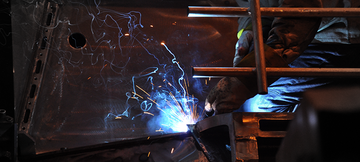
Comment souder l’aluminium ? Vous vous posez peut-être des questions à ce sujet, qui est vraiment un projet très difficile pour les nouveaux arrivants dans le soudage, cet article sera un guide ultime pour vous aider à en savoir plus sur la façon de souder des matériaux en aluminium. c'est le résumé de l'article.
- Introduction
- Caractéristiques de l'aluminium
- Désignation des alliages d'aluminium
- Problèmes de soudabilité de l'aluminium
- Sélection de matériaux d'apport de soudage
- Préparation au soudage
- Procédés de soudage utilisés dans le soudage de l'aluminium
- Soudage TIG
- Soudage MIG
- MIG pulsé
Introduction
L'aluminium et les alliages d'aluminium font partie des matériaux non ferreux et se caractérisent par leur légèreté et leur haute résistance à la corrosion. C'est pourquoi ces alliages sont utilisés dans de nombreuses applications importantes :
- Avions : où l'aluminium représente environ 80% du poids d'un avion civil type (fig. 1)
- Superstructures des vraquiers et des navires (fig. 2)
- Matériel roulant ferroviaire, mobilier routier, pipelines et appareils sous pression, grandes structures civiles et militaires comme les ponts et fabrication de feuilles utilisées dans l'industrie de l'emballage.
- Véhicules blindés militaires où la combinaison de légèreté et de performances balistiques en fait le matériau idéal pour les véhicules militaires rapides (fig. 3).

Fig. 1 Avion concept Boeing SUGAR Volt ‐ Wikimedia Commons

Fig. 2 navires construits principalement en aluminium

Fig. 3 Véhicule blindé de l'armée M113, véhicule blindé de transport de troupes.
Ainsi, en raison de la diversité des utilisations modernes des alliages d'aluminium, l'ingénieur en soudage doit connaître les différents types d'alliages d'aluminium et savoir comment les souder sans aucune dégradation des propriétés. C'est pourquoi dans cet article, nous passerons en revue les différents alliages d'aluminium. alliages et les procédures de soudage appropriées qui doivent être suivies ainsi que les techniques de soudage modernes utilisées pour souder ce type d'alliages.
Caractéristiques de l'aluminium
Certaines caractéristiques de l’aluminium et de ses alliages doivent être prises en compte :
- La grande différence entre le point de fusion de l'aluminium et de l'oxyde d'aluminium, où le point de fusion de l'aluminium est d'environ 1 400 degrés Celsius et celui de l'oxyde d'aluminium est de 2 060 degrés Celsius, de sorte que lorsque l'oxyde d'aluminium se forme pendant le soudage, il devient très difficile d'avoir soudure saine en raison de l'absence de fusion de l'oxyde d'aluminium dû à son point de fusion plus élevé, il faut donc utiliser une technique pour briser cette couche d'oxyde en continu pendant le soudage.
- Le film d'oxyde sur l'aluminium est durable, très tenace et auto-cicatrisant et se forme à température normale. C'est pourquoi les alliages d'aluminium ont une excellente résistance à la corrosion sans aucune protection supplémentaire et par conséquent ils conviennent aux applications exposées comme les avions.
- Le soudage de l'aluminium présente une forte probabilité de déformation par rapport à l'acier, car le coefficient de dilatation thermique de l'aluminium est environ deux fois supérieur à celui de l'acier.
- Dissipation élevée de la chaleur de soudage pendant le soudage par rapport à l'acier en raison de la conductivité thermique élevée de l'aluminium qui atteint 6 fois celle de l'acier en plus de la chaleur spécifique élevée de l'aluminium qui atteint 2 fois celle de l'acier. C'est pourquoi le soudage de l'aluminium nécessite une source de chaleur hautement concentrée en utilisant des procédés pulsés pour obtenir une fusion complète.
- Le soudage par points par résistance de l'aluminium est très difficile en raison de la conductivité électrique élevée de l'aluminium qui atteint les trois quarts de celle du cuivre mais six fois celle de l'acier.
- L’aluminium ne change pas de couleur lorsque sa température augmente, contrairement à l’acier. Cela peut rendre difficile pour le soudeur de déterminer quand la fusion est sur le point de se produire, ce qui rend impératif un recyclage adéquat du soudeur lors de la conversion du soudage de l'acier au soudage de l'aluminium.
- L'aluminium est non magnétique, ce qui signifie que le soufflage d'arc est éliminé comme problème de soudage.
- Le fait que l'aluminium ait une structure cristalline cubique à faces centrées (voir Fig. 4) signifie qu'il ne souffre pas de perte de ténacité lorsque la température diminue. C'est pourquoi l'aluminium est utilisé dans des applications cryogéniques à une température de -200 degrés Celsius.
- L'aluminium a la même structure cristalline lors des cycles de chauffage et de refroidissement contrairement à l'acier qui subit des transformations cristallines, donc un refroidissement rapide n'a aucun effet sur les alliages d'aluminium.

