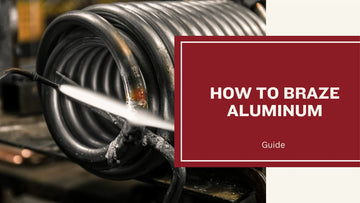
Brazing aluminum can be a tricky process, but with the right knowledge and technique, it can be done successfully. Brazing is a method of joining two or more pieces of metal by heating them to a temperature above 450°C and melting a filler metal into the joint. It is commonly used in the manufacturing of aircraft, automotive, and other high-tech industries.
Aluminum is a popular metal for brazing due to its lightweight, high strength-to-weight ratio, and corrosion resistance. However, it can be difficult to braze because it has a high thermal conductivity and a low melting point compared to other metals. Therefore, it is important to have a good understanding of the properties of aluminum and the brazing process before attempting to braze aluminum. In this article, we will provide you with the knowledge and techniques necessary to successfully braze aluminum.
What Is Aluminum Brazing?
Aluminum brazing is a process of joining two aluminum pieces together using a filler metal that has a lower melting point than the base metal. The process involves heating the aluminum parts and the brazing rod to a temperature above the melting point of the filler metal, but below the melting point of the base metal. The filler metal then flows between the aluminum parts, creating a strong and durable joint.
It is commonly used in the automotive, aerospace, and HVAC industries, among others. It is often preferred over welding because it does not require the melting of the base metal, which can cause distortion and weakening of the joint.
Aluminum Brazing Rod
The aluminum brazing rod is the filler metal used in the aluminum brazing process. It is typically made of aluminum-silicon alloy, which has a lower melting point than the base aluminum metal. The aluminum brazing rod is available in different diameters and compositions, depending on the application and the type of aluminum being brazed.
In summary, aluminum brazing is a process of joining two aluminum parts together using a filler metal with a lower melting point than the base metal. The aluminum brazing rod is the filler metal used in the process, and it is typically made of aluminum-silicon alloy.
The Different Types of Aluminum Brazing
When it comes to aluminum brazing, there are several different methods to choose from. Each method has its own advantages and disadvantages, and the one you choose will depend on your specific needs and circumstances. Here are the different types of aluminum brazing:
1. Manual and Automatic Brazing
Manual brazing involves using a torch to heat the joint and applying the filler metal manually. This method is simple and inexpensive, but it can be time-consuming and requires a high level of skill. Automatic brazing, on the other hand, uses a machine to heat the joint and apply the filler metal. This method is faster and more consistent, but it can be more expensive.
2. Aluminum Dip Brazing
Aluminum dip brazing involves immersing the parts to be joined in a molten salt bath containing the filler metal. The heat from the bath melts the filler metal and bonds the parts together. This method is ideal for complex parts and assemblies, but it requires specialized equipment and can be expensive.
3. Furnace (Controlled Atmosphere) Brazing
Furnace brazing involves heating the parts in a controlled atmosphere furnace and applying the filler metal. This method is ideal for large or complex parts, and the controlled atmosphere helps prevent oxidation and other defects. However, it can be expensive and requires specialized equipment.
4. Induction Brazing
Induction brazing uses an electromagnetic field to heat the parts and apply the filler metal. This method is fast, efficient, and precise, and it can be used for a wide range of part sizes and shapes. However, it requires specialized equipment and can be expensive.
In summary, each type of aluminum brazing has its own advantages and disadvantages, and the one you choose will depend on your specific needs and circumstances. Whether you choose manual or automatic brazing, dip brazing, furnace brazing, or induction brazing, make sure to follow the proper safety procedures and use the appropriate equipment for the job.
Materials and Tools Required
When it comes to brazing aluminum, you'll need a few specific materials and tools to get the job done right. Here are the key items you'll need to gather before you begin:
1. Choosing the Right Brazing Rod
The brazing rod you choose will depend on the specific type of aluminum you're working with and the intended use of the finished product. For general-purpose brazing, a 4043 aluminum brazing rod is a good choice. However, if you're working with a different type of aluminum, such as 6061 or 7075, you'll need to choose a brazing rod that is specifically designed for that alloy.
2. Selecting a Suitable Torch and Heat Source
When it comes to brazing aluminum, you'll need a torch that is capable of producing enough heat to melt the brazing rod and fuse it to the aluminum. A propane or acetylene gas torch is a good choice, as they are both capable of producing high temperatures. You'll also need a heat source, such as a firebrick or a heat-resistant surface, to place your workpiece on while you're brazing.
