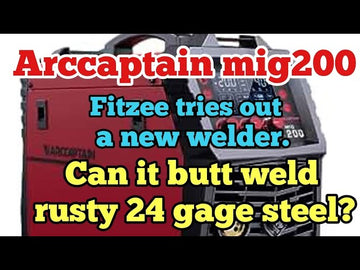
In the world of welding, versatility and precision are key. That's why the Arccaptain MIG200 Multi-Process Welder has been creating a buzz in the industry. As a seasoned welding enthusiast, I recently had the opportunity to delve into the capabilities of this multi-functional welding machine, and I'm eager to share my findings.
1. Voltage and Wire Speed Coordination: One of the first discoveries was the importance of balancing voltage with wire speed. I found that a setting of 70 on the wire speed, combined with 14.8 volts, was effective. However, this was just a starting point.
2. Manual Adjustments for Precision: Switching to manual mode, I experimented with keeping the voltage constant while varying the wire speed. For instance, maintaining 14.8 volts and adjusting the wire speed to 7.5 provided a different welding character.
3. Exploring Higher Voltage Settings: Surprisingly, increasing the voltage to around 17 volts while managing the wire speed yielded better penetration and smoother welds. This was particularly evident in the quality of the welds, which were significantly improved compared to the lower voltage settings.
4. Fine-Tuning for Thin Metal: The real test came with welding the thin metal. After several trials, I settled on a setting of 15 for wire speed and 6 for voltage. This provided a good balance for welding 24-gauge metal without excessive heat or burn-through.
5. Spot Welding Feature: I also explored the spot welding feature, setting the timer to one second per spot weld. This ensured consistency and precision in each weld, crucial for maintaining the integrity of thin metal.
6. Gap Welding Adjustments: For welding with a gap, I adjusted the settings to 14 volts with a wire speed of 6. This allowed for filling gaps effectively without overheating the metal.
7. Final Preferred Settings: After extensive testing, my preferred settings for the Arccaptain MIG200 were a higher voltage (around 16 volts) with a slightly lower wire speed (around 5 or 6). This combination seemed to offer the best results for both penetration and smoothness in the welds.
The Arccaptain MIG200: A Jack of All Trades
The Arccaptain MIG200 stands out as a multi-process welder, capable of handling MIG, Flux, TIG, and Arc welding. It even boasts the ability to weld aluminum, a feature not commonly found in many welders. While there are numerous videos showcasing its heavy-duty welding capabilities, I noticed a gap in demonstrations of its performance on lighter materials, particularly sheet metal. This piqued my interest: could this robust machine handle the delicate art of welding thin metals without overpowering them?
Putting the Welder to the Test
To answer this question, I decided to conduct a hands-on test using 24-gauge rusty metal. My goal was to explore the welder's ability to butt weld these thin sheets without causing burn-through or excessive heat damage.Features and Setup
Before diving into the welding process, it's worth noting the Arccaptain MIG200's impressive range of features. It offers a variety of welding modes, including MIG, TIG, Arc, and Flux Core, though my focus was primarily on its MIG welding capabilities for sheet metal work. The welder can operate on both 220V and 110V, though I used the 110V setting for my tests. It comes equipped with a ground cable and a MIG gun, both of decent quality. However, I encountered a minor hiccup with the welding tips provided; they didn't include the 0.23 six-millimeter tips needed for my project, necessitating a quick run to the store.Welding Process and Adjustments
After setting up the welder with the correct wire and tips, I began experimenting with various settings. The Arccaptain MIG200 offers a user-friendly interface, allowing for easy adjustments of wire speed and heat settings. I started with the lowest settings, gradually tweaking them to find the optimal balance for welding thin metal.Initial Settings and Adjustments
Initially, I started with the machine's lowest settings, as working with thin, 24-gauge rusty metal required a gentle approach. The Arccaptain MIG200's interface facilitated this process, allowing for incremental adjustments. However, finding the sweet spot required more than just starting low; it demanded a nuanced understanding of how each change affected the weld.Detailed Parameter Settings
As I progressed, I meticulously noted the various settings and their impact on the welding quality:1. Voltage and Wire Speed Coordination: One of the first discoveries was the importance of balancing voltage with wire speed. I found that a setting of 70 on the wire speed, combined with 14.8 volts, was effective. However, this was just a starting point.
2. Manual Adjustments for Precision: Switching to manual mode, I experimented with keeping the voltage constant while varying the wire speed. For instance, maintaining 14.8 volts and adjusting the wire speed to 7.5 provided a different welding character.
3. Exploring Higher Voltage Settings: Surprisingly, increasing the voltage to around 17 volts while managing the wire speed yielded better penetration and smoother welds. This was particularly evident in the quality of the welds, which were significantly improved compared to the lower voltage settings.
4. Fine-Tuning for Thin Metal: The real test came with welding the thin metal. After several trials, I settled on a setting of 15 for wire speed and 6 for voltage. This provided a good balance for welding 24-gauge metal without excessive heat or burn-through.
5. Spot Welding Feature: I also explored the spot welding feature, setting the timer to one second per spot weld. This ensured consistency and precision in each weld, crucial for maintaining the integrity of thin metal.
6. Gap Welding Adjustments: For welding with a gap, I adjusted the settings to 14 volts with a wire speed of 6. This allowed for filling gaps effectively without overheating the metal.
7. Final Preferred Settings: After extensive testing, my preferred settings for the Arccaptain MIG200 were a higher voltage (around 16 volts) with a slightly lower wire speed (around 5 or 6). This combination seemed to offer the best results for both penetration and smoothness in the welds.
The Verdict: A Reliable Tool for Thin Metal Welding
The Arccaptain MIG200 exceeded my expectations. It demonstrated exceptional versatility, handling thin sheet metal with the same ease as it would thicker materials. This welder proved to be an excellent choice for those working with a variety of metal thicknesses, particularly in automotive applications where precision is crucial.Final Thoughts
In conclusion, the Arccaptain MIG200 Multi-Process Welder is a robust, versatile tool that's surprisingly adept at handling both heavy-duty and delicate welding tasks. Its ability to weld thin metal with precision makes it a valuable asset for any welder, from hobbyists to professionals. Whether you're working on automotive repairs or creative metal projects, the Arccaptain MIG200 is a reliable, high-quality choice that won't disappoint.
Tags: