Electron Beam Welding (EBW) Explained: How It Works, Advantages & Applications
May 19, 2025
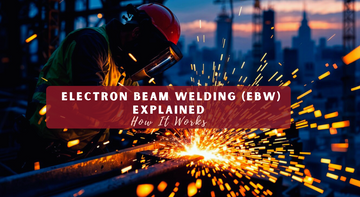
Electron beam welding, often called EBW, is a modern method that uses a focused beam of high-speed electrons to join metal parts.
With electron beam technology, you can create strong, clean welds that are perfect for parts used in aerospace, cars, and electronics.
This advanced welding process works in a vacuum and makes precise connections, even on thick or complicated parts. You're in the right place if you want to know how EBW can help your projects or why so many industries trust it for quality results.
Electron Beam Welding: What It Is and How It Works
Electron beam welding is a type of fusion welding that joins metals by melting them with an intense, focused beam of electrons. It is known for making precise and strong welds, especially in cleaner environments like a vacuum chamber.
Definition of Electron Beam Welding
Electron beam welding, also called EBW, is a process that uses a focused stream of fast-moving electrons to join metals. The beam is aimed directly at the spot where two pieces of metal meet, and the electrons carry a lot of kinetic energy.
When this energy hits the metal, it changes into heat. The intense heat melts the metal at the joint, creating a weld pool. As the metals cool, they fuse and form a strong bond. EBW is used when deep, clean welds are needed, like in aerospace or electronics.
How the EBW Process Works Step-by-Step
To use electron beam welding, you need a special setup inside a vacuum chamber. The vacuum is essential because it keeps air and gas away, letting the beam travel straight to the metal without getting scattered.
The main steps are:
- You place the metal pieces into the vacuum chamber.
- An electron gun generates electrons by heating a special metal part, often called a cathode.
- The gun's electric field pulls the electrons away, while magnetic or electric lenses focus the beam into a tiny spot.
- You aim this sharp beam exactly where the metal pieces meet.
- When the electron beam hits the metal, its energy turns to heat and quickly melts the area, making a weld pool that joins the metals.
- After welding, you let the metals cool so they become solidly joined.
All beam controls, speeds, and positions are set to match the type and thickness of metal you are working with.
Electron Beam Welding: Advantages, Limitations & When to Use It

Electron beam welding (EBW) offers unique benefits and challenges based on its highly controlled process. You’ll see it used for particular jobs where other welding methods might not perform as well.
1. Advantages of EBW
Electron beam welding delivers deep weld penetration with very little distortion to the surrounding metal. This means you get strong, clean joints without causing the nearby material to warp or change shape.
This process occurs in a vacuum, so the welds are free from gas contamination, producing exceptional purity and strength. The electron beam can be focused on a tiny spot, giving you precise control. This is especially important for critical joints where accuracy matters.
EBW can be used on a wide range of metals, including some tricky or hard-to-weld materials. The process also works for similar and dissimilar metals, adding to its flexibility. EBW is ideal when you need both quality and reliability in your welds.
Key advantages:
- Deep, narrow welds
- Low heat input, minimal distortion
- High weld purity
- Precise automation and control
- Suitable for complex or sensitive materials
2. Limitations of EBW
EBW does have some important limitations you should know about. The equipment is expensive, with high upfront and operating costs compared to more common welding machines.
To perform EBW, you need a vacuum chamber, which adds extra time and complexity. This chamber also controls the size of the parts you can weld, so huge pieces may not fit.
EBW works only on electrically conductive materials since the process relies on directing electrons into the metal. Plus, weld preparation and setup are more involved, which can drive up costs and slow down production.
Main limitations:
Limitation |
Impact |
High equipment cost |
Limits general workshop or field use |
Needs a vacuum |
Adds time, cost, and size constraints |
Only for conductive metals |
Non-metals or poor conductors can’t be used |
Complex setup |
Increases preparation and processing time |
3. Ideal Applications of EBW
Electron beam welding is best suited for projects that need deep, precise welds and extremely clean joints. In aerospace, EBW is used to join turbine blades, where even tiny flaws aren’t allowed.
EBW helps create implants and surgical tools from specialized metals that must remain pure and strong in the medical field.
Automotive manufacturing also relies on this technology to weld transmission components that face high stress and must not fail.
You’ll also see EBW used in nuclear and scientific equipment, where both strength and cleanliness of the weld are critical. These applications benefit most from EBW's specific strengths and help justify its higher costs.
