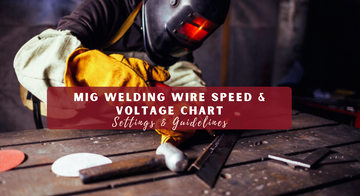
A MIG welding wire speed and voltage chart helps you quickly find the right settings for your welder to match the metal type, thickness, and wire size.
Using the correct speed and voltage settings gives you cleaner welds, stronger bonds, and less frustration.
Whether you’re new to MIG welding or want to improve your skills, knowing how to read and use these charts can save you a lot of trial and error.
This article gives simple steps and tips to set your welder for the best results.
MIG Welding Wire Speed and Voltage Chart: How to Read It and Use It

MIG welding wire speed and voltage charts are helpful tools for choosing the correct machine settings. They make picking good values for your material and wire type easier, helping you get strong welds with less guesswork.
1. What Is a Wire Speed and Voltage Chart?
A MIG welding wire speed and voltage chart lists recommended settings for different welding jobs. The chart usually matches wire feed speed (measured in inches per minute) and voltage with the metal thickness you want to weld and the type of wire you are using.
For example, if you are welding 1/8-inch steel with ER70S-6 wire, the chart might suggest a voltage range of 18 to 19 volts and a wire speed of 280 to 320 inches per minute.
You just look up your metal thickness and wire diameter, then set your welder based on the chart’s numbers.
Charts will vary depending on the brand of welder and the exact wire type. Flux-core and solid wire need different settings, so always check that your chart matches what you are using.
2. Where to Find the Right Chart
The easiest way to find a reliable chart is to look in your MIG welder’s instruction manual. Most machines include a chart printed on a sticker inside the lid or on a page in the manual.
If you can’t find a chart for your machine, visit the website of your welder’s manufacturer. They often have downloadable guides and charts for different models and wire types.

Sample Chart Guide for our MIG130 Welding Machine
You can also search for universal MIG welding charts online, but make sure the information matches your specific wire and metal.
Many welding supply stores have reference charts available. If you buy your wire or welder from them, ask for a copy or check the packaging since some brands print a simple guide right on the box.
📌 Also Read: MIG130 Welding Machine Set Up Gudie
3. Common Units on the Chart
MIG welding charts use several standard units. Knowing what each one means helps you set your machine correctly.
- Wire Feed Speed (WFS): Measured in inches per minute (IPM) or millimeters per minute (mm/min). This tells you how fast the welding wire moves through the gun.
- Voltage (V): Measured in volts. It controls the arc’s heat and how deeply the weld penetrates the metal.
- Amperage (A): Usually not set directly but calculated based on how fast the wire feeds. More wire speed means more amps.
- Plate Thickness: Shown in inches or millimeters. Pick the row that matches your material’s thickness.
Check the chart carefully, as aluminum, stainless steel, or carbon steel settings will differ. Always match the numbers to your actual project for the best results.
MIG Welding Wire Speed and Voltage Chart: Parameters by Wire Type and Thickness
Choosing the correct voltage and wire feed speed is key to getting strong, clean welds. These settings change based on the wire type and the metal thickness you are welding.
ER70S-6 Solid Wire – Mild Steel Settings
When using ER70S-6 solid wire for mild steel, your settings will depend on the thickness of the material. For 1/8-inch steel, set the voltage between 18 and 20 volts and adjust the wire speed from 300 to 400 inches per minute (IPM).
For thin materials like 18-gauge steel, set the voltage lower, around 14 to 16 volts, and lower the wire speed to 150 to 200 IPM. Always use a 75 percent argon and 25 percent carbon dioxide gas mix to protect the weld and reduce spatter.
Quick Reference Table:
Material Thickness |
Voltage |
Wire Speed (IPM) |
Shielding Gas |
1/8 inch (3.2mm) |
18–20 V |
300–400 |
75/25 Ar-CO2 |
18 gauge (1.2mm) |
14–16 V |
150–200 |
75/25 Ar-CO2 |
Check your MIG Welding Wire Speed and Voltage Chart before starting, and make test welds if you are unsure.
Check Out Related Products:
![]() |
Arccaptain 2 Lbs ER70S-6 MIG Welding Wire Gas Solid Wire High-quality: ARCCAPTAIN's ER70S-6 mig welding wire meets industry standards(Net Weight: 2lbs), ensuring consistent performance, superior strength. With its smooth feeding and stable welding parameters, you can achieve optimal penetration, high deposition rates, and exceptional overall welding performance.
|
Flux-Cored Wire Settings (Self-Shielded)
Flux-cored wire works without a separate shielding gas. The wire already has flux inside to protect the weld. For 1/8 inch steel, you usually need a higher voltage, about 19 to 21 volts, and a slower wire speed, around 200 to 300 IPM. This helps the flux burn properly and gives good penetration.
