode onto the metal and lifting it away. This approach can be significantly faster, but it requires more practice to execute effectively. If you are too slow lifting off, the rod almost always sticks.
- Both methods get better with practice. If you find the rod keeps sticking, try slowing down with scratch-start or lifting a bit quicker with tapping.
- Keep the arc short, but don’t touch the rod directly to the metal for too long.
Adjusting for Thin Metal
Thin metals need special attention or rods will stick more.
- Use a lower amperage setting. High amps can burn through thin metal, but too low amps will make the rod stick.
- For thin metal, rods like 3/32 inch work better than larger ones like 1/8 inch. Small rods heat up faster and need less current.
- Hold a steady hand and keep the rod angle shallow—not straight up and down, but slightly tilted.
- Clean the surface well. Dirt and rust exacerbate the issue by blocking the electrical flow.
Choosing the Right Rod
Not all welding rods work the same way. Pick the one that fits your metal and job type.
- 6010 or 6011 rods are suitable for use with dirty or rusty metal. They strike arcs easily and break through old grime, reducing sticking.
- 7018 rods work best on clean, newer metal. These rods need your settings to be just right and the surface dry. They often give a smoother arc and a clean weld, but are more likely to stick if the conditions are not perfect.
- Look for rod sizes and brands that match your welder’s specs. Using a rod that’s too thick or too thin can increase the likelihood of sticking.
- Store rods in a dry place. Moisture can cause sticking and bad welds.
Table: Common Welding Rod Types
Rod Type |
Best For |
Notes |
6010 |
Dirty/Rusty |
Easy arc start, deep penetration |
6011 |
Dirty/Rusty |
Similar to 6010, it works on AC |
7018 |
Clean/New Metal |
Needs dry storage, smooth arc |
💥 Also Read: What Welding Rod Should You Use For Your Project? Factors to Consider
Conclusion
When your welding rod keeps sticking, it usually points to a few main issues. Most often, the cause is related to your machine settings or technique.
Top reasons your rod may stick:
- Low amperage
- Wrong angle
- Damp or old rods
- Dirty work surface
You can use this simple table to double-check the basics:
Problem |
Quick Fix |
Low amperage |
Increase the amps |
Rod angle issue |
Adjust rod angle |
Moisture |
Store rods dry |
Dirty metal |
Clean surface first |
Pay attention to your setup. Adjusting your amps and technique can make a big difference. Keeping your rods dry and your workpiece clean will also help you avoid sticking.
As you keep welding, use these checks to troubleshoot quickly. Small changes often solve the problem, helping you work with less interruption and cleaner results.
You May Also Like 👍
❓Frequently Asked Questions
Welding rod sticking often occurs due to issues with amperage, technique, or the condition of your electrode. Using the correct settings and handling the rods with care can help you avoid most common problems.
How to keep a welding rod from sticking?
Set the welder to the recommended amperage for your rod size and material. Hold the rod at the right angle, usually 10 to 15 degrees from vertical, and keep a steady hand while striking the arc. Ensure the metal surface is clean and free from rust or paint before welding.
How to unstick a welding rod?
If your rod becomes stuck, turn off the welder or break the circuit quickly to prevent damage to the machine or the workpiece. Use a quick twist or tap to loosen the rod from the metal. Try not to force it, as the rod may break.
Why does my welder keep getting stuck?
Your welder may stick if you use low amperage, the wrong rod for the job, or poor welding technique. Dirty or damp rods and a dirty work surface can also cause sticking. Double-check your machine settings and the condition of your rods.
Why is my electrode sticking?
Electrodes stick when the amperage is too low, the arc gap is too small, or if the rod is old or moist. Using the proper technique and keeping your rods dry helps prevent this problem.
Does the welding machine brand or model affect rod sticking?
Most rod sticking problems are caused by user error or rod condition, not the brand or model of the machine. However, some machines are more consistent in delivering stable current, which can help reduce sticking.
Can I use a welding rod that’s been left outside or is rusty?
Welding rods left outside or covered in rust may not work well and can cause sticking. Moisture and rust change how the rod conducts electricity and burns during welding. It's best to use dry, clean rods stored properly for good results.