Fig. 4 Cellule d'unité cubique à faces centrées
Désignation des alliages d'aluminium
Il existe une méthode numérique adoptée par le Comité européen de normalisation (CEN) qui sera utilisée comme norme. Ce système utilise quatre chiffres pour identifier les alliages corroyés et cinq chiffres pour identifier les alliages coulés.
Tableau 1 : Classement des alliages d'aluminium corroyés.
Classement numérique |
Élément d'alliage |
AH 1XXX |
Aluminium commercialement pur |
AH 2XXX |
Alliages aluminium-cuivre |
AH 3XXX |
Alliages aluminium-manganèse |
AH 4XXX |
Alliages aluminium-silicium |
AH 5XXX |
Alliages aluminium-magnésium |
AH 6XXX |
Alliages aluminium-magnésium-silicium |
AH 7XXX |
Alliages aluminium-zinc-magnésium |
AH 8XXX |
Autres éléments, par exemple le lithium, le fer. |
AH 9XXX |
Aucun groupe d'alliage attribué. |
Tableau 2 : Classification des alliages d'aluminium coulé.
Classement numérique |
Élément d'alliage |
CA 2 1XXX |
Al-Cu |
CA 4 1XXX |
Al SiMgTi |
CA 4 2XXX |
AlSi7Mg |
CA 4 3XXX |
AlSi10Mg |
CA 4 4XXX |
Al Si |
CA 4 5XXX |
AlSi5Cu |
CA 4 6XXX |
AlSi9Cu |
CA 4 7XXX |
AlSi(Cu) |
CA 4 8XXX |
Al SiCuNiMg |
CA 5 1XXX |
Al Mg |
CA 7 1XXX |
AlZnMg |
Dans le système européen, les préfixes sont utilisés :
- « AB » désigne des lingots destinés à la refusion.
- « AC » désigne un produit coulé.
- « AM » un alliage maître moulé.
- Le préfixe « AW » désigne un produit forgé.
Problèmes de soudabilité de l'aluminium
Avant d'approfondir les processus et techniques de soudage utilisés en soudage, nous devons d'abord connaître les défis courants auxquels vous êtes confronté en tant qu'ingénieur en soudage, superviseur de soudage et soudeur lors du soudage de l'aluminium et des alliages d'aluminium :

Fig. 5 Porosité finement répartie dans une plaque TIG soudée bout à bout de 6 mm d'épaisseur. Avec l’aimable autorisation de TWI Ltd
Les gaz responsables de la porosité proviennent de l’humidité des joints ou des gaz de protection utilisés. Le changement soudain de solubilité des gaz comme H2 est la principale raison de la porosité (voir Fig. 6), c'est pourquoi il est extrêmement difficile de produire une soudure sans porosité dans l'aluminium.

Fig. 6 Solubilité de l'hydrogène dans l'aluminium.
Tableau 3 : Résumé des causes et préventions de la porosité.
Mécanisme de formation de porosité |
Causes potentielles |
Mesures correctives |
Piégeage de l'hydrogène |
|
|
Piégeage de gaz/air |
|
|
Gaz de piégeage à congélation rapide |
|
|
Alimentation en fil irrégulière |
|
pointe contact, régler la pression du rouleau d'entraînement, installer le revêtement approprié, installer les rouleaux rainurés. |
Dans le soudage MIG, il existe un phénomène connu sous le nom de nettoyage cathodique pour briser la couche d'oxyde formée où l'électrode est connectée au pôle positif de la source d'alimentation dans lequel les électrons circulent de la pièce à travailler vers l'électrode et les ions circulent dans la direction opposée. entraînant la rupture de la couche d'oxyde.
Mais il y a un point important à expliquer : pourquoi utilisons-nous le courant AC et DCEP en MIG et AC uniquement pour le soudage TIG ?

Fig. 7 Physique de l'arc pour le procédé de soudage MIG.
Fig. 8 Physique de l'arc pour le procédé de soudage TIG.

Fig. 9 Physique des arcs avec changement de polarité du courant
d'après les figures 7, 8 et 9, il apparaît clairement que le comportement lors de l'utilisation d'électrodes négatives et d'électrodes positives n'est pas le même, car la nature des électrodes utilisées n'est pas la même, dans le cas du soudage MIG, le métal d'apport est l'électrode elle-même qui est de l'aluminium. ayant le même nombre d'électrons à l'échelle atomique où l'aluminium a 13 électrons, donc la puissance d'émission des électrons est la même que celle du métal de base, c'est pourquoi l'électrode positive en MIG est très appropriée pour avoir une pénétration profonde car la surface du métal de base est très grand par rapport à l'électrode, ce qui permet un arc stable et un nettoyage cathodique.
D'autre part, dans le soudage TIG, l'arc est initié à l'aide d'électrodes non consommables comme le tungstène qui ont plus d'électrons à l'échelle atomique où chaque atome possède 74 électrons. C'est pourquoi le TIG avec électrode négative est plus approprié car il permet une plus grande pénétration, comme indiqué. dans les figures ci-dessus en raison du taux d'émission élevé d'électrons lors de l'assemblage du processus d'électrode négative, mais ce processus n'est pas efficace pour le soudage de l'aluminium car il n'aidera pas au nettoyage cathodique. C'est pourquoi le soudage AC par TIG est recommandé pour l'aluminium.
D'après le nom du problème, il est clair que ce problème se produit lors du soudage lorsque le métal d'apport est encore chaud et ce problème est très courant lors du soudage de certains alliages d'aluminium en raison de la présence de composants à faible point de fusion le long des joints de grains de la matrice solidifiée. .

