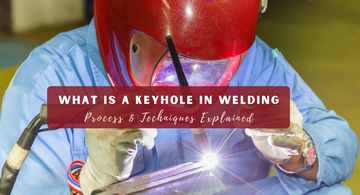
Keyhole welding is a specialized technique in which a strong heat source creates a small hole, or "keyhole," that penetrates deeply into the metal.
This method enables you to create deep, narrow welds that are exceptionally strong and clean. You may see keyhole welding used on thick steel or aluminum, particularly when you require reliable, high-quality weld seams.
Whether you're just learning about welding or want to improve your skills, understanding the keyhole technique in welding can help you get better and faster results.
You'll see why this method is important for both small projects and large industrial jobs.
What Is Keyhole Welding?
Keyhole welding is a welding process that utilizes a concentrated heat source to melt through a workpiece, creating a hole known as a "keyhole." This technique results in deep and narrow welds with good penetration.
Keyhole Mode vs Conventional Fusion Welding
In keyhole mode welding, a powerful heat source such as a laser or plasma arc melts completely through the material. This creates a small hole, or "keyhole," at the front of the weld pool. The keyhole is surrounded by molten metal, which solidifies as the weld moves forward.
Key differences from conventional fusion welding include:
- Heat Source: Keyhole welding uses a highly concentrated energy source. Conventional fusion welding distributes heat more broadly over the surface.
- Penetration: Keyhole mode produces deeper and narrower welds compared to broader, shallower welds in conduction mode.
- Process Physics: The keyhole allows gases to escape, enabling the weld pool to remain stable and reducing pores and defects.
- Applications: Keyhole welding is used for thick sections and metals that require full penetration, such as steel or aluminum.
In summary, keyhole welding offers distinct benefits for joining thicker materials with strong, consistent welds.
📌 Also Read: What is Spray Transfer Welding? (Beginner's Guide)
How Keyhole Welding Works
Keyhole welding uses a highly concentrated heat source, such as a laser, electron beam, or plasma arc. This heat melts and even vaporizes the material at the joint, creating a narrow cavity or keyhole.
Formation of the Keyhole:
The intense energy creates a small hole in the workpiece. A column of vaporized metal forms within this hole, often referred to as a plasma column. The keyhole allows heat to penetrate more deeply into the material.
Energy Density Requirements:
Different welding methods offer different energy densities:
- Laser and electron beam welding provide very high energy density. This is key for forming and maintaining the keyhole.
- Arc welding methods, such as plasma arc, can also create a keyhole, but they typically require more power.
While the energy is focused on a small area, the rest of the material remains cooler, helping to reduce part distortion.
📌 Also Read: Arc Welding VS Laser Welding
Material Flow and Solidification:
As the heat source moves forward, the molten metal at the rear of the keyhole flows back into the cavity. This fills the space and solidifies quickly, creating a strong weld.
You can expect minimal spatter and a neat weld bead. Because the keyhole process limits excess heat, the heat-affected zone stays small.
Types of Keyhole Welding Processes
Keyhole welding uses a concentrated heat source to create a deep, narrow weld with a high aspect ratio.
The main types are based on the type of energy source used and the welding method employed in various settings.
Laser Beam Keyhole Welding
Laser beam keyhole welding uses a focused laser to produce intense heat at a precise point. This high power melts the metal quickly, making a hole called a keyhole that goes through the workpiece.
You will find that this method is best suited for thin to medium-thick materials and parts that require very clean, accurate welds. It is often used in the electronics, medical, and automotive industries.
Key features:
- Works at high welding speeds, which increases productivity.
- Leaves minimal spatter and heat-affected zones, so your workpieces retain their shape and properties.
- Can join metals like steel, aluminum, and titanium, even in complex shapes.
- Needs precise alignment and high-quality equipment.
Laser keyhole welding reduces distortion; however, it typically requires safety precautions, such as shielding and protective eyewear.
Plasma Arc Keyhole Welding
Plasma arc keyhole welding uses a hot, ionized gas called plasma to create a narrow, deep weld. The plasma jet forms the keyhole and melts the base metal.
This method is suited for thick sections of metal and is widely used in industrial fabrications, shipbuilding, and pipeline work.
Plasma arc welding is reliable for joining stainless steel, aluminum, and other heat-resistant alloys.
