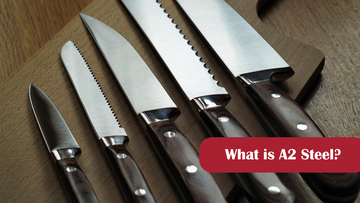
A2 steel stands out as one of the most versatile and widely used air-hardening tool steels in modern manufacturing and craftsmanship.
Known for its exceptional balance of hardness, toughness, wear resistance, and dimensional stability, A2 steel is a favorite among toolmakers, machinists, and knife makers alike.
This comprehensive guide explores everything you need to know about A2 steel. Its chemical composition, key properties, common applications, heat treatment processes, advantages, disadvantages, and how it compares to other popular tool steels.
Whether you’re selecting steel for a new tool, knife, or die, understanding A2 steel’s unique characteristics will help you make an informed decision.
What is A2 Steel?
A2 steel is a medium-alloy, air-hardening tool steel classified under the “A” group of tool steels by the AISI (American Iron and Steel Institute). The “A” designation indicates that it hardens in air rather than in oil or water, offering excellent dimensional stability and reducing the risk of distortion during heat treatment.
Chemical Composition of A2 Steel
A2 steel’s performance is rooted in its carefully balanced alloying elements. Here’s a typical chemical composition:
Element |
Symbol |
Typical Content (%) |
Function |
Carbon |
C |
0.95–1.05 |
Hardness, wear resistance |
Chromium |
Cr |
4.75–5.50 |
Hardenability, wear resistance, corrosion resistance |
Molybdenum |
Mo |
0.90–1.40 |
Toughness, hardenability |
Vanadium |
V |
0.15–0.50 |
Wear resistance, grain refinement |
Manganese |
Mn |
0.50–1.00 |
Deoxidizer, improves hardness |
Silicon |
Si |
0.20–0.50 |
Deoxidizer, strength |
Phosphorus |
P |
≤0.03 |
Impurity (should be low) |
Sulfur |
S |
≤0.03 |
Impurity (should be low) |
Iron |
Fe
|
Balance |
Matrix
|
Role of Key Alloying Elements
Each alloying element in A2 steel plays a specific role in tailoring its mechanical and physical properties for demanding applications.
The careful balance of these elements results in a tool steel that offers an optimal combination of hardness, toughness, wear resistance, and dimensional stability.
- Carbon (C): Provides hardness and wear resistance.
- Chromium (Cr): Increases hardenability and wear resistance, some corrosion resistance.
- Molybdenum (Mo): Enhances toughness and hardenability.
- Vanadium (V): Improves wear resistance and refines grain structure.
- Manganese (Mn) & Silicon (Si): Aid in deoxidation and contribute to strength.
Key Properties of A2 Steel
A2 steel is prized for its well-rounded set of properties, making it suitable for demanding tooling and cutting applications.
- Hardness: After proper heat treatment, A2 steel typically achieves a Rockwell C hardness (HRC) in the range of 57–62 \(HRC\).
- Toughness: Offers better toughness than many high-carbon, high-wear tool steels (like D2), making it less prone to chipping or cracking under impact.
- Wear Resistance: Provides good wear resistance, suitable for many tooling and knife applications, though not as high as some high-chromium grades.
- Machinability: Relatively easy to machine in the annealed state, making it convenient for manufacturing complex shapes before hardening.
- Dimensional Stability: Outstanding dimensional stability during heat treatment, thanks to its air-hardening nature—critical for precision tools and dies.
- Hardenability: Uniform hardness can be achieved even in larger cross-sections due to its strong air-hardening response.
You May Also Like
Common Applications of A2 Steel
A2 steel's exceptional balance of hardness, toughness, wear resistance, and dimensional stability makes it a highly versatile material, finding widespread use in numerous demanding applications across various industries:
Tool and Die Making
This remains one of the primary application areas for A2 steel due to its ability to maintain precise shapes and withstand significant forces. Specific examples include:
- Stamping Dies: Used for cutting, punching, and shaping sheet metal components in high-volume production. A2's toughness helps prevent chipping and cracking under repeated impact.
- Forming Dies: Employed to bend, mold, or otherwise shape metal into desired forms. A2's wear resistance ensures the die maintains its profile over extended production runs.
- Shear Blades: Utilized for cutting various materials, from paper and plastics to thicker gauge metals. A2's ability to hold a good edge and resist wear is crucial for clean and efficient cutting.