Fig. 10 Fissuration de solidification dans une plaque A6082 de 3 mm d'épaisseur à l'aide d'une soudure TIG avec métal d'apport 4043. Avec l’aimable autorisation de TWI Ltd.

Fig. 11 Effet de la concentration en atomes de soluté sur la sensibilité à la fissuration à chaud.
Comme le montre la figure 11, la sensibilité à la fissuration à chaud dépend principalement de la concentration en élément d'alliage dans l'alliage d'aluminium.
En résumé, en cas de fissuration à chaud, certains facteurs doivent être utilisés pour éliminer ce problème :
- L'utilisation de fils d'apport capables de produire des soudures de petite granulométrie et cela peut se produire par l'ajout de titane, de zirconium ou de scandium agiront comme des noyaux pour la formation d'un grain très fin lors de la solidification.
- Préparation appropriée des joints de soudure en contrôlant la préparation des bords et l'espacement des joints pour permettre d'ajouter suffisamment de métal d'apport au joint pour contrôler que la composition du métal de soudure soit hors de la plage de température élevée.
- Temps de raccourcissement dans la plage chaude courte en utilisant une vitesse de soudage élevée.
Sélection de matériaux d'apport de soudage
Les métaux d'apport en aluminium sont sélectionnés en fonction des problèmes qui préoccupent l'ingénieur en soudage, tels que la résistance aux fissures, la résistance, la couleur et la résistance à la corrosion, contrairement à la sélection des métaux d'apport en acier qui sont sélectionnés en fonction de leurs propriétés chimiques et mécaniques.
AWS A5.10 « Spécifications pour les électrodes et les tiges de soudage en aluminium nu et en alliage d'aluminium » comprend 15 compositions de métaux d'apport distinctes, comprenant des alliages des séries 1XXX, 2XXX, 4XXX et 5XXX.
Tableau 4 : Guide de sélection des matériaux de remplissage
Métal parent |
1050 1080 1200 |
2219 |
3103 3105 |
5005 5083 5251 5454 |
6061 6063 6082 |
7005 7019 7020 7039 |
8090 |
8090 |
5556 |
5556 |
|||||
7039 |
5556 |
5556 |
5356 |
5556 |
5556 |
||
7019 |
5356 |
5356 |
5356 |
5356 |
|||
7020 |
5183 |
5183 |
5183 |
5183 |
|||
7005 |
5039 |
||||||
6061 |
5356 |
4043 |
5356 |
5556 |
|||
6063 |
5356 |
5356 |
|||||
6082 |
4043 |
5183 |
|||||
5454 |
5356 |
5356 |
5356 |
||||
5251 |
5356 |
5356 |
5056 |
||||
5083 |
5356 |
5356 |
|||||
5005 |
5356 |
||||||
3103 |
5356 |
2319 |
5356 |
5356 |
5356 |
5556 |
5556 |
3105 |
4043 |
5056 |
5356 |
||||
2219 |
4043 2319 |
2319 |
|||||
1050 |
4043 |
2319 |
|||||
1080 |
1050 |
4043 |
|||||
1200 |
1080 |
Un certain nombre de points spécifiques doivent être soulignés pour amplifier les orientations données dans les tableaux 4 :
- Lorsque vous soudez des alliages contenant plus de 2% de magnésium, évitez d'utiliser des métaux d'apport contenant du silicium pour éviter la formation de composés intermétalliques de siliciure de magnésium (Mg3Si) qui provoquent une fragilisation des joints.
- Lors de l'utilisation de métaux d'apport 5XXX avec plus de 5 % de Mg comme le 5654, la température de service doit être considérée comme ne dépassant pas 65 degrés Celsius pour éviter la formation d'Al2Mg qui rend l'alliage sensible à la corrosion chimique. Dans ce cas, vous devez utiliser des métaux d’apport à faible teneur en magnésium comme le 5454 ou le 5554 qui contiennent 3 % de magnésium.
- Le 5654 de haute pureté est préféré pour le soudage de l'aluminium de haute pureté dans le service de peroxyde d'hydrogène.
- Le 4643 doit être utilisé avec les alliages 6XXX car la faible teneur en magnésium améliorera la réponse au traitement en solution.
- Les alliages d'aluminium pur 1XXX sont très mous et ductiles, ce qui peut entraîner des problèmes d'alimentation en fil.
- Les alliages 5XXX à faible teneur en magnésium (<2 %) tels que le 5251 peuvent devenir sensibles à des problèmes de fissuration à chaud pendant le soudage lors de l'utilisation de métaux d'apport avec une composition chimique correspondante. C'est pourquoi il est recommandé d'utiliser plutôt le type Al-Mg5.
- Il est recommandé d'utiliser du fil d'apport 5039 lors du soudage des alliages 7XXX pour donner de bons résultats dans les applications à faible dilution.
- Faites attention lors du soudage des alliages 6XXX car ils présentent des fissures de solidification s'ils sont soudés de manière autogène.
- Éléments d'alliage Le titane et le zirconium sont parfois ajoutés aux métaux d'apport pour réduire le risque de fissuration à chaud du métal fondu par affinage des grains.
Préparation au soudage
La préparation des soudures comprend les processus de coupe, de chanfreinage et de réglage fin qui sont couramment utilisés, que ce soit des outils mécaniques comme ceux traditionnels utilisés dans tous les ateliers traditionnels, comme les outils légers de coupe et de meulage, ou la préparation peut être effectuée à l'aide d'un outil de coupe à arc plasma.
Les outils de découpe mécaniques sont les méthodes les plus rentables couramment utilisées dans les ateliers en raison de leur capital inférieur par rapport aux systèmes de découpe laser et plasma.
La préparation des bords pour le soudage peut être effectuée par des méthodes mécaniques en utilisant de nombreux outils, notamment des fraiseuses à grande vitesse, des raboteuses de bords, des défonceuses et divers types de scies, en plus d'équipements pneumatiques dans lesquels vous devez veiller à ce que l'air fourni soit sec et propre ne provoque aucune porosité pendant le soudage.
L'arc plasma peut être utilisé que ce soit pour le soudage ou le coupage et il est considéré comme le processus thermique le plus courant dans la découpe des alliages d'aluminium qui peut être utilisé en mode manuel, mécanisé ou entièrement automatisé.

