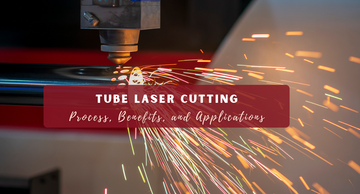
Tube laser cutting transforms metal tubes into precise shapes using high-powered lasers, delivering cleaner cuts than traditional methods.
It works with round, square, and rectangular tubing, ideal for custom designs, structural frames, and industrial parts.
Discover how it outperforms manual cutting in terms of speed, precision, and material flexibility, and learn how to choose the best service for your project.
📌 Also Read: Basics of Plasma Cutting - A Guide
What Is Tube Laser Cutting?
Tube laser cutting is a process that uses a focused laser beam to cut through metal tubes and structural shapes.
The laser can cut pipes, square and rectangular tubes, angles, and channels to precise lengths. It can also make detailed holes or patterns in the tubing.
This technology differs from flat laser cutting, which operates only on flat sheets of metal. Tube laser cutting handles shapes with curves and edges that flat laser cutters cannot process.
There are two main types of lasers used in tube cutting:
- Fiber lasers: Work well on metals like steel, aluminum, and copper. They use fiber optic cables to focus the laser beam.
- CO₂ lasers: Use a gas mixture to produce the laser. They are effective for materials that are not easily cut with fiber lasers.
Industries that use tube laser cutting include:
- Automotive: For cutting frames, exhausts, and roll cages.
- Aerospace: For making lightweight structures and support frames.
- Construction: For cutting beams, supports, and scaffold structures.
Tube laser cutting combines speed, accuracy, and the ability to handle complex shapes. It is a valuable tool for manufacturers working with metal tubes and structural components.
How Does Tube Laser Cutting Work?
Tube laser cutting is a precise manufacturing process that uses a high-power laser to cut metal tubing with accuracy and speed.
Here's how it works in simple terms:
The Laser Cutting Process
- A concentrated laser beam melts or vaporizes metal at the cutting point
- CNC (Computer Numerical Control) guides the laser with extreme precision
- The system can cut complex shapes and patterns with consistent repeatability
Key Components & Automation
- Material handling: Tubes are automatically loaded and held by a rotating chuck
- 360° cutting: The tube rotates while the laser cuts, allowing full circumferential cuts
- Smart detection: Optical sensors often locate weld seams or features for optimal cutting
Standard Workflow
- Load the metal tube into the machine
- The chuck secures and positions the tube
- Sensors scan the tube (if equipped)
- The CNC moves both laser and tube into position
- The laser cuts while the tube rotates/feeds through
Material & Shape Flexibility
- Works with: Steel, stainless steel, aluminum, and other metals
- Handles shapes: Round, square, rectangular, and custom tube profiles
- Benefits: Clean edges, high precision, and minimal manual intervention
This automated process delivers fast, accurate cuts while reducing labor compared to traditional methods.
📌 Also Read: How Does a Plasma Cutter Work?
Key Benefits of Tube Laser Cutting
Tube laser cutting offers several distinct advantages over other cutting methods. The key benefits include higher precision, faster production with less scrap, and the ability to cut a wide range of materials.
1. High Precision & Complex Geometries
You achieve high precision when using tube laser cutting. Lasers produce a narrow, focused beam, resulting in accurate cuts and smooth edges.
This is ideal if your project needs tight tolerances or detailed patterns.
Complex shapes that are difficult or impossible to make by hand or with traditional machines are possible because no physical blades or tooling are needed.
You can cut sharp corners, curves, or custom slots directly into the tube.
Key points:
- Cuts parts to very exact measurements
- No need for special dies or tooling for custom shapes
- Clean edges that often need little or no finishing
- Supports designs like holes and notches placed almost anywhere on the tube
This precision can help reduce the need for additional steps later and provides you with more design freedom.
2. Faster Production & Reduced Waste
Tube laser cutting is usually faster than standard sawing or milling. The laser can cut intricate shapes in a single pass, whereas other methods may require multiple steps.
This speeds up your whole workflow.
You also get less material waste. The laser beam removes a thin line of material, allowing you to nest parts closely together.
That means you use more of each tube and throw away less.
Key points:
- Shorter cutting times per tube
- Cuts many parts from one tube using efficient nesting
- Produces fewer offcuts and mistakes, lowering scrap
- Less material handling because most operations are in one step
This means your production can be both quicker and more cost-effective.
3. Versatility in Materials
Laser tube cutting is compatible with a wide range of metals and alloys, making it a versatile tool for cutting various materials.