- Punches: Used to create holes or specific shapes in materials. A2's combination of hardness and toughness prevents premature dulling and breakage under compressive forces.
- Coining Dies: Employed to impart intricate designs onto metal blanks, requiring high compressive strength and resistance to deformation, which A2 provides.
- Thread Rolling Dies: Used to form screw threads on metal fasteners. A2's wear resistance is essential for maintaining the precise thread profile over many cycles.
- Lamination Dies: Used in the production of thin layers (laminations) for electric motors and transformers, requiring dimensional accuracy and wear resistance.
Knife Making
A2 steel has gained significant popularity among knife makers for its well-rounded properties:
- Fixed-blade knives: Prized for their durability and ability to hold a sharp edge for extended periods, while still being relatively easier to sharpen compared to more wear-resistant steels. This makes it a good choice for general-purpose, hunting, and survival knives.
- Utility and outdoor knives: Its toughness is particularly valued in knives that may encounter significant stress or impact during use in outdoor environments. The balance of edge retention and ease of maintenance makes it a practical choice for these applications.
- Tooling for Woodworking Knives: Used in the creation of high-quality plane irons, chisels, and other woodworking tools where edge retention and toughness are critical for precision work.
Gauges and Fixtures
The excellent dimensional stability of A2 steel after hardening makes it ideal for precision applications:
- Precision Gauges: Used for accurate measurement of dimensions in manufacturing and quality control A2's resistance to distortion ensures the long-term accuracy of these critical tools, including plug gauges, ring gauges, and feeler gauges.
- Workholding Fixtures: Employed to securely hold workpieces during machining or assembly operations. A2's dimensional stability ensures that the fixture maintains its precise shape and dimensions, leading to accurate and repeatable manufacturing processes. This includes jigs, clamps, and specialized holding devices.
- Mandrels: Used as a core around which material is formed or shaped. A2's hardness and dimensional stability are crucial for maintaining the required shape and size of the final product.
Machine Parts
A2 steel's combination of good wear resistance and toughness makes it a reliable choice for various machine components that experience friction, abrasion, and impact during operation:
- Wear-resistant components: This includes parts designed to withstand continuous rubbing or contact with other surfaces. Examples are bushings that reduce friction between moving parts, guide rails that provide smooth and wear-resistant pathways for machinery movement, and cams that convert rotary motion into linear motion with consistent surface contact. A2's hardness helps these components maintain their shape and function over extended periods.
- Rolls and Forming Rolls: Used in metalworking and other industrial processes to shape materials. A2's wear resistance and toughness ensure the rolls maintain their profile and resist chipping under pressure.
- Chuck Jaws: Found in machining equipment to securely hold workpieces. A2's hardness and resistance to deformation provide reliable gripping force and longevity.
- Tool Holders: Used to securely hold cutting tools in machining operations. A2's strength and resistance to wear contribute to stable and accurate machining.
- Industrial Hammers: In applications where durable hammers are needed, A2 steel offers a good balance of hardness to prevent deformation and toughness to resist chipping.
Plastic Molds
While not as wear-resistant as specialized mold steels, A2 steel can be suitable for certain plastic molding dies:
- Moderate wear resistance and dimensional stability are required: For shorter production runs or when the plastic being molded is not highly abrasive, A2 can offer a cost-effective solution. Its dimensional stability during heat treatment is crucial for maintaining the accuracy of the mold cavity, ensuring consistent part dimensions.
- Prototype and short-run molds: A2's machinability can be advantageous for creating prototype molds or molds for limited production quantities.
- Mold components: Certain components of more complex molds, such as ejector pins, mold frames, and support plates, can be made from A2 steel due to its strength and dimensional stability.
Advantages of A2 Steel
A2 steel's popularity stems from its well-rounded performance characteristics, making it a favored material in toolmaking and beyond. The following highlights the key benefits that contribute to its widespread use.
- Excellent balance of hardness and toughness
- Good wear resistance for most tooling and knife applications
- Outstanding dimensional stability during heat treatment
- Good hardenability (uniform hardness, even in thick sections)
- Relatively good machinability (when annealed)
Disadvantages of A2 Steel
Despite its many positive attributes, A2 steel does have certain limitations that should be considered for specific applications. The following points outline the primary drawbacks associated with its use.