Main points:
- Produces deep penetration with a consistent, high-quality weld bead.
- Helps you weld through thick plates in a single pass, saving time.
- Needs a pilot arc and a special nozzle system for stability and control.
- Can be automated for long continuous welds.
Shielding gases are required to protect the weld area from oxidation.
Electron Beam Keyhole Welding
Electron beam keyhole welding utilizes a high-speed electron beam in a vacuum to generate intense, focused heat on the workpiece. The energy melts the material, forming a keyhole that allows for deep weld penetration.
This type works best where ultra-clean and very deep welds are required, such as in aerospace, nuclear, and high-precision equipment manufacturing.
Important details:
- Can join thick or dissimilar metals with small heat-affected zones.
- Requires a vacuum chamber, which adds setup time and cost.
- Offers high welding speeds, very little distortion, and high-quality results.
- Excellent for applications where standard welding methods might introduce contamination.
This process is not suitable for on-site repairs due to the equipment and vacuum requirements.
Check out Related Products:
|
Arccaptain CUT50 Plasma Cutter Dual Voltage HF Start CutterThe CUT50 only needs to be connected to air, using an air compressor with a minimum pressure of 60 PSI and a flow rate of 3-5 CFM. Wait for the screen to turn off and the fan to stop before switching power. |
|
Arccaptain CUT55 Non-Touch Pilot Arc Plasma Cutter LED Display
|
|
Arccaptain iControl CUT55 Pro Pilot Arc Plasma CutterThe CUT55 Pro Pilot Arc Cutter by Arccaptain is a premium plasma cutter that boasts an upgraded design and an innovative air duct system, which improves cutting efficiency by 39%. Its non-contact pilot arc design enhances cutting performance across a variety of materials and applications while maintaining high quality. |
Advantages of Keyhole Welding
Keyhole welding offers several key benefits that make it a valuable tool in various industries. This process is especially valuable when you need strong, reliable welds. You will notice that keyhole welding is often chosen for demanding applications.
✅ Deep Penetration Capability: One of the main advantages is its ability to weld thick materials in a single pass. You can achieve strong welds without the need for multiple layers or extra preparation.
✅ Reduced Heat Affected Zone (HAZ): Keyhole welding focuses heat into a small area. This means less of the surrounding metal is affected by heat, which helps keep parts of your material stronger and more stable. It also reduces problems like distortion.
✅ High Welding Speeds & Efficiency: You can also complete keyhole welds quickly. The process is efficient, saving time and costs, especially for large and detailed projects.
- It reduces the risk of defects, such as lack of fusion and gas pores.
- Clean, smooth weld seams lessen the need for extra finishing.
- Both laser and electron beam methods utilize keyhole mode for achieving high-quality results.
Advantage |
Benefit |
Deep Penetration |
Thick materials welded in one pass |
Reduced HAZ |
Less metal affected by heat |
High Speed & Efficiency |
Faster, cleaner welding with fewer defects |
Keyhole welding is a dependable choice for critical joints, including those used in aerospace and heavy manufacturing.
Limitations and Challenges of Keyhole Welding
Keyhole welding offers deep, narrow welds at high speed, but there are several challenges to consider before using it.
1. Equipment Cost & Complexity
- You need advanced laser or electron beam equipment for keyhole welding.
- These machines are expensive to purchase and maintain.
- Setup and calibration often require skilled operators, making the process less accessible for smaller shops.
2. Process Control Requirements
- This welding method is very sensitive to changes in speed, power, and focus.
- Poor control over these factors can cause defects like porosity, undercuts, or humping at the weld root.
- Consistent, precise process parameters are necessary to avoid flaws.
3. Material Thickness Restrictions
- While keyhole welding works well for moderate to thick materials, very thin metals can be challenging.
- It's easier to burn through thin sections, resulting in poor-quality welds.
Common Limitations:
Challenge |
Impact |
Equipment Cost |
Higher initial investment |
Process Sensitivity |
Increased risk of weld defects |
Material Limitations |
Not ideal for very thin metals |
Joint Fit-Up |
Tight tolerances required |
Operator Skill |
Experienced personnel needed |
Key Applications of Keyhole Welding
Keyhole welding is used in industries where deep, precise welds and strong joints are required. You often see it wherever thick metals must be joined with minimal defects.
