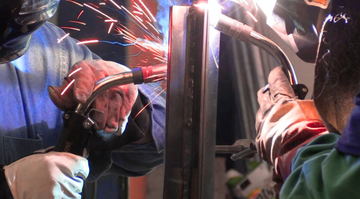
Dual shield welding is a go-to process for building strong steel structures, heavy equipment, and industrial projects.
This welding method combines a flux-cored wire with a shielding gas, delivering deep penetration and reliable welds, even on thick or dirty metal.
The result is a weld that stands up to demanding conditions, with less cleanup and fewer defects than many other methods.
If you want to create durable welds for construction, repairs, or fabrication, dual shield welding is worth considering. Read on to discover how this process works, where it excels, and how you can get started with confidence.
What Is Dual Shield Welding and Why Does It Matter?
Dual shield welding, also known as flux-cored arc welding with gas (FCAW-G), uses a special wire filled with flux and a shielding gas supplied from a tank.
The wire’s flux creates a protective slag, while the gas shields the weld pool from air. This dual protection gives the process its name and makes it especially effective for welding thicker steel.
The combination of flux and gas produces a stable arc, deep weld penetration, and less spatter. That’s why dual shield welding is a top choice for jobs where weld quality and productivity matter.
Dual shield welding is important because it allows welders to join heavy steel quickly and reliably. It is commonly used in construction, shipbuilding, and heavy equipment repairs, where welds need to be both strong and efficient.
How Dual Shield Welding Works: Step by Step
Knowing how dual shield welding works can help you achieve better results and avoid common mistakes. Let’s break down the process and the key equipment you’ll need.
The Dual Shield Welding Process
Dual shield welding starts with a wire feeder and a welding gun. The welder loads a spool of flux-cored wire into the machine and connects a gas cylinder, usually filled with carbon dioxide or a CO₂/argon mix.
As the gun’s trigger is pulled, the machine feeds the wire and releases shielding gas at the same time.
The arc melts the wire and the base metal, while the flux inside the wire forms a protective slag over the weld.
The shielding gas keeps oxygen and nitrogen away from the weld pool, preventing defects like porosity and cracking. The result is a strong, clean weld with good mechanical properties.
While dual shield welding produces less spatter and is easier to clean than stick welding, it does still create slag that must be chipped away after welding.
Key Equipment for Dual Shield Welding
- Wire feeder and compatible welding machine
- Flux-cored (dual shield) wire
- Shielding gas (CO₂ or CO₂/argon blend)
- Welding helmet, gloves, and protective clothing
Proper setup is crucial. Adjust your voltage and wire feed speed to match the thickness of your steel. Always check your shielding gas flow before you strike an arc.
Advantages of Dual Shield Welding
Dual shield welding offers a unique balance of speed, strength, and versatility. It is faster than stick or TIG welding and produces stronger welds than self-shielded flux core or MIG on thick steel.
The process handles dirty or slightly rusty metal better than most, making it ideal for tough job sites.
- High deposition rates: You can lay down more metal in less time.
- Deep penetration: Welds fuse thick steel with confidence.
- Cleaner results: Less spatter and easier slag removal mean less time spent grinding.
This makes dual shield welding a top pick for structural fabrication, bridge building, and repairing heavy machinery.
📌 Want to see the different types of welds and joints you can make? Browse this guide for more details.
Common Applications for Dual Shield Welding
Dual shield welding is trusted in a variety of industries because it’s efficient, reliable, and versatile. Here’s where you’ll see it most often.
Dual shield welding shines in environments where strength and productivity are critical. You’ll find it in:
- Construction: Beams, columns, and steel frames
- Shipbuilding: Hulls and structural supports
- Heavy equipment: Repairs and fabrication
- Industrial fabrication: Large tanks, bridges, and platforms
While it is most common in industrial settings, dual shield welding can also be used for farm repairs, trailer builds, and home projects if you have the right equipment and ventilation.
📌 Thinking about a welding career? Check out what it’s like to be a welder and if it’s a good career choice.
Dual Shield Welding vs. Other Welding Processes
It’s important to compare welding processes so you can choose the best one for your project. Here’s how dual shield welding stacks up against other popular methods.
Dual Shield Welding vs. MIG Welding
- MIG welding uses a solid wire and shielding gas. It is best suited for clean, thin metals.
- Dual shield welding uses a flux-cored wire plus shielding gas. It provides deeper penetration and better performance on thick or less-than-perfect steel. It is less affected by drafts, making it more reliable for outdoor work.
Dual Shield Welding vs. Self-Shielded Flux Core
- Self-shielded flux core welding does not require a gas cylinder, so it is portable and works well in windy conditions.