Fig. 12 Schéma illustrant les principes de la découpe au jet plasma. Avec l’aimable autorisation de TWI Ltd.
Comme le montre la figure 12, la torche de coupage au plasma utilise une électrode en tungstène qui est entourée d'un flux de gaz plasmatique qui peut être de l'air, de l'argon, de l'argon-hydrogène, de l'azote ou du dioxyde de carbone.
Il existe deux types d’arc plasma : l’arc transféré et l’arc non transféré. Dans l'arc transféré, l'arc est amorcé entre l'électrode de tungstène et la pièce à usiner, mais en cas d'arc non transféré, l'arc est amorcé à l'intérieur de la torche à plasma entre l'électrode de tungstène et l'anneau. En découpe, l'arc transféré est généralement utilisé.
La composition du gaz pour le coupage plasma dépend de la qualité de coupe requise, de l'épaisseur du métal à couper et du coût du gaz (tableau 3). L'air est l'option la moins chère et des systèmes monogaz utilisant de l'air et une électrode en hafnium ont été développés pour la découpe de matériaux jusqu'à environ 6 mm d'épaisseur (Fig. 13).

Fig. 13 Découpage au plasma pneumatique. Avec l’aimable autorisation de TWI Ltd.

Épaisseur du métal (mm) |
Gaz plasmatique |
Débit de gaz (L/min) |
Gaz de protection |
Débit de gaz (L/min) |
Courant (Ampère) |
Tension (Volts) |
Vitesse de coupe (mm/min) |
Type de méthode |
1 |
Air |
98 |
4800 |
Manuel |
||||
1,5 |
Air |
98 |
6300 |
Manuel |
||||
3 |
Air |
98 |
3000 |
Manuel |
||||
6.5 |
Air |
98 |
1000 |
Manuel |
||||
6.5 |
N2 |
34 |
CO2 |
100 |
1800 |
Manuel |
||
6.5 |
Ar+H2 |
25 |
200 |
50 |
1500 |
Manuel |
||
dix |
N2 |
35 |
CO2 |
100 |
200 |
1250 |
Manuel |
|
12,5 |
Ar+H2 |
28 |
280 |
55 |
1000 |
Manuel |
||
25 |
Ar+H2 |
33 |
330 |
70 |
500 |
Manuel |
||
50 |
Ar+H2 |
45 |
400 |
85 |
500 |
Manuel |
||
6 |
Ar+H2 |
55 |
300 |
140 |
7500 |
Mécanisé |
||
6 |
N2 |
32 |
CO2 |
100 |
115 |
1800 |
Mécanisé |
|
dix |
N2 |
32 |
CO2 |
100 |
120 |
900 |
Mécanisé |
|
12,5 |
N2 |
32 |
CO2 |
100 |
120 |
480 |
Mécanisé |
|
12,5 |
N2 |
32 |
CO2 |
100 |
300 |
3200 |
Mécanisé |
|
12,5 |
Ar+H2 |
60 |
300 |
140 |
5000 |
Mécanisé |
||
25 |
N2 |
70 |
CO2 |
100 |
400 |
1800 |
Mécanisé |
|
25 |
Ar+H2 |
60 |
375 |
160 |
2300 |
Mécanisé |
||
50 |
N2 |
32 |
CO2 |
100 |
400 |
800 |
Mécanisé |
|
50 |
Ar+H2 |
60 |
375 |
165 |
500 |
Mécanisé |
||
75 |
Ar+H2 |
95 |
420 |
170 |
380 |
Mécanisé |
||
75 |
Ar+H2 |
45 |
N2 |
100 |
400 |
500 |
Mécanisé |
|
75 |
Ar+H2 |
45 |
N2 |
100 |
700 |
650 |
Mécanisé |
|
100 |
Ar+H2 |
95 |
450 |
180 |
750 |
Mécanisé |
||
125 |
Ar+H2 |
95 |
475 |
200 |
250 |
Mécanisé |
Tableau 3 Paramètres suggérés pour la découpe au jet plasma
Pour le soudage TIG de l'aluminium, il existe des préparations de soudage suggérées conformément à la norme BS 3019, comme indiqué dans le tableau 4 ci-dessous :
Épaisseur (mm) |
Préparation des bords |
Remarques |
20swg = Le bridage doit 0,9 mm et être utilisé uniquement 16swg = où carré 1,6 mm |
![]() |
Les préparations de bords à bride sont recommandées lorsque les préparations de bords carrés ne sont pas pratiques. |
3,8 mm |
![]() |
Lorsque la barre de support ne peut pas être utilisée, il est recommandé de souder des deux côtés. |
4,8 mm |
|
|
6,4 mm |
![]() |
Si aucune barre de support n'est utilisée, un écaillage arrière jusqu'au métal soudé sain est effectué et une passe de scellement est ajoutée. |
9,5 mm |
![]() ![]() |
|
12,7 mm |
|
Un préchauffage peut être nécessaire |
|
![]() |
Le tableau 4 suggère une préparation des bords pour le soudage TIG selon BS 3019.