- Wear resistance not as high as some tool steels (e.g., D2 steel)
- Corrosion resistance is limited, not comparable to stainless steels
- Not suitable for saltwater or highly corrosive environments
Heat Treatment of A2 Steel
Proper heat treatment is crucial to unlocking A2 steel’s full potential. The typical heat treatment cycle includes:
1. Annealing
- Purpose: Soften the steel for machining.
- Process: Heat to 850–870°C (1560–1600°F), hold, then cool slowly (furnace or still air) at a rate of 10–20°C (20–40°F) per hour down to 650°C (1200°F), then air cool.
2. Stress Relieving
- Purpose: Remove internal stresses after machining.
- Process: Heat to 650–700°C (1200–1290°F), hold for 2 hours, then air cool.
3. Hardening
- Austenitizing Temperature: Heat to 955–980°C (1750–1800°F).
- Soak Time: Hold at temperature for 20–30 minutes.
- Cooling: Air cool (or forced air) to room temperature. This air-hardening step minimizes distortion.
4. Tempering
- Purpose: Adjust hardness and increase toughness.
- Process: Temper immediately after hardening. Typical tempering range is 175–540°C (350–1000°F), depending on desired hardness.
- Result: Double tempering is often recommended for optimal toughness and stability.
A2 Steel vs. Other Tool Steels
A2 is often compared to other popular tool steels, especially D2 and O1. Here’s how they stack up:
Property |
A2 Steel |
D2 Steel |
O1 Steel |
Hardening |
Air |
Air/Oil |
Oil |
Typical HRC |
57–62 |
58–62 |
57–62 |
Wear Resistance |
Good |
Excellent |
Moderate |
Toughness |
Good |
Moderate |
High |
Machinability |
Good (annealed |
Fair |
Good |
Dim. Stability |
Excellent |
Good |
Moderate |
Corrosion Res. |
Limited |
Limited |
Limited |
A2 vs. D2 Steel
- D2 steel offers higher wear resistance due to its higher chromium content (~12%), but at the cost of reduced toughness and increased brittleness.
- A2 steel provides a better balance of toughness and wear resistance, making it less prone to chipping.
A2 vs. O1 Steel
- O1 steel is oil-hardening and offers excellent toughness, but less dimensional stability and wear resistance than A2.
- A2 steel is preferred when dimensional accuracy after heat treatment is critical.
Conclusion
A2 steel is a versatile, air-hardening tool steel that strikes an impressive balance between hardness, toughness, wear resistance, and machinability.
Its exceptional dimensional stability during heat treatment makes it a top choice for precision tools, dies, and knife blades.
While it may not offer the extreme wear resistance of D2 or the corrosion resistance of stainless steels, A2’s all-around performance ensures its continued popularity in tool and die making, knife making, and beyond.
If your application demands a reliable, well-balanced tool steel, A2 is a proven contender.
Frequently Asked Questions
Is A2 steel good for knives?
Yes, A2 steel is highly regarded in the knife-making community. Its combination of hardness (for edge retention), toughness (resistance to chipping and breaking), and relative ease of sharpening makes it suitable for a wide range of knives, from outdoor and survival blades to utility knives. While not stainless, it is less prone to corrosion than high-carbon steels, though care should still be taken to prevent rust.
What is the Rockwell hardness of A2 steel?
After proper heat treatment, A2 steel typically achieves a Rockwell C hardness (\(HRC\)) in the range of 57–62 \(HRC\). The exact value depends on the tempering temperature and intended application.
How corrosion-resistant is A2 steel?
A2 steel offers better corrosion resistance than plain high-carbon steels due to its chromium content (\(4.75\% - 5.50\%\)), but it is not classified as a stainless steel. While it can resist light surface oxidation and staining in dry environments, A2 steel will rust if exposed to moisture, acids, or salts without proper care. For applications where corrosion resistance is critical, a true stainless steel should be considered.
Can A2 steel be welded?
Welding A2 steel is generally not recommended due to its high carbon and alloy content, which make it susceptible to cracking and loss of desirable mechanical properties in the heat-affected zone. If welding is absolutely necessary, preheating, post-weld heat treatment, and carefully controlled welding procedures must be used to minimize the risk of cracking and to restore hardness and toughness. For most tool and die applications, mechanical fastening or other joining methods are preferred over welding.
Related Articles:
Expert Guide to Increasing Deposition Rate in Welding