- Dual shield welding produces cleaner, stronger welds and is preferred for structural projects where weld quality is critical.
When to Use Dual Shield Welding
Dual shield welding is best for steel 1/8 inch (3 mm) thick or more. For thinner metals, MIG or TIG welding may be a better choice, as dual shields can burn through thin material more easily.
Choose dual shield welding when you need speed, strength, and reliability, especially on thick steel or in demanding environments. For thin materials or light fabrication, MIG or TIG might be a better fit.
📌 Want to learn about welding positions and how they affect your welds? Browse this helpful article.
Getting Started with Dual Shield Welding
If you’re ready to try dual shield welding, a good setup is essential for strong, clean welds. Here’s how to pick the right materials and dial in your machine.
Choosing Wire and Gas
Select a dual shield wire that matches your base metal and thickness. Common wires are designed for mild or low-alloy steel.
For shielding gas, a common choice is a 75 percent Argon and 25 percent CO₂ mix for a smoother arc and less spatter. Straight CO₂ provides deeper penetration but may result in more spatter.
Setting Up Your Welder
- Load the wire spool and thread it through the gun.
- Connect your shielding gas and set the flow rate, usually 25 to 35 cubic feet per hour.
- Adjust voltage and wire speed based on your metal thickness.
- Test your setup on scrap steel and fine-tune as needed.
Welding Technique Tips
Hold the gun at a slight drag angle, about 10 to 15 degrees from vertical, and move steadily along the joint.
Listen for a smooth, steady arc. Keep your work area clean and well-ventilated to minimize fumes and ensure safety.
Safety Considerations in Dual Shield Welding
Welding safely is crucial to protect yourself and your workspace from hazards. Dual shield welding produces heat, sparks, and significant fumes, so extra precautions are needed.
-
Always wear:
- A welding helmet with the correct shade
- Fire-resistant gloves
- Long sleeves and pants
-
Protect your eyes and skin from:
- Sparks
- UV light
- Hot metal
-
Ensure proper ventilation:
- Dual shield welding produces more fumes than MIG or TIG welding
- Work in a well-ventilated area or use fume extraction
-
Additional safety steps:
- Keep a fire extinguisher nearby
- Avoid welding near flammable materials
- Inspect your gas connections and equipment before every job
Troubleshooting Dual Shield Welding
Even with the best setup, challenges can arise during dual shield welding. Here’s how to identify and fix common problems for better welds.
- Porosity: Check for proper gas flow and clean your base metal.
- Excess spatter: Adjust your voltage and wire speed, and make sure your gas is flowing.
- Inconsistent welds: Practice steady hand movement and keep your wire stick-out, the distance from the tip to the work, consistent.
Practice and patience are key. Test your settings on scrap pieces before working on your actual project.
Final Thoughts
Dual shield welding delivers reliable, high-strength welds for heavy steel and demanding projects.
By combining a flux-cored wire with shielding gas, this process offers deep penetration, fast welding speeds, and cleaner results.
With the right setup, safety practices, and a bit of practice, you can achieve professional-quality welds for construction, fabrication, or repairs.
For more helpful welding guides, tips, and in-depth resources, don’t forget to check out Arccaptain.
And if you’re looking to upgrade your equipment or want the best results for your next project, browse and shop Arccaptain welding machines. These are designed to help you weld with confidence and precision.
You May Also Like
Frequently Asked Questions About Dual Shield Welding
Do you drag or push dual shields?
Most welders use the drag, or pull, technique with dual shield welding. This means you point the welding gun back toward the weld and move away from the finished bead. Dragging helps keep the weld pool protected by the shielding gas and flux, leading to a cleaner, stronger weld.
What is the difference between dual shield and flux core wire?
Dual shield wire is a flux-cored wire designed to be used with an external shielding gas, providing extra protection around the weld. Regular, self-shielded, flux core wire creates its own shield and doesn’t need gas. Dual shield wires are preferred for heavy-duty jobs and usually produce stronger, cleaner welds.
What are the disadvantages of FCAW welding?
FCAW, including dual shield welding, tends to produce more smoke and fumes than other welding processes, so good ventilation is important. The process also creates slag that must be chipped away after welding. It may not be the best option for thin metals, as it can burn through more easily.
What are the two types of welding shields?
The two main types of welding shields are passive and auto-darkening helmets. Passive helmets have a fixed dark lens, while auto-darkening helmets automatically adjust their shade when you start welding. Both types protect your eyes and face from the bright light and sparks created during welding.
📖 Related Articles to Read:
What is Stick Welding and How Does it Work?