Pour le soudage MIG, des préparations de bords sont suggérées selon la norme BS 3019 selon le tableau 5 ci-dessous :
Épaisseur du matériau (mm) |
Préparation des bords |
Remarques |
1,6-4,8 mm |
![]() |
La barre de support donne un meilleur contrôle sur la pénétration |
6,4-9,5 mm |
![]() |
Souder des deux côtés |
4,8-12,7 mm |
![]() |
Convient pour le soudage des deux côtés |
6,4-12,7 mm |
![]() |
L'écaillage arrière est indispensable avant de souder de l'autre côté |
6,4-19,1 mm |
![]() |
Convient au soudage des deux côtés, mais l'écaillage arrière est indispensable en plus du préchauffage. |
12,7-25,4 mm |
|
L'écaillage arrière est indispensable avant de souder de l'autre côté |
Le tableau 5 suggère des préparations de bords pour le soudage MIG.
Le découpeur plasma ARCCAPTAIN 50A offre d'excellentes performances pour couper l'acier allié, l'acier inoxydable, l'acier doux, le cuivre, l'aluminium, etc. Équipé d'un grand écran LED, vous pouvez lire toutes les données et fonctions clairement et facilement sans enlever votre casque.
Source : Arccaptain , Arccaptain CUT50| Découpeur plasma portable 50 ampères CUT 50 | Facile à utiliser pour les débutants
Procédés de soudage utilisés dans le soudage de l'aluminium
Soudage TIG
TIG signifie soudage au gaz inerte au tungstène et également appelé GTAW qui signifie soudage à l'arc au gaz tungstène selon la norme américaine, mais selon la norme européenne, le processus prend une abréviation numérique qui est 144 pour le soudage TIG.
Comme le montre la figure 14, une électrode en tungstène non consommable est utilisée pour créer l'arc de soudage qui représente la source de chaleur de soudage et cet arc est protégé par un gaz inerte qui est généralement de l'argon pour protéger l'électrode, la colonne d'arc et le bain de fusion.

Fig. 14 Schéma du processus de soudage TIG.
Le soudage TIG de l'aluminium s'effectue généralement en utilisant un courant alternatif pour obtenir l'effet de nettoyage en enlevant la couche d'oxyde et cela se produit sur le demi-cycle positif de l'électrode dans lequel les électrons circulent de la pièce à l'électrode non consommable et les ions circulent dans le sens opposé. direction mais dans l'autre moitié du cycle AC dans laquelle l'électrode est négative, l'électrode refroidit et une pénétration profonde est obtenue.
Dans le soudage AC, l'arc est éteint et rallumé chaque demi-cycle lorsque le courant d'arc passe par zéro, c'est pourquoi une source d'alimentation haute fréquence est généralement utilisée pour obtenir un rallumage instantané de l'arc à haute fréquence (HF), permettant le soudage. arc pour se rallumer dans un délai minimum.
Comme le montre la figure 15, l'équipement moderne utilise un circuit à semi-conducteurs qui modifie le courant alternatif de la forme d'onde sinusoïdale normale à la forme d'onde alternative carrée. Ces sources d'énergie peuvent être ajustées selon les besoins, que ce soit en changeant la fréquence ou en modifiant la durée des moitiés positives ou négatives du cycle.
Les dernières unités basées sur un onduleur offrent un degré élevé de contrôle, la durée négative de l'électrode pouvant être ajustée de 50 % à 90 % du cycle, ce qui entraîne une plus grande pénétration. L'augmentation de la fréquence entraîne un arc plus concentré, augmentant la pénétration, permettant d'utiliser des vitesses de déplacement plus rapides et réduisant la distorsion.