Aerospace Components
In the aerospace industry, keyhole welding is widely used for parts that require high strength and minimal weight.
This process is also applied to turbine blades and other engine components, where safety and performance are crucial.
Key benefits include:
- High penetration, allowing for welding of thick materials in a single pass
- Lower risk of weld defects, which reduces inspection and repair times
- Ability to weld specialized alloys used in aircraft engines
Keyhole welding also helps maintain the strict quality standards that aerospace parts require. The process supports the precise shapes and tight tolerances needed in jet engines and structural components.
Automotive Manufacturing
In automotive factories, keyhole welding is crucial for producing parts such as battery enclosures for electric vehicles and drivetrain components. These parts must be strong, leak-proof, and sometimes corrosion-resistant.
Why it is used in automotive manufacturing:
- Consistent weld quality, which is necessary for high-volume production lines
- Capable of joining dissimilar metals, such as aluminum to steel
- Fast cycle times that fit into automated manufacturing systems
The method is particularly useful for battery packs and structural components where precision is crucial. You may see it on floor panels, frames, and other components that are subjected to high stress.
Nuclear and Power Generation
Keyhole welding is a good choice for making pressure vessels, piping, and containment systems in nuclear and conventional power plants. These parts must remain safe under high pressure and temperature for extended periods.
Common uses:
- Joining thick-walled sections of steel or alloy pipes
- Creating strong, leak-proof seals in components that hold radioactive or hazardous materials
- Ensuring welds are free from voids or weak points that could cause failure
Your facility might rely on keyhole welding to meet strict safety standards required in the power sector. The process allows you to create reliable welds with minimal distortion, even on very large or complex assemblies.
📌 Also Read: Benefits of TIG Welding Pipe
Keyhole Welding Parameters & Optimization
When setting up keyhole welding, several key parameters should be closely monitored. Small changes in these factors can have a significant impact on weld quality, keyhole stability, and final results.
Key Parameters to Adjust:
- Power Density: Adjusting the welding current or laser power controls the amount of energy focused on the workpiece. Higher settings produce deeper and narrower keyholes, while lower power may result in incomplete penetration.
- Travel Speed: Moving too fast can lead to shallow welds and weaker joins. If you travel too slowly, you risk overheating the material or causing excess spatter.
- Shielding Gas Type and Flow Rate: The type and flow of shielding gas, such as argon or helium, protect the molten pool and influence weld quality. Using the right gas helps reduce contamination and improve keyhole stability.
- Plasma Gas Flow Rate: For plasma welding, the rate at which plasma gas is delivered is essential. Adjusting this rate can help keep the keyhole open and consistent.
- Welding Current: This controls the intensity of the process. Careful adjustment is needed to balance penetration depth and weld pool control.
Typical parameter effects:
Parameter |
Low Setting Effects |
High Setting Effects |
Power Density |
Poor penetration |
Deep, narrow welds |
Travel Speed |
Overheating, wide weld |
Shallow, weak welds |
Shielding Gas Flow |
Oxidation, instability |
Turbulence, porosity |
Fine-tuning these values helps reduce defects such as porosity, lack of fusion, or unstable keyholes.
Attention to detail and small tests with your specific materials can guide your settings for better results.
📌 Also Read: Amperage in Welding: How to Choose the Right Settings
Keyhole vs Conventional Arc Welding
Keyhole welding and conventional arc welding use different methods and produce different results.
Key differences:
- Keyhole welding uses a high-energy arc. This creates a narrow, deep opening, or “keyhole,” in the material.
- Conventional arc welding, like standard TIG, uses lower energy. It melts material mostly by conduction, leading to broader and shallower welds.
Comparison Table
Feature |
Keyhole Welding |
Conventional Arc Welding |
Arc Energy |
High |
Lower |
Weld Profile |
Deep, narrow |
Wide, shallow |
Penetration |
Excellent |
Moderate |
Typical Uses |
Thick materials, pipes |
Thin to medium plates |
Welding Speed |
Usually faster |
Slower |
Aspect Ratio |
>1.5 |
<1.5 |
Keyhole welding is well-suited for welding thicker materials or achieving full penetration in a single pass. The high-energy focus also helps reduce the need for multiple weld passes.