You can use this process on:
- Steel (mild, stainless, galvanized)
- Aluminum
- Copper
- Brass
- Some specialty alloys
The same machine can switch between these types often without complex setup changes. Whether you need strong steel tubes, lightweight aluminum, or decorative copper, laser cutting can handle them.
Laser technology can also manage different tube shapes and sizes, including round, square, and rectangular profiles.
This is particularly useful for various industries, including automotive, construction, and furniture manufacturing.
📌 Also Read: A Guide to Choosing the Right Plasma Cutter
Types of Tubes Suitable for Laser Cutting
Laser cutting works with nearly any tube shape or material, consistently delivering clean, precise cuts.
Here's a breakdown of the most common types:
Round Tubes & Pipes
- Best for: Automotive parts, furniture, bike frames, handrails
- Materials: Steel, stainless steel, aluminum
-
Why laser cutting works well:
- Smooth rotation ensures even cuts all around
- Handles both thin and thick walls with precision
- Creates perfect holes, slots, and complex patterns
- Leaves clean edges that need little to no finishing
Square & Rectangular Tubes
- Best for: Building frames, machine parts, shelving
-
Key advantages:
- Straight edges make assembly easier
- Precise notches and cutouts fit together perfectly
- Reduces material waste
- Maintains structural integrity
- Ideal for welding applications
Oval & Custom Shapes
- Best for: Design projects, automotive trim, unique furniture
-
Special capabilities:
- Handles unusual profiles with 3D laser heads
- Cuts complex patterns consistently
- Works with T-sections, L-sections, and other special shapes
- Perfect when exact fit or unique appearance matters
Why Choose Laser Cutting for Tubes?
- Works with all common metals
- Cuts any shape with equal precision
- Faster than traditional methods
- Reduces finishing work
- Minimizes material waste
- Handles both simple and complex designs
Whether you need standard round pipes or custom profiles, laser cutting provides accurate results with clean edges that are ready for assembly. The process adapts to your specific tube shape while maintaining tight tolerances.
Tube Laser Cutting vs. Traditional Cutting Methods
Tube laser cutting offers clean edges, tight tolerances, and speed that outpaces several traditional methods.
It is a non-contact process, which results in less material distortion and often reduces the need for additional finishing.
Laser Cutting vs. Saw Cutting
Laser cutting is much faster than saw cutting. The laser enables accurate, repeatable cuts in a single operation. Saw cutting often needs extra steps to smooth edges or adjust the piece.
With laser cutting, you get:
- Smooth, burr-free edges: In most cases, no additional grinding or finishing is needed.
- Higher precision: Accurate to within fractions of a millimeter.
- Speed: Faster processing, especially for complex or repeated shapes.
- Less physical contact: The material isn’t pressed or pushed, reducing tube deformation.
Saw cutting can struggle with tight tolerances and typically produces rougher edges. This results in additional secondary work and longer production times.
Laser Cutting vs. Plasma Cutting
Laser cutters use a focused beam of light, while plasma cutting uses a jet of hot plasma to melt metal. Both are faster than mechanical cutting options, but they handle material heat differently.
- Heat-affected zone (HAZ): Lasers create a smaller HAZ because they focus energy tightly. This lowers the risk of warping or weakening the material at the cut.
- Precision: Laser cutting provides finer detail and a better fit, especially for thinner tubes or intricate designs.
- Finish quality: Edges from plasma cutting can be rough and may require extra finishing.
Plasma cutting is often used for thicker or less detailed cuts. It is less precise and can alter the structure of the metal near the cut due to increased heat.
Check out Related Products:
|
Arccaptain CUT50 Plasma Cutter Dual Voltage HF Start CutterThe CUT50 only needs to be connected to air, using an air compressor with a minimum pressure of 60 PSI and a flow rate of 3-5 CFM. Wait for the screen to turn off and the fan to stop before switching power. |
|
Arccaptain CUT55 Non-Touch Pilot Arc Plasma Cutter LED Display
|
|
Arccaptain iControl CUT55 Pro Pilot Arc Plasma CutterThe CUT55 Pro Pilot Arc Cutter by Arccaptain is a premium plasma cutter that boasts an upgraded design and an innovative air duct system, which improves cutting efficiency by 39%. Its non-contact pilot arc design enhances cutting performance across a variety of materials and applications while maintaining high quality. |
Laser Cutting vs. Waterjet Cutting
Laser cutting and waterjet cutting both avoid direct material contact, but they excel in handling different types of jobs.