There is no shielding gas to set up, so it's easier for outdoor work. If your weld has lots of spatter, slow down the wire speed slightly, then retest.
Tips:
- Start with 19 volts and 250 IPM for 1/8 inch steel.
- Always check labels on your wire for manufacturer recommendations.
- Watch for a smooth, stable arc.
Check Out Related Products:
|
Arccaptain E71T-GS Flux Core Wire 2 Lbs Spool Gasless Carbon Steel Mig Wire
This Flux Core welding MIG wire is self-shielded, with no shielding gas required, making it ideal for work on rusty, dirty, and painted surfaces material. This welding wire produces stable arc action, low spatter, less welding smoke, excellent welding process properties, no hole seam. |
Stainless Steel Wire
Welding stainless steel requires special attention to gas and settings. To keep the weld shiny and strong, use a tri-mix gas of helium, argon, and carbon dioxide.
Match your voltage and wire speed very carefully. If the wire speed is too high, you get lots of spatter. If it is too low, the weld may not melt evenly.
- For thin stainless: Voltage about 15 to 17 volts and wire speed 150 to 250 IPM.
- For thicker stainless steel, Increase the voltage to 18 to 20 volts and the wire speed to 250 to 350 IPM.
Stainless steel is much less forgiving, so make small test welds first and check for smoothness.
Aluminum MIG Welding Settings
Aluminum needs higher heat and faster feeding. For 1/8 inch aluminum, set your voltage at 21 to 23 volts and wire speed between 450 and 600 IPM.
Only use 100 percent argon as the shielding gas to keep the weld clean.
Settings for thinner aluminum (like 14 gauge) drop to about 18 to 20 volts and 300 to 400 IPM wire speed.
- Use a push technique.
- Keep the gun at a slight angle.
- Feed wire steadily to avoid burn-back.
Before starting, refer to a MIG Welding Wire Speed and Voltage Chart to help you dial in your aluminum settings.
📌 Also Read: MIG Welding Aluminum for Beginners - Tips and Techniques
How Wire Speed and Voltage Affect MIG Welding Quality
The right wire speed and voltage balance is essential for making strong, clean welds. The settings you choose can cause significant differences in how the weld looks, how well it penetrates the metal, and how easy your welding job will be.
Low Voltage or Feed Speed
If you use low voltage or set the wire feed speed too low, your welds will not be strong or reliable. The arc may sputter and keep stopping, making the welds look messy and full of small holes.
Some problems you might see are:
- Poor fusion: The metal does not melt together and will be weak.
- Cold welds: The weld looks dull and might not hold the parts together well.
- Sputtering arc: The welding gun pops and makes a lot of noise.
The weld bead may sit high on top of the base metal and not melt in enough, which means it will not last under stress.
High Voltage or Excessive Wire Feed
Using high voltage or feeding the wire too fast will also hurt the quality of your weld. It can cause the arc to become unstable and make the weld too hot.
Here’s what you might notice:
- Burn-through: The arc gets so hot it melts through thinner metal, leaving holes.
- Excessive spatter: Hot metal splashes all around, making cleanup harder.
- Flat, wide beads: The welds lay too flat and spread out, which does not look good and is hard to control.
Too much wire may pile up, or the weld pool can get out of control. These settings waste wire and gas and make your work more difficult.
Ideal Voltage/Wire Speed Combo
Finding the right combination gives you the best welds. Make a test weld on scrap metal and look at how the bead forms.
Adjust your voltage and wire feed in small steps, focusing on:
- Smooth arc: You should hear a steady, even sound, not loud popping or hissing.
- Consistent bead: The weld bead should be smooth and just slightly raised.
- Good penetration: The metal joins together all the way through without gaps.
You can use a sample chart or guide, but always do a test first because every job is a little different. Making small changes helps you get a clean, strong weld with little spatter.
📌 Also Read: Amperage in Welding: How to Choose the Right Settings
Tips for Adjusting MIG Welding Wire Speed and Voltage

To get the best results from your MIG welder, setting the wire speed and voltage just right is important. Small changes can make a big difference in the strength and look of your weld.
1. Start With the Chart, Then Fine-Tune
Begin by checking the wire speed and voltage chart that comes with your MIG welder or welding wire. These charts show recommended settings for different metal thicknesses, types, and wire sizes. Write down the settings before you adjust anything.
The chart is only a guide. Your welding machine might perform a little differently. Try the settings suggested on the chart first, then test on scrap metal.
Adjust wire feed speed up or down if the weld bead is too thin, thick, or doesn’t fully join the metal. Raise or lower the voltage to get proper penetration and a flatter bead. Practice and patience help you learn how each setting affects the weld.
2. Watch and Listen to the Arc
You can tell a lot about your weld by how the arc looks and sounds. A correct arc sounds like sizzling bacon, with steady and even pops. The arc should look bright and constant, not jumpy.