3. Flux Types and Their Uses
Flux is used to clean the surface of the aluminum and help the brazing rod flow smoothly. There are several different types of flux available, including flux paste and all-purpose flux. The type of flux you choose will depend on the specific type of aluminum you're working with and the intended use of the finished product.
In addition to these key items, you'll also need basic supplies such as safety goggles, gloves, and a wire brush to clean the aluminum before brazing. With the right materials and tools, you'll be well on your way to brazing aluminum like a pro.
Preparing the Aluminum for Brazing
Before brazing aluminum, it is essential to properly prepare the surface to ensure a strong and reliable bond. This section will cover two key steps in preparing aluminum for brazing: cleaning and degreasing, and surface abrasion techniques.
1. Cleaning and Degreasing
To achieve a successful brazing joint, it is crucial to remove any contaminants from the aluminum surface. Contaminants such as dirt, oil, and grease can prevent the brazing material from adhering properly, resulting in a weak bond.
To clean the aluminum, use a wire brush or emery cloth to remove any loose dirt or debris. Next, use a degreasing solvent, such as acetone, to remove any remaining oil or grease. Be sure to wear gloves and work in a well-ventilated area when using solvents.
2. Surface Abrasion Techniques
To ensure a strong bond, the aluminum surface should be abraded to remove any oxidation or aluminum oxide layer. Abrading the surface will also increase the surface area, allowing for better adhesion of the brazing material.
One common method of surface abrasion is using sandpaper. Begin by using a coarse grit sandpaper, such as 80 grit, and work your way up to a finer grit, such as 220. Be sure to sand the surface evenly and in one direction.
Another method of surface abrasion is using a wire brush or abrasive blasting. These methods are particularly useful for larger surfaces or complex shapes.
By properly cleaning and abrading the aluminum surface, you can ensure a strong and reliable brazing joint.
Safety Measures and Precautions
When brazing aluminum, it is important to take safety measures and precautions to protect yourself and those around you. Here are some key things to keep in mind:
1. Personal Protective Equipment
Wearing the right personal protective equipment (PPE) is essential when brazing aluminum. This includes:
- Safety glasses or goggles to protect your eyes from flying debris and hot metal.
- Welding Gloves to protect your hands from burns and cuts. Choose gloves that are heat-resistant and provide a good grip on your tools.
- A respirator or mask to protect your lungs from harmful fumes. Make sure the respirator is rated for aluminum brazing and fits properly.
It is also important to wear clothing that covers your skin and does not dangle or hang loosely. Avoid wearing synthetic fabrics that can melt or catch fire.
2. Proper Ventilation and Fume Management
Brazing aluminum produces fumes that can be harmful if inhaled. To protect yourself and others, make sure you work in a well-ventilated area. This means opening windows and doors, and using fans or ventilation systems to move air through the workspace.
If you are brazing in a confined space, use a fume extractor to remove harmful fumes from the air. Be sure to position the extractor close to your work area, and change the filter regularly.
It is also important to properly dispose of any materials that may contain hazardous substances, such as used flux or brazing rods. Check with your local waste management facility to find out how to dispose of these materials safely.
By following these safety measures and precautions, you can protect yourself and others while brazing aluminum. Remember to always wear the proper PPE, work in a well-ventilated area, and properly dispose of any hazardous materials.
Brazing Process and Techniques
Brazing is a process that involves joining two pieces of aluminum by melting a filler metal and allowing it to flow into the joint by capillary action. The following subsections will describe the brazing process and techniques in detail.
1. Applying Flux and Assembling the Joint
Before brazing, it is important to clean the joint thoroughly to remove any dirt or oil. Once the joint is clean, apply a flux to the joint area. The flux helps to prevent oxidation of the aluminum during the brazing process.
Next, assemble the joint with the correct joint clearance. The joint clearance is the distance between the two pieces of aluminum that are being joined. The proper joint design and clearance are important for creating a strong joint.
2. Heating the Aluminum to the Correct Temperature
The next step is to heat the aluminum to the correct brazing temperature. The brazing temperature is the temperature at which the filler metal melts and flows into the joint. The brazing temperature varies depending on the type of aluminum being brazed and the filler metal being used.
Torch brazing and dip brazing are two common methods used to heat the aluminum. Torch brazing involves using a torch to heat the joint area, while dip brazing involves immersing the joint in a molten salt bath.
3. Applying the Filler Metal
Once the aluminum has reached the correct brazing temperature, it is time to apply the filler metal. The filler metal should be in the form of a filler rod or wire. The filler material should match the composition of the aluminum being brazed.