In contrast, you may prefer conventional arc welding for thin or medium materials. It is easier to control but may not penetrate as deeply.
Choose keyhole welding for specialized tasks needing deep welds. Conventional arc welding remains useful for general applications and projects that don’t require deep penetration.
Keyhole vs Friction Stir Welding
Keyhole welding and friction stir welding are two distinct techniques used for joining metals.
Keyhole Welding:
- This method utilizes an intense and focused heat source, such as a laser or electron beam.
- The heat melts the metal, creating a hole that moves along the weld path.
- As the tool moves, the molten metal solidifies behind it, forming the joint.
- It's often used for deep, narrow welds in thick materials.
Friction Stir Welding (FSW):
- FSW relies on a rotating tool that stirs and softens the material without melting it.
- The tool moves along the joint, mixing the softened plastic-like metals together until they bond.
- There is no keyhole or melting in this process.
- FSW is known for producing strong joints with fewer defects.
Feature |
Keyhole Welding |
Friction Stir Welding |
Heat Source |
Laser or electron beam |
Mechanical friction (rotating tool) |
Material State |
Melts |
Plasticized, not melted |
Common Uses |
Thick, deep welds |
Aluminum, softer metals, sheet joints |
Formation of Keyhole |
Yes |
No |
Defect Risk |
Can form pores or cracks |
Less risk of common weld defects |
Many industries employ both methods, but you should select the one that best suits your needs.
If you require deep penetration, keyhole welding may be a better option. For clean, strong joints in softer materials, friction stir welding (FSW) is often preferred.
Keyhole vs Resistance Welding
When comparing keyhole welding and resistance welding, you will notice some critical differences in process, speed, and results.
Keyhole welding uses a high-powered laser or electron beam to melt the material, forming a deep, narrow hole known as a "keyhole." This process allows you to achieve strong, deep welds and precise control over penetration.
Resistance welding works by clamping pieces of metal together and passing an electrical current through the joint. The heat produced by electrical resistance melts the metal, creating a weld. This method is most commonly used for joining thin sheets, like in the automotive industry.
Key differences:
- Weld shape: Keyhole welds are characterized by their deep and narrow profile. Resistance welds are usually shallow and broad.
- Speed: Keyhole welding can be three to four times faster than traditional resistance spot welding.
- Materials: Keyhole welding handles thicker materials better. Resistance welding is best for thin metals.
- Equipment: Keyhole needs a laser or electron beam machine. Resistance welding uses electrodes and a power supply.
Feature |
Keyhole Welding |
Resistance Welding |
Power Source |
Laser/Electron Beam |
Electrical Current |
Weld Depth |
Deep |
Shallow |
Precision |
High |
Moderate |
Material Thickness |
Thin to Thick |
Thin |
Speed |
Fast |
Moderate |
You might choose keyhole welding if you need deeper and more precise welds, or greater speed for thicker materials. Resistance welding is better suited for quick, repetitive jobs involving thin metals.
Frequently Asked Questions
Keyhole welding is compatible with various metals and is utilized in industries such as shipbuilding and aerospace. Success depends on factors such as material thickness, welding settings, and the welder's skill.
What metals can be welded using keyhole welding?
You can use keyhole welding on metals such as steel, stainless steel, aluminum, and certain alloys. It is most effective on materials that conduct heat well and have melting points suitable for the process.
Is keyhole welding stronger than MIG welding?
Keyhole welding produces a deep, narrow weld with good penetration. While MIG welding is strong and efficient, keyhole welding can create joints with higher strength and fewer defects in specific applications, especially when complete fusion is important.
How thick can materials be for keyhole welding?
The material thickness for keyhole welding typically ranges from a few millimeters to several centimeters, depending on the equipment and process used. Thicker materials may require multiple passes or special techniques to get a complete weld.
What industries use keyhole welding most?
You will see keyhole welding used in shipbuilding, pressure vessel manufacturing, pipeline construction, and the aerospace industry. These industries require robust, strong welds that can withstand stress and pressure.
What factors influence keyhole formation in welding?
Keyhole formation depends on various factors, including welding current, travel speed, type of shielding gas, and the fit-up of the workpieces. Proper heat input and technique are crucial for creating a stable and controlled keyhole during welding.