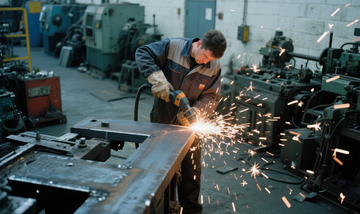
This article explains the definition of gouging in welding, explores the four most common gouging processes, including their principles, applications, pros, and cons. Additionally, this article explains how to select the appropriate gouging process based on material type, processing requirements, equipment, and environmental considerations.

I. What is Gouging in Welding
Gouging is a critical process in metal surface preparation and welding that involves removing corrosion and creating holes, grooves, or indentations on metallic surfaces. Known as metal gouging or welding gouging, this technique is widely used across various industry applications for inspection, surface assessment, and structural integrity. In maintenance and repair, the ability to execute precise metal grooving and gouging is essential for effective corrosion removal and ensuring metal surface treatment. Mastering gouging processes helps improve safety, prevent further corrosion, and maintain the longevity of structures and equipment.
II. The Most Popular Gouging Process
1.The Plasma Gouging
Plasma arc gouging utilizes a high-temperature plasma arc, reaching temperatures of up to 30,000°C, to melt metal while a compressed gas (such as air or nitrogen) blows away the molten material to create precise grooves. This plasma gouging process is ideal for welding repair and groove preparation on difficult-to-weld metals like stainless steel and aluminum. Its key advantages include high accuracy, minimal heat distortion, and excellent surface quality. However, the equipment tends to be expensive and requires professional operation, making it suitable for industrial applications and advanced welding projects.
2. Arc Gouging
Air carbon arc gouging involves creating a rough groove by melting metal with an electric arc between the electrode and workpiece, while compressed air blows away the molten slag. This method is commonly used for rapid grooving or defect repair on carbon steel. Its main advantages include low cost, high flexibility, and portability, making it suitable for on-site repair and rough cutting. However, the process produces poor surface quality and generates significant smoke and dust, which should be considered in work environments.
3. Air Carbon-arc Gouging
Air Carbon arc gouging uses a carbon rod electrode to create an electric arc that melts the metal, while high-pressure air (80-100 psi) is jetted into the molten pool to blow away slag. This technique is particularly effective for deep grooving or removing large defects on thick steel plates and castings. It offers high efficiency and rapid material removal but generates significant noise and produces carbon residues that may affect welding quality. Suitable for heavy-duty welding applications where speed and depth of cut are priorities.
4. Oxyfuel Gouging
Oxy-fuel flame (such as acetylene) heats metal to its ignition point, while pure oxygen flow oxidizes and blows away the molten material. This gas welding process is suitable for rough machining of low-carbon steel and maintenance of old structures. It features simple equipment but has a large heat-affected zone, slow welding speed, and low precision, making it ideal for basic metal fabrication and structural repairs where high accuracy is not critical.
III. How to Choose a Proper Gouging Process for Your Fabrication
1. Material Types and Suitable Cutting Methods
Carbon Steel / Low-Alloy Steel: Suitable for arc gouging, carbon arc gouging, and flame cutting.
Stainless Steel / Aluminum: Prioritize plasma arc gouging to prevent carbon contamination and oxidation issues.
Cast Iron / High-Carbon Steel: Use caution with flame cutting due to risk of cracking; carbon arc gouging or plasma gouging are recommended.
2. Processing Requirements and Choosing the Right Method
Precision Needs: For high-precision work (e.g., aerospace weld repair), select plasma gouging; for rough preprocessing, consider arc or flame cutting.
Cutting Depth: Use carbon arc gouging for thick plates (>20mm); plasma or arc gouging for shallow cleaning.
Surface Quality: Ranking from best to worst: plasma > carbon arc gouging > arc > flame.
3. Equipment, Cost, and Automation
Budget Constraints: Arc gouging or flame cutting are affordable with simple equipment.
Automation Needs: Plasma gouging integrates well with robotic systems for mass production.
Power Supply: For no-electric environments, flame cutting is preferred due to reliance on fuel gases.
4. Environmental Impact
Dust and Noise: Carbon arc gouging produces high levels of dust and noise; requires dust extraction. Plasma cutting is relatively more environmentally friendly.
Heat Deformation: High heat input from flame and arc methods can cause deformation of thin materials; careful parameter control is necessary.
5. Post-Processing Considerations
Welding Requirements: Avoid carbon residues from carbon arc gouging (may need grinding before welding); plasma gouging allows for direct welding.
Surface Coating / Corrosion Protection: For smooth surfaces, plasma gouging is preferred for subsequent spraying or anticorrosion treatments.

IV. The Future of Gouging
The future of gouging and cutting processes will focus on advancements in efficiency, environmental sustainability, and intelligent automation. As industrial automation becomes more widespread, robot-assisted plasma and laser gouging will dominate, enabling millimeter-level precision. Stricter environmental regulations are driving the development of low-dust arc technology and hydrogen fuel flame cutting as clean, eco-friendly alternatives. Additionally, emerging AI real-time control systems and advanced power supply technologies (such as high-frequency inverters) are expected to cut energy consumption by over 30%, making carbon steel, aluminum alloys, and even composite materials more cost-effective to process. Over the next five years, gouging technology is poised to evolve from a “metal surgical knife” into a fully automatic, eco-friendly processing center that supports smart manufacturing and green production.
Arccaptain is set to launch a new plasma cutter equipped with advanced plasma gouging functionality soon. Stay tuned for innovative cutting and gouging solutions that deliver high precision, efficiency, and eco-friendly performance!
Arccaptain Plasma Cutter Series: https://www.arccaptain.com/collections/plasma-cutter-portable