Fig.15 Ondes carrées AC.
Il existe des paramètres de soudage recommandés pour le soudage de l'aluminium, comme indiqué dans le tableau 6 :
Le tableau 6 suggère des paramètres de soudage - protection contre le gaz argon en position plate .
Épaisseur (mm) |
Type de joint |
Écart radiculaire (mm) |
Courant (A) |
Nombre de passes |
Diamètre de remplissage. (mm) |
Vitesse de voyage (mm/min) |
Diamètre de la buse. (mm) |
0,8 |
Cul carré |
néant |
55 |
1 |
1.6 |
300 |
9.5 |
1.2 |
Cul carré |
néant |
100 |
1 |
2.4 |
400 |
9.5 |
1,5 |
Cul carré |
0,8 |
130 |
1 |
2.4 |
470 |
9.5 |
1,5 |
Filet |
100 |
1 |
2.4 |
250 |
9.5 |
|
2 |
Cul carré |
0,8 |
160 |
1 |
3.2 |
380 |
9.5 |
2.5 |
Cul carré |
0,8 |
170 |
1 |
3.2 |
300 |
9.5 |
2.5 |
Filet |
140 |
1 |
3.2 |
250 |
9.5 |
|
3.2 |
Cul carré |
0,8 |
180 |
1 |
3.2 |
300 |
12.7 |
3.2 |
Filet |
175 |
1 |
3.2 |
300 |
12.7 |
|
5 |
Cul carré |
1.6 |
250 |
1 |
4.8 |
200 |
12.7 |
5 |
Filet |
240 |
1 |
4.8 |
250 |
12.7 |
|
6.5 |
70 V-Cul |
néant |
320 |
1 |
4.8 |
150 |
12.7 |
6.5 |
Filet |
290 |
1 |
4.8 |
250 |
12.7 |
|
8 |
70 V-Cul |
néant |
340 |
2 |
4.8 |
165 |
12.7 |
dix |
70 V-Cul |
néant |
350 |
2 |
6.4 |
180 |
12.7 |
dix |
Filet |
370 |
2 |
6.4 |
250 |
16 |
Vous remarquerez qu'il n'y a aucune recommandation concernant les paramètres de soudage TIG pour le soudage de l'aluminium d'une épaisseur supérieure à 10 mm en raison de considérations économiques où le soudage TIG est rarement utilisé.
La soudeuse AC/DC TIG 200P est une puissante machine à souder TIG en aluminium qui offre le soudage avec les méthodes TIG AC Square/Triangular/Pulse Square/Pulse Triangular/DC Pulse/DC/STICK. Il peut être utilisé pour souder divers métaux, notamment l’aluminium, l’acier, l’acier inoxydable, l’acier au carbone et le cuivre. La technologie brevetée DASH-ARC améliore la vitesse d'amorçage de l'arc, l'efficacité du soudage et les résultats, tandis que les fonctions de forme d'onde impulsionnelle, carrée et triangulaire empêchent la combustion du matériau, minimisent la distorsion et améliorent l'apparence des cordons. Le système de contrôle numérique rend la machine fiable et stable, et le grand écran LED permet un réglage facile des paramètres.
Fig. 16 La soudeuse multi-procédés AC/ DC TIG 200P
Soudage MIG
MIG signifie soudage au gaz inerte des métaux dans lequel les consommables de soudage se présentent sous la forme de bobines et non d'électrodes comme dans SMAW ou TIG et le fil est alimenté vers la torche de soudage via une unité d'alimentation en fil et le blindage du fil fondu est effectué à l'aide d'un gaz inerte qui est généralement de l'argon ou un mélange d'argon et d'hélium ou d'hélium.
L'arc MIG nécessite une source d'alimentation qui fournira un courant continu et avec une relation appropriée établie entre le courant de soudage et la tension, cette relation étant connue sous le nom de caractéristique dynamique de la source d'alimentation. Comme mentionné ci-dessus, le procédé MIG utilise un dévidage continu du fil et pour la majorité des opérations de soudage, il est important que la vitesse à laquelle le fil brûle dans l'arc corresponde à la vitesse de dévidage du fil. Ne pas le faire peut entraîner un arc instable et une qualité de soudure variable.
Les développements récents en matière de sources d'énergie ont permis d'utiliser également le processus MIG avec le courant alternatif. La majeure partie de la chaleur développée dans l'arc est générée au pôle positif, dans le cas du soudage MIG de l'électrode, ce qui entraîne des taux de combustion élevés du fil et un transfert efficace de cette chaleur dans le bain de soudure au moyen du fil d'apport.
En soudage MIG. Le fil d'apport fondu est transféré au joint via différents types de modes de transfert qui dépendent principalement du courant et du gaz de protection utilisés et peuvent être liés au diamètre du fil dans le cas du soudage de l'aluminium, comme dans le tableau 7.
Mode de transfert de métal |
Diamètre du fil |
Tremper |
0,8 mm |
Pulsé |
1,2 à 1,6 mm |
Pulvérisation conventionnelle |
1,2 à 1,6 mm |
Pulvérisation à courant élevé |
1,6 mm |
Mixte à courant élevé |
2,4 mm |
Tableau 7 Mode de transfert de métal et diamètre du fil.
Lors du soudage MIG de l'aluminium, le faible point de fusion de l'aluminium entraîne un transfert de pulvérisation jusqu'à des courants de soudage relativement faibles, donnant un joint sans projections.
Dans le tableau 8 ci-dessous, les paramètres de soudage recommandés pour le soudage de l'aluminium par soudage MIG :
Épaisseur (mm) |
Écart de racine/face (mm) |
