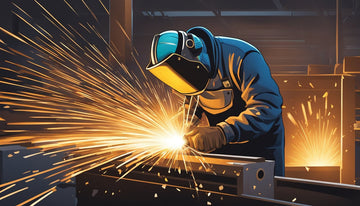
What exactly is an arc welder? It's a device that revolutionizes metal work by using electricity to heat and join metals with precision. Employed across sectors from high-rise construction to intricate car repairs, arc welders come in two forms—those that use up their electrodes and those that don’t, each critical for particular welding jobs.
Want to find the right arc welder for your job or learn about its effects? Read on for key insights into selecting and operating this essential equipment.
What Is Arc Welding?
Arc welding involves a welding process where the intense heat required to melt metal is produced by an electric arc. This process enables different metals to join once they cool and solidify.
An arc welder is a powerful tool to join metals by applying heat generated from an electric arc.
Whether in the open air, underwater, or in space, arc welding is incredibly versatile.
Basic Principles of Arc Welding
At the core of arc welding is the principle of using electricity to generate sufficient heat to melt the workpieces and any filler metal being used.
Once melted, these metals bond as they cool, creating a strong joint.
The welding process involves either a consumable or non-consumable electrode to maintain the electric arc between the electrode and the metal workpieces.
Understanding Electric Arc
The electric arc is a discharge of current between two conductors. In arc welding, this arc is stabilized and controlled to concentrate intense heat on the metal parts to be joined, effectively melting them to create a strong weld upon solidification.
Different Types of Arc Welding
Arc welding encompasses a spectrum of methods tailored for different applications and materials. Each presents unique advantages and uses.
1. Shielded Metal Arc Welding (SMAW)
Also known as stick welding, SMAW is a traditional and widely used technique.
It employs a consumable electrode coated in flux to lay the weld. This method is celebrated for its simplicity and the ability to be used outdoors, as it is less sensitive to wind.
2. Gas Metal Arc Welding (GMAW)
Commonly referred to as MIG (Metal Inert Gas) welding, GMAW utilizes a continuously fed wire electrode and shielding gas.
This type of welding is noted for its high speed and ease of use, making it popular for both industrial and home projects.
3. Flux-Cored Arc Welding (FCAW)
Similar to GMAW, flux-cored welding uses a special tubular wire filled with flux.
The core materials within the wire protect the weld pool, allowing for a higher deposition rate. FCAW is often chosen for its versatility and is particularly effective in construction.
4. Gas Tungsten Arc Welding (GTAW)
Known as TIG (Tungsten Inert Gas) welding, GTAW uses a non-consumable tungsten electrode.
Precise and producing high-purity joints, it's typically used where high-quality welds are imperative, such as in aerospace and piping applications.
5. Submerged Arc Welding (SAW)
In submerged arc welding, the arc operates beneath a covering of granular fusible flux.
This process is known for its deep weld penetration and reduced welding fume and spatter, ideal for large-scale industrial applications.
6. Other Arc Welding Processes
In addition to the main types, specialized techniques such as plasma arc welding offer distinct benefits for cutting and welding thin metals, combining the precision of GTAW with the power of electron beam welding.
Arc Welding Equipment
To engage in arc welding, you require specific equipment that ensures the process is executed effectively and safely. This includes a reliable welding machine, appropriate electrodes, and essential safety gear.
Welding Machines
Arc welding utilizes a welding machine to generate an electric arc that fuses base material and filler metal.
These machines can be either stick welders or portable equipment suitable for various environments.
Factors such as power output, weight, and whether they accommodate alternate consumable electrode methods are to be considered.
Electrodes and Consumables
Choosing the right electrode is crucial, as it conducts the current to form the arc.
Welding rods and welding wire act as consumables; they not only facilitate the arc but also supply additional metal to the weld pool.
The materials used for electrodes and filler metals must be compatible with the metals being welded to ensure a strong bond.
Safety Gear and Accessories
The intense light and heat from the electric arc demand the use of safety gear by welders.
This includes helmets with protective visors, gloves, and aprons made from durable materials to shield against sparks and spatter. But that's not all—protective gear also extends to proper headwear, such as welding caps, which are crucial for shielding the welder's head from heat and debris.
It is also important to have proper ventilation systems. These are essential to dispel harmful fumes and gasses that emanate during the welding process, ensuring a safe breathing environment for the welder.
The Welding Process
The arc welding process is a method of joining metals using intense heat generated by an electric arc. This section will walk you through the steps, from preparation to the actual welding.
1. Preparation and Safety
Before beginning arc welding, select the appropriate electrode and filler material for your metal types. Then, ensure the surfaces are clean to facilitate a strong weld.
For safety, wear protective clothing, a welding cap, a welding helmet with the correct shade number, and gloves.
Set up your work area with proper ventilation to avoid inhaling fumes.
2. Initiating the Arc
Turn on your welding machine and set the correct current (AC or DC) based on your electrode and metal.
To start the arc, strike the electrode like a match against the metal, creating a circuit.
This action generates heat of up to 6500°F, enough to melt the metal at the point of contact.