As the filler metal is applied, it will flow into the joint by capillary action. Capillary action is the ability of a liquid to flow in narrow spaces without the assistance of, or in opposition to, external forces like gravity.
4. Cooling and Cleaning the Brazed Joint
After the filler metal has flowed into the joint, allow the joint to cool slowly. Do not quench the joint in water, as this can cause the joint to crack.
Once the joint has cooled, clean the joint to remove any flux residue. The brazed joint should be visually inspected for any defects or cracks. The joint strength should also be tested to ensure that it meets the required specifications.
Therefore, to brazed aluminum it requires proper joint design, joint clearance, and the correct brazing temperature. By following the above techniques, you can create strong and reliable brazed joints.
Benefits of Aluminum Brazing
Aluminum brazing has several benefits that make it a popular choice for joining aluminum parts. Here are some of the advantages of aluminum brazing:
-
Strong and Durable Joints: Aluminum brazing produces joints that are strong and durable. The brazed joints are able to withstand high stresses and strains, making them ideal for use in applications that require high strength and durability.
-
High Thermal Conductivity: Aluminum brazing is an excellent method for joining aluminum parts that need to transfer heat. The brazed joints have high thermal conductivity, which means that they can transfer heat efficiently from one part to another.
-
Corrosion Resistance: Aluminum brazing produces joints that are highly resistant to corrosion. This makes them ideal for use in harsh environments where the parts are exposed to moisture, salt, and other corrosive substances.
-
Cost-Effective: Aluminum brazing is a cost-effective method for joining aluminum parts. It requires less time, labor, and equipment than other methods such as welding or soldering.
-
Versatility: Aluminum brazing can be used to join a wide range of aluminum parts, including different alloys and thicknesses. This makes it a versatile method that can be used in various industries such as automotive, aerospace, and electronics.
Overall, aluminum brazing is a reliable and effective method for joining aluminum parts. Its benefits make it a popular choice for many applications where strong, durable, and efficient joints are required.
Applications of Brazed Aluminum
Brazing aluminum has a wide range of applications, from manufacturing to DIY projects and home repairs. Brazed aluminum is commonly used in heat exchangers due to its excellent thermal conductivity and corrosion resistance.
DIY Projects and Home Repairs
For DIY enthusiasts and hobbyists, brazing aluminum can be a useful skill to have. It can be used to repair aluminum parts, such as bicycle frames, car parts, and even household items like pots and pans. Brazing aluminum can also be used to create custom metal sculptures and jewelry.
When brazing aluminum for DIY projects, it is important to use the right equipment and follow proper safety procedures. Make sure to wear protective gear, such as gloves and eye goggles, and work in a well-ventilated area. It is also important to choose the right brazing rod and flux for the job.
Overall, brazed aluminum is a versatile material that can be used in a variety of applications. Whether you are a manufacturer or a DIY enthusiast, brazing aluminum can help you create durable and reliable products.
Conclusion
You now have a good understanding of how to braze aluminum. Remember that aluminum brazing requires a few specific steps to ensure a strong and reliable bond.
First, make sure the aluminum surfaces are clean and free of any oil, grease, or other contaminants. Use a wire brush or sandpaper to remove any oxidation or corrosion.
Next, choose the appropriate brazing alloy and flux for your specific application. Consider factors such as joint design, joint clearance, and the strength and ductility required.
When brazing, use a neutral flame and apply heat evenly to both sides of the joint. Avoid overheating the aluminum, as this can cause warping or distortion.
Finally, allow the joint to cool slowly and avoid quenching it in water. This will help prevent cracking or other defects in the joint.
By following these steps and using the proper techniques, you can successfully braze aluminum and create strong, long-lasting bonds.
Frequently Asked Questions
What can I use to braze aluminum?
There are several options for brazing aluminum, including oxy-acetylene torches, MAPP gas torches, and propane torches. You will also need a brazing rod or filler metal that is specifically designed for aluminum.
Can I braze aluminum with propane torch?
Yes, you can use a propane torch for aluminum brazing, but it is important to note that propane does not burn as hot as oxy-acetylene or MAPP gas. This means that the brazing process may take longer and require more skill to achieve a good bond.
What kind of rod to use for aluminum brazing?
When brazing aluminum, it is important to use a brazing rod or filler metal that is specifically designed for aluminum. Some common options include aluminum-silicon, aluminum-zinc, and aluminum-magnesium filler metals.
Is brazed aluminum as strong as welded?
Brazed aluminum can be just as strong as welded aluminum, but it depends on the specific application and the skill of the person performing the brazing. It is important to follow proper brazing techniques and use the correct filler metal to ensure a strong bond.