EBW vs. TIG Welding
There are some important differences between Electron Beam Welding (EBW) and Tungsten Inert Gas (TIG) welding.
EBW uses a focused beam of electrons inside a vacuum. TIG welding uses a tungsten electrode, usually done in open air with an inert gas shield.
Penetration Depth
- EBW can weld very thick materials in a single pass.
- TIG welding is better for thinner materials or when you need more control over smaller welds.
Precision
- TIG welding is often done by hand, so your skill level really matters.
- EBW is mostly done by machines in special chambers, so you can get higher precision and cleaner welds.
Cost
- EBW is more expensive than TIG welding. The equipment and vacuum chambers cost more.
- TIG welding is more common and costs less to set up and run.
In Short:
Feature |
EBW |
TIG |
Penetration |
Deep, one pass |
Shallow to moderate, multi-pass |
Precision |
Very high, machine controlled |
High, manual or semi-automatic |
Equipment Cost |
High |
Moderate |
Environment |
Vacuum required |
Open air or inert gas |
Choosing between EBW and TIG welding depends on what you need. If you want super precise welds on thick parts and have the budget, you may pick EBW. If you need flexibility and lower costs, TIG welding works well.
Electron Beam Welding vs. Laser Beam Welding

Electron beam welding (EBW) and laser beam welding are high-energy welding methods. They use focused beams to join metal parts. While they sound similar, they have some key differences.
➜ Vacuum Requirement: EBW happens in a vacuum. Special equipment is needed to remove air from the chamber before welding. Laser welding usually works in open air or with a simple gas shield, making it easier and quicker to set up.
➜ Beam Focus and Penetration: The electron beam is tightly focused, which helps it penetrate the metal deeper. EBW can weld thick parts up to half an inch in copper. Laser beams are also focused, but they do not usually reach the same depth, especially in metals like copper.
➜ Speed and Cost: Laser welding is faster to start and often costs less because there's no vacuum. You can change setups quickly, saving time. EBW setups are more complex, and the vacuum adds steps to each weld job.
➜ Material Compatibility: Both methods work well on many metals. EBW is especially good for joining different metals or hard-to-weld materials. Laser welding can have trouble with very reflective metals like copper.
Comparison Table
Feature |
Electron Beam Welding |
Laser Beam Welding |
Works in Vacuum |
Yes |
No |
Typical Weld Depth |
Deeper |
Shallower |
Set Up Speed |
Slow, needs vacuum |
Fast, no vacuum |
Material Options |
Good for many metals |
Good, less for copper |
Equipment Cost |
Higher |
Lower |
📌 Also Read: What is Laser Welding
Electron Beam Welding Equipment and Setup
Electron beam welding (EBW) uses advanced machines that work in a vacuum to rapidly join metal parts. Setting up this equipment requires careful planning and special safety measures to keep operators safe.
Key Components of an EBW System
The main parts of an EBW system include:
- Electron gun: This device generates a beam of electrons that creates the heat needed for welding. It's controlled precisely for different jobs.
- Power supply: Provides the high voltage needed to produce the electron beam. It must be stable, as changes in voltage can affect weld quality.
- Magnetic lenses: These focus and direct the electron beam to the exact spot on the workpiece where welding happens.
- Vacuum chamber: The welding happens inside this chamber, which is fully sealed and pumped free of air to let the electron beam work properly.
- CNC or robotic controls: Automated systems position the workpiece and move the electron beam, allowing for complex shapes and repeated welds with high accuracy.
Each part of the setup needs regular checks and calibration to make sure the welding stays consistent and reliable.
Safety Considerations
Using EBW equipment involves several safety risks that you need to manage:
- Radiation shielding: The electron beam can produce X-rays. Thick lead shielding or other barriers are installed to protect workers from radiation exposure.
- Vacuum safety protocols: The vacuum chamber is under high stress, and sudden air leaks can be dangerous. Before starting, make sure all seals and doors are in good condition.
- High-voltage handling precautions: The power supply runs at very high voltages. Only trained staff should operate or repair it. Use proper grounding, insulated tools, and lockout procedures when working near the system.
Workers should always follow standard safety rules, wear the right protective equipment, and receive regular training on EBW machine operation.
Future of Electron Beam Welding in Industry
Electron beam welding (EBW) is changing fast because of new technology. Automatic systems and new methods make EBW more useful for factories and new products.