3. Controlling the Weld Pool
Managing the weld pool, a pool of molten metal, is crucial to a successful weld.
Maintain a consistent temperature and manual metal arc welding technique by moving the electrode at a steady speed and angle, allowing the molten metal to fuse properly.
The filler material is often added to the weld pool to reinforce the joint, ensuring the joining metals are properly bonded as the pool solidifies.
Metals Compatible with Arc Welding
Arc welders work with a range of both ferrous and non-ferrous metals.
Commonly welded metals include steel, stainless steel, aluminum, and copper, with thicknesses varying based on the application.
The base metal is the primary piece to be joined, while the filler metal is often added to the join area to strengthen and complete the weld.
Applications in Various Industries
Arc welding's versatility extends to multiple industries due to its ability to create strong, reliable joints.
From construction—where it's used to erect buildings and bridges—to manufacturing of vehicles and machinery, and even to specialized sectors like aerospace, arc welding has a pivotal role.
In the energy sector, it's essential to create durable connections in pipelines and wind turbines, ensuring safety and efficiency.
Technical Considerations
When using an arc welder, understanding the technical aspects is essential for achieving strong welds and ensuring safety.
Proper management of voltage, electricity, temperature, and heat is key to the strength and quality of the welded joint.
Voltage, Current, and Polarity
The selection of voltage and current affects the heat generated by an arc welder and, consequently, the quality of the weld.
Welders commonly use either direct (DC) or alternating (AC) current, and the choice between them influences the heat of the arc and the ease of starting.
DC current provides a steady arc with easy start-up and is preferred for strong welds and thicker metals; AC current is more suitable for metals like aluminum.
Additionally, polarity—either electrode positive (DCEP) or electrode negative (DCEN)—needs to be adjusted based on the electrode and the welding position to control the penetration and strength of the weld.
Heat and Temperature Control
Control of temperature is vital to prevent metal distortion and maintain the structural integrity of the weld.
Maintaining the right level of heat is a balancing act; too much heat can cause warping or burn-through, while insufficient heat can lead to weak, porous welds.
Utilizing appropriate settings on your arc welder and employing techniques such as preheating and controlling travel speed can assist in maintaining the optimum temperature for your welding project.
Joining and Strength Factors
Several factors influence the joining quality and strength of welds, including weld design, joint preparation, and electrode selection.
It's important to understand the type of joint being welded (butt, lap, corner, etc.) and prepare it properly.
Clean, well-prepared surfaces without contaminants contribute to the formation of strong welds.
Electrode selection is also critical and should match the metal being welded, affecting both the strength of the weld and the ease of welding.
For example, some electrodes are designed with specific coatings to provide deeper penetration and stronger weld joints.
Conclusion
Arc welding is a vital skill with diverse applications, from construction to manufacturing. The success of a weld depends on using the right settings, managing heat properly, and choosing suitable materials and equipment.
This ensures not only strong and reliable joins but also the safety of the welder. With these basics, anyone can begin to practice arc welding with an eye toward craftsmanship and quality work.
Frequently Asked Questions
Is arc welding good for beginners?
Yes, arc welding, particularly Shielded Metal Arc Welding (SMAW), also known as stick welding, is considered good for beginners. It requires less equipment and is more forgiving with regards to weld cleanliness. Its simplicity makes it a great starting point for those new to welding.
Do arc welders need gas?
Not all arc welders need gas. Stick welders (SMAW) and some types of Flux-Cored Arc Welders (FCAW) do not require shielding gas because they use flux-coated electrodes or flux-cored wire that provides the necessary protection from contamination.
However, other types like GMAW/MIG and Gas Tungsten Arc Welders (GTAW/TIG) do need shielding gas to protect the weld area from atmospheric gasses.
Are most arc welders AC or DC?
Many modern arc welders can operate on both AC and DC. However, DC is more commonly used because it provides a steadier arc, easier starts, better control, and smoother welds. DC welding machines are primarily used for most applications, although some specific processes might call for AC.
Do arc welders use a lot of electricity?
The amount of electricity arc welders use can vary widely based on the welding process and the thickness of the materials being welded.
Generally, welding equipment can consume a significant amount of power, but newer inverter-based models are designed to be more energy-efficient compared to traditional transformer-based welders.
How thick can an arc welder weld?
The welding thickness an arc welder can handle depends on the machine’s power and the welding process used. Stick welders can typically handle materials from about 1/16-inch thick up to 1/2-inch or more with a single pass, but multi-pass techniques can weld thicker sections.
Is an arc weld stronger than MIG weld?
Whether an arc weld is stronger than a MIG weld depends on the context of the welding job. Both can produce high-quality, strong welds if done correctly. The difference often lies in the specifics of the application and the skill of the welder.
For instance, MIG welding is generally preferred for thinner metals and produces cleaner welds, whereas stick welding is often used for outdoor applications and on thicker materials.
What is an arc welder good for?
An arc welder is versatile and can be good for a variety of tasks, including construction, fabrication, shipbuilding, and automotive work. It is particularly useful for its portability, ability to weld in various positions, and effectiveness with rusty or dirty metal. Arc welders are also valued in environments where simplicity and reliability are necessary.