Angle inclus (degrés) |
Support |
Courant (A) |
Tension (V) |
Nombre de passes |
Diamètre de remplissage. (mm) |
Vitesse de déplacement (mm/min) |
1.6 |
néant |
Carré |
Temporaire |
100 |
19 |
1 |
0,6 |
1000 |
1.6 |
2.5 |
Carré |
Permanent |
100 |
19 |
1 |
0,6 |
1000 |
2.4 |
néant |
Carré |
Temporaire |
140 |
21 |
1 |
0,6 |
1000 |
2.4 |
3.2 |
Carré |
Permanent |
130 |
23 |
1 |
0,6 |
780 |
3.2 |
2.5 |
Carré |
Temporaire |
160 |
24 |
1 |
1.2 |
780 |
3.2 |
5 |
Carré |
Permanent |
135 |
23 |
1 |
1.2 |
720 |
4 |
1,5 |
Carré |
Aucun |
170 |
26 |
2 |
1.2 |
750 |
4 |
1,5/2,5 |
60 sigle-V |
Temporaire |
160 |
27 |
1 |
1.2 |
750 |
4 |
4,5/2,5 |
60 sigle-V |
Permanent |
185 |
27 |
2 |
1.6 |
750 |
6.3 |
2.5 |
60 sigle-V |
Aucun |
200 |
28 |
3 |
1.6 |
750 |
6.3 |
2,5/2,5 |
60 sigle-V |
Temporaire |
185 |
27 |
2 |
1.6 |
750 |
6.3 |
6/1,5 |
60 sigle-V |
Permanent |
225 |
29 |
3 |
1.6 |
750 |
8 |
2,5/1,5 |
60 sigle-V |
Temporaire |
245 |
29 |
2 |
1.6 |
750 |
8 |
4,5/néant |
60 sigle-V |
Permanent |
255 |
29 |
3 |
1.6 |
750 |
dix |
2,5/4,5 |
60 sigle-V |
Aucun |
290 |
29 |
1 |
1.6 |
750 |
dix |
2,5/2,5 |
60 sigle-V |
Temporaire |
275 |
29 |
2 |
1.6 |
900 |
dix |
4,5/néant |
60 sigle-V |
Permanent |
275 |
26 |
1 |
1.6 |
800/850 |
12,5 |
0,8/1,5 |
60 sigle-V |
Aucun |
260/225 |
24/26 |
3face/3inverse |
1.6 |
1050racine/800 |
12,5 |
2,5/1,5 |
60 sigle-V |
Permanent |
260 |
24 |
3face/1inverse |
1.6 |
850racine/550 |
12,5 |
4,5/néant |
60 sigle-V |
Aucun |
270 |
24 |
3 |
1.6 |
550racine/500 |
16 |
1,5/1,5 |
60 sigle-V |
Permanent |
275 |
23/26 |
4face/4inverse |
1.6 |
850racine/650 |
16 |
4,5/néant |
60 sigle-V |
Temporaire |
280 |
26 |
4 |
1.6 |
550racine/450 |
20 |
1,5/1,5 |
60 sigle-V |
Aucun |
255racine/230 |
22/26 |
4face/4inverse |
1.6 |
900racine/550 |
20 |
3/2,5 |
60 sigle-V |
Permanent |
350 |
29 |
4face/1inverse |
2.4 |
1000 |
20 |
6/néant |
60 sigle-V |
Temporaire |
380 |
30 |
5 |
2.4 |
1000 |
25 |
1,5/1,5 |
60 sigle-V |
Aucun |
255 racine/230 |
22/26 |
6face/6inverse |
1.6 |
600 |
25 |
4/2,5 |
60 sigle-V |
Permanent |
350 |
29 |
2.4 |
1000 |
|
25 |
6/néant |
60 sigle-V |
Temporaire |
350 |
29 |
2.4 |
1000 |
Tableau 8 Paramètres de soudage suggérés de l'aluminium par soudage MIG.
16 Soudeuse MIG multiprocédés ARCCAPTAIN MIG200 200 A, machine à souder multi-procédés 6 en 1 (MIG, Spot, TIG, MMA...) - ARCCAPTAIN MIG200 | Déballage et test
L'un des bons soudeurs utilisés dans le soudage de l'aluminium est l'ARCCAPTAIN MIG200 qui utilise une soudeuse mig multi-processus 6 en 1 à double tension, qui convient très bien aux projets de bricolage, de fabrication, de réparation, etc., que vous soyez débutant ou professionnel. soudeur, vous pouvez facilement l'utiliser. La conception polyvalente du MIG200 en fait un excellent investissement pour tous ceux qui recherchent une soudeuse MIG fiable et efficace.
Le MIG 200 intègre les fonctions de soudeuse à bâton , de soudeuse mig, de soudeuse aluminium et de soudeuse tig lift, qui est vraiment une soudeuse polyvalente. Compte tenu de ses performances et de son prix abordable, cette soudeuse est une véritable soudeuse MIG exceptionnelle pour les soudeurs débutants et professionnels. Il est idéal pour les projets de bricolage typiques, car il peut souder pratiquement tout ce dont un propriétaire pourrait avoir besoin. Vous pouvez régler le courant facilement grâce au grand écran LED. Sa taille compacte le rend léger et ultra-portable. Cette machine ne pèse que 28,2 lb, vous pouvez facilement l'emporter partout où vous avez besoin de souder.
MIG pulsé
Le procédé MIG pulsé utilise un faible courant de « fond », suffisant pour maintenir l'arc mais pas assez élevé pour faire fondre le fil. Sur ce courant de fond, une impulsion de « crête » à courant élevé est superposée. Dans des conditions optimales, une seule gouttelette de fil d'apport fondu est projetée à travers l'arc dans le bain de soudure par transfert par pulvérisation. Il est ainsi possible d'obtenir un transfert par pulvérisation et un arc stable à des courants de soudage moyens faibles. Cela permet de souder des métaux très fins avec des fils de grand diamètre, là où auparavant il fallait utiliser des fils très fins, difficiles à alimenter dans l'aluminium tendre. Les courants plus faibles réduisent également la pénétration, ce qui est utile lors du soudage.
matériaux fins et permettent également d'utiliser des vitesses de soudage plus lentes, ce qui facilite la manipulation de la torche par le soudeur dans des conditions d'accès difficiles ou lors du soudage en position.