If you hear loud popping, your wire speed may be too high or your voltage too low. If the arc hisses, the voltage might be too high, or the wire speed too slow.
Pay attention to how the weld bead forms. If it is tall and narrow, turn up the wire speed or lower the voltage. Do the opposite if it is flat and wide with lots of spatter. Small changes help you dial in the perfect settings.
Troubleshooting Tips:
- Popping arc: Decrease wire speed, increase voltage.
- Hissing arc: Increase wire speed, decrease voltage.
- Smooth, even arc: Keep current settings.
3. Keep Wire Clean and Dry
A clean, dry wire is critical for a steady arc and consistent feed. Dirty or rusty wire will not feed smoothly and can cause burnbacks or unstable arcs, even with the right voltage and speed.
Store your wire spool in a dry place. If there is moisture or rust, replace the wire.
Wipe the wire and check the liner and tip before each weld. Don’t forget to keep your gloves clean, as dirty gloves can transfer oil or moisture to the wire.
Quick checklist:
- Store wire spool in a sealed bag or dry box.
- Replace rusty or oily wire immediately.
- Clean rollers and tips regularly to prevent poor feeding.
📌 Also Read: What is the Ideal Mig Welding Gas Flow Rate?
Conclusion: Master the MIG Settings, Master the Weld
Using a MIG welding wire speed and voltage chart helps you set up your machine for clean, strong welds. Whether you are working on steel, aluminum, or stainless steel, these charts eliminate guesswork.
Wire speed and voltage work together to control how the weld looks and holds. If you set them correctly, you get better penetration and fewer problems like spatter or weak joints. If the settings are off, you may have a burn-through or a lack of fusion.
A basic settings chart may look like this:
Material Thickness (inches) |
Voltage (V) |
Wire Speed (IPM) |
1/8 |
17-19 |
200-300 |
3/16 |
18-21 |
300-400 |
1/4 |
20-23 |
400-500 |
Start with the chart, then make small changes to fine-tune your weld. Listen for a steady, even arc while you work. Check the bead for consistency and strength.
Practice makes these settings feel more natural over time. Keep your chart nearby, adjust your dials as needed, and you'll see real improvement in your welds. Consistent use of proper settings leads to safer, neater, and stronger work.
MIG Welding Machines You May Also Like
|
Arccaptain MIG200 Multi Process MIG WelderARCCAPTAIN's top-selling MIG200 is a versatile multi-process All-in-1 MIG Welder suitable for both beginner and professional welders, meeting a wide range of welding project needs. |
|
Arccaptain MIG205MP All-in-One MIG Welder and Cutter ComboEffortlessly transition between MIG, Pulse MIG, Gasless MIG, TIG, TIG Pulse, HF TIG, Lift TIG, Plasma Cutting, MMA, and Cleaning functionalities. |
|
Arccaptain MIG205 Pro Gas MIG Welder Stainless Steel Multi Process MachineThe ARCCAPTAIN MIG205 Pro is an enhanced MIG welder, the successor to the MIG200. It offers improved performance, superior heat dissipation, and app-based control for fine-tuning. This welder is designed to be sleek, portable, and user-friendly. |
❓ FAQs About MIG Welding Wire Speed and Voltage Settings
Setting the right wire speed and voltage in MIG welding affects how well your welds come out. You need to match your machine settings to the thickness of the metal, the type of wire, and the job at hand.
What happens if wire speed is too fast in MIG welding?
If your wire speed is too fast, the welding wire will push into the weld pool and cause spatter. This can also stutter the gun and give you a rough, uneven weld. The arc may become unstable, leading to poor penetration.
How do I adjust the MIG welder settings for different thicknesses of metal?
To weld thicker metal, raise both the voltage and wire speed. For thin metal, use lower voltage and wire speed to avoid burning through. Many machines have charts inside the panel that offer starting points based on metal thickness.
How do I calculate voltage for MIG welding?
Voltage is set by adjusting your machine. There is no formula to calculate a perfect voltage for all projects. You should use a MIG welding chart or start with the recommended wire and metal thickness settings, then test and fine-tune as needed.
What’s the best wire speed for 1/4" steel?
For 1/4" steel, MIG wire speed usually ranges from 200 to 300 inches per minute if you use .035" wire. You must still adjust based on the voltage setting and your welding position. Always make a test weld and adjust if necessary.
Do different wire sizes require different voltage settings?
Yes, different wire sizes need different voltage and wire speed settings. Thicker wires usually use higher voltage and faster wire speed. Using the wrong settings for the wire size can cause either poor penetration or too much spatter.
Is there a universal MIG welding chart?
There isn’t a universal chart that works for all situations. Manufacturer charts are a good starting point, but you’ll still need to fine-tune settings. Factors like shielding gas, metal type, welding position, and other variables all play a role.