Automation and Robotics
Robotic welding plays a big role in modern EBW. When robots are added to EBW systems, they produce steady results and faster work.
Most factories use EBW robots in places where they need to weld many products quickly. These robots can work day and night without a break. You can program them to move with high precision, essential for welding small or complex parts.
Many industries, such as aerospace, car manufacturing, and energy, are adding EBW robots to their production lines.
Automated EBW also lets you track quality with sensors and software, which reduces mistakes and saves material.
Main benefits of robotic EBW:
- High accuracy and less human error
- Faster production and better use of resources
- Safer working environments
📌 Also Read: Aerospace Welding: Techniques and Advancements
Innovations in Non-Vacuum EBW
Traditional EBW needs a vacuum chamber, but new ideas are changing that.
Scientists are working on non-vacuum EBW to make welding faster, cheaper, and simpler. Without the vacuum, you can weld bigger parts and different shapes. Factories save time because they don't need to wait for the chamber to empty air.
Some new systems use a local vacuum or shield the welding spot with special gases. This method still produces clean, strong welds. Non-vacuum EBW opens the door to wider uses, like heavy equipment and large tools.
Why non-vacuum EBW matters:
- Cuts down setup time
- Makes it easier to weld large or odd-shaped items
- Reduces costs by removing the need for full vacuum chambers
📌 Also Read: Understanding Cobot Welding: Benefits, Applications and Safety
Conclusion: Is EBW Right for Your Welding Needs?
Electron beam welding, or EBW, is a high-tech process that joins metals using a focused beam of electrons. It produces strong, neat welds with little distortion, and it is best suited for projects with special needs.
You might want to choose EBW if your job:
- Needs very precise and strong welds
- Uses thick or complex metal parts
- Involves expensive materials where waste must be low
- Needs clean and reliable joints
EBW can join many kinds of metal. It also works under a vacuum, making the welds immaculate and free of common defects.
EBW may not be the best choice for every situation. The equipment is expensive, and you need special training to use it safely. It is usually not used for quick, simple repairs or low-cost projects.
If your job requires top quality with little room for error, EBW is worth considering. As industry demands grow, this method is becoming more common in high-tech fields.
Welding Machines You May Also Like
|
Arccaptain MIG200 Multi Process MIG WelderARCCAPTAIN's top-selling MIG200 is a versatile multi-process All-in-1 MIG Welder suitable for both beginner and professional welders, meeting a wide range of welding project needs. |
|
Arccaptain MIG205MP All-in-One MIG Welder and Cutter ComboEffortlessly transition between MIG, Pulse MIG, Gasless MIG, TIG, TIG Pulse, HF TIG, Lift TIG, Plasma Cutting, MMA, and Cleaning functionalities. |
|
Arccaptain MIG205 Pro Gas MIG Welder Stainless Steel Multi Process MachineThe ARCCAPTAIN MIG205 Pro is an enhanced MIG welder, the successor to the MIG200. It offers improved performance, superior heat dissipation, and app-based control for fine-tuning. This welder is designed to be sleek, portable, and user-friendly. |
❓ FAQs About Electron Beam Welding (EBW)
Electron beam welding (EBW) is a precise process commonly used in advanced manufacturing. It works with many metals, does not use filler, and is often compared to laser welding for clean, strong joints.
What is electron beam welding used for?
You will often find electron beam welding in aerospace, automotive, medical devices, and electronics. It is best for joining small and complex parts that need robust and clean welds. People also use it for welding thick metal sections with little distortion.
Is electron beam welding better than laser welding?
EBW can create deeper, narrower welds than many laser welders. It is often used when a vacuum environment is needed to avoid oxidation or for very thick materials. Laser welding works well in the open air and can be faster for some jobs, but EBW may deliver higher weld quality for certain applications.
Can electron beam welding be used on aluminum?
You can use electron beam welding on aluminum. The process works well, though aluminum’s reflectivity and thermal properties need careful handling. EBW’s focused energy helps join aluminum parts that might be tricky with other methods.
Does electron beam welding require filler material?
Electron beam welding usually does not need filler material. The process melts and fuses the edges of the parts together directly, resulting in a clean, precise weld.
Is electron beam welding expensive?
EBW equipment costs are high, and setup takes careful preparation. The process is more expensive than common welding methods. It is often chosen when you need the special benefits only electron beam welding can provide.