Fig. 17 Courant pulsé CC, Miller Welding
Comme le montre la figure 17, le changement de fréquence entraîne un changement du nombre d'impulsions pour la même période de temps et vous pouvez également contrôler la période de temps au niveau du courant d'impulsion et du courant de fond.
Résumé:
L'article donne un aperçu du soudage de l'aluminium, y compris les caractéristiques de l'aluminium, la désignation de l'alliage d'aluminium, les problèmes de soudabilité de l'aluminium, la sélection des matériaux d'apport de soudage, la préparation au soudage et les procédés de soudage utilisés dans le soudage de l'aluminium. Il souligne l’importance de comprendre les différents alliages d’aluminium et les procédures de soudage appropriées pour maintenir l’intégrité des joints soudés.
L'aluminium est largement utilisé dans diverses applications en raison de sa légèreté et de sa haute résistance à la corrosion. Il est utilisé dans les avions, les navires, le matériel roulant ferroviaire, les ponts et les véhicules militaires. Cependant, le soudage de l'aluminium présente des défis tels que la formation d'un film d'oxyde, la porosité, la fissuration à chaud et la distorsion.
Pour surmonter ces défis, divers procédés de soudage sont utilisés, notamment le soudage TIG (gaz inerte au tungstène) et le soudage MIG (gaz inerte métallique). Le soudage TIG utilise une électrode en tungstène non consommable et un courant alternatif pour briser la couche d'oxyde et obtenir une pénétration profonde. Le soudage MIG utilise un dévidage continu du fil et un gaz de protection pour protéger le bain de fusion.
L'article fournit également les paramètres de soudage recommandés pour le soudage TIG et MIG de l'aluminium en fonction de l'épaisseur, du type de joint, du courant, de la tension, du diamètre de charge et de la vitesse de déplacement. Il souligne l'importance d'une bonne préparation des bords et de la sélection des matériaux de remplissage en fonction des propriétés souhaitées du joint soudé.
L'article est un bon guide pour les ingénieurs en soudage, les superviseurs et les soudeurs pour comprendre les principes fondamentaux du soudage de l'aluminium et mettre en œuvre des procédures de soudage efficaces pour les alliages d'aluminium.