- Material limitations: Laser cutting works very well with metals like steel, stainless steel, and aluminum but can struggle with reflective or heat-sensitive materials. Waterjets can cut a wider range of materials, including some non-metals and composites.
- Thickness: Waterjets can cut thicker material but at slower speeds.
- Cost: Laser cutting is generally more cost-effective for metal tubes, particularly for large-scale production runs. Waterjet cutting can be more expensive due to its slower cutting speed and higher maintenance requirements.
- Edge quality: Both methods produce high-quality edges; however, laser cutting is generally faster and requires less cleanup for metals.
Select the method that best suits your specific needs in terms of speed, precision, material, and budget.
Top Applications of Tube Laser Cutting
Tube laser cutting is widely used in various industries, offering both speed and accuracy. You find this technology in places where metal tubes and profiles need to be cut quickly and with tight tolerances.
Automotive Industry
You see tube laser cutting in automotive manufacturing, where it helps shape exhaust systems and chassis parts. It allows you to create complex and lightweight structures that meet the demands for safety and performance.
Furniture and Architecture
This process enables designers and builders to create custom metal frames for furniture and architectural details. Unique patterns and strong joints can be produced, letting you achieve both style and function.
Medical and Aerospace Fields
Tube laser cutting is essential when you need high precision and quality. In these fields, you use it for making surgical instruments, implants, and aircraft parts that must meet strict standards.
Key Benefits:
- Precise cuts for complex shapes
- Less material waste
- Faster production time
Tube laser cutting enables you to achieve designs and meet functional requirements that are challenging to attain with other methods.
How to Choose a Tube Laser Cutting Service
When selecting a tube laser cutting service, prioritize the service’s experience, expertise, and equipment. Good communication and flexible support are also important.
Key factors to review before selecting a provider:
-
Machine Capabilities: Check the power and size of their laser cutters. Ensure the machines are compatible with the tube lengths and diameters you require. Automation features can help with faster production and consistent results.
-
Material Expertise: Look for a service that has experience cutting the specific type and thickness of materials you need, such as steel, aluminum, or other metals. Some companies might not handle all metals or may have thickness limits.
- Tolerances & Finishing Options: Ask about their ability to meet tight tolerances. Check if they offer additional services, such as deburring, polishing, or coatings, to ensure a clean and finished product.
Select a provider with a proven track record and effective quality control measures. Use these criteria to find a service that matches your needs.
Conclusion
Now that you understand the precision, speed, and versatility of tube laser cutting, it's clear why it's revolutionizing industries from automotive to construction.
This process delivers clean, burr-free cuts with minimal material waste, making it ideal for complex tubular designs.
To complement your laser-cut components, you'll need reliable fabrication and welding tools.
ARC Captain offers premium metal fabrication tools for finishing, durable MIG welding guns for assembly, and portable plasma cutters for modifications.
Pair laser cutting with quality welding equipment for complete fabrication solutions. Explore our tools to take your projects to the next level.
Frequently Asked Questions
Tube laser cutting can be used to cut through different metals, achieve precise tolerances, and handle various thicknesses. The process is known for its accuracy and flexibility in manufacturing.
What materials can be cut with tube laser cutting?
You can cut a wide range of metals, including steel, stainless steel, aluminum, copper, and brass. Most tube lasers are designed for metal cutting, but their exact capabilities depend on the machine and its power.
Other materials, such as plastics or composites, are generally not recommended for tube laser cutting due to the risk of melting or burning.
What is the maximum thickness for tube laser cutting?
The maximum thickness depends on the type of laser and the power output. Most tube laser cutters can handle materials up to approximately 10 mm (around 0.4 inches) thick for mild steel. For stainless steel and aluminum, the limit is often lower, usually around 6-8 mm.
Thicker tubes may require special equipment or cutting techniques.
How accurate is tube laser cutting?
Tube laser cutting is highly accurate. You can expect precision with very small deviations, which allows parts to fit together easily.
Most modern tube lasers have positioning accuracy within 0.1 to 0.2 mm. The exact results depend on the equipment and proper setup.
How accurate is a tube laser?
A tube laser can consistently achieve high accuracy for most industrial jobs. Tolerances are tight, meaning cuts are clean and measurements are precise.
In many cases, a tube laser is precise enough for applications like frames, furniture, or machine parts.
What is the tolerance of laser tube cutting?
Tolerance refers to the allowable difference between the specified measurement and the actual cut. For tube laser cutting, the typical tolerance is about ±0.2 mm, but some advanced machines can achieve even tighter tolerances.
It's important to verify your machine’s tolerance by checking its